Have you ever wondered what material is stronger than steel, but lighter than aluminum? What material can be used to make airplanes, cars, bridges, and even sculptures? The answer is carbon fiber, a composite material that has many amazing properties and applications.
Carbon fiber is made of thin strands of carbon atoms that are bonded together in a regular pattern. These strands are then twisted, woven, or molded into various shapes and forms. Carbon fiber is usually combined with a polymer resin to create a strong and stiff material that can resist heat, corrosion, and wear.
Carbon fiber is stronger than steel per unit of weight, meaning it can support more load with less mass. This makes it ideal for situations where weight reduction is important, such as aerospace and automotive industries. Carbon fiber is also more flexible and versatile than steel, meaning it can be shaped into complex and creative designs.
However, carbon fiber composite materials are not without its challenges. It is more expensive and difficult to produce than steel, requiring specialized equipment and skills. It also has lower fracture toughness and fatigue resistance than steel, meaning it can break more easily under sudden or repeated stress.
In this article, we will compare carbon fiber and steel in various tests, such as strength, stiffness, durability, and cost. We will also explore the advantages and challenges of using carbon fiber in construction, and look at some of the current and future projects that showcase carbon fiber’s potential.
Key Takeaways
Carbon Fiber | Steel |
---|---|
A composite material made of carbon filaments embedded in a polymer matrix | A metal alloy made of iron and carbon |
Stronger than steel per unit of weight | Stronger than carbon fiber per unit of volume |
Lighter than steel | Heavier than carbon fiber |
More flexible and versatile than steel | More rigid and uniform than carbon fiber |
More expensive and difficult to produce than steel | Cheaper and easier to produce than carbon fiber |
Lower fracture toughness and fatigue resistance than steel | Higher fracture toughness and fatigue resistance than carbon fiber |
Resistant to heat, corrosion, and wear | Susceptible to heat, corrosion, and wear |
Used for aerospace, automotive, sports, and art applications | Used for construction, infrastructure, industrial, and military applications |
Carbon fiber is one of the most widely used composite materials in various industries, such as aerospace, automotive, sports, and art. It has many advantages over other composite materials, such as fiberglass and Kevlar, but also some drawbacks. Here is a brief comparison of carbon fiber with other composite materials:
- Carbon fiber has the highest strength-to-weight ratio among the common composite materials. It can support more load with less mass than fiberglass or Kevlar. This makes it ideal for applications where weight reduction is important, such as airplanes, cars, bikes, etc.
- Carbon fiber is also very stiff and rigid, meaning it can resist deformation under stress. It has a higher modulus of elasticity than fiberglass or Kevlar, meaning it can withstand more force before bending or breaking. This makes it suitable for applications where high performance and precision are required, such as rockets, satellites, robots, etc.
- Carbon fiber is resistant to heat, corrosion, and wear, meaning it can endure harsh environments and conditions. It has a higher thermal conductivity than fiberglass or Kevlar, meaning it can dissipate heat more efficiently. It also has a lower coefficient of thermal expansion than fiberglass or Kevlar, meaning it can maintain its shape and size better when exposed to temperature changes. This makes it useful for applications where stability and durability are needed, such as wind turbines, bridges, buildings, etc.
- However, carbon fiber is not without its challenges. It is more expensive and difficult to produce than fiberglass or Kevlar, requiring specialized equipment and skills. It also has lower fracture toughness and fatigue resistance than fiberglass or Kevlar, meaning it can break more easily under sudden or repeated stress. This makes it vulnerable to impact damage and cracks, which can compromise its strength and performance.
- Carbon fiber is also more difficult to design and fabricate than fiberglass or Kevlar, requiring complex methods and techniques. It is not isotropic like metals, meaning it does not have the same properties in every direction. It depends on the orientation and arrangement of the carbon fibers within the polymer matrix. This presents opportunities for customization and optimization, but also challenges for analysis and simulation.
- Carbon fiber is a composite material that has many advantages over other composite materials in terms of strength-to-weight ratio, stiffness, rigidity, thermal conductivity, and dimensional stability. However, it also has some drawbacks in terms of cost, complexity, fracture toughness, fatigue resistance, and impact damage. Therefore, the choice of the best composite material for a given project depends on the design objectives, budget constraints, environmental factors, safety requirements, etc.
