The oil and gas industry relies heavily on pipeline infrastructure to transport crude oil, natural gas, and refined petroleum products over long distances. Traditionally, steel and concrete have been the materials of choice for constructing these pipelines. However, in recent decades, composite materials have emerged as a viable alternative for certain applications within the oil and gas sector.
Composite pipes offer a number of potential benefits compared to traditional pipe materials:
Lightweight
One of the main advantages of composites is their light weight. For example, glass fiber reinforced plastic (GRP) pipes weigh approximately 80% less than equivalent steel pipes. This significantly reduces transportation and installation costs, especially in offshore applications. The lighter weight also enables the fabrication of larger diameter pipes that would be impractical with heavy steel.
Corrosion Resistance
Steel pipes corrode over time when exposed to water, salts, and aggressive chemicals present in oil and gas environments. This corrosion leads to wall thinning and eventual leakage or failure. Composite pipes made of resins and fibers such as epoxy and glass are highly resistant to corrosion. Their non-metallic construction provides excellent long-term integrity and extended service life.
Fatigue Resistance
Pipelines experience cyclic stresses due to variations in pressure and flow. Over time, these cycles can lead to fatigue cracks and failure in steel pipes. Composites exhibit much greater fatigue resistance allowing them to withstand a high number of pressure cycles without cracking or leaking.
Leak-Before-Break
When steel pipelines fail, they tend to do so catastrophically with little warning. Composite pipes typically exhibit leak-before-break behavior. Small leaks will develop at stress concentrations but will not immediately lead to rupture. This gives operators advanced warning to shut down the pipeline before a major failure event.
Custom Properties
One of the key advantages of composites is the ability to tailor properties to meet specific application requirements. Factors such as resin type, fiber type, orientation, and quantity can be optimized to attain the desired strength, stiffness, temperature resistance, and other properties.
Non-Conductive
Composites are non-conductive materials unlike metals. This provides electrical isolation and eliminates corrosion due to galvanic currents. It also prevents spark hazards which is critical when transporting flammable hydrocarbons.
Non-Magnetic
Composites are non-magnetic, an important characteristic for pipes located near sensitive instrumentation that could be affected by magnetic fields. Steel pipes can potentially interfere with devices such as cathodic protection systems.
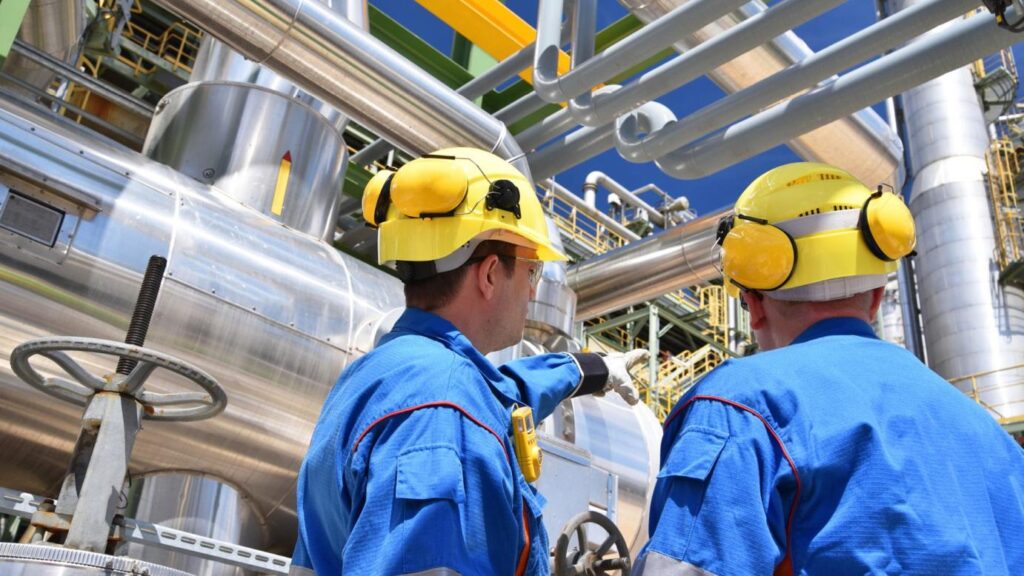
Composite Pipe Manufacturing Processes
There are several processes available for manufacturing composite pipes for oil and gas industry:
Filament Winding
Filament winding is the most common process for composite pipe fabrication. It involves winding fiber reinforcements saturated with resin around a rotating mandrel. The fibers are impregnated with resin before winding using methods like bath immersion or metered dispensing. Thermoset resins such as epoxy, polyester, or vinyl ester are typically used. Common fiber reinforcements include glass, carbon, and aramid fibers.
