Applications of Nanocomposites
Nanocomposites are materials composed of nano-scale particles dispersed in a matrix material. The nano-scale particles can enhance the properties of the composite significantly compared to conventional micro-scale composites. Some of the key applications of nanocomposites include:
Automotive Industry
The automotive industry utilizes nanocomposites to reduce vehicle weight and improve mechanical properties. Some examples include:
- Nano clay reinforced polymer composites – These are used to produce lightweight and strong plastic parts. The nanoclay particles improve strength, heat resistance and barrier properties.
- Carbon nanotube reinforced polymer composites – CNTs have extremely high tensile strength. CNT/polymer composites are used to make strong yet lightweight exterior body panels. This helps reduce weight and improve fuel efficiency.
- Nano-structured coatings – Coatings made from nanocomposite materials provide resistance against scratching, UV radiation, corrosion etc. They are used to coat exterior body panels, windshields etc.
Aerospace Industry
Aerospace components need to be lightweight and extremely durable. Nano composites help meet these requirements in the following applications:
- CNT-reinforced composites for aircraft wings and fuselage – CNT nanocomposites improve the mechanical properties of the composite tremendously. This allows for lighter and stronger wings and body components.
- Nanostructured thermal coatings – Nanocomposite thermal barrier coatings (TBCs) protect jet engine components from high temperatures. The nano structure improves heat resistance.
- Nano-structured anti-icing coatings – Special nano coatings prevent buildup of ice on aircraft surface. This eliminates the need for mechanical ice removal.
Construction Industry
Nanocomposites and other composite materials are enabling the development of novel high-performance construction materials:
- Self-cleaning concrete – Concrete containing nano particles of TiO2 breaks down organic dirt and cleans itself when exposed to UV light. This reduces maintenance costs.
- Translucent concrete – Concrete containing nano silica particles scatters light to give a translucent appearance. This can be used to construct aesthetically pleasing buildings.
- High-strength concrete – Adding small amounts of carbon nanotubes or nano-silica to concrete can nearly double its strength and halve porosity.
Industry | Application | Benefits |
---|---|---|
Automotive | Body panels | Lightweight, strong |
Scratch resistant coatings | Improved durability | |
Aerospace | Aircraft wings | Lightweight, strong |
Engine components | Thermal resistance | |
Construction | Self-cleaning concrete | Reduced maintenance |
Translucent concrete | Aesthetics |
Challenges
While nanocomposites provide significant enhancements in material properties, there are some challenges that need to be addressed:
- High production costs – Nano particles are expensive to manufacture which increases the cost of nanocomposites. Automated and efficient manufacturing techniques need to be developed.
- Stability and aggregation issues – Nanoparticles tend to clump together which compromises properties. Better dispersion techniques need to be found.
- Toxicity concerns – The human health impact of nanoparticles via various exposure routes needs more evaluation. Appropriate handling precautions need to be taken.
- Recycling issues – It is difficult to recover and reuse nano particles from composite materials after use. More research is needed in this area.
Nanocomposites are an exciting class of engineered materials that provide substantial improvements in properties such as strength, heat resistance, electrical characteristics etc. They enable development of high performance, multi-functional and smart materials that find uses across industries such as automotive, aerospace and construction. Continued research and development is required to improve manufacturing techniques and understand environmental impact of nanocomposites. Their widespread use can enable development of novel materials and components having advanced capabilities.