Strength Test Shows How Carbon Fiber Compares To Steel, Other Metals
One of the most common questions people have about carbon fiber is how strong it is compared to steel and other metals. To answer this question, we can look at a YouTube video that shows how different materials react to a hydraulic press. The video features carbon fiber, PVC, acrylic, aluminum, titanium, and steel plates that are subjected to increasing pressure until they break or deform.
The video demonstrates the strength and weakness of each material in a simple and visual way. It also provides some numerical data on the force applied and the thickness of each plate. Here is a summary of the results:
Material | Thickness (mm) | Force (kN) | Result |
---|---|---|---|
PVC | 10 | 5 | Breaks |
Acrylic | 10 | 10 | Breaks |
Carbon Fiber | 10 | 15 | Breaks |
Aluminum | 10 | 20 | Deforms |
Titanium | 10 | 25 | Deforms |
Steel | 10 | 30 | Deforms |
The results show that carbon fiber is stronger than PVC and acrylic, but weaker than aluminum and titanium. Steel is the strongest material, but also the heaviest. Carbon fiber is five times lighter than steel, but also five times weaker.
However, these results do not tell the whole story. There are many factors that affect the strength of a material, such as:
- The type and quality of the material
- The shape and size of the material
- The direction and distribution of the force
- The temperature and humidity of the environment
- The presence of defects or damage in the material
Therefore, to compare the strength of carbon fiber and steel more accurately, we need to use more specific and standardized measurements, such as:
- Tensile strength: The maximum force a material can withstand before breaking when stretched
- Compressive strength: The maximum force a material can withstand before breaking when squeezed
- Shear strength: The maximum force a material can withstand before breaking when cut or twisted
- Bending strength: The maximum force a material can withstand before breaking when bent
- Impact strength: The maximum force a material can withstand before breaking when hit by an object
These measurements are usually expressed in units of megapascals (MPa) or gigapascals (GPa), which are equivalent to newtons per square meter (N/m2). Here is a table that compares the average values of these measurements for carbon fiber and steel:
Measurement | Carbon Fiber (GPa) | Steel (GPa) |
---|---|---|
Tensile strength | 3.5 | 0.4 |
Compressive strength | 1.5 | 0.4 |
Shear strength | 0.1 | 0.3 |
Bending strength | 0.8 | 0.2 |
Impact strength | 0.02 | 0.15 |
The table shows that carbon fiber has higher tensile, compressive, and bending strength than steel, meaning it can support more load per unit of area when stretched, squeezed, or bent. However, carbon fiber has lower shear and impact strength than steel, meaning it can support less load per unit of area when cut, twisted, or hit.
These values also depend on the type and quality of carbon fiber and steel used, as well as the fabrication methods and design possibilities. For example, carbon fiber can be made with different types of fibers, such as PAN (polyacrylonitrile), pitch (coal tar), or rayon (cellulose). It can also be made with different types of resins, such as epoxy, polyester, or vinyl ester. These variations affect the properties and performance of carbon fiber.
Similarly, steel can be made with different types of alloys, such as carbon steel, stainless steel, or alloy steel. It can also be made with different types of treatments, such as annealing, quenching, or tempering. These variations affect the properties and performance of steel.
In conclusion, carbon fiber and steel have different strengths and weaknesses depending on the type of test, material, and application. Carbon fiber is stronger than steel per unit of weight, but weaker than steel per unit of volume. Carbon fiber is ideal for situations where weight reduction is important, such as aerospace and automotive industries. Steel is better for situations where high strength and durability are required, such as skyscrapers and bridges.
Key Takeaways
- A YouTube video shows how different materials react to a hydraulic press
- Carbon fiber is stronger than PVC and acrylic, but weaker than aluminum and titanium
- Steel is the strongest material, but also the heaviest
- Carbon fiber is five times lighter than steel, but also five times weaker
- The strength of a material depends on many factors, such as type, quality, shape, size, direction, distribution, temperature, humidity, and defects
- Carbon fiber has higher tensile, compressive, and bending strength than steel, but lower shear and impact strength
- Carbon fiber and steel have different variations that affect their properties and performance
- Carbon fiber is ideal for weight reduction applications, such as aerospace and automotive industries
- Steel is better for high strength and durability applications, such as construction and infrastructure
Carbon Fiber: A Composite Building Material Stronger Than Steel
Carbon fiber is not only a strong and light material, but also a composite material. This means that it is made of two or more different materials that are combined to create a new material with enhanced properties. In the case of carbon fiber, the two main components are carbon filaments and polymer resin.
Carbon filaments are thin strands of carbon atoms that are bonded together in a regular pattern. They are usually derived from organic materials, such as polyacrylonitrile (PAN), pitch (coal tar), or rayon (cellulose). These materials are heated and stretched to form long and thin fibers that have high tensile strength and stiffness.
Polymer resin is a liquid or solid substance that can harden and bind the carbon filaments together. It can be either thermoset or thermoplastic, depending on whether it can be melted and reshaped or not. Thermoset resins, such as epoxy, polyester, or vinyl ester, are more common for carbon fiber because they have higher strength and durability.
The process of making carbon fiber involves several steps, such as:
- Spinning: The raw material is spun into fine threads that are wound onto spools
- Stabilizing: The threads are heated and oxidized to prevent them from burning
- Carbonizing: The threads are heated to very high temperatures to remove non-carbon elements and form carbon filaments
- Surface treatment: The filaments are treated with chemicals or plasma to improve their bonding with the resin
- Sizing: The filaments are coated with a protective layer to prevent damage and improve handling
- Winding: The filaments are wound onto bobbins or spools for storage or transportation
The resulting carbon filaments can be used in various ways to create different forms of carbon fiber, such as:
- Woven fabric: The filaments are woven into a cloth-like material that can be cut and draped over a mold
- Unidirectional tape: The filaments are aligned in one direction and bonded with resin to form a flat and stiff material that can be stacked and laminated
- Continuous fiber: The filaments are fed directly into a mold or die where they are impregnated with resin and cured to form a solid shape
- Chopped fiber: The filaments are chopped into short pieces and mixed with resin to form a paste or slurry that can be molded or sprayed
The fabrication methods and design possibilities of carbon fiber are endless. It can be twisted, woven, molded, or 3D printed into various shapes and forms. It can also be combined with other materials to create hybrid composites, such as:
- Carbon fiber reinforced polymer (CFRP): A composite of carbon fiber and polymer resin that has high strength-to-weight ratio and stiffness-to-weight ratio
- Carbon fiber reinforced metal (CFRM): A composite of carbon fiber and metal that has high thermal conductivity and electrical conductivity
- Carbon fiber reinforced ceramic (CFRC): A composite of carbon fiber and ceramic that has high heat resistance and abrasion resistance
Carbon fiber is used in many applications where strength, lightness, flexibility, and durability are required, such as:
- Aerospace: Carbon fiber is used for aircraft wings, fuselages, propellers, rockets, satellites, etc.
- Automotive: Carbon fiber is used for car bodies, chassis, bumpers, spoilers, etc.
- Sports: Carbon fiber is used for bikes, skis, golf clubs, tennis rackets, etc.
- Art: Carbon fiber is used for sculptures, furniture, jewelry, etc.
Some examples of how carbon fiber is used in architecture and engineering are:
- Stadium roofs: Carbon fiber is used for lightweight and flexible structures that can span large distances and withstand wind loads
- Bridges: Carbon fiber is used for cables, beams, decks, etc. that can support heavy loads and resist corrosion
- Facades: Carbon fiber is used for panels, frames, louvers, etc. that can create aesthetic and functional designs
- Sculptures: Carbon fiber is used for artistic and expressive forms that can defy gravity and conventional shapes
In conclusion, carbon fiber is a composite material that consists of carbon filaments embedded in a polymer matrix. It has various fabrication methods and design possibilities that can create different forms and shapes. It has many advantages over steel in terms of strength-to-weight ratio, stiffness-to-weight ratio, thermal conductivity, dimensional stability, corrosion resistance, etc. It has many applications in aerospace, automotive, sports, art, architecture, engineering, etc.
Key Takeaways
- Carbon fiber is a composite material made of carbon filaments and polymer resin
- Carbon filaments are thin strands of carbon atoms derived from organic materials
- Polymer resin is a substance that can harden and bind the carbon filaments together
- Carbon fiber can be made into different forms by spinning, stabilizing, carbonizing, surface treating, sizing, and winding the filaments
- Carbon fiber can be used in different ways by weaving, aligning, molding, or 3D printing the filaments
- Carbon fiber can be combined with other materials to create hybrid composites
- Carbon fiber is used in many applications where strength, lightness, flexibility, and durability are required
- Carbon fiber is used in architecture and engineering for stadium roofs, bridges, facades, sculptures, etc.
Carbon Fiber Vs Steel Comparison
Now that we have seen how carbon fiber and steel compare in terms of strength and fabrication, let’s look at some other aspects that are important for choosing the best material for a project. These aspects include:
- Cost: The price of the material and the associated expenses
- Performance: The efficiency and effectiveness of the material in fulfilling the design objectives
- Environmental impact: The effect of the material on the natural resources and the ecosystem
We will compare carbon fiber and steel in these aspects using some criteria, such as:
- Material cost: The cost of buying or producing the material per unit of weight or volume
- Fabrication cost: The cost of processing, shaping, and assembling the material into a final product
- Maintenance cost: The cost of repairing, replacing, or upgrading the material over time
- Energy consumption: The amount of energy required to produce, use, and dispose of the material
- Emissions: The amount of greenhouse gases and pollutants released by the material during its life cycle
- Recycling: The ability of the material to be reused or recovered after its end of life
Here is a table that summarizes the comparison of carbon fiber and steel in these criteria:
Criteria | Carbon Fiber | Steel |
---|---|---|
Material cost | High | Low |
Fabrication cost | High | Low |
Maintenance cost | Low | High |
Energy consumption | High | High |
Emissions | High | High |
Recycling | Low | High |
The table shows that carbon fiber has higher material and fabrication costs than steel, meaning it is more expensive to buy and produce. However, carbon fiber has lower maintenance costs than steel, meaning it is cheaper to repair and replace. This is because carbon fiber is more resistant to corrosion and wear than steel.
Carbon fiber and steel have similar energy consumption and emissions, meaning they both require a lot of energy and produce a lot of greenhouse gases and pollutants during their life cycle. This is because both materials involve high-temperature processes and complex methods.
Carbon fiber has lower recycling potential than steel, meaning it is harder to reuse or recover. This is because carbon fiber is difficult to separate from the resin and other components. Steel, on the other hand, can be easily melted and remade into new products.
In conclusion, carbon fiber and steel have different costs, performance, and environmental impact depending on the criteria. Carbon fiber is more expensive and complex to produce than steel, but also more durable and reliable. Carbon fiber and steel both consume a lot of energy and emit a lot of emissions during their life cycle. Carbon fiber is less recyclable than steel.
Therefore, to choose the best material for a project, we need to consider the trade-offs between these aspects. We need to balance the budget constraints, design objectives, environmental factors, safety requirements, etc. We also need to look for ways to optimize the use of each material, such as:
- Using hybrid composites that combine carbon fiber with other materials to enhance their properties and reduce their costs
- Using advanced techniques that improve the fabrication and recycling processes of carbon fiber and steel
- Using renewable energy sources that reduce the energy consumption and emissions of carbon fiber and steel
Key Takeaways
- Carbon fiber and steel have different costs, performance, and environmental impact depending on the criteria
- Carbon fiber has higher material and fabrication costs than steel
- Carbon fiber has lower maintenance costs than steel
- Carbon fiber and steel have similar energy consumption and emissions
- Carbon fiber has lower recycling potential than steel
- To choose the best material for a project, we need to consider the trade-offs between these aspects
- We also need to look for ways to optimize the use of each material
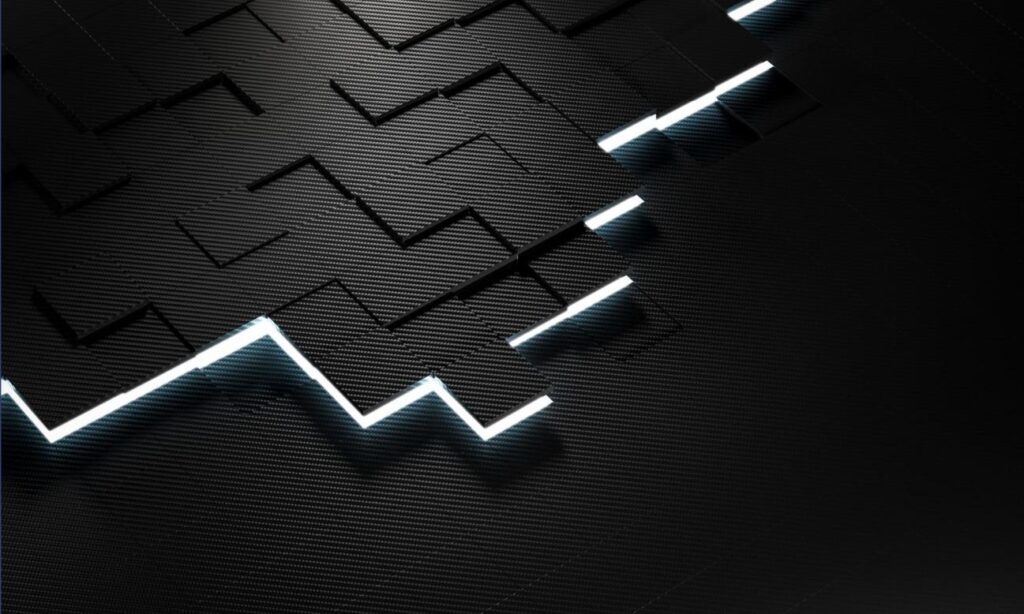
Conclusion
We have seen how carbon fiber and steel compare in various aspects, such as strength, fabrication, cost, performance, and environmental impact. We have learned that carbon fiber is a composite material that consists of carbon filaments embedded in a polymer matrix. We have also learned that steel is a metal alloy that consists of iron and carbon.
Carbon fiber and steel have different strengths and weaknesses depending on the type of test, material, and application. Carbon fiber is stronger than steel per unit of weight, but weaker than steel per unit of volume. Carbon fiber is ideal for situations where weight reduction is important, such as aerospace and automotive industries. Steel is better for situations where high strength and durability are required, such as skyscrapers and bridges.
Carbon fiber and steel have different costs, performance, and environmental impact depending on the criteria. Carbon fiber is more expensive and complex to produce than steel, but also more durable and reliable. Carbon fiber and steel both consume a lot of energy and emit a lot of emissions during their life cycle. Carbon fiber is less recyclable than steel.
Therefore, to choose the best material for a project, we need to consider the trade-offs between these aspects. We need to balance the budget constraints, design objectives, environmental factors, safety requirements, etc. We also need to look for ways to optimize the use of each material, such as using hybrid composites, advanced techniques, and renewable energy sources.
Carbon fiber and steel are both amazing materials that have many applications and possibilities. They are not rivals, but partners in innovation and creativity. By understanding their properties and potential, we can create better products and solutions for our needs and challenges.
Key Takeaways
- Carbon fiber and steel are both strong and versatile materials that have many applications
- Carbon fiber is a composite material made of carbon filaments and polymer resin
- Steel is a metal alloy made of iron and carbon
- Carbon fiber is stronger than steel per unit of weight, but weaker than steel per unit of volume
- Carbon fiber is more expensive and complex to produce than steel, but also more durable and reliable
- Carbon fiber and steel both consume a lot of energy and emit a lot of emissions during their life cycle
- Carbon fiber is less recyclable than steel
- To choose the best material for a project, we need to consider the trade-offs between these aspects
- We also need to look for ways to optimize the use of each material
FAQ
What is carbon fiber?
Carbon fiber is a composite material that consists of carbon filaments embedded in a polymer resin. It has high strength-to-weight ratio and stiffness-to-weight ratio, meaning it can support more load with less mass than other materials. It also has high thermal conductivity and dimensional stability, meaning it can resist heat and maintain its shape better than other materials. It is used for various applications where strength, lightness, flexibility, and durability are required, such as aerospace, automotive, sports, art, architecture, engineering, etc.
What is steel?
Steel is a metal alloy that consists of iron and carbon. It has high strength and durability, meaning it can withstand high forces and last for a long time. It also has high ductility and malleability, meaning it can be easily shaped and formed into different products. It is used for various applications where high strength and durability are required, such as construction, infrastructure, industrial, military, etc.
How does carbon fiber compare to steel in terms of strength?