Filament winding allows for precise control of fiber orientation, which is critical for achieving the desired mechanical performance. Fibers are aligned close to the hoop direction to provide strength and stiffness to resist internal pressure. Axial fibers are also incorporated to provide compressive and tensile load capacity. More complex winding patterns with alternating hoop and helical fibers can be implemented.
Manufacturing Considerations
- Winding angle – Varies from 80-90° relative to pipe axis depending on required hoop/axial properties
- Fiber volume fraction – Typically 50-70% for optimum strength and toughness
- Tooling – Mandrels designed for rapid fabrication and fiber compaction
- Curing – Can be done at room temperature or in heated ovens/autoclaves
- Secondary bonding operations – Internal liners and external coatings can be applied
Filament winding enables high rates of production and is highly automated using computer-controlled machines. It is the standard manufacturing technique for GRP pipes up to 60 inches in diameter.
Pultrusion
Pultrusion involves pulling fiber reinforcements and resin through a heated die to produce a continuous composite profile. The fiber impregnation and curing happen simultaneously within the die. For pipes, the profile has a hollow center. Pulling speed is precisely controlled to achieve full curing by the time a part exits the die.
Pultrusion can incorporate various fiber materials including glass, carbon, hybrids, and natural fibers. Popular resins systems include polyester, epoxy, vinyl ester, and phenolics. It is ideal for making parts with constant cross-sections like I-beams, tubes, and pipes.
Although not as widely used as filament winding, pultrusion enables high-volume production of composite pipes up to 16 inches diameter. It produces consistent quality parts with excellent fiber alignment and smooth surfaces.
Resin Transfer Molding (RTM)
Resin transfer molding (RTM) involves first placing a fiber preform into a two-part mold cavity. The mold is then closed and liquid resin injected under pressure to impregnate the preform. The part cures inside the mold before demolding.
For pipes, the preform is wrapped around a mandrel with hoop windings overlaid with axial reinforcements. Flexible bladders can be integrated into the preform to assist with resin distribution. RTM is ideal for fabricating complex composite geometries.
The closed mold provides excellent control over fiber volume and alignment. RTM also enables the use of low viscosity and fast-curing resins for rapid fabrication. The equipment cost is relatively low compared to filament winding and pultrusion.
Pipe diameters up to 60 inches with unlimited lengths can be readily produced using RTM processes.
Pipe Type | Materials | Manufacturing Process | Diameters | Pressure Rating | Key Applications |
---|---|---|---|---|---|
Filament wound | Epoxy, polyester, vinyl ester resins; glass, carbon, aramid fibers | Filament winding | 1″ – 60″ | Up to 10,000 psi | Offshore flowlines, risers, gathering lines |
Pultruded | Polyester, epoxy, vinyl ester, phenolic resins; glass, carbon, natural fibers | Pultrusion | 1″ – 16″ | Up to 1,000 psi | Gathering lines, water injection lines |
RTM | Epoxy, polyester, vinyl ester resins; glass, carbon, natural fiber fabrics | Resin transfer molding | 1″ – 60″ | Up to 3,000 psi | Oil and gas flowlines, downhole tubing |
Thermoplastic | PE, PP, PVDF, PPS, PEK, PEEK | Extrusion, sintering | 1″ – 24″ | Up to 1,000 psi | Low pressure injection lines, flowlines |
GRE | Epoxy resin; glass fibers | Filament winding | 1″ – 36″ | Up to 7,500 psi | Corrosive gas gathering and injection lines |
CRA | Epoxy resin; carbon fibers | Filament winding | 2″ – 16″ | Over 15,000 psi | Offshore risers, wellbore tubing |
High pressure | Epoxy resin; carbon or glass braiding | Braiding + winding | 1″ – 4″ | Up to 20,000 psi | Wellbore production tubing |
This covers the common composite pipe types, their material systems, manufacturing methods, diameter capabilities, pressure ratings, and typical oil and gas applications.