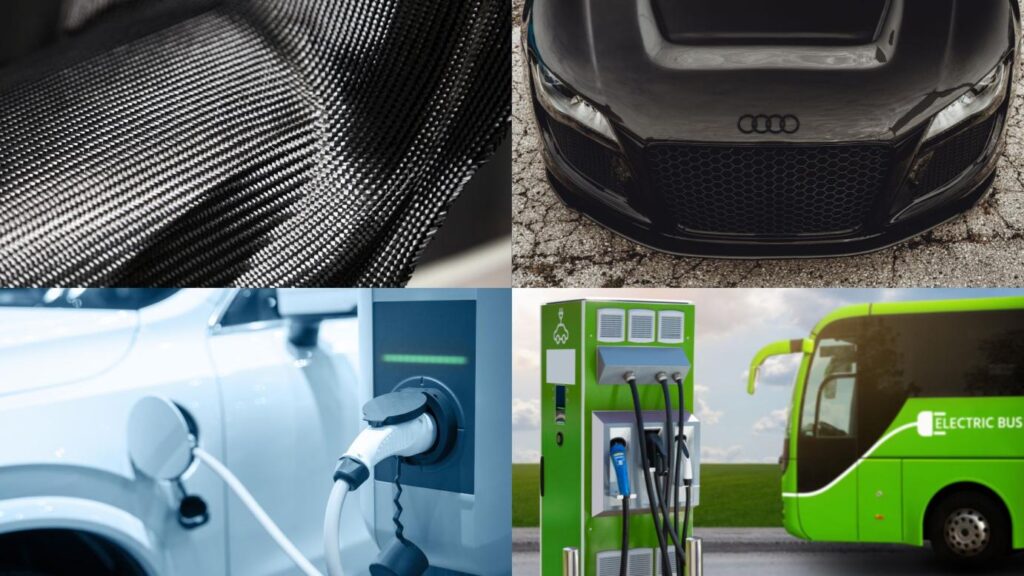
Manufacturing Methods for Nanocomposites
Producing nanocomposites requires combining nano-scale fillers like nanoparticles, nanotubes, nanoclays etc uniformly within a matrix material like a polymer, metal or ceramic. Even dispersion of the nano-scale fillers is critical to achieve the desired properties. Some key methods used for manufacturing nanocomposites are:
Mixing Methods
They involve mechanical mixing of the nano-fillers within the matrix material:
- Solution mixing – The matrix is dissolved in a suitable solvent and nano filler dispersed in it by sonication or mechanical stirring. The solvent is then removed.
- Melt mixing – Used for thermoplastic polymer matrices. Done at elevated temps using equipment like extruder or internal mixer. Shear forces help disperse the nano filler.
- In-situ polymerization – Nano fillers are mixed into monomer. Polymerization reaction is then initiated, resulting in formation of nano composite.
Deposition Methods
Nano fillers are deposited on surface of the matrix material:
- Electrochemical deposition – Matrix material is immersed in a solution containing nanofiller particles. Application of electric field results in deposition of particles.
- Electrophoretic deposition – Charged nanofillers suspended in a solution migrate and deposit on oppositely charged matrix surface under electric field.
- Sol-gel process – Used with ceramic matrix composites. Ceramic precursor sol containing dispersed nano filler is coated on substrate. Heating converts it into nanocomposite film.
Direct Growth Methods
Nano fillers are directly grown on the matrix material:
- Chemical vapor deposition (CVD) – Matrix is exposed to precursor gases which react and deposit solid nanostructured films. E.g. Carbon nanotubes grown on fibers.
- Physical vapor deposition (PVD) – Vaporized material is deposited as thin nano-structured film on matrix. E.g. deposition of nano silver coatings.
Method | Principle | Suitable For |
---|---|---|
Solution mixing | Mechanical mixing in solvent | Polymer matrices |
Melt mixing | Shear mixing in molten state | Thermoplastics |
In-situ polymerization | Mixing fillers in monomer | Thermoset polymers |
Electrochemical deposition | Electric field-driven deposition | Metals, ceramics |
Sol-gel process | Coating using sol, heating to form gel | Ceramics |
CVD | Gas phase deposition reactions | CNTs, metal oxides |
PVD | Physical deposition from vapor | Metals, ceramics |
Challenges
Some challenges present in manufacturing nanocomposites:
- Achieving uniform nanofiller dispersion – Particles tend to clump together driven by surface forces.
- Preventing damage to nanofillers – Some processes like sonication and high shear mixing can damage and alter nanoparticles.
- Removing contaminants – Impurities arising from precursors must be minimized.
- Scaling up processes – Methods like CVD and PVD may be difficult to scale up for mass production.
A variety of methods exist for producing nanocomposites, each having specific pros and cons. Combinations of techniques are usually employed to produce the composites. More research is needed to improve dispersion, scale up processes and minimize damage to nanofillers. Manufacturing techniques need to be tailored to the specific nanofiller and matrix combination to obtain optimal properties.
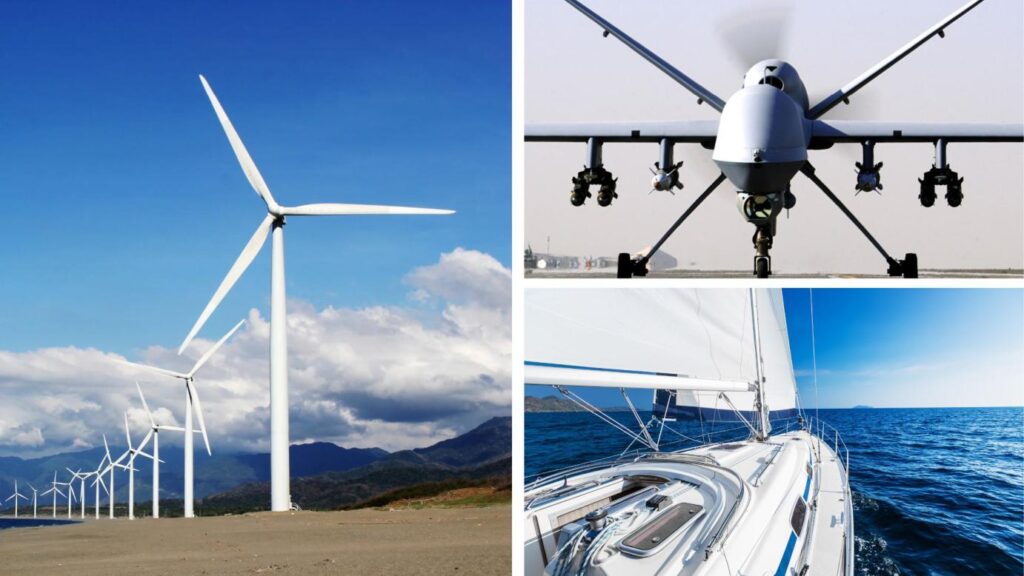
Characterization of Nanocomposites
Nanocomposites are materials that incorporate nano-scale fillers within a matrix material. The nano-scale fillers impart enhanced properties like strength, conductivity, heat resistance etc to the composites. In order to understand the structure-property relationships in nanocomposites, a wide range of characterization techniques are utilized. Some key techniques include:
Microscopy
Microscopes are used to analyze the morphology and distribution of nano-fillers:
- Optical Microscope – Used for initial examination but limited to resolutions > 200 nm.
- Scanning Electron Microscope (SEM) – Shows fine details down to ~5nm. Can view topology and cross-sections.
- Transmission Electron Microscope (TEM) – Provides very high resolution (< 0.5 nm) images of nano particles.
Spectroscopy
Spectroscopic analysis provides information on atomic structure:
- Fourier Transform Infrared (FTIR) Spectroscopy – Identifies chemical structure of matrix and filler materials.
- Raman Spectroscopy – Provides information on defects, stress and alignment of nano fillers.
- X-ray Photoelectron Spectroscopy (XPS) – Determines elemental composition and chemical bonding at surface.
X-ray Techniques
X-ray diffraction and scattering are used to analyze crystal structure:
- X-ray Diffraction (XRD) – Determines atomic structure, crystallinity and orientation of nano fillers.
- Small Angle X-ray Scattering (SAXS) – Provides statistical data on nanoparticle size distribution and dispersion.
Thermal Analysis
- Differential Scanning Calorimetry (DSC) – Measures thermal transitions to obtain data on crystallinity, cure reactions etc.
- Thermogravimetric Analysis (TGA) – Monitors weight changes during heating to determine composition.
Technique | Information Obtained |
---|---|
Optical Microscopy | Particle distribution, matrix defects |
SEM | Topology, particle dispersion |
TEM | High resolution particle images |
FTIR | Chemical composition |
Raman Spectroscopy | Filler alignment, defects |
XPS | Surface composition, chemical bonding |
XRD | Filler crystal structure |
SAXS | Particle size distribution |
DSC | Thermal transitions, curing |
TGA | Decomposition behavior, composition |
A wide variety of analytical techniques are essential to understand the complex structure-property relationships in nanocomposites. These include microscopy, spectroscopy, diffraction and thermal analysis. Using multiple complementary techniques provides comprehensive characterization of parameters like particle morphology, matrix-filler interface, bonding structure and thermal stability. The knowledge obtained helps optimize nanocomposite fabrication methods and properties.
Carbon Nanotube based Nano Composites
Carbon nanotubes (CNTs) are tiny cylindrical structures composed of rolled up graphene sheets. Their nanometer dimensions coupled with extraordinary mechanical and electrical properties make them ideal candidates for developing enhanced nano composites. Some applications include:
CNT Polymer Nano Composites
- Incorporating small amounts (~1% by weight) of CNTs into polymers like epoxy, nylon etc results in materials with superior strength and electrical conductivity.
- CNT/polymer composites are fabricated by solution mixing, melt blending and in-situ polymerization methods. Functionalization improves CNT dispersion.
- Applications include lightweight conductive parts like enclosures, capacitive touch sensors, anti-static materials.
CNT Ceramic Nano Composites
- Addition of CNTs to ceramics like alumina and zirconia improves fracture toughness and wear resistance significantly.
- Such nano composites are applied as coatings on metal cutting tools to prolong tool life.
- CNTs also enhance electrical and thermal conductivity of ceramic nanocomposites for applications like heating elements.
CNT Metal Matrix Nano Composites
- Dispersed CNTs act as barrier to dislocations, strengthening metal matrices like aluminum, magnesium and copper alloys.
- Other benefits include increased hardness, tensile strength and thermal conductivity.
- Used to develop light weight and wear resistant aluminum components for aerospace and automotive uses.
Matrix | Key Properties Enhanced | Applications |
---|---|---|
Polymers | Strength, conductivity | Enclosures, sensors |
Ceramics | Toughness, conductivity | Cutting tools |
Metals | Strength, conductivity | Aerospace components |
Challenges
Some issues in utilizing CNTs in nano composites:
- Achieving homogeneous dispersion without damaging CNTs
- Reducing CNT agglomeration caused by van der Waals forces
- Tailoring interface between CNTs and matrix for load transfer
- Controlling chirality and arrangement during alignment of CNTs
CNT reinforced nano composites enable development of lightweight structural materials with advanced multifunctional capabilities. Further research is focused on improving the quality of CNT dispersion, orientation and matrix-filler interfaces. With significant enhancements in mechanical, conductive, and thermal properties, CNT nano composites hold promise for numerous high-tech applications.
Modeling the Properties of Nano Composites
Modeling involves developing mathematical relationships to predict how the nano-scale structure influences the overall properties of composites. It helps provide directions for experiments and improve understanding of nano composite behavior. Some modeling approaches include:
Micromechanics Modeling
- Predicts mechanical properties by modeling interactions between nano particles and matrix at micron level.
- Common analytical models are Halpin-Tsai, Mori-Tanaka and shear-lag models.
- Accounts for factors like particle shape, orientation, aggregation and interface.
- Allows determination of optimal nano filler loading fraction.
Multiscale Modeling
- Uses computational methods like finite element analysis to model nano to macro scale structure.
- Can incorporate actual micrographs or simulated microstructures as input geometry.
- Provides detailed stress-strain output at matrix and nano particle length scales.
- Helpful for composites with complex hierarchical structures.
Molecular Dynamics Simulation
- Uses physics-based modeling of atoms and molecules to study nano scale interactions.
- Provides insight into formation, structure and properties of interphases.
- Can simulate fracture, creep, fatigue behavior at nano level.
- Computationally intensive but provides high resolution predictions.
Method | Scale | Key Information |
---|---|---|
Micromechanics | Micron | Overall mechanical properties |
Multiscale | Nano to macro | Local stress-strain fields |
Molecular dynamics | Nano | Interface structure, dynamics |
Challenges
- Generating realistic nano scale geometry and microstructures
- Obtaining accurate material and interface properties as input
- Validation of models with systematic experiments
- Computational requirements for atomistic simulations
Modeling is a powerful tool for design and optimization of nano composites. It bridges relationships between structure, processing and properties. With increasing computational capabilities, highly sophisticated models incorporating actual nano geometries can provide deep insights that complement experimental work. Modeling will play a pivotal role in accelerating nano composite development.
