Advanced composite materials are transforming industries across the globe. These engineered materials, made by combining fiber reinforcements and polymer resins, are enabling innovations from next-generation aircraft to seaworthy vessels. Now, advanced composites are poised to revolutionize one of the most ubiquitous and essential infrastructure assets – pipelines.
Composite pipes constructed with materials like fiberglass, carbon fiber, and resins are emerging as an innovative new solution for pipeline infrastructure. While metals like steel have long dominated piping applications, advanced composites pipes offer game-changing properties and capabilities. As demand grows for safer, more efficient, and environmentally sustainable pipeline networks, composite piping is positioned as the infrastructure material of the future.
What Are Composite Pipes?
Composite pipes are constructed using a combination of polymer resins reinforced with fibers like glass, carbon, kevlar, and basalt. The resin matrix binds the reinforcing fibers together, creating a durable pipe material. This results in a pipe with properties that can surpass traditional pipe materials in many aspects.
There are two main types of composite pipes:
- Thermoset Composite Pipes: The resin undergoes an irreversible chemical reaction when cured, creating a rigid, solid material. Common thermoset resins used are epoxy, polyester, and vinyl ester.
- Thermoplastic Composite Pipes: The resin softens when heated and hardens when cooled. This allows the material to be remelted and reshaped. Common thermoplastic resins are PE, PP, PVC, and Nylon.
The main fiber reinforcements used in composite piping are:
- Glass Fibers: Provide strength, chemical resistance, and low cost. Can be E-glass, S-glass, AR-glass.
- Carbon Fibers: Extremely strong and stiff for their weight. Useful where high performance is critical.
- Aramid Fibers: Offer very high strength and heat resistance. Kevlar is a common aramid fiber used.
- Basalt Fibers: Made from volcanic rock, they are abundant, inexpensive, and heat resistant.
The fiber and resin are combined using processes like filament winding, pultrusion, or in-situ polymerization to manufacture the pipes. The resulting composite material offers significantly improved performance compared to traditional pipe materials.
Composite Pipe Manufacturing
Composite pipes are manufactured using a range of processes that are optimized based on the pipe dimensions, performance requirements, and production volumes. Here are some of the main manufacturing methods:
- Filament Winding: Fibers are impregnated with resin and wound around a mandrel to form the pipe. This allows tailored fiber orientation and strength.
- Pultrusion: Fibers drawn through a resin bath and cured using heating dies to form constant profile pipes. Highly automated process.
- In-situ Polymerization: The pipe is formed on a mandrel or existing pipe and the resin is directly polymerized on site. Allows larger pipes.
- