
The mining industry is a cornerstone of global economic development, providing essential raw materials for various sectors such as construction, manufacturing, and energy production. With the growing demand for resources, mining companies are constantly seeking innovative solutions to optimize operations, increase efficiency, and reduce environmental impact. One such solution that has gained significant attention in recent years is the utilization of composite materials.
A. Overview of the Mining Industry
The mining industry encompasses the extraction and processing of valuable minerals and metals from the Earth’s crust. It involves a range of operations, including exploration, site development, extraction, transportation, and processing. Mining activities are essential for the production of various commodities such as coal, iron ore, copper, gold, and diamonds, among others. These resources serve as raw materials for numerous industries and are integral to global economic growth.
Mining operations can be divided into two main categories: surface mining and underground mining. Surface mining involves the removal of overlying soil and rock to access mineral deposits near the Earth’s surface. On the other hand, underground mining involves accessing mineral deposits that are located at significant depths through shafts or tunnels.
The mining industry operates under strict regulations and safety standards to ensure worker protection, environmental sustainability, and responsible resource management. Advancements in technology and innovative practices have played a vital role in transforming the mining sector and driving its evolution.
B. Introduction to Composite Materials and Their Applications
Composite materials are engineered materials composed of two or more constituent materials with different physical and chemical properties. These materials are combined to create a new material that possesses enhanced characteristics and performance compared to its individual components. In the context of the mining industry, composite materials offer numerous advantages over traditional materials such as steel or concrete.
Composite materials are widely known for their exceptional strength-to-weight ratio, which makes them lightweight yet durable. This property is particularly valuable in the mining industry, where heavy equipment and structures are prevalent. By utilizing composite materials, mining companies can achieve weight reduction in equipment and infrastructure, leading to increased efficiency and cost savings.
Additionally, composite materials exhibit excellent corrosion resistance, making them ideal for harsh mining environments that involve exposure to corrosive substances or extreme weather conditions. The durability of composites ensures a longer lifespan for mining equipment and structures, reducing maintenance costs and downtime.
The unique properties of composite materials also contribute to enhanced safety in the mining industry. For example, composite components can be designed to be fire-resistant, providing an additional layer of protection in case of accidents. Moreover, composites can be tailored to be non-conductive, reducing the risk of electrical hazards in mining operations.
The versatility and design freedom offered by composite materials allow for innovative solutions in the mining industry. Composite components can be custom-designed to fit specific requirements and seamlessly integrated into existing equipment and infrastructure. This flexibility opens up opportunities for optimized designs and improved performance.
In the next section, we will delve deeper into the advantages of composite materials in the mining industry, exploring their specific applications and the transformative impact they have had on mining equipment and operations.
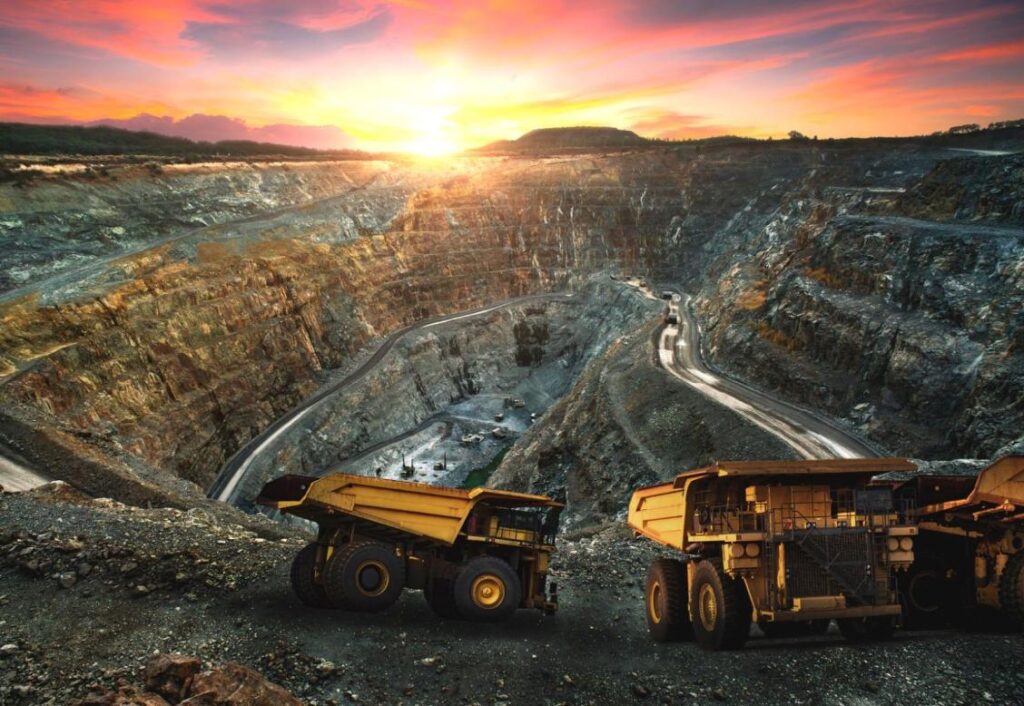
II. The Advantages of Composite Materials in Mining
Composite materials have emerged as a game-changer in the mining industry, offering a multitude of advantages that revolutionize equipment design, operational efficiency, safety, and environmental sustainability. Let’s explore these advantages in detail:
A. Lightweight and Increased Efficiency
One of the primary benefits of composite materials in mining is their remarkable lightweight nature combined with exceptional strength. Traditional materials like steel and concrete are heavy, requiring substantial energy for transportation, installation, and operation. In contrast, composite materials significantly reduce the weight of mining equipment and infrastructure, leading to improved energy efficiency and cost savings. Lighter components also minimize wear and tear on machinery, extending their lifespan and reducing maintenance requirements.
Moreover, the reduced weight of composite materials enables the use of smaller and more efficient power sources, such as electric motors, in mining equipment. This transition towards electrification in mining contributes to lower emissions, improved air quality, and a shift towards more sustainable practices.
B. Corrosion Resistance and Durability
Mining operations often take place in challenging environments where corrosion is a prevalent issue. Composite materials excel in this aspect, offering excellent resistance to corrosion, chemicals, and harsh weather conditions. Unlike traditional materials, composites do not rust, corrode, or deteriorate over time, ensuring the longevity and durability of mining equipment and structures.
By utilizing corrosion-resistant composite materials, mining companies can reduce the frequency of maintenance and replacement, leading to substantial cost savings. Additionally, the enhanced durability of composites enhances overall operational efficiency, as downtime due to repairs and maintenance is minimized.
C. Enhanced Safety and Reduced Environmental Impact
Safety is of paramount importance in the mining industry, and composite materials contribute significantly to creating safer working conditions. Composites can be engineered with specific properties to enhance safety measures. For instance, they can be designed to have fire-resistant properties, preventing the rapid spread of fires in mining operations. Non-conductive composites also reduce the risk of electrical accidents.
Furthermore, the reduced weight of composite materials translates into lower energy requirements during equipment operation. This not only enhances operational efficiency but also reduces carbon emissions and the environmental impact of mining activities. By adopting composite materials, mining companies can align with sustainability goals and regulatory requirements, promoting responsible resource extraction practices.
D. Flexibility and Design Freedom
Composite materials offer unparalleled design flexibility and freedom. They can be tailored to meet the precise requirements of mining equipment and infrastructure. Unlike traditional materials, composites can be molded into complex shapes, enabling the creation of intricate components and structures. This customization facilitates the optimization of designs for enhanced performance and efficiency.
Moreover, composite materials can be seamlessly integrated into existing mining equipment and structures, allowing for retrofitting and upgrades. This adaptability ensures compatibility with existing systems, reducing downtime during implementation and maximizing the benefits of composite materials without requiring a complete overhaul of mining operations.