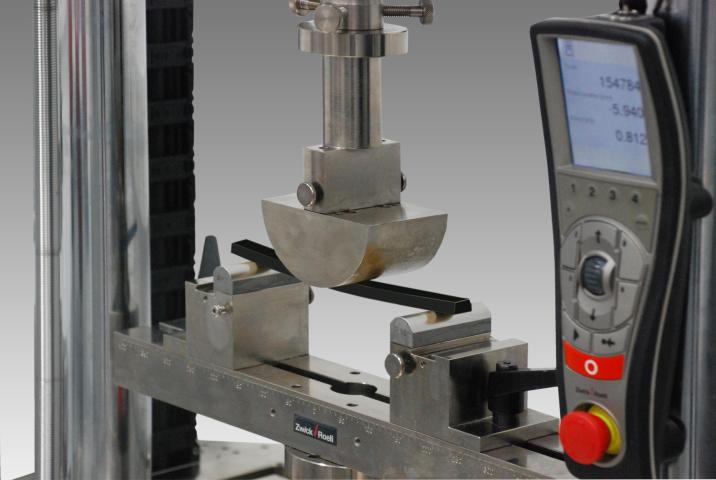
Health and Safety Concerns with Nano Composites
The tiny size and unique properties of engineered nanomaterials provide significant performance benefits but also raise concerns regarding their interactions with biological tissues and the environment. Some key aspects include:
Exposure Routes
- Inhalation – Most common route. Nano particles can deposit deep in lungs. Face masks provide protection.
- Ingestion – Some nano fillers used in food packaging could migrate into edibles/drinks. Toxic effects need evaluation.
- Skin contact – Few nano particles can penetrate skin. But prolonged exposure may cause irritation. Gloves are recommended.
Toxicity Mechanisms
- Cellular damage – Sharp corners of some nano materials damage cell membranes. Fiber shaped ones (CNTs, nanowires) cause inflammation.
- Oxidative stress – Reactive oxygen species generated by nano particles cause DNA damage and protein denaturation.
- Metal toxicity – Soluble metal nano particles release toxic ions that disrupt tissue function.
Managing Risks
- Assessment of exposure potential during all stages of product life cycle.
- Adequate ventilation, protective gear for workers handling nanocomposites.
- Proper disposal guidelines to prevent release into environment.
- Further toxicology studies for risk identification. Development of safer alternatives.
Routes | Hazards | Safeguards |
---|---|---|
Inhalation | Lung inflammation | Masks, ventilation |
Ingestion | Toxic effects | Migration testing |
Skin contact | Irritation | Gloves, protective clothing |
Nanomaterials provide immense advantages but also have potential biological side-effects that need careful assessment. A combination of safe handling practices and gear coupled with toxicology studies to identify hazards will allow mitigating the risks involved. Regulatory oversight and development of safer nano forms are required for responsible commercialization.
Flame Retardant Nano Composite Materials
Flame retardancy is the ability of a material to resist ignition, delay the onset of fire, and inhibit the spread of flame. Nano composites with flame retardant capabilities are being developed as safe alternatives to traditional halogenated flame retardants. Strategies include:
Nano Clay Reinforced Composites
- Nanoclays like montmorillonite are added to polymer matrices like polypropylene and epoxy resins.
- Nanoclay layers create a tortuous path that slows heat and mass transfer during burning.
- Additional flame retardant fillers like metal hydroxides can be added to further improve fire response.
- Used for building insulation, electronic appliance housings to prevent fire risks.
Intumescent Nano Coatings
- Coatings containing nano scale ingredients that expand into an insulating char layer upon heating.
- Components include nano graphite, ammonium polyphosphate, metal oxides and carbon nanotubes.
- Applied to wood, textiles and polyurethane foams to significantly reduce flammability.
Hybrid Organic-Inorganic Flame Retardants
- Combining nano scale organic resin with inorganic nano particles produces hybrid system with high flame retardancy.
- Exhibits improved thermal stability, adhesion and ability to form protective char layers.
- Used as flame retardant coatings on furniture, automotive interiors and building panels.
Nano Composite System | Benefits | Applications |
---|---|---|
Nano clay and polymer | Reduced burning rate | Insulation, appliances |
Intumescent coatings | Expanded char layer | Textiles, polyurethane |
Hybrid organic-inorganic | Char formation |
Self-healing Nano Composites
Self-healing materials have the ability to autonomously repair damage. Incorporating nano fillers enables imparting self-healing capability to polymer and cement based composite materials.
Self-healing Polymer Composites
- Microcapsules containing repairing agents like epoxy are embedded within the polymer matrix.