Applications of Composite Pipes in Oil and Gas
Composite pipes offer performance advantages over steel and concrete pipes in several oil and gas applications:
Offshore Pipelines
Transportation of oil and gas from offshore production platforms to onshore facilities requires extensive subsea pipeline infrastructure. Composite pipes made of materials like GRP are widely used for these long undersea pipelines.
The low weight of composites significantly reduces installation costs. Large diameter pipes exceeding 50 inches can be readily deployed. GRP has excellent resistance to corrosion and abrasion in the harsh subsea environment. The pipes also need to withstand high hydrostatic collapse pressures which composites are ideally suited for.
Flexible Risers
Flexible risers connect subsea production equipment to floating production platforms. These long hybrid piping assemblies consist of rigid composite pipe sections joined by flexible joints. GRP is the main material used because of its strength, fatigue resistance, and low weight.
The composite pipe sections provide the primary conduit for oil and gas transport. The flexible joints accommodate the dynamic motion of the floating platform. GRP flexible risers enable efficient and reliable transfer of hydrocarbons to surface facilities.
Flowlines
Smaller diameter flowlines transport oil, gas, and water between wells, manifolds, separation equipment, and storage facilities. Flowlines often operate under high pressures exceeding 5000 psi. GRP is well suited for these demanding applications due to its pressure containment capacity combined with corrosion resistance.
Gathering Lines
Larger pipeline networks known as gathering lines collect petroleum products from multiple wells and fields. They feed into storage tanks and processing plants. GRP gathering lines offer leak-free transport over long distances without corrosion concerns. The lower installation costs are also advantageous.
Downhole Tubing
Specialty GRP downhole tubing is used in wellbores for applications like gas lift injection and production tubing. The pipes must withstand exposure to hydrocarbons, brine water, and elevated temperatures exceeding 250°F. GRP provides the required corrosion resistance and mechanical strength.
Risers
Risers convey produced fluids from underwater wellheads up to offshore platforms. The risers experience severe loading and fatigue cycles as well as internal pressures over 2000 psi. GRP is the preferred material given its light weight, corrosion resistance, and fatigue strength. Carbon fiber composites can also be used for risers requiring exceptionally high stiffness.
Design Standards for Composite Pipes
Composite pipe systems in oil and gas service must be engineered to meet stringent design and performance requirements. There are several major standards that specify the minimum specifications:
API Specification 15HR
Covers filament-wound GRP pipes for offshore applications. Provides requirements for materials, manufacture, dimensions, testing, and markings. Defines pressure ratings up to 10,000 psi based on pipe diameter and wall thickness.
API Specification 15S
Applies to spoolable reinforced thermoset and thermoplastic composite pipe. Contains provisions for pipe design, qualification testing, installation, and inspection. Pressure ratings up to 5000 psi are covered.
API Specification 15LR
Includes qualification tests and design criteria for composite line pipe. Used for designing low pressure gathering and transmission lines up to 16 inches diameter with operating pressures below 1000 psi.
ISO 14692-1/2/3
International standard for petroleum and natural gas industries. Covers design, materials, testing, fabrication, and installation of composite piping systems. Applicable for both reinforced thermoset and thermoplastic materials.
ASME RTP-1
Provides requirements for qualification, manufacture, inspection, and testing of resin transfer molded composite pipes. Includes filament wound pipes, tape wraps, and braided preforms. Covers diameters up to 60 inches.
Key Considerations for Composite Pipes
There are some important factors to take into account when designing, selecting, and implementing composite piping systems:
Temperature Resistance
The maximum service temperature is limited by the resin matrix. Standard polyester and vinyl ester resins can withstand approximately 180°F continuously. Epoxy resins offer better thermal performance up to 250°F. For higher temperatures, thermoplastic matrices like PPS, PEK, and PEEK can be utilized.
Pressure Rating
Hoop tensile strength provides composite pipes their internal pressure capacity. Pressure ratings are based on the composite material, winding angle, and pipe geometry. The standards provide pressure design criteria as a function of these parameters.
Permeability
Composite materials are porous and allow some gas/liquid transmission through the pipe wall. For critical applications, a non-permeable thermoplastic or metal liner provides a completely impermeable barrier.