In the next section, we will explore the specific applications of composite materials in the mining industry. From conveyor belts to protective gear, composites have revolutionized various aspects of mining equipment and operations.

III. Applications of Composite Materials in Mining Equipment
The remarkable properties of composite materials have found extensive applications in various aspects of mining equipment and infrastructure. Let’s explore some of the key areas where composites have revolutionized the mining industry:
A. Conveyor Belts and Conveyor Systems
Conveyor belts are vital for efficient material transportation in mining operations. By utilizing composite materials in the construction of conveyor belts, mining companies can benefit from improved performance and longevity. Composite belts offer exceptional resistance to wear, impact, and abrasion, ensuring reliable and efficient operation even in harsh environments. Additionally, their lightweight nature reduces energy consumption and minimizes strain on conveyor systems.
B. Pipes and Piping Systems
Composite materials have found wide acceptance in mining piping systems. Traditional metal pipes are susceptible to corrosion, which can lead to leaks, reduced flow rates, and increased maintenance. By employing composite pipes, mining companies can overcome these challenges. Composite pipes are highly resistant to corrosion, chemical reactions, and scaling, ensuring smooth flow rates and minimizing maintenance requirements. Furthermore, their lightweight nature makes installation and transportation easier and more cost-effective.
C. Tanks and Storage Solutions
Storage tanks play a crucial role in mining operations, and composite materials offer significant advantages in this area. Composite tanks are highly resistant to corrosion, making them suitable for storing a wide range of chemicals and fluids used in mining processes. They offer excellent structural integrity and durability, ensuring the safe storage of materials without the risk of leaks or environmental contamination. Moreover, the lightweight nature of composite tanks reduces installation costs and simplifies maintenance procedures.
D. Structural Components and Support Systems
Composite materials have revolutionized the design and construction of structural components and support systems in mining operations. From mine shaft supports to underground roof bolting, composites provide exceptional strength-to-weight ratios, enhancing the safety and stability of mining structures. Composite components can be designed to withstand extreme loads, vibrations, and seismic events, ensuring the integrity of mining infrastructure in challenging environments. Additionally, the lightweight nature of composites simplifies installation and reduces the strain on support systems.
E. Protective Gear and Personal Safety Equipment
The safety of mining personnel is a top priority, and composite materials have played a crucial role in enhancing personal safety equipment. Composite materials are used in the manufacturing of safety helmets, protective clothing, and equipment like respirators and eye protection. These materials offer excellent impact resistance, heat resistance, and electrical insulation properties, ensuring the well-being of miners in hazardous working conditions. Composite-based safety gear provides lightweight and comfortable options, enabling miners to perform their tasks effectively while minimizing the risk of injury.
In the next section, we will explore real-world case studies that highlight the successful implementation of composite materials in the mining industry. These examples demonstrate the tangible benefits and transformative potential of composites in mining equipment and operations.