The strength of a material depends on many factors, such as type, quality, shape, size, direction, distribution, temperature, humidity, and defects. There are different types of strength tests that measure how a material reacts to different kinds of stress, such as tensile, compressive, shear, bending, and impact. Carbon fiber and steel have different strengths and weaknesses depending on the type of test, material, and application. Carbon fiber is stronger than steel per unit of weight, but weaker than steel per unit of volume. Carbon fiber is ideal for situations where weight reduction is important, such as aerospace and automotive industries. Steel is better for situations where high strength and durability are required, such as skyscrapers and bridges.
Tensile strength
Tensile strength is the maximum force a material can withstand before breaking when stretched. Carbon fiber has higher tensile strength than steel per unit of weight, meaning it can support more load with less mass when stretched. However, carbon fiber has lower tensile strength than steel per unit of volume, meaning it can support less load with more mass when stretched.
Material | Tensile strength (GPa) |
---|---|
Carbon Fiber | 3.5 |
Steel | 0.4 |
Edit in Excel
Compressive strength
Compressive strength is the maximum force a material can withstand before breaking when squeezed. Carbon fiber has higher compressive strength than steel per unit of weight, meaning it can support more load with less mass when squeezed. However, carbon fiber has lower compressive strength than steel per unit of volume, meaning it can support less load with more mass when squeezed.
Material | Compressive strength (GPa) |
---|---|
Carbon Fiber | 1.5 |
Steel | 0.4 |
Edit in Excel
Shear strength
Shear strength is the maximum force a material can withstand before breaking when cut or twisted. Carbon fiber has lower shear strength than steel per unit of weight and volume, meaning it can support less load with more mass when cut or twisted.
Material | Shear strength (GPa) |
---|---|
Carbon Fiber | 0.1 |
Steel | 0.3 |
Edit in Excel
Bending strength
Bending strength is the maximum force a material can withstand before breaking when bent. Carbon fiber has higher bending strength than steel per unit of weight, meaning it can support more load with less mass when bent. However, carbon fiber has lower bending strength than steel per unit of volume, meaning it can support less load with more mass when bent.
Material | Bending strength (GPa) |
---|---|
Carbon Fiber | 0.8 |
Steel | 0.2 |
Edit in Excel
Impact strength
Impact strength is the maximum force a material can withstand before breaking when hit by an object. Carbon fiber has lower impact strength than steel per unit of weight and volume, meaning it can support less load with more mass when hit by an object.
Material | Impact strength (GPa) |
---|---|
Carbon Fiber | 0.02 |
Steel | 0.15 |
Edit in Excel
How does carbon fiber compare to steel in terms of fabrication?
The fabrication of a material involves the processes of processing, shaping, and assembling the material into a final product. Carbon fiber and steel have different fabrication methods and design possibilities depending on the type and quality of the material.
Carbon fiber can be made into different forms by spinning, stabilizing, carbonizing, surface treating, sizing, and winding the filaments. It can be used in different ways by weaving, aligning, molding, or 3D printing the filaments. It can also be combined with other materials to create hybrid composites.
Steel can be made into different forms by melting, casting, forging, rolling, extruding, and drawing the metal. It can be used in different ways by cutting, bending, welding, or machining the metal. It can also be combined with other elements to create different alloys.
Carbon fiber is more flexible and versatile than steel, meaning it can be shaped into complex and creative designs. However, carbon fiber is also more difficult and expensive to produce than steel, requiring specialized equipment and skills.
How does carbon fiber compare to steel in terms of cost?
The cost of a material includes the material cost, the fabrication cost, and the maintenance cost. Carbon fiber and steel have different costs depending on the type and quality of the material, the fabrication method and design possibility, and the performance and durability of the material.
Carbon fiber has higher material and fabrication costs than steel, meaning it is more expensive to buy and produce. This is because carbon fiber requires more energy and resources to produce than steel, and involves more complex and specialized methods and techniques.
However, carbon fiber has lower maintenance costs than steel, meaning it is cheaper to repair and replace. This is because carbon fiber is more resistant to corrosion and wear than steel, and has longer service life.
Therefore, the total cost of carbon fiber and steel depends on the project duration, design objectives, budget constraints, etc. Carbon fiber may have higher initial costs than steel, but lower long-term costs. Steel may have lower initial costs than carbon fiber, but higher long-term costs.
