The mining industry relies heavily on materials that can withstand extreme operating conditions. High strength, wear resistance, corrosion resistance, fatigue strength, and impact strength are critical properties for materials used in mining applications. Composite materials made of polymers, metals, ceramics, and fibers are increasingly being used in mining due to their advantageous properties compared to traditional materials like steel and iron.
What are Composite Materials?
Composite materials are made by combining two or more materials with different properties to create a new material with enhanced overall properties. The different materials work together to give the composites increased strength, stiffness, weight savings, corrosion resistance, temperature resistance, and other benefits compared to traditional materials.
Composites are made up of:
- Polymer matrix: Plastics reinforced with fibers
- Metal matrix: Metals reinforced with fibers
- Ceramic matrix: Ceramics reinforced with fibers
The reinforcement material provides strength and stiffness, while the matrix material binds it together. Common reinforcement materials include carbon fibers, glass fibers, boron, and silicon carbide. Common matrix materials include polyester, epoxies, aluminum, titanium, and silicon carbide.
By combining different reinforcement materials and matrix materials, composites can be tailored to have specific properties needed for mining applications.
Advantages of Composites in Mining
Using composite materials in mining equipment and infrastructure provides many advantages:
- High strength: Composites have extremely high strength for their weight by incorporating strong reinforcement fibers.
- Lightweight: Composites weigh significantly less than traditional steel which reduces fuel costs.
- Wear resistance: They resist abrasion and wear even in highly abrasive environments.
- Corrosion resistance: Composites won’t rust or corrode like metals.
- Fatigue strength: They resist cyclic stresses and fatigue failure.
- Impact strength: Composites absorb impacts and resist fracture.
- Design flexibility: They can be formed into complex shapes not possible with metals.
These properties make composites ideal for the demanding conditions found in mining operations.
Applications of Composites in Mining
Composite materials are used in a wide range of mining applications:
Mining Equipment
- Drill bits: Matrix body with diamond or tungsten carbide inserts.
- Excavator buckets: Reinforced with carbon fiber. Lighter and tougher than steel.
- Haul truck beds: Made from reinforced polymers, resistant to impacts/wear.
- Conveyor belts: Reinforced with fabric plies for strength and durability.
Processing Equipment
- Piping: Corrosion resistant fiberglass pipes.
- Wear plates: Protective wear sheets made from composites.
- Scrubber tubes: Withstand abrasion from slurries.
- Cyclones: Lighter composite cyclones replace steel.
- Mills: Composite mill liners resist wear.
- Flotation cells: Composite tanks don’t corrode.
- Screens: Composite screens are rigid and corrosion free.
Composites make equipment lighter, stronger, and more durable compared to traditional steel components. This improves performance and lifetime, while reducing maintenance costs.
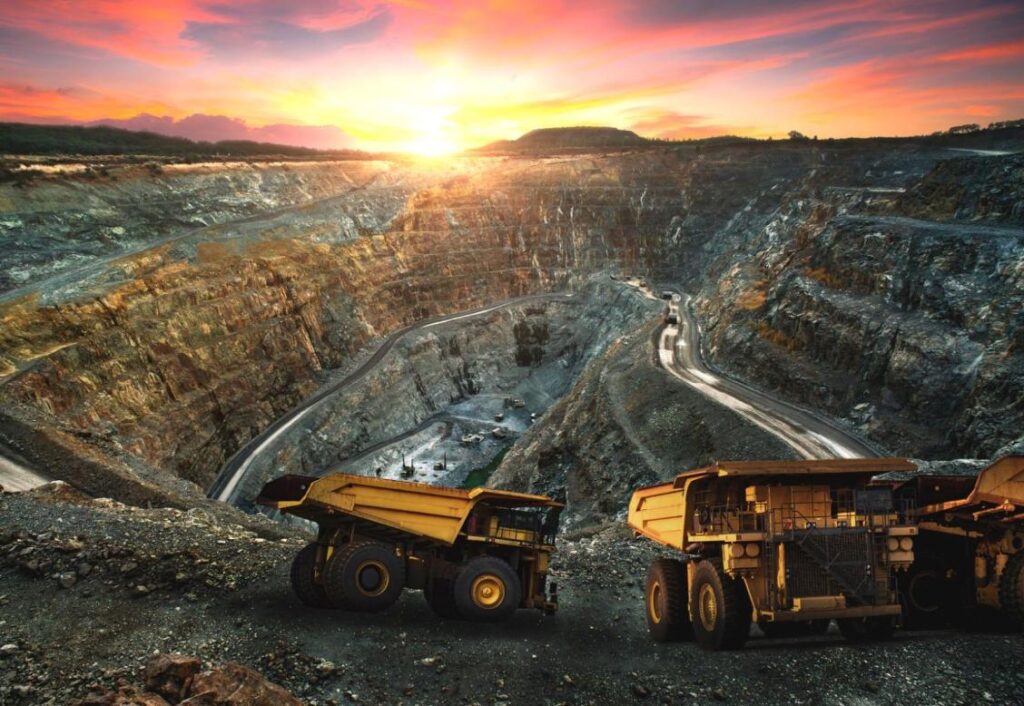
Types of Composite Materials Used in Mining
Many different composite materials are used in the mining industry. Some of the most common include:
- Fiber reinforced polymers (FRPs): Glass, carbon, aramid fibers in a polymer matrix. Used for pipes, tanks, grating, structures.
