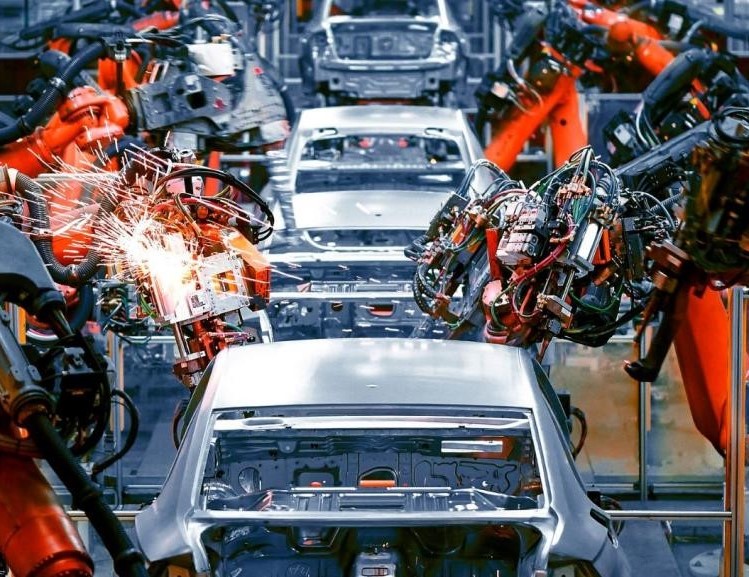
I. Introduction
The automotive industry is undergoing a transformative shift, driven by the increasing demand for lightweight, fuel-efficient, and environmentally friendly vehicles. One of the key technologies revolutionizing the industry is the use of composite materials. In this article, we will explore the tremendous potential of composite materials and their profound impact on the automotive sector.
A. Definition of Composite Materials
Composite materials are engineered materials composed of two or more distinct components that, when combined, exhibit superior properties compared to their individual constituents. These components, known as the matrix and the reinforcement, work together synergistically to create a material with enhanced strength, durability, and performance.
Composite materials can be tailored to meet specific requirements by selecting the appropriate combination of matrix and reinforcement materials. Common matrix materials include thermoset resins, thermoplastic polymers, and metals, while reinforcement materials can be fibers such as carbon, glass, or natural fibers.
B. Importance of Composite Materials in the Automotive Industry
Composite materials have gained significant importance in the automotive industry due to their unique characteristics and advantages. Their lightweight nature, coupled with exceptional mechanical properties, makes them an ideal choice for improving fuel efficiency, vehicle performance, and sustainability.
By replacing traditional metal components with composites, automakers can significantly reduce the weight of vehicles. A lighter vehicle requires less energy to propel, resulting in improved fuel efficiency and reduced emissions. This weight reduction also enhances overall vehicle performance, including acceleration, handling, and braking.
Moreover, composite materials offer design flexibility, enabling innovative vehicle architectures and aesthetic enhancements. They can be molded into complex shapes, allowing designers to create streamlined and aerodynamic vehicle structures. Additionally, composites offer a wide range of color and texture options, providing opportunities for unique styling and visual appeal.
C. Overview of the Article’s Content
In this article, we will delve into the diverse aspects of composite materials in the automotive industry. We will explore their evolution, types, benefits, and applications in various automotive components. Furthermore, we will discuss the challenges associated with their adoption and provide insights into future trends and innovations.
By understanding the impact and potential of composite materials, readers will gain valuable insights into how these materials are shaping the automotive industry. Whether you’re an automotive enthusiast, industry professional, or simply curious about the future of transportation, this article will provide you with a comprehensive understanding of the power of composite materials in revolutionizing the automotive landscape.

Early Use of Composite Materials in Automobiles: Pioneering Innovation in Vehicle Manufacturing
In the ever-evolving landscape of automotive engineering, one cannot undermine the role of composite materials in shaping the industry. These innovative materials have revolutionized the way vehicles are designed and built, offering a range of advantages over traditional metal counterparts. In this article, we delve into the early use of composite materials in automobiles, exploring the pioneering innovations that paved the way for their widespread adoption.
Fiberglass: The Game Changer
In the mid-20th century, a significant breakthrough occurred in the automotive industry with the introduction of fiberglass-reinforced composites. Fiberglass, composed of fine glass fibers embedded in a polymer matrix, offered automakers a lightweight alternative to steel and other heavy metals. This transformative material had excellent corrosion resistance and remarkable design flexibility.
One of the most notable examples of early composite use was witnessed in the iconic Chevrolet Corvette. In 1953, the Corvette made history as the first mass-produced American sports car to feature a fiberglass body. By incorporating fiberglass body panels, Chevrolet achieved a substantial reduction in weight, enhancing the car’s agility, performance, and fuel efficiency.
Advancements in Composite Material Technology
As the automotive industry embraced the potential of composites, research and development efforts intensified, leading to significant advancements in composite material technology. Engineers and scientists began exploring alternative fibers and matrices, seeking materials that would further push the boundaries of automotive design and performance.
One such groundbreaking development came in the form of carbon fiber-reinforced polymers (CFRP). Carbon fiber composites offered exceptional strength-to-weight ratios, making them an ideal choice for demanding automotive applications. Although initially limited to high-performance and luxury vehicles due to cost considerations, the advancements in manufacturing techniques and economies of scale have made carbon fiber composites more accessible across a wider range of vehicles.
Impact on Automotive Design and Performance
The introduction of composite materials had a profound impact on automotive design and performance. The lightweight nature of composites allowed designers to explore innovative vehicle architectures, pushing the boundaries of traditional design constraints. By reducing the weight of vehicle structures, automakers achieved substantial improvements in fuel efficiency, range, and overall performance.
Composite materials also revolutionized safety standards in automobiles. The high strength and stiffness of composites allowed for the design of lighter yet stronger components, enhancing crash safety and occupant protection. In the event of a collision, composite materials excel at absorbing and dissipating impact energy, safeguarding the passengers and minimizing the potential for severe injuries.
Moreover, the design flexibility offered by composites opened up new avenues for aerodynamic advancements. The sleek and curvaceous designs made possible by composite body panels reduced drag and improved aerodynamic efficiency. This not only translated to better fuel economy but also contributed to a smoother and quieter driving experience.
The early use of composite materials in automobiles marked a pivotal moment in the history of vehicle manufacturing. The advent of fiberglass and subsequent breakthroughs in composite material technology reshaped automotive design, performance, and safety standards. From the lightweight and corrosion-resistant properties of fiberglass to the remarkable strength-to-weight ratios of carbon fiber composites, these materials continue to drive innovation in the industry.
As automakers embrace the possibilities offered by composites, we can expect to witness even greater advancements in the future. From electric vehicles to autonomous driving, the early pioneers of composite materials in automobiles laid the foundation for a promising and transformative future in the automotive industry.
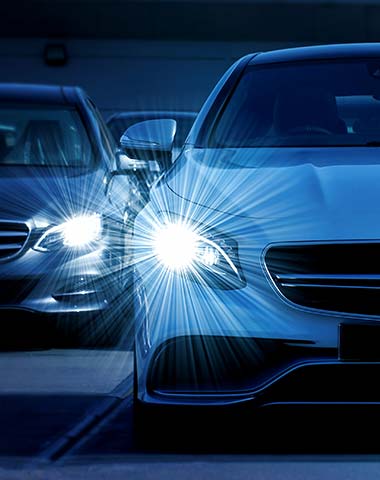
Advancements and Breakthroughs in Composite Material Technology: Shaping the Future of Automotive Innovation
In the dynamic world of automotive engineering, the continuous pursuit of technological advancements has led to remarkable breakthroughs in composite material technology. Composite materials, comprising a combination of fibers and matrices, have revolutionized the automotive industry by offering unparalleled strength, lightweight properties, and design flexibility. In this article, we explore the advancements and breakthroughs that have propelled composite materials to the forefront of automotive innovation.
Carbon Fiber Composites: From Luxury to Mainstream
Carbon fiber composites have emerged as a game-changer in the realm of automotive materials. Initially restricted to high-end luxury and performance vehicles due to their high cost, advancements in manufacturing techniques and economies of scale have made carbon fiber composites increasingly accessible across a broader range of vehicles.
One significant breakthrough was the development of carbon fiber reinforced polymers (CFRPs). These composites offer exceptional strength-to-weight ratios, surpassing traditional materials like steel and aluminum. The use of CFRPs in critical components such as chassis, body panels, and structural reinforcements has significantly contributed to weight reduction and improved overall vehicle performance.
Advanced Manufacturing Techniques: From Hand Layup to Automated Production
The evolution of composite material technology has been closely tied to advancements in manufacturing techniques. In the early stages, composites were predominantly manufactured using labor-intensive processes like hand layup, where layers of fibers and resin were manually stacked and cured. While effective, this method was time-consuming and limited in terms of scalability.
The introduction of automated manufacturing processes, such as automated fiber placement (AFP) and automated tape laying (ATL), revolutionized composite production. These techniques utilize robotic systems to precisely lay down continuous fibers and resin tapes, resulting in more consistent and efficient production. Automated manufacturing not only reduces production time but also enhances product quality and repeatability, making composite materials more commercially viable for mass-produced vehicles.
Hybrid Composites: Combining the Best of Both Worlds
To further optimize performance and cost-effectiveness, hybrid composites have gained prominence in recent years. Hybrid composites combine different types of fibers, such as carbon and glass, with various resin matrices, allowing manufacturers to tailor the material properties to specific application requirements.
By strategically utilizing hybrid composites, automakers can achieve a balance between strength, stiffness, weight reduction, and cost. For example, carbon fiber composites can be strategically placed in high-stress areas, while glass fiber composites can be used in less demanding regions. This approach maximizes performance while minimizing material costs, making hybrid composites an attractive option for a wide range of vehicles.
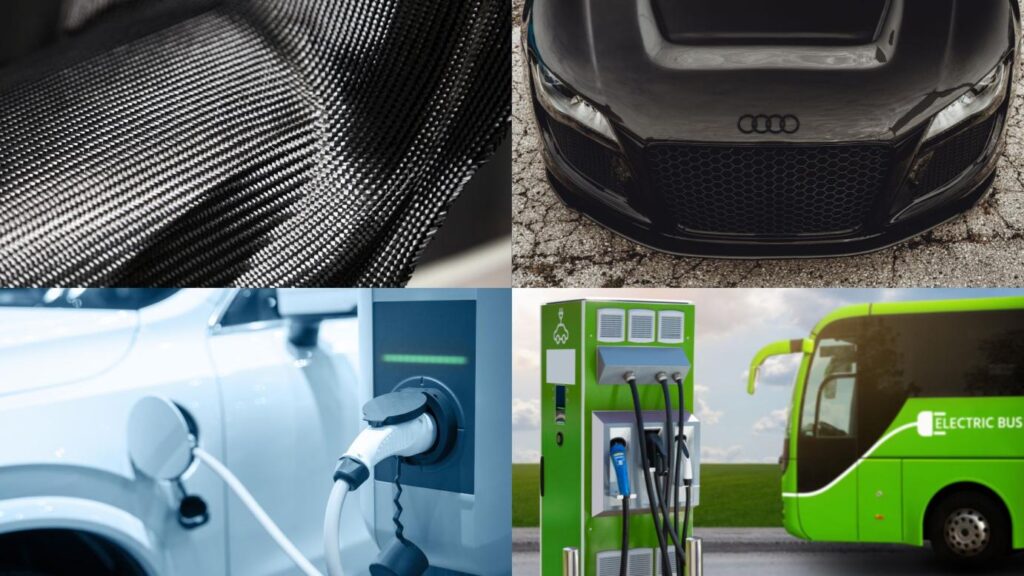
Sustainable Composite Solutions: Towards a Greener Future
In response to increasing environmental concerns, the automotive industry has been actively seeking sustainable composite solutions. Bio-based resins derived from renewable sources, such as plant oils and lignin, are gaining attention as a greener alternative to petroleum-based resins. These bio-based resins offer similar performance characteristics while reducing the carbon footprint associated with composite manufacturing.
Furthermore, the development of recycling and repurposing techniques for composite materials is gaining momentum. Researchers and industry players are exploring innovative methods to efficiently recycle composite components, reducing waste and promoting a circular economy.
The advancements and breakthroughs in composite material technology have propelled the automotive industry into an era of unprecedented innovation. From the increasing accessibility of carbon fiber composites to the integration of advanced manufacturing techniques and the development of hybrid and sustainable solutions, composite materials continue to redefine the possibilities in vehicle design, performance, and sustainability.
As research and development efforts persist, we can anticipate further advancements in composite materials, including enhanced strength, improved manufacturing efficiency, and increased recyclability. The marriage of composite material technology with emerging trends such as electric vehicles, autonomous driving, and connectivity will shape the future of automotive design and manufacturing, paving the way for a more sustainable, efficient, and exciting automotive landscape.
Impact of Composite Materials on Automotive Design and Performance: Redefining the Driving Experience
The automotive industry has witnessed a remarkable transformation with the advent of composite materials. These advanced materials, consisting of a combination of fibers and matrices, have revolutionized automotive design and performance. In this article, we delve into the profound impact of composite materials on the way vehicles are designed and how they perform on the road, elevating the driving experience to new heights.
Lightweight Design for Enhanced Performance:
Composite materials, such as carbon fiber composites, offer a remarkable strength-to-weight ratio, significantly lighter than traditional materials like steel or aluminum. By incorporating composite materials into vehicle structures, automakers can achieve substantial weight reduction without compromising structural integrity or safety.
The lightweight nature of composites has a profound impact on performance. Vehicles equipped with composite components exhibit improved acceleration, agility, and handling characteristics. The reduced mass allows for faster and more precise response to driver inputs, resulting in a thrilling driving experience.
Improved Fuel Efficiency and Range:
One of the most significant advantages of using composite materials in automotive design is their contribution to fuel efficiency and range in both conventional and electric vehicles. The reduced weight of composite structures decreases the energy required for propulsion, resulting in improved fuel economy and extended driving range.
In electric vehicles (EVs), the lightweight properties of composite materials play an even more vital role. By reducing the overall weight, composite components contribute to increased battery efficiency, allowing for longer electric range and improved overall performance.
Flexibility in Design and Styling:
Composite materials offer unparalleled design flexibility, allowing automakers to push the boundaries of creativity and aesthetics. Unlike traditional materials that have limitations in shape and formability, composites can be molded into complex and intricate shapes, giving designers the freedom to create visually striking vehicles.
This design flexibility opens up new possibilities in vehicle styling, enabling sleeker profiles, sharper lines, and more aerodynamic forms. The use of composite materials in body panels, such as carbon fiber hoods or roof panels, enhances the overall visual appeal while reducing weight.
Enhanced Strength and Structural Integrity:
Composite materials possess excellent strength characteristics, making them an ideal choice for critical automotive components. The high stiffness and resistance to deformation offered by composites contribute to improved structural integrity, especially in areas prone to impact or collision.
The integration of composite materials in vehicle structures, such as chassis and frames, enhances safety by providing enhanced protection to occupants. Composite components absorb and dissipate energy more effectively during a crash, minimizing the risk of injury and improving overall crashworthiness.
Noise and Vibration Reduction:
Composite materials offer inherent damping properties, effectively reducing noise and vibration within the vehicle cabin. By utilizing composites in the construction of body panels, acoustic insulation, and interior components, automakers can create a quieter and more refined driving environment.
Reducing noise and vibration enhances the overall comfort and pleasure of the driving experience. Passengers can enjoy a tranquil and serene ambiance, free from the disturbances typically associated with road and engine noise.
The impact of composite materials on automotive design and performance cannot be overstated. These advanced materials have reshaped the way vehicles are engineered, delivering lightweight designs, improved fuel efficiency, and exceptional strength. From enhanced driving dynamics to increased safety and refined comfort, composite materials have elevated the driving experience to new heights.
As the automotive industry continues to push the boundaries of innovation, we can expect further advancements in composite materials, leading to even more remarkable improvements in vehicle design, performance, and sustainability. With composite materials as a driving force, the future of automotive engineering holds endless possibilities, setting the stage for a new era of intelligent, efficient, and exhilarating mobility.
Carbon Fiber Composites: Powering Automotive Innovation
In the ever-evolving automotive industry, the quest for lightweight yet robust materials has led to the emergence of carbon fiber composites. With their exceptional strength and lightness, carbon fiber composites have revolutionized vehicle design, offering a multitude of advantages over traditional materials. In this article, we explore the properties, characteristics, and wide-ranging applications of carbon fiber composites in the automotive industry.
Properties and Characteristics:
Carbon fiber composites are composed of carbon fibers embedded in a matrix material, commonly epoxy resin. These composites are characterized by their outstanding mechanical properties that arise from the unique structure of carbon fibers.
a) High Strength-to-Weight Ratio: Carbon fibers are incredibly strong, exhibiting tensile strengths up to 10 times higher than steel, while being significantly lighter. This exceptional strength-to-weight ratio makes carbon fiber composites an ideal choice for lightweighting applications in automobiles.
b) Rigidity and Stiffness: Carbon fibers possess high rigidity and stiffness, offering superior resistance to deformation under applied loads. This property contributes to the overall structural integrity of vehicles, improving handling, stability, and control.
c) Corrosion Resistance: Unlike metals, carbon fiber composites are inherently corrosion-resistant. This characteristic makes them highly suitable for automotive applications, as it eliminates concerns related to rust and degradation over time.
d) Thermal Conductivity: Carbon fiber composites exhibit low thermal conductivity, which means they do not readily conduct heat. This property allows for better thermal management in vehicle components, reducing the risk of heat-related damage and improving overall efficiency.
Applications in the Automotive Industry:
Carbon fiber composites find extensive use in various automotive applications, offering unparalleled performance and design opportunities.
a) Structural Components: One of the primary applications of carbon fiber composites is in the manufacturing of structural components. From car frames and chassis to suspension components, carbon fiber composites provide exceptional strength while significantly reducing weight. This reduction in mass translates to improved fuel efficiency, better handling, and enhanced overall performance.
b) Body Panels: Carbon fiber composites are widely employed in the production of body panels, such as hoods, roofs, and fenders. By using carbon fiber composites for these exterior components, automakers can achieve weight reduction while maintaining or even enhancing vehicle aesthetics.
c) Interior Components: Carbon fiber composites have also found their way into the interior of vehicles, adding a touch of luxury and sophistication. From dashboard trims and center consoles to seat frames and door panels, carbon fiber composites offer a lightweight alternative without compromising on strength or comfort.
d) Performance Enhancements: Carbon fiber composites are utilized in performance-oriented vehicles to improve aerodynamics and optimize weight distribution. Components such as spoilers, diffusers, and air intake systems benefit from the lightweight and high-strength properties of carbon fiber composites, resulting in improved stability, downforce, and overall driving dynamics.
e) Electric Vehicles (EVs): The lightweight nature of carbon fiber composites is particularly advantageous in electric vehicles. By reducing the weight of EVs, carbon fiber composites contribute to extended driving range and improved battery efficiency, addressing two critical factors in electric vehicle adoption.
Carbon fiber composites have revolutionized the automotive industry by offering a compelling combination of strength, lightness, and versatility. These advanced materials have reshaped vehicle design, enabling automakers to achieve weight reduction, improve fuel efficiency, and enhance overall performance. From structural components to body panels and interior trims, carbon fiber composites have become an integral part of automotive innovation.
As technology continues to advance, the cost-effectiveness and production efficiency of carbon fiber composites are improving, making them increasingly accessible for broader automotive applications. The adoption of carbon fiber composites paves the way for a new generation of vehicles that are not only more fuel-efficient but also environmentally friendly.
With ongoing research and development, the potential for carbon fiber composites in the automotive industry is limitless. As automakers strive for continuous improvement, carbon fiber composites will undoubtedly play a pivotal role in shaping the future of mobility, propelling us toward a more sustainable and exhilarating driving experience.
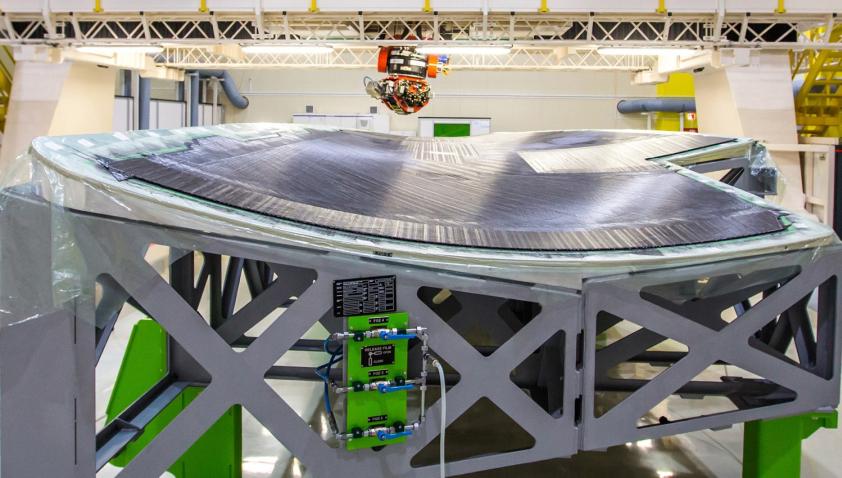
Glass Fiber Composites: Enhancing Automotive Performance and Versatility
Properties and Characteristics:
In the realm of composite materials, glass fiber composites have emerged as a vital component in the automotive industry. With their exceptional strength, versatility, and cost-effectiveness, glass fiber composites have revolutionized vehicle design and manufacturing. In this article, we delve into the properties, characteristics, and diverse applications of glass fiber composites in the automotive sector.
Glass fiber composites, also known as fiberglass composites, are composed of fine glass fibers embedded in a matrix material, typically a polymer resin. These composites possess several notable properties and characteristics that make them a preferred choice in automotive applications.
a) High Strength: Glass fibers offer excellent tensile strength and stiffness, allowing them to withstand high loads and resist deformation. This strength contributes to the overall structural integrity of automotive components, ensuring durability and longevity.
b) Lightweight: Despite their high strength, glass fiber composites are relatively lightweight compared to traditional materials such as steel or aluminum. This characteristic contributes to weight reduction in vehicles, leading to improved fuel efficiency and enhanced performance.
c) Thermal and Electrical Insulation: Glass fiber composites exhibit excellent thermal and electrical insulation properties. This feature makes them suitable for various automotive applications where thermal management and electrical insulation are critical, such as in engine compartments and electrical systems.
d) Corrosion Resistance: Unlike metals, glass fiber composites are inherently corrosion-resistant, providing an advantage in harsh environmental conditions. This resistance to corrosion ensures the longevity and reliability of automotive components, even when exposed to moisture or chemicals.
Applications in the Automotive Industry:
Glass fiber composites find a wide range of applications in the automotive industry, offering numerous benefits and opportunities for innovation.
a) Body Panels: Glass fiber composites are extensively used in the manufacturing of body panels, including hoods, doors, fenders, and trunk lids. These composites provide lightweight alternatives to traditional materials, contributing to weight reduction and improved fuel efficiency. Additionally, glass fiber composites offer design flexibility, enabling automakers to create complex shapes and contours for enhanced aesthetics.
b) Interior Components: Glass fiber composites are utilized in interior components such as door panels, dashboards, and console trims. The lightweight nature of these composites allows for reduced vehicle mass, leading to improved energy efficiency. Moreover, the versatility of glass fiber composites enables designers to achieve visually appealing textures, finishes, and customizable designs.
c) Reinforcement: Glass fiber composites are commonly used as reinforcement materials in automotive applications. They are incorporated into various components, including suspension systems, chassis structures, and engine mounts, to enhance strength and rigidity. The addition of glass fiber composites improves the overall structural integrity of vehicles, resulting in better handling, stability, and safety.
d) Sound and Vibration Damping: Glass fiber composites exhibit excellent sound and vibration damping properties. This characteristic makes them suitable for reducing noise and vibration in automotive interiors, providing a quieter and more comfortable driving experience.
Environmental Considerations:
Glass fiber composites offer certain environmental benefits in the automotive industry. They are recyclable, making them an eco-friendly choice compared to some other materials. Recycling glass fiber composites can help reduce waste and minimize the environmental impact of automotive manufacturing.
Glass fiber composites have significantly influenced automotive design and manufacturing, providing a lightweight, strong, and cost-effective solution for various applications. From body panels and interior components to reinforcement and noise reduction, glass fiber composites play a crucial role in enhancing vehicle performance, efficiency, and aesthetics.
As the automotive industry continues to evolve, the demand for glass fiber composites is expected to grow. Ongoing advancements in manufacturing techniques and material formulations will further expand their potential in creating lighter, safer, and more sustainable vehicles. The versatility and remarkable properties of glass fiber composites make them an indispensable tool for automakers, driving innovation and shaping the future of the automotive industry.
Natural Fiber Composites: Sustainable Solutions for Automotive Applications
As sustainability and eco-consciousness become increasingly important in the automotive industry, natural fiber composites have emerged as a viable alternative to traditional materials. These composites, derived from renewable resources, offer a unique combination of strength, lightweight, and environmental benefits. In this article, we explore the properties, characteristics, and applications of natural fiber composites in the automotive sector.
Properties and Characteristics:
Natural fiber composites are composed of a matrix material, typically a polymer resin, reinforced with natural fibers obtained from sources such as flax, hemp, jute, sisal, and kenaf. These composites possess several noteworthy properties and characteristics that make them attractive for automotive applications.
a) Renewable and Sustainable: The use of natural fibers in composites offers a sustainable alternative to synthetic materials. Natural fibers are derived from plant sources and are biodegradable, reducing the environmental impact of automotive production and end-of-life disposal.
b) High Strength-to-Weight Ratio: Natural fibers possess excellent tensile strength, making them suitable for reinforcing composite materials. Despite their relatively low density, natural fiber composites exhibit a high strength-to-weight ratio, contributing to lightweight vehicle components and improved fuel efficiency.
c) Good Acoustic and Thermal Insulation: Natural fiber composites offer superior acoustic and thermal insulation properties, reducing noise and heat transfer within the vehicle. This feature enhances passenger comfort and energy efficiency.
d) Low Carbon Footprint: The production of natural fiber composites requires significantly less energy compared to traditional materials like steel or carbon fiber. This lower energy consumption results in reduced greenhouse gas emissions, further contributing to the sustainability of automotive manufacturing.
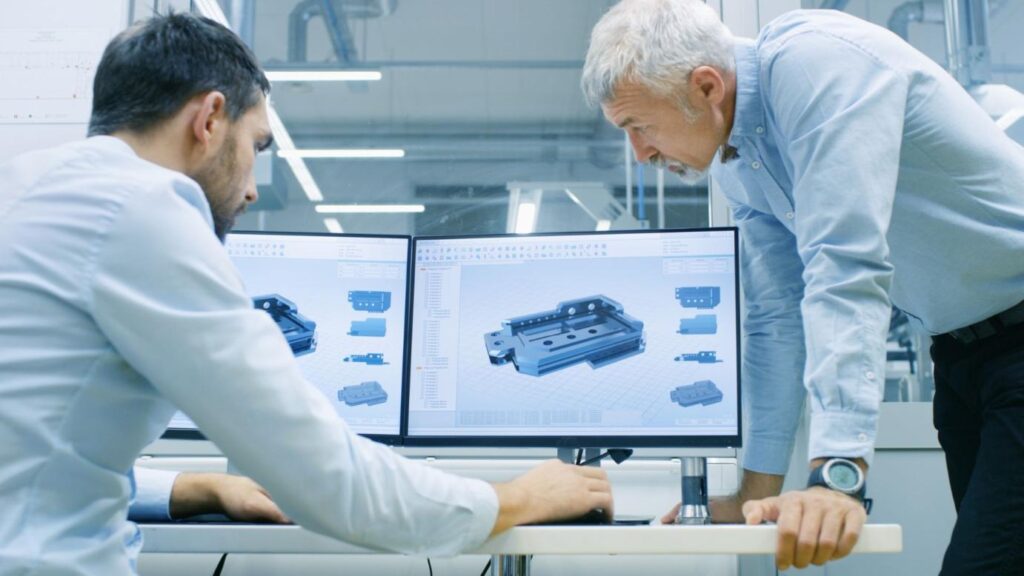
Applications in the Automotive Industry:
Natural fiber composites find a range of applications in the automotive industry, offering benefits in terms of weight reduction, sustainability, and aesthetics.