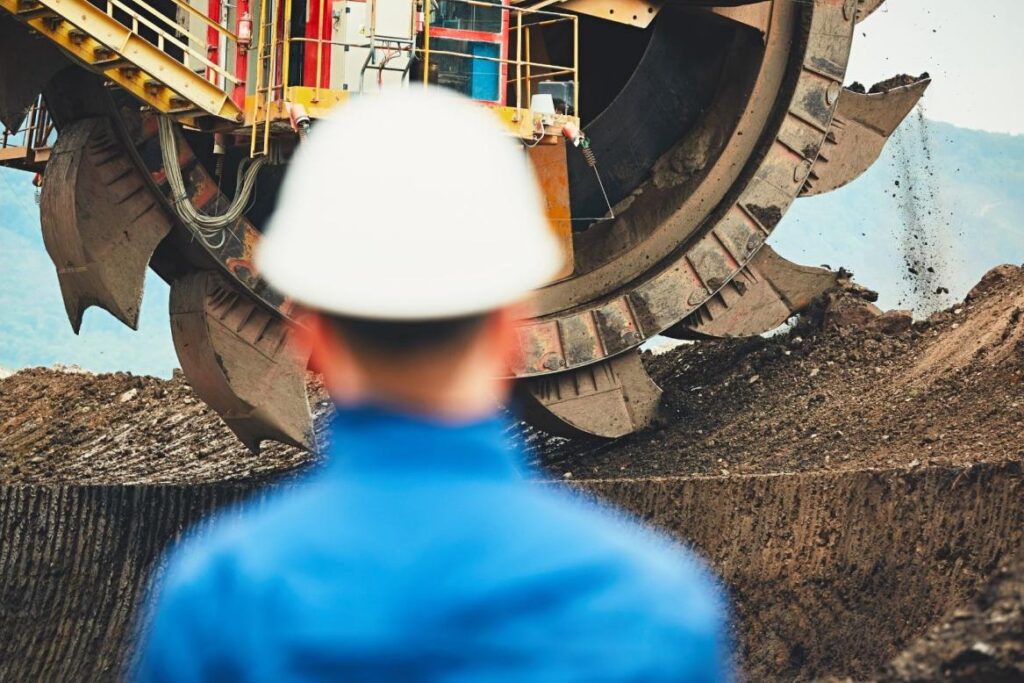
IV. Case Studies: Successful Implementation of Composite Materials in Mining
To gain a deeper understanding of the transformative impact of composite materials in the mining industry, let’s examine some real-world case studies where their implementation has resulted in significant improvements:
A. Case Study 1: Composite Conveyor Belt Revolutionizes Material Transportation
In a large-scale mining operation, a composite conveyor belt was introduced to replace traditional rubber belts. The composite belt showcased exceptional durability, wear resistance, and reduced weight, resulting in improved operational efficiency. The lightweight nature of the composite belt reduced energy consumption and strain on the conveyor system, enabling increased material transportation capacity. Furthermore, the composite material’s resistance to abrasion and impact prolonged the belt’s lifespan, significantly reducing downtime and maintenance costs. This case study exemplifies how composite materials can revolutionize material transportation in the mining industry.
B. Case Study 2: Composite Piping Systems Improve Operational Efficiency
In another mining operation, composite piping systems were implemented to replace traditional metal pipes. The use of composite pipes offered numerous advantages, including superior resistance to corrosion, chemical reactions, and scaling. This resulted in improved flow rates, reduced maintenance requirements, and enhanced overall operational efficiency. The lightweight nature of the composite pipes facilitated easier installation and transportation, leading to cost savings and streamlined processes. The case study highlights how composite materials can optimize fluid transportation in mining operations.
C. Case Study 3: Reinventing Mining Tanks with Composite Materials
A mining company sought to address the challenges associated with storage tanks by adopting composite materials. By replacing traditional metal tanks with composite ones, they achieved exceptional corrosion resistance and increased durability. The composite tanks effectively stored various chemicals and fluids used in mining processes without the risk of leaks or environmental contamination. Additionally, the lightweight nature of the composite tanks simplified installation and reduced maintenance efforts, resulting in improved operational efficiency and cost savings. This case study demonstrates the transformative potential of composite materials in storage solutions within the mining industry.
These case studies exemplify how composite materials have revolutionized specific aspects of mining operations, offering superior performance, increased durability, and enhanced efficiency. The successful implementation of composites in these scenarios showcases their significant potential for improving various facets of the mining industry.
In the next section, we will discuss the challenges and limitations associated with the use of composite materials in mining, as well as the advances in composite material technology that are driving innovation in the field.
V. Challenges and Limitations of Composite Materials in Mining
While composite materials have shown great promise in revolutionizing the mining industry, their implementation is not without challenges and limitations. It is important to understand and address these factors to ensure the successful integration of composite materials in mining operations. Let’s explore some of the key challenges and limitations:
A. Cost Considerations and Return on Investment
One of the primary challenges in adopting composite materials in mining is the initial investment cost. Compared to traditional materials, composites can be more expensive upfront due to the specialized manufacturing processes and the cost of high-performance fibers and resins. However, it’s essential to consider the long-term benefits and return on investment (ROI) that composite materials can offer. These benefits include improved operational efficiency, reduced maintenance costs, and increased lifespan, which can outweigh the initial investment and result in significant cost savings over time.