- Metal matrix composites (MMCs): Aluminum, magnesium, titanium reinforced with fibers. Used for buckets, truck beds, drill bits.
- Ceramic matrix composites (CMCs): Ceramic matrices reinforced with fibers. Used for chutes, cyclones,screens.
- Polymer concrete: Polymers reinforced with aggregates. Used for wear liners, pulleys, Rollers.
- Reinforced elastomers: Rubber reinforced with steel cords. Used for sealing products, liners.
- Sandwich composites: Two thin composite skins on core material. Used for equipment doors, panels.
Type of Composite | Typical Uses in Mining |
---|---|
Fiber reinforced polymers | Pipes, tanks, structures |
Metal matrix composites | Excavator buckets, truck beds |
Ceramic matrix composites | Chutes, cyclones, screens |
Polymer concrete | Wear liners, pulleys |
Reinforced elastomers | Seals, liners |
Sandwich composites | Equipment doors, panels |
The wide range of composite materials allows mining companies to select the optimal material for each application to maximize performance and equipment lifetime.
Fabricating Composites for Mining Equipment
Specialized fabrication techniques are used to manufacture composite components for mining applications:
- Polymer molding: Thermoset resins and fibers molded into parts.
- Filament winding: Fiber strands wound over a mandrel to form pipes, tubes.
- Pultrusion: Pulling composites through a die to make structural profiles.
- Compression molding: Composite molding using external pressure.
- Resin transfer molding: Resin injected into closed mold with fibers.
- Vacuum infusion: Drawing resin into a fiber preform.
- Machining: Cutting composites with diamond tooling.
- Bonding: Joining composite parts with structural adhesives.
Automated manufacturing methods allow high volume production of composites for the mining industry. Strict quality control and testing maintains the required mechanical properties and performance.
Design Considerations for Composite Mining Equipment
Equipment designers must consider the complex mechanical properties of composites when designing mining components:
- Composites have anisotropic properties (directionally dependent strength). Parts must be analyzed to optimize fiber orientation.
- The fatigue behavior and lifetime under cyclic loads must be modeled.
- Effects of the service environment like temperature, abrasion, and chemicals must be accounted for.
- Impact resistance and damage tolerance is important for equipment safety.
- Bonding and joints between composites parts requires specialized design.
- Manufacturability, production cost, and part size limitations must be evaluated.
Advanced computer-aided engineering tools like finite element analysis are essential to predict composite behavior and optimize designs.
Benefits of Using Composites in Mining
There are many benefits of utilizing composite materials rather than traditional metals in mining equipment:
- Increased safety: Equipment made from composites is lighter reducing risks associated with handling heavy components. Composite components are also less prone to corrosion leading to failures.
- Higher equipment availability: Composites last longer than metals, reducing downtime for repairs and replacements. This leads to increased utilization and productivity.
- Lower operating costs: Fuel consumption, maintenance, and replacement costs are reduced due to the lightweight, long-lasting nature of composites. This provides major cost savings over the life of equipment.
- Increased component life: On average, composite components last 2-3 times longer than steel components in mining applications.
- Easier repairs: Composite parts can often be patched and repaired instead of replaced entirely. This keeps equipment downtime to a minimum.
Overall, composites improve the safety, reliability, and cost-effectiveness of mining equipment compared to traditional materials. Their unique properties make them well suited to withstand the demanding conditions.
Future Outlook for Composites in Mining
The use of composite materials in the mining industry is expected to grow rapidly in the future as the benefits become more widely recognized. Some key trends include:
- Expanding use of composites beyond wear parts into structural components.
- New fiber reinforcements like basalt and carbon nanotubes to improve strength and functionality.
- Development of smart composites with integrated sensors for condition monitoring.
- Focus on eco-friendly resins such as bio-epoxies to reduce environmental impacts.
- Recycling methods for reusing fibers from retired composite components.
- More training for engineers to properly design and analyze composite mining equipment.
- Closer collaboration between mining companies, composite manufacturers, and research institutions.
As composite technology advances, mining companies have an opportunity to significantly improve their operations and reduce costs by taking advantage of these innovative new materials. Composites represent the future for equipment in the mining industry.
Frequently Asked Questions
1. What are the main benefits of using composites in mining equipment?
The main benefits of using composites in mining equipment are:
- High strength and durability – Composites last 2-3 times longer than metals in mining applications
- Lightweight – Reduces fuel consumption and risks handling heavy parts
- Corrosion resistant – Unlike metals, composites won’t rust or degrade over time
- Wear resistance – Withstand abrasive conditions better than metals
- Easier repairs – Composite parts can often be patched instead of fully replaced
2. How are composite materials made?
Composite materials are made by combining two or more material components:
- Reinforcement material – Provides strength and stiffness (e.g. fibers)
- Matrix material – Binds reinforcement together (e.g. polymers)
Common reinforcements include carbon, glass, and aramid fibers. Common matrices include polyester, epoxy, aluminum, and titanium.
3. What equipment uses composites in mining?
Some common mining equipment using composites:
- Drill bits
- Excavator buckets
- Haul truck beds
- Conveyor belts
- Piping
- Wear plates and liners
- Mills and flotation cells
4. What industries besides mining use composite materials?
Composites are used in many industries including:
- Aerospace – Aircraft structures, engine parts
- Automotive – Body panels, drive shafts
- Construction – Rebars, structural profiles
- Marine – Boat hulls, masts
- Sporting goods – Golf clubs, racquets
5. How do you fabricate composite parts?
Common fabrication methods include:
- Molding
- Filament winding
- Pultrusion
- Resin transfer molding
- Vacuum infusion
- Machining
- Bonding
6. How long do composite mining components last compared to traditional materials?
On average, properly designed composite parts last 2-3 times longer than equivalent steel parts in mining applications. For example, a composite valve box could last 5 years compared to just 2 years for a steel version.
7. Can you repair damaged composite equipment?
Yes, composite parts can often be repaired instead of replaced entirely. Some repair techniques include:
- Patching holes or gouges
- Infusing resin to rebuild lost material
- Using composite wraps to reinforce damage
- Bonding replacement fragments
8. Are composites environmentally friendly?
Composites are generally considered an environmentally progressive material since they have long lifetimes and can reduce energy consumption. Manufacturers are also developing eco-friendly resins such as bio-epoxies that reduce environmental impacts.
9. Are composites safe for mining applications?
Yes, composites can be designed to be very safe for mining use. Advantages include:
- Won’t suddenly corrode or degrade
- Less prone to impact damage
- Lighter weight reduces risks of handling
- Can integrate sensors for condition monitoring
10. Are composites expensive compared to traditional mining materials?
The initial cost of composites may be higher than metals. But the total lifetime costs are often reduced due to longer part lifetime, lower maintenance, and better performance. Switching to composites provides overall savings in the long run.
11. What is the future outlook for use of composites in mining?
The mining industry is expected to dramatically increase adoption of composites in the future as the technology advances. Key trends include:
- Use in more structural applications
- New fiber reinforcements like basalt
- Smart composites with integrated sensors
- Recycling methods for retired parts
- More training in composite design for engineers
12. What industries compete with mining for composite materials?
Other industries that heavily utilize composites include:
- Aerospace and aviation
- Automotive and motorsports
- Marine and shipbuilding
- Construction
- Alternative energy (wind turbines)
But composites suppliers continue investing to meet demand from all industries.
13. Can you easily repair composite mining equipment in the field?
Basic repairs can be done on-site, but composites typically require curing at specific pressures and temperatures for optimal properties. More complex repairs may need to be done at dedicated composite repair facilities.
14. How are sandwich composite structures used in mining?
Sandwich composites consist of two thin, stiff outer skins over a lighter core material. In mining, they are often used for:
- Equipment doors and access panels – Low weight but high stiffness
- Sound insulation panels – Absorb noise
- Guard structures – Impact protection
15. How do material engineers learn to design with composites?
Designing composites requires special training and analysis methods. Many material engineering programs now incorporate advanced composite courses into their curriculum. There are also professional training courses focused specifically on proper composite design and manufacturing.