Joining Methods
Special considerations are required when joining composite pipe sections. Standard methods include adhesive bonding, flanged connections, snapped joints, and welded sleeves. Joints are often the limiting factor for pressure capacity.
Quality Control
Stringent quality control is implemented during composite pipe manufacture. NDT techniques such as ultrasound and radiography are used to detect defects and ensure integrity. A key consideration is controlling the fiber/resin ratio and fiber orientation.
Fire Performance
Unprotected GRP can deteriorate in fire situations leading to fuel contribution and smoke hazards. Fire-resistant epoxy resins, insulation layers, and fireproof coatings can be incorporated to achieve desired fire ratings.
Cost
Composite pipe systems have significantly higher upfront material and manufacturing costs compared to steel pipe. The payback comes from lower installation costs and longer operational lifetime without corrosion damage. Life cycle cost analysis is needed to justify the investment.
The Future of Composite Pipes in Oil and Gas
Composite materials technology will continue evolving and find increased applications in the oil and gas sector. Some areas of rapid development include:
- New resin systems with improved temperature resistance, chemical resistance, and faster cure speeds
- Novel fiber reinforcements like basalt fibers and renewable natural fibers
- Optimized processing methods for cost-effective mass production of large diameter pipe
- Advanced composite repair and retrofit solutions for extending service life
- Smart composite pipes with integrated sensor networks for condition monitoring
- High pressure composite pipework with capacity exceeding 15,000 psi
- Active pipe technologies with shape/diameter adjustment capabilities
The superior durability, fatigue life, and lightweight properties of composites make them an essential material for oil and gas pipelines. Their non-corrosive construction provides major benefits for harsh subsea environments and corrosive gas transport. As manufacturing technology continues to advance, composite pipeline systems will take on an even greater role across the industry.
What are the main advantages of composite pipes?
Composite pipes offer many benefits compared to traditional metal pipes:
Lightweight
- Weigh 80% less than steel pipes
- Lower transportation and installation costs
Corrosion resistance
- Resist corrosion in harsh oil and gas environments
Fatigue resistance
- Withstand cyclic pressure stresses without cracking
Leak-before-break
- Develop small leaks before rupture
Custom properties
- Tailor strength, stiffness, temperature resistance
Non-conductive
- Eliminate corrosion and ignition risks
Non-magnetic
- Don’t interfere with instrumentation
How are composite pipes manufactured?
Three main methods:
Filament winding
- Most common process
- Fibers wound over a mandrel
Pultrusion
- Continuous pulling through a heated die
Resin transfer molding (RTM)
- Liquid resin injected into fiber preform
What oil and gas applications use composite pipe?
Typical applications:
- Offshore pipelines
- Flexible risers
- Flowlines
- Gathering lines
- Downhole tubing
- Risers
What standards apply to composite pipe design?
Major applicable standards:
- API 15HR/15S/15LR
- ISO 14692
- ASME RTP-1
Cover materials, testing, ratings, etc.
What factors affect performance of composite pipes?
Key considerations:
- Temperature resistance
- Pressure rating
- Permeability
- Joining methods
- Quality control
- Fire performance
- Cost
What are composite pipes made of?
Typical materials:
- Resins: Epoxy, polyester, vinyl ester
- Reinforcements: Glass, carbon, aramid fibers
How do composite pipes compare to steel or HDPE pipes?
Parameter | Composite Pipe | Steel Pipe | HDPE Pipe |
---|---|---|---|
Strength | High | High | Medium |
Stiffness | High | High | Medium |
Corrosion resistance | Excellent | Poor | Excellent |
Temperature resistance | Medium | Excellent | Poor |
Fatigue life | Long | Medium | Short |
Cost | High | Low | Low |
What are the limitations of composite pipes?
Limitations include:
- Moderate temperature resistance
- Permeability of resins
- Higher costs
- Joining challenges
- Potential fire hazards
How big can you make composite pipes?
- Filament wound pipes up to 60″ diameter
- Pultruded pipes up to 16″ diameter
- RTM pipes over 60″ diameter
No theoretical limit on diameter.
Are composite pipes suitable for high pressure applications?
Yes, advanced composite materials like carbon/epoxy can achieve pressure ratings over 15,000 psi. Specific benefits for high pressure:
- Handle extreme hoop stresses
- Lightweight compared to steel
- Corrosion resistance
- Fatigue resistance