B. Maintenance and Repair Challenges
Another challenge is the maintenance and repair of composite materials in mining equipment. While composites are known for their durability and resistance to corrosion, they can still be susceptible to damage from heavy impacts, extreme temperatures, and prolonged exposure to abrasive materials. Proper maintenance protocols and repair procedures need to be established to ensure the longevity and performance of composite components. Additionally, training personnel on the proper handling and repair techniques specific to composite materials becomes crucial for efficient maintenance practices.
C. Regulatory and Certification Requirements
The mining industry is subject to various regulations and safety standards. Introducing composite materials into mining operations may require compliance with specific regulatory and certification requirements. It is necessary to ensure that composite materials used in critical applications meet the necessary standards for structural integrity, fire resistance, and other safety considerations. Collaborating with regulatory bodies and certification agencies can help streamline the process and ensure the successful integration of composite materials while maintaining compliance.
Despite these challenges and limitations, the advancements in composite material technology continue to address these concerns, driving innovation and overcoming barriers to adoption. In the next section, we will explore the latest advances in composite material technology for mining applications.
VI. Advances in Composite Material Technology for Mining Applications
To overcome the challenges and limitations associated with composite materials in the mining industry, continuous advancements in technology are paving the way for innovative solutions. Here are some of the key areas where significant progress has been made:
A. New Composite Material Formulations
Researchers and engineers are constantly developing new composite material formulations tailored specifically for mining applications. These formulations aim to enhance the mechanical properties, durability, and resistance to harsh environments. By incorporating advanced fibers, such as carbon fiber or aramid, with high-performance resins, composite materials can achieve greater strength-to-weight ratios and improved corrosion resistance. The development of new material compositions enables mining companies to explore new possibilities for lightweight, durable, and efficient equipment.
B. Innovative Manufacturing Processes
In addition to material formulations, there have been significant advancements in manufacturing processes for composite materials in the mining industry. Advanced techniques such as automated fiber placement, resin transfer molding, and filament winding enable the production of complex shapes and structures with high precision. These manufacturing processes enhance the efficiency and consistency of composite production, resulting in reliable and cost-effective mining equipment. Moreover, additive manufacturing techniques, including 3D printing, are being explored to further customize and optimize composite components.
C. Integration of Smart Technologies
The integration of smart technologies with composite materials opens up new opportunities for monitoring, maintenance, and performance optimization. Sensors embedded within composite structures can provide real-time data on structural health, temperature, and stress levels. This data can be utilized to predict maintenance needs, optimize operational parameters, and ensure the safety and reliability of mining equipment. By harnessing the power of the Internet of Things (IoT) and data analytics, mining companies can leverage composite materials as smart, connected solutions.
These advances in composite material technology are pushing the boundaries of what is possible in the mining industry. The integration of these technologies allows for stronger, lighter, and more durable mining equipment, ultimately enhancing operational efficiency, reducing downtime, and improving safety.
In the next section, we will explore the future prospects and emerging trends in the field of composite materials in mining applications.
VII. Future Prospects and Emerging Trends
The mining industry is on the cusp of significant transformations, and the future prospects for composite materials in mining applications look promising. Here are some of the emerging trends that are likely to shape the industry:
A. Automation and Robotics in Composite Material Mining Applications
Automation and robotics have already made their mark in the mining industry, improving efficiency and safety. With the integration of composite materials, these technologies are poised to revolutionize mining operations further. Automated systems can be designed to handle composite material manufacturing, inspection, and repair processes, reducing human intervention and enhancing precision. Robotic mining vehicles and drones equipped with composite components can navigate challenging terrains, perform remote inspections, and assist in hazardous tasks. The combination of automation, robotics, and composite materials will enable mining companies to achieve higher productivity, accuracy, and worker safety.