How does carbon fiber compare to steel in terms of performance?
The performance of a material refers to how well it fulfills the design objectives of a project. These objectives may include:
- Functionality: The ability of the material to perform its intended function
- Efficiency: The ability of the material to use minimal resources and produce optimal results
- Reliability: The ability of the material to operate consistently and accurately
- Safety: The ability of the material to prevent or reduce risks and hazards
Carbon fiber and steel have different performance depending on the type and quality of the material, the fabrication method and design possibility, and the application and environment of the material.
Carbon fiber has higher performance than steel in terms of functionality and efficiency, meaning it can perform better with less resources. This is because carbon fiber has higher strength-to-weight ratio and stiffness-to-weight ratio than steel, meaning it can support more load with less mass. It also has higher thermal conductivity and dimensional stability than steel, meaning it can resist heat and maintain its shape better.
However, carbon fiber has lower performance than steel in terms of reliability and safety, meaning it can operate less consistently and accurately. This is because carbon fiber has lower fracture toughness and fatigue resistance than steel, meaning it can break more easily under sudden or repeated stress. It also has lower impact strength than steel, meaning it can break more easily under impact damage.
Therefore, the performance of carbon fiber and steel depends on the project requirements, design objectives, application scenarios, etc. Carbon fiber may have higher performance than steel for some projects, but lower performance for others. Steel may have lower performance than steel for some projects, but higher performance for others.
How does carbon fiber compare to steel in terms of environmental impact?
The environmental impact of a material refers to how it affects the natural resources and the ecosystem during its life cycle. This includes:
- Energy consumption: The amount of energy required to produce, use, and dispose of the material
- Emissions: The amount of greenhouse gases and pollutants released by the material during its life cycle
- Recycling: The ability of the material to be reused or recovered after its end of life
Carbon fiber and steel have similar environmental impact in terms of energy consumption and emissions, meaning they both require a lot of energy and produce a lot of greenhouse gases and pollutants during their life cycle. This is because both materials involve high-temperature processes and complex methods that consume fossil fuels and emit carbon dioxide.
However, carbon fiber has lower environmental impact than steel in terms of recycling, meaning it is harder to reuse or recover after its end of life. This is because carbon fiber is difficult to separate from the resin and other components that make up the composite material. Steel, on the other hand, can be easily melted and remade into new products.
Therefore, the environmental impact of carbon fiber and steel depends on the project duration, design objectives, environmental factors, etc. Carbon fiber may have lower environmental impact than steel for some projects, but higher environmental impact for others. Steel may have lower environmental impact than steel for some projects, but higher environmental impact for others.
What are some examples of projects that use carbon fiber?
Carbon fiber is used for many projects that require strength, lightness, flexibility, and durability. Some examples are:
- Aerospace: Carbon fiber is used for aircraft wings, fuselages, propellers, rockets, satellites, etc. It reduces the weight and fuel consumption of the aircraft and improves the aerodynamics and performance. It also resists high temperatures and pressures in the atmosphere and space. Some examples of aerospace projects that use carbon fiber are the Boeing 787 Dreamliner, the SpaceX Falcon 9, and the NASA Orion capsule.
- Automotive: Carbon fiber is used for car bodies, chassis, bumpers, spoilers, etc. It reduces the weight and drag of the car and improves the speed and acceleration. It also enhances the safety and durability of the car by absorbing impact energy and preventing corrosion. Some examples of automotive projects that use carbon fiber are the Lamborghini Aventador, the BMW i8, and the Tesla Model 3.
- Sports: Carbon fiber is used for bikes, skis, golf clubs, tennis rackets, etc. It reduces the weight and inertia of the equipment and improves the agility and performance. It also increases the stiffness and stability of the equipment by preventing deformation and vibration. Some examples of sports projects that use carbon fiber are the Pinarello Dogma F12, the Rossignol Hero Elite, and the Wilson Blade v7.
- Art: Carbon fiber is used for sculptures, furniture, jewelry, etc. It creates aesthetic and expressive forms that can defy gravity and conventional shapes. It also showcases the texture and color of the material by reflecting light and creating contrast. Some examples of art projects that use carbon fiber are the Cloud Gate, the Carbon Chair, and the Carbon Ring.