a) Interior Components: Natural fiber composites are used in the production of various interior components such as door panels, seat backs, and trim pieces. These composites provide a visually appealing and environmentally friendly alternative to synthetic materials, adding a touch of natural elegance to the vehicle’s interior.
b) Structural Components: Natural fiber composites are also employed in structural components like load-bearing beams and panels. The high strength and lightweight nature of these composites contribute to the overall structural integrity of the vehicle while reducing its weight and enhancing fuel efficiency.
c) Noise Reduction: Natural fiber composites exhibit excellent sound absorption properties, making them ideal for reducing noise and vibrations in the cabin. By incorporating these composites in automotive components, manufacturers can create a quieter and more comfortable driving experience.
d) Battery Enclosures: With the growing popularity of electric and hybrid vehicles, natural fiber composites are being explored for use in battery enclosures. These composites provide electrical insulation, thermal stability, and lightweight characteristics, ensuring the safety and performance of the battery system.
Advantages and Considerations:
Natural fiber composites offer several advantages for automotive applications. They are renewable, biodegradable, and have a lower environmental impact compared to traditional materials. Additionally, the use of natural fibers can contribute to weight reduction, improved fuel efficiency, and enhanced passenger comfort.
However, there are also considerations when using natural fiber composites. These composites may have lower mechanical properties compared to other reinforcement options, and their performance can be influenced by environmental factors such as moisture absorption and UV degradation. Manufacturers need to carefully select the appropriate natural fibers, resin systems, and processing techniques to ensure optimal performance and durability.
Natural fiber composites represent a sustainable and innovative solution for the automotive industry, offering a balance between performance, environmental consciousness, and aesthetic appeal. As the demand for greener automotive materials continues to rise, natural fiber composites have the potential to revolutionize vehicle design and manufacturing, contributing to a more sustainable and eco-friendly future. By harnessing the power of nature, automakers can create vehicles that are not only efficient and high-performing but also in harmony with the environment.
Unleashing the Potential: Benefits and Advantages of Composite Materials in the Automotive Industry
Composite materials have revolutionized the automotive industry, offering a wide range of benefits and advantages over traditional materials like steel and aluminum. With their unique combination of strength, lightness, and versatility, composites have become a preferred choice for automakers. In this article, we delve into the numerous advantages that composite materials bring to the automotive sector, paving the way for enhanced performance, efficiency, and design possibilities.
Weight Reduction and Fuel Efficiency:
One of the most significant advantages of composite materials in the automotive industry is their ability to achieve substantial weight reduction. Composites are inherently lightweight and have a high strength-to-weight ratio, allowing vehicles to shed excess pounds without compromising structural integrity. This weight reduction translates into improved fuel efficiency, reducing energy consumption and greenhouse gas emissions. By employing composites, automakers can create vehicles that are lighter, more aerodynamic, and eco-friendly.
Enhanced Strength and Durability:
Composite materials possess exceptional strength and durability properties, surpassing those of traditional materials. The fibers embedded within the composite matrix reinforce the structure, providing high tensile and impact strength. This enhanced strength allows for the design of lighter yet robust vehicle components, ensuring improved safety and longevity. Composite materials exhibit resistance to corrosion, weathering, and chemical degradation, making them ideal for withstanding harsh environmental conditions and extending the lifespan of automotive parts.
Design Flexibility and Aesthetics:
Composites offer unparalleled design flexibility, enabling automakers to create innovative and visually appealing vehicles. The moldability and formability of composite materials allow for complex shapes, curves, and contours that are challenging to achieve with conventional materials. This design freedom empowers designers to push the boundaries of automotive aesthetics, resulting in sleek, aerodynamic profiles and striking visual impressions. Composite materials can be customized to meet specific design requirements, giving automakers the opportunity to differentiate their vehicles and create a unique brand identity.
Noise and Vibration Reduction:
The exceptional damping properties of composite materials make them effective in reducing noise and vibration levels within vehicles. The ability of composites to absorb and dampen vibrations results in a quieter and more comfortable cabin environment for passengers. By minimizing noise disturbances, composites enhance the overall driving experience and contribute to a sense of luxury and refinement.
Corrosion Resistance:
Unlike traditional materials such as steel, composites are inherently corrosion-resistant. This property makes them well-suited for automotive applications, particularly in regions with high humidity or exposure to road salt. By utilizing composites, automakers can mitigate corrosion-related issues, reducing maintenance and repair costs while ensuring the longevity and appearance of vehicle components.
The benefits and advantages of composite materials in the automotive industry are undeniable. From weight reduction and fuel efficiency to enhanced strength, durability, and design flexibility, composites have reshaped the way vehicles are engineered and manufactured. As the industry continues to strive for sustainability, performance, and innovation, composite materials will play a pivotal role in driving the automotive revolution forward. With their transformative properties, composites are propelling the industry towards a future of lighter, greener, and more advanced vehicles.
Reinforcing the Automotive Structure: Composite Materials in Automotive Body Structures
In the automotive industry, the structural integrity of vehicles is of paramount importance. The choice of materials used in the construction of automotive body structures significantly impacts safety, performance, and overall vehicle quality. Composite materials have emerged as a game-changer in this regard, offering unique properties that can revolutionize the way vehicles are designed, manufactured, and experienced. In this chapter, we explore the crucial role of composite materials in automotive body structures, including car frames, chassis, body panels, and crash safety.