B. Integration of Composite Materials in Mining Vehicles and Machinery
Mining vehicles and machinery are crucial components of mining operations. Integrating composite materials into their design offers numerous benefits, including weight reduction, increased fuel efficiency, and improved structural integrity. Composite materials can be used in the construction of vehicle bodies, engine components, and equipment enclosures, resulting in lighter yet robust solutions. By reducing the weight of mining vehicles, companies can minimize fuel consumption and emissions, ultimately contributing to sustainability efforts. Additionally, composite materials can offer better resistance to corrosion and wear, extending the lifespan of mining equipment.
C. 3D Printing and Customization of Composite Mining Equipment
Additive manufacturing, particularly 3D printing, is rapidly evolving and holds immense potential for the mining industry. The ability to 3D print composite materials enables the customization and on-demand production of mining equipment and components. This technology allows for complex geometries, intricate designs, and optimized structures that were previously difficult to achieve using traditional manufacturing methods. With 3D printing, mining companies can quickly produce spare parts, prototypes, and even entire equipment tailored to their specific needs. This not only reduces lead times and costs but also enables rapid innovation and adaptability in the mining sector.
As the mining industry embraces these future prospects and emerging trends, composite materials will play a central role in driving innovation, efficiency, and sustainability. The combination of advanced technologies, automation, and customized solutions will unlock new possibilities for the industry, revolutionizing the way mining operations are conducted.
In the next section, we will delve into the sustainability and environmental benefits of composite materials in the mining industry.
VIII. Sustainability and Environmental Benefits of Composite Materials in Mining
The mining industry has long been associated with environmental challenges due to its resource-intensive nature. However, the integration of composite materials brings forth numerous sustainability and environmental benefits. Let’s explore how composite materials contribute to a greener and more responsible mining industry:
A. Reduction in Carbon Footprint
One of the significant environmental advantages of composite materials in mining is their ability to reduce the carbon footprint of mining operations. Traditional mining equipment and structures often rely on materials with high energy requirements during extraction, processing, and transportation. Composite materials, on the other hand, offer lightweight alternatives that require less energy for production and operation. The reduced weight of composite mining equipment translates into lower fuel consumption and emissions, thereby mitigating the industry’s environmental impact.
B. Waste Reduction and Recycling Potential
Composite materials possess excellent durability and resistance to wear, enabling them to outperform traditional materials in harsh mining environments. This durability translates into a longer lifespan for mining equipment, reducing the frequency of replacements and, consequently, the generation of waste. Additionally, composite materials can be designed for easy disassembly and recycling, allowing for the recovery of valuable components and reducing landfill waste. By embracing composite materials, mining companies can minimize waste generation and promote a more sustainable approach to resource utilization.
C. Environmental Regulations and Compliance
Governments and regulatory bodies worldwide are placing increased emphasis on environmental protection and sustainable practices in the mining industry. Composite materials offer mining companies an opportunity to align with these regulations and compliance standards. By adopting composite materials, mining operations can demonstrate their commitment to reducing environmental impact, meeting emissions targets, and promoting responsible resource extraction. Compliance with environmental regulations not only ensures long-term sustainability but also enhances the industry’s reputation and social license to operate.
As the mining industry continues to prioritize sustainability, composite materials emerge as a vital solution for minimizing the environmental footprint. The reduced carbon emissions, waste reduction, and compliance with environmental regulations make composite materials a compelling choice for responsible mining practices.
In the next section, we will explore the economic impact and cost-benefit analysis of using composite materials in the mining industry.
IX. Economic Impact and Cost-Benefit Analysis
In addition to the sustainability and environmental benefits, the adoption of composite materials in the mining industry also has significant economic implications. Let’s delve into the economic impact and cost-benefit analysis of utilizing composite materials in mining:
A. Cost Savings and Efficiency Gains
While the initial investment in composite materials may be higher than that of traditional materials, the long-term cost savings can be substantial. Composite materials are known for their durability, corrosion resistance, and extended lifespan, resulting in reduced maintenance and replacement costs. With lower maintenance requirements, mining companies can allocate fewer resources to equipment upkeep, enabling them to redirect funds towards other critical areas of operations.