- Cracks rupture the microcapsules, releasing repair resin that fills cracks via capillary action and then hardens.
- Carbon nanotubes help improve capsule dispersion and strengthen healed regions.
- Used in structural composites for aerospace and automotive to restore mechanical properties.
Self-healing Cementitious Composites
- Microcapsules carrying chemicals like sodium silicate solution are added to cement matrix.
- Cracking triggers capsule rupture and release of chemicals that precipitate healing products in cracks.
- Nano silica improves distribution of microcapsules and enhances strength recovery.
- Used in concrete structures like bridges and buildings to close cracks and prevent degradation.
Composite | Nano Reinforcement | Applications |
---|---|---|
Epoxy | Carbon nanotubes | Aerospace composites |
Cement | Nano silica | Concrete structures |
Challenges
- Reducing microcapsule brittleness and improving crack resistance
- Achieving good bonding between healing agent and matrix
- Retaining mechanical strength after repeated self-healing
- Developing methods to deliver sufficient repair material
Self-healing nano composites provide built-in repair mechanism that reduces need for costly and difficult manual maintenance of critical structures. Further improvements in capsule strength, healing efficiency and repeatability can help maximize the benefits of these smart materials.
Electrical Conductivity of Nano Composites
Nano composites containing conductive nano fillers like carbon nanotubes exhibit enhanced electrical and thermal conductivity. This enables their use in advanced electronic applications.
Graphene Enhanced Conductive Composites
- Graphene nano platelets added to acrylonitrile butadiene styrene (ABS) improves electrical conductivity up to 8 orders of magnitude.
- Very low percolation threshold of 0.1 vol% due to graphene’s high intrinsic conductivity and large surface area.
- Used as conductive plastic enclosures for electronics requiring EMI shielding like medical devices.
Silver Nano Wire Composites
- High aspect ratio silver nano wires provide conductivity at low fractions compared to particles.
- Flexible transparent electrodes fabricated using silver nanowire-polymer composite films.
- Used as heating films, current-carrying coatings, substrates for flexible displays.
CNT/Polymer Conductive Films
- CNTs can be aligned during processing using electric fields to form conductive pathways in insulating polymers.
- Improves electrical conductivity and mechanical strength of composites.
- Used for antistatic coatings, capacitive sensors, electromagnetic shielding applications.
Nano Filler | Matrix | Applications |
---|---|---|
Graphene | ABS | Enclosures, EMI shielding |
Silver nanowires | Polymer | Transparent electrodes |
CNTs | Polymer | Conductive films, sensors |
Nano composites containing graphene, CNTs and metal nanostructures exhibit tailored electrical conductivity and permit novel electronic applications and devices. Further improvements in filler dispersion and alignment can help achieve optimal properties.
Energy Applications of Nano Composites
The addition of nano fillers enables the development of composites for efficient energy generation, storage and saving applications.
Thermoelectric Nano Composites
- Polymer composites containing carbon nano tubes and graphene allow flexibility and low processing temperatures.
- Exhibit 100-1000x higher thermoelectric figures of merit compared to polymers.
- Used as coatings to harvest waste heat from sources like metal surfaces and human skin.
Nano Composite Battery Electrodes
- Carbon nano fibers, graphene and CNTs enhance electrical conductivity and charge mobility in both anode and cathode.
- Silicon nanoparticles in nano structured carbon matrix provide high lithium ion battery capacity with stability.
- Enable development of high performance Li-ion batteries for electric vehicles and grid storage.
Nano Insulation Materials
- Addition of nano silica, alumina or titania enhances thermal resistance and energy efficiency of fiber composites.
- Aerogel composites containing silica or carbon nano particles have extremely low thermal conductivity.
- Used as insulators for buildings, refrigerated transport and industrial systems.
Application | Nano Composite | Benefits |
---|---|---|
Waste heat harvesting | Polymer-CNT/graphene | High thermoelectric efficiency |
Batteries | Nanostructured carbon-silicon electrodes | High capacity, stability |
Thermal insulation | Nano silica/alumina composites, aerogels | Low thermal conductivity |
Nano composites can enable energy applications ranging from thermoelectric power generation to battery storage to insulation. Further research aims to improve nano filler dispersion, electrical and thermal transport to optimize energy conversion efficiencies.