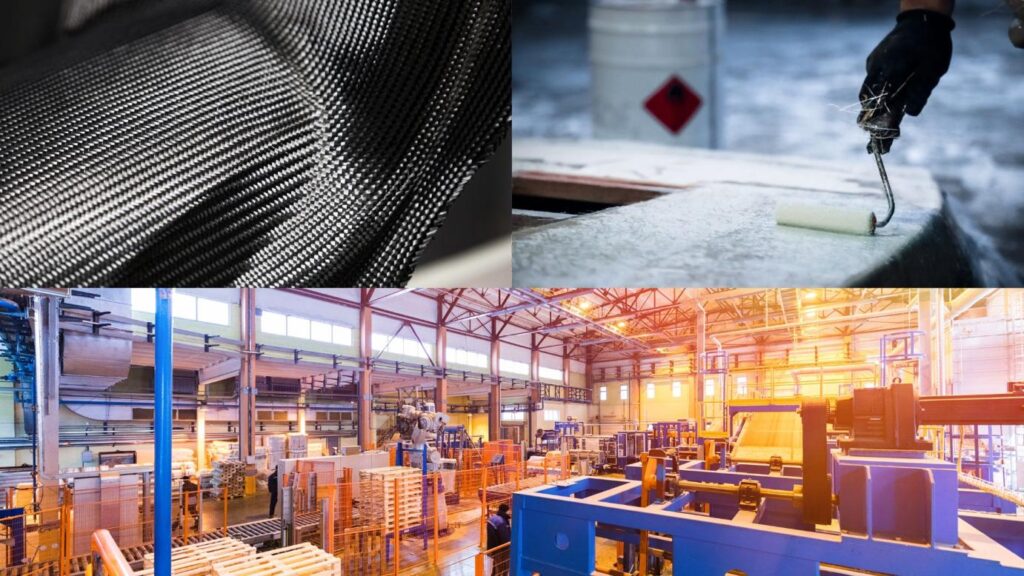
Composite Materials in Car Frames and Chassis:
Car frames and chassis are the backbone of a vehicle, providing structural strength and support. Traditionally, steel has been the primary material used for these critical components. However, the automotive industry is increasingly turning to composite materials for their exceptional strength-to-weight ratio and design flexibility. Composite frames and chassis offer higher rigidity and reduced weight compared to their steel counterparts. This translates into improved vehicle dynamics, handling, and fuel efficiency. Furthermore, composite materials dampen vibrations and contribute to a smoother and more comfortable ride.
Application of Composite Materials in Body Panels:
Body panels play a vital role in the aesthetics, aerodynamics, and overall performance of a vehicle. Composite materials have opened up new possibilities in terms of design, allowing for sleek contours and unique styling elements. Composite body panels offer several advantages over traditional materials. They are lightweight, which reduces vehicle weight and improves fuel efficiency. Additionally, composites can be molded into complex shapes and integrated with other components, providing seamless and aerodynamically efficient surfaces. Composite body panels also exhibit excellent impact resistance, reducing the risk of denting or damage during minor collisions or parking incidents.
The Role of Composite Materials in Crash Safety:
Ensuring occupant safety is a top priority in the automotive industry. Composite materials have proven to be highly effective in enhancing crash safety performance. Their energy-absorbing properties help dissipate impact forces, minimizing the transfer of kinetic energy to the vehicle occupants. Composite structures can be designed to crumple strategically during a crash, absorbing and redirecting energy away from the passenger compartment. This feature reduces the risk of injury and increases the likelihood of survival in the event of an accident. Additionally, the lightweight nature of composites contributes to improved handling and maneuverability, enhancing the overall safety of the vehicle.
The integration of composite materials in automotive body structures has revolutionized the industry, offering a range of benefits in terms of performance, safety, and design. From car frames and chassis to body panels and crash safety, composites have reshaped the way vehicles are constructed and experienced. The lightweight, high-strength properties of composite materials have led to advancements in vehicle dynamics, fuel efficiency, and occupant safety. As the automotive industry continues to innovate and strive for excellence, composite materials will play an increasingly vital role in shaping the vehicles of the future, reinforcing their structures and raising the bar for performance and safety standards.
Elevating Interior Comfort and Style: Composite Materials in Automotive Interior Components
When it comes to the interior of a vehicle, comfort, aesthetics, and functionality are key considerations. The use of composite materials in automotive interior components has significantly transformed the way we experience the inside of a vehicle. In this chapter, we delve into the diverse applications of composite materials in various interior components, such as seating systems, dashboard and instrument panels, door panels, and trims. We explore how composites enhance the overall interior design, provide comfort, and contribute to a more enjoyable driving experience.
Composite Materials in Seating Systems:
Seating systems are critical for driver and passenger comfort during short commutes and long journeys alike. Composite materials have brought about remarkable advancements in seating design and functionality. Composites offer high strength-to-weight ratios, allowing for the creation of lightweight yet durable seat structures. They enable designers to incorporate ergonomic features, ensuring optimal support and posture for occupants. Moreover, composite materials offer excellent vibration damping properties, reducing the transmission of road-induced vibrations to the seats and enhancing overall comfort.
Application of Composites in Dashboard and Instrument Panels:
The dashboard and instrument panels are central to the driver’s experience, providing vital information and controls. Composite materials have revolutionized these components, enabling sleek and visually appealing designs. Composites offer design flexibility, allowing for the integration of various shapes, textures, and finishes. They also provide excellent heat and sound insulation, enhancing the overall cabin comfort. Additionally, composites are resistant to warping and fading, ensuring long-lasting aesthetics and functionality.
Composite Materials in Door Panels and Trims:
Door panels and trims contribute to the overall aesthetics and functionality of the vehicle’s interior. Composite materials have enabled designers to create lightweight and stylish door panels that offer enhanced durability and impact resistance. Composites also provide excellent acoustic properties, reducing noise transmission from the outside environment into the cabin. Furthermore, composite trims offer a wide range of design options, allowing for customization and personalization to meet the preferences of individual vehicle owners.
Composite materials have revolutionized the interior components of automobiles, enhancing comfort, style, and functionality. From seating systems that prioritize ergonomic support to dashboard and instrument panels that offer sleek designs and information accessibility, composites have elevated the driving experience. Additionally, composite materials have facilitated the creation of lightweight, durable, and visually appealing door panels and trims that contribute to overall cabin aesthetics. As the automotive industry continues to push boundaries in interior design, composite materials will remain a driving force in shaping the future of automotive interiors, ensuring that comfort, style, and functionality go hand in hand for every vehicle occupant.
Unleashing Performance and Efficiency: Composite Materials in Automotive Powertrain and Suspension Systems
The powertrain and suspension systems of a vehicle play a crucial role in determining its performance, efficiency, and handling characteristics. In this chapter, we explore the significant impact of composite materials on these critical automotive systems. From engine components to transmission parts and suspension elements, composite materials have revolutionized the way vehicles perform on the road. Join us as we delve into the benefits and applications of composites in automotive powertrain and suspension systems.
Use of Composite Materials in Engines and Transmissions:
The heart of any vehicle is its engine, and composite materials have found their way into various engine components, unlocking a range of benefits. One prominent application is the use of composites in intake manifolds, which can provide weight reduction, improved airflow, and enhanced thermal management. Additionally, composite materials have been employed in valve covers, oil pans, and cylinder head covers, offering weight savings and reducing noise and vibration. In transmission systems, composites are utilized in components such as clutch plates, gears, and shafts, resulting in reduced weight and enhanced performance.
Application of Composites in Suspension Systems:
The suspension system is vital for a vehicle’s ride quality, handling, and stability. Composite materials have made significant contributions to suspension systems, offering various advantages. Composite springs, for example, provide weight reduction while maintaining the required stiffness and durability. These lightweight springs result in improved suspension performance, reduced unsprung mass, and enhanced fuel efficiency. Additionally, composite anti-roll bars offer increased strength and rigidity compared to traditional steel bars, leading to enhanced cornering capabilities and improved handling.