Moreover, the lightweight nature of composite materials contributes to increased operational efficiency. Reduced equipment weight translates into lower fuel consumption, which can result in significant cost savings, particularly in large-scale mining operations. The improved efficiency also allows for faster material handling and increased productivity, leading to overall cost reductions and improved profitability.
B. Economic Benefits for Mining Companies
By integrating composite materials into their mining operations, companies can gain a competitive edge and capitalize on various economic benefits. The enhanced durability and lifespan of composite mining equipment minimize downtime, ensuring uninterrupted production and maximizing output. This increased productivity can lead to higher revenue generation and improved financial performance for mining companies.
Furthermore, the use of composite materials can enhance worker safety and reduce the risk of accidents, leading to reduced healthcare and insurance costs. Additionally, mining companies that prioritize sustainability and environmental responsibility through the use of composite materials often enjoy favorable public perception and stronger relationships with stakeholders, including investors and local communities. These positive relationships can contribute to long-term economic stability and growth.
C. Job Creation and Economic Growth
The widespread adoption of composite materials in the mining industry can also have a positive impact on job creation and economic growth. The development and production of composite materials require specialized knowledge and skilled labor, leading to the creation of new jobs in manufacturing, research and development, and related sectors. Moreover, as the demand for composite materials increases, the industry’s expansion can stimulate economic growth, attracting investments and fostering innovation in the mining sector.
The economic benefits associated with the use of composite materials in mining extend beyond individual companies, positively impacting regional and national economies. The growth and prosperity generated by the adoption of composite materials can contribute to job creation, increased tax revenues, and overall economic development.
In summary, the integration of composite materials in the mining industry not only offers environmental advantages but also brings substantial economic benefits. The cost savings, efficiency gains, and job creation potential make composite materials a compelling choice for mining companies aiming to improve their bottom line and contribute to economic growth.
In the next section, we will provide a summary of the key points discussed throughout the article and present an overview of the future prospects and potential challenges of composite materials in the mining industry.
X. Summary
Throughout this article, we have explored the revolutionary impact of composite materials on the mining industry. We began by providing an overview of the mining industry, highlighting its importance in global economic development and the challenges it faces. We then introduced composite materials and their wide range of applications in various industries.
In the subsequent sections, we delved into the advantages of composite materials in mining, emphasizing their lightweight nature, corrosion resistance, durability, enhanced safety features, and reduced environmental impact. We examined their applications in critical mining equipment such as conveyor belts, piping systems, tanks, structural components, and personal safety gear.
To illustrate the real-world benefits of composite materials in mining, we presented several case studies showcasing successful implementations. These included a composite conveyor belt revolutionizing material transportation, composite piping systems improving operational efficiency, and the reinvention of mining tanks using composite materials.
However, we also acknowledged the challenges and limitations associated with composite materials in mining. Cost considerations, maintenance and repair challenges, and regulatory requirements were identified as potential hurdles to widespread adoption. Nevertheless, we highlighted the advances in composite material technology, including new formulations, innovative manufacturing processes, and the integration of smart technologies, which offer promising solutions to overcome these challenges.
We then explored future prospects and emerging trends, such as the integration of automation and robotics, composite materials in mining vehicles and machinery, and the potential for 3D printing and customization. Additionally, we discussed the sustainability and environmental benefits of composite materials in mining, including a reduction in carbon footprint, waste reduction, and compliance with environmental regulations.
In the previous section, we examined the economic impact and cost-benefit analysis of utilizing composite materials in the mining industry. We discussed how cost savings, efficiency gains, economic benefits for mining companies, and job creation contribute to the overall economic prosperity and growth stimulated by the adoption of composite materials.
To conclude, the utilization of composite materials in the mining industry represents a paradigm shift with profound implications. It offers enhanced performance, improved safety, reduced environmental impact, and significant economic benefits. While challenges and limitations exist, ongoing advancements in technology and increasing awareness of sustainability drive the continuous development and application of composite materials in mining.
As the mining industry continues to evolve, embracing composite materials will be key to unlocking further efficiency, safety, and sustainability gains. By harnessing the power of composite materials, mining companies can pave the way for a more innovative, sustainable, and economically prosperous future.
In the final section, we will address frequently asked questions (FAQs) to provide additional clarity and address common queries related to composite materials in the mining industry.
XI. Frequently Asked Questions (FAQs)
In this section, we will address some commonly asked questions related to composite materials in the mining industry. These questions aim to provide further clarity and address any lingering queries you may have. Let’s dive in:
A. What are composite materials and why are they suitable for the mining industry?
Composite materials are engineered materials made by combining two or more constituent materials with distinct properties. They are designed to have superior properties compared to their individual components. Typically, composites consist of a reinforcement material, such as fibers or particles, embedded in a matrix material.
Composite materials are highly suitable for the mining industry due to their unique characteristics. They offer a combination of lightweight, high strength, corrosion resistance, durability, and design flexibility. These properties make them ideal for various applications in mining equipment, where performance, efficiency, and safety are paramount.
B. What are some common applications of composite materials in mining equipment?
Composite materials find numerous applications in mining equipment. Some common examples include:
Conveyor Belts and Conveyor Systems: Composite materials are used to create lightweight and durable conveyor belts that can withstand the demanding conditions of mining operations.
Pipes and Piping Systems: Composite piping systems offer corrosion resistance and excellent mechanical properties, making them suitable for transporting fluids and gases in mining operations.
Tanks and Storage Solutions: Composite materials are used to construct tanks and storage solutions that can resist corrosion, store hazardous substances safely, and withstand harsh environmental conditions.
Structural Components and Support Systems: Composite materials are utilized to build strong, lightweight structural components and support systems for mining equipment, ensuring both strength and efficiency.
Protective Gear and Personal Safety Equipment: Composite materials are employed in the manufacturing of safety helmets, vests, and other protective gear, providing enhanced safety to mining personnel.
C. What are the cost considerations and return on investment for using composite materials?
The cost considerations of using composite materials in the mining industry involve factors such as material costs, manufacturing processes, and maintenance expenses. While composite materials may have higher upfront costs compared to traditional materials, they often provide long-term cost savings due to their durability, reduced maintenance requirements, and improved operational efficiency. The return on investment (ROI) for using composite materials can be substantial in terms of extended equipment lifespan, reduced downtime, increased productivity, and improved safety.
D. How do composite materials contribute to sustainability in the mining industry?
Composite materials contribute to sustainability in the mining industry in multiple ways. First, their lightweight nature reduces the energy required for transportation and installation. Second, their corrosion resistance and durability extend the lifespan of mining equipment, reducing the need for frequent replacements and associated resource consumption. Third, composite materials offer opportunities for waste reduction and recycling, minimizing environmental impact. Finally, compliance with environmental regulations and the adoption of sustainable practices demonstrate the mining industry’s commitment to responsible and eco-friendly operations.
E. What are the emerging trends and future prospects for composite materials in mining?
The future prospects for composite materials in the mining industry are promising. Emerging trends include the integration of automation and robotics in mining processes, the use of composite materials in advanced mining vehicles and machinery, and the potential for 3D printing and customization of composite mining equipment. These advancements aim to further improve efficiency, safety, and sustainability in the mining industry, paving the way for a more technologically advanced and environmentally conscious future.
That concludes the frequently asked questions section. We hope these answers have provided you with a better understanding of composite materials in the mining industry. In the final section of the article, we will summarize the key points discussed and provide an overview of the benefits, applications, challenges, and future prospects of composite materials in mining.