Benefits of Composites in Powertrain Components:
The use of composite materials in powertrain components extends beyond engines and transmissions. Composites find application in components such as drive shafts, engine mounts, and bearing housings, offering substantial benefits. Composite drive shafts provide weight savings, reducing rotational inertia and improving throttle response. Engine mounts made from composites offer improved vibration isolation, enhancing the overall comfort and refinement of the vehicle. Furthermore, composite bearing housings provide weight reduction, increased durability, and improved lubrication characteristics.
Composite materials have revolutionized the performance and efficiency of automotive powertrain and suspension systems. From engine components to suspension elements, composites offer weight reduction, enhanced durability, improved thermal management, and superior performance characteristics. By incorporating composite materials into these critical systems, automakers can unlock higher levels of performance, fuel efficiency, and driving pleasure. As the automotive industry continues to embrace innovative technologies, composite materials will play an increasingly significant role in shaping the future of powertrain and suspension systems, ensuring vehicles are not only powerful but also efficient and dynamic on the road.
Embracing Sustainability: Composite Materials in Automotive Electric and Hybrid Vehicles
As the world shifts towards a greener future, electric and hybrid vehicles have gained significant traction in the automotive industry. In this chapter, we explore the pivotal role of composite materials in advancing the development of electric and hybrid vehicles. These innovative materials have the potential to revolutionize the design, performance, and sustainability of these eco-friendly automobiles. Join us as we delve into the integration of composites in electric vehicle (EV) design, their application in battery systems, and their role in shaping the EV charging infrastructure.
Integration of Composite Materials in Electric Vehicle Design:
The unique properties of composite materials have made them an ideal choice for electric vehicle design. Composites offer high strength-to-weight ratios, enabling automakers to construct lightweight vehicle structures without compromising on safety or performance. From the chassis and body panels to the interior components, composites provide design flexibility, allowing for aerodynamic shapes and sleek aesthetics. The integration of composite materials in electric vehicle design contributes to increased range, improved energy efficiency, and enhanced overall performance.
Role of Composites in Battery Systems and Enclosures:
The battery is the heart of an electric vehicle, and composite materials have a significant impact on its performance, safety, and longevity. Composites are used in battery enclosures to provide structural integrity, protection against external impacts, and thermal management. By using composites, automakers can create lightweight and durable battery enclosures that safeguard the battery pack while minimizing weight penalties. Additionally, composites can be employed in battery cell casings, modules, and connectors, contributing to improved energy density, increased safety, and extended battery life.
Application of Composites in EV Charging Infrastructure:
The growth of electric vehicles necessitates the development of a robust charging infrastructure. Composite materials play a vital role in this area by offering innovative solutions for charging stations and components. Composites can be used to manufacture lightweight and durable charging station structures, ensuring their long-term reliability and resistance to environmental conditions. Additionally, composites can be employed in charging cables and connectors, providing efficient power transmission and reducing weight. The integration of composites in the EV charging infrastructure contributes to the expansion of electric mobility while promoting sustainability.
Composite materials are driving the sustainability revolution in the automotive industry, particularly in the realm of electric and hybrid vehicles. From enhancing vehicle design and performance to improving battery systems and enabling efficient charging infrastructure, composites play a vital role in shaping the future of sustainable transportation. As the demand for electric and hybrid vehicles continues to rise, the integration of composite materials will further advance the efficiency, range, and environmental friendliness of these automobiles. By embracing composite materials, automakers are paving the way for a greener and more sustainable future of transportation.
Overcoming Challenges: Composite Materials in the Automotive Industry
While composite materials offer numerous benefits and advantages in the automotive industry, their widespread adoption does not come without challenges. In this chapter, we explore the various obstacles faced when using composite materials and discuss potential solutions to overcome them. From cost considerations and manufacturing challenges to reparability and safety concerns, understanding and addressing these limitations is crucial for the successful integration of composites in automobiles.
Cost Considerations and Manufacturing Challenges:
One of the primary challenges associated with composite materials is their cost. Compared to traditional materials like steel and aluminum, composites can be more expensive to produce, resulting in higher manufacturing costs for vehicles. However, advancements in manufacturing techniques, such as automated processes and optimized production methods, are helping to reduce costs and make composites more economically viable. Additionally, increased demand and technological advancements in composite manufacturing are expected to drive down costs over time, making them a more accessible option for automotive applications.
Reparability and Recycling of Composite Components:
Another challenge relates to the reparability and recycling of composite components. Unlike traditional materials, composites can be more complex to repair in the event of damage. Specialized skills, tools, and techniques are often required to address repairs effectively. Moreover, recycling composites can be challenging due to their heterogeneous nature and the need to separate the different materials within the composite structure. However, research and development efforts are underway to develop innovative repair techniques and recycling methods for composite materials, aiming to improve their sustainability and reduce environmental impact.
Regulatory and Safety Concerns:
The use of composite materials in automobiles requires compliance with regulatory standards and safety considerations. Automakers must ensure that composites meet specific safety requirements, such as crashworthiness and fire resistance. Additionally, regulatory bodies and organizations play a crucial role in establishing standards and guidelines for the use of composite materials in the automotive industry. Collaborative efforts between industry stakeholders, regulatory authorities, and research institutions are necessary to develop comprehensive standards that ensure the safe and reliable use of composites in vehicles.
While composite materials offer tremendous potential in revolutionizing the automotive industry, addressing the challenges they present is vital for their widespread adoption. Overcoming cost considerations through advancements in manufacturing techniques, focusing on reparability and recycling solutions, and ensuring compliance with regulatory and safety standards are key areas of focus for industry players. By actively tackling these challenges, the automotive industry can unlock the full potential of composite materials, harnessing their benefits while addressing their limitations. Through continuous innovation and collaboration, composite materials will continue to shape the future of automotive design, performance, and sustainability.
Future Trends and Innovations in Composite Materials for Automotive Applications
The automotive industry is constantly evolving, driven by advancements in technology and a growing focus on sustainability. In this chapter, we explore the future trends and innovations in composite materials that are set to shape the automotive landscape. From the development of advanced composites to the integration of smart materials and additive manufacturing, the automotive industry is poised to witness groundbreaking changes that will further enhance the performance, efficiency, and design of vehicles.
Advanced Composite Materials on the Horizon:
Researchers and engineers are continuously exploring new materials with enhanced properties to further optimize the use of composites in automobiles. Advanced composite materials, such as graphene composites, nanocomposites, and high-performance polymers, hold great promise for the future. These materials offer improved strength-to-weight ratios, enhanced durability, and enhanced thermal and electrical properties, making them ideal candidates for various automotive applications. Their integration into vehicle structures and components will result in lighter, stronger, and more efficient vehicles.
Integration of Smart Materials and Sensors:
The future of composite materials in the automotive industry lies in the integration of smart materials and sensors. Smart materials, also known as intelligent or responsive materials, have the ability to respond to external stimuli and change their properties accordingly. By incorporating smart materials into composites, vehicles can benefit from self-healing capabilities, adaptive aerodynamics, and shape-shifting structures. Additionally, the integration of sensors within composites enables real-time monitoring of structural integrity, performance, and environmental conditions, ensuring optimal vehicle safety and performance.
Impact of Automation and Additive Manufacturing:
Automation and additive manufacturing, commonly known as 3D printing, are revolutionizing the production processes in the automotive industry. These technologies offer tremendous opportunities for the fabrication of complex composite structures with high precision and efficiency. Automation streamlines the manufacturing process, reducing costs and improving consistency, while additive manufacturing allows for the creation of customized, lightweight components with intricate designs. By leveraging automation and additive manufacturing, the automotive industry can accelerate the adoption of composite materials, opening up new possibilities for design freedom and production optimization.
The future of composite materials in the automotive industry is bright and filled with exciting possibilities. Advanced composite materials, integration of smart materials and sensors, and the utilization of automation and additive manufacturing will drive significant advancements in vehicle performance, efficiency, and design. As research and development efforts continue to push the boundaries of material science and manufacturing technologies, we can expect to see lighter, safer, and more sustainable vehicles on the roads. The convergence of these innovations will not only enhance the driving experience but also contribute to a greener and more sustainable future for the automotive industry and the planet as a whole.
The Promising Future of Composite Materials in the Automotive Industry
Throughout this article, we have explored the revolutionizing impact of composite materials on the automotive industry. From their early use to advancements in technology, various types of composites, and their benefits, we have witnessed how these materials have transformed automotive design, performance, and sustainability. In this final chapter, we provide a comprehensive summary of the key points discussed, highlighting the promising future of composite materials in the automotive industry.
Composite Materials: A Game-Changer for the Automotive Industry:
Composite materials, consisting of two or more distinct components, have emerged as a game-changer for the automotive industry. They offer a unique combination of strength, lightness, and versatility that traditional materials struggle to match. By adopting composite materials, automakers can achieve significant improvements in fuel efficiency, safety, durability, and design flexibility.
Evolution and Breakthroughs in Composite Material Technology:
Over the years, composite materials have evolved from their early use in limited applications to becoming an integral part of automotive design. Breakthroughs in material technology have led to the development of advanced composites with superior properties. Carbon fiber composites, glass fiber composites, and natural fiber composites have found their way into various automotive components, ensuring lightweight construction, enhanced performance, and improved sustainability.
Benefits and Advantages of Composite Materials:
Composite materials offer a multitude of benefits and advantages for the automotive industry. By reducing the weight of vehicles, composites contribute to improved fuel efficiency, reduced emissions, and increased range in electric and hybrid vehicles. Their inherent strength and durability enhance crash safety and structural integrity, while design flexibility allows for innovative and aesthetically pleasing vehicle designs. Moreover, composites provide noise and vibration reduction, corrosion resistance, and the potential for recyclability, contributing to a more sustainable automotive industry.
Applications of Composite Materials in Automotive Components:
Composite materials find extensive applications in various automotive components. They are used in car frames, chassis, body panels, and interior components such as seating systems, dashboard and instrument panels, and door panels. Composites also play a crucial role in powertrain and suspension systems, improving performance, efficiency, and overall driving experience.
Future Trends and Innovations:
The future of composite materials in the automotive industry is poised for even greater advancements. Researchers are exploring advanced materials, integrating smart technologies and sensors, and leveraging automation and additive manufacturing to further enhance the properties and applications of composites. These developments will enable the creation of lightweight, high-performance vehicles with improved safety, sustainability, and user experience.
The use of composite materials in the automotive industry has transformed the way vehicles are designed, built, and perform. With their unique combination of strength, lightness, and versatility, composites offer a promising future for the automotive industry. From lightweight construction and fuel efficiency to enhanced safety and innovative design, composites continue to revolutionize the automotive landscape. As technology advances and new materials and manufacturing processes emerge, we can expect to witness further breakthroughs and exciting possibilities in the field of composite materials. The automotive industry is on a path towards a greener, more sustainable, and technologically advanced future, all made possible by the power of composite materials.
As we conclude our comprehensive exploration of composite materials in the automotive industry, it is essential to address some frequently asked questions to provide further clarity and understanding. In this chapter, we will address common inquiries related to the use, advantages, challenges, and future developments of composite materials in automobiles. Let’s dive into the FAQs and shed light on these important aspects.
FAQs:
Q1. What are composite materials?
A composite material refers to a combination of two or more distinct materials, each contributing specific properties to the overall structure. In the context of the automotive industry, composite materials typically involve reinforcing fibers, such as carbon, glass, or natural fibers, embedded in a matrix material, such as epoxy or resin.
Q2. How are composite materials used in the automotive industry?
Composite materials are used extensively in the automotive industry for various applications. They are employed in structural components like car frames, chassis, and body panels to reduce weight while maintaining strength and durability. Composites are also utilized in interior components, powertrain systems, suspension components, and even in electric vehicle battery enclosures and charging infrastructure.
Q3. What are the advantages of using composite materials in automobiles?
Composite materials offer numerous advantages in automotive applications. Some key benefits include weight reduction, leading to improved fuel efficiency and reduced emissions. Composites also provide exceptional strength-to-weight ratio, enhancing structural integrity and crash safety. They offer design flexibility, allowing for innovative and aerodynamic vehicle designs. Additionally, composites exhibit corrosion resistance, noise and vibration reduction, and potential recyclability, contributing to a more sustainable automotive industry.
Q4. Are composite materials environmentally friendly?
Composite materials have the potential to be environmentally friendly. Their lightweight nature contributes to fuel efficiency and reduced emissions, especially in electric and hybrid vehicles. Additionally, some composite materials, such as natural fiber composites, can be derived from renewable sources, further enhancing their sustainability. However, challenges related to the recycling and disposal of composite components need to be addressed to ensure their long-term environmental impact.
Q5. What are the challenges in using composite materials in the automotive industry?
There are several challenges associated with the use of composite materials in the automotive industry. One of the primary challenges is the cost of manufacturing composite components, which can be higher than traditional materials. Additionally, the reparability of composites, especially in case of damage or accidents, can be complex. Recycling composite materials is another challenge, as current processes are not as established compared to traditional materials like steel or aluminum. Lastly, regulatory and safety concerns related to the use of composite materials require careful consideration and adherence to industry standards.
Q6. What can we expect in terms of future developments in composite materials for cars?
The future of composite materials in the automotive industry holds great promise. Ongoing research and development aim to enhance the properties of composites, such as increasing their strength, reducing costs, and improving manufacturing processes. Integration of smart materials and sensors within composites can enable real-time monitoring and self-healing capabilities. Moreover, the advancement of automation and additive manufacturing techniques will facilitate faster and more efficient production of complex composite structures.
Conclusion:
Addressing common questions related to composite materials in the automotive industry helps provide a deeper understanding of their applications, advantages, challenges, and future prospects. As technology continues to evolve, composite materials will play an increasingly vital role in shaping the future of automotive design, performance, and sustainability. By addressing concerns, fostering innovation, and collaborating across industries, we can further unlock the potential of composite materials, revolutionising the automotive industry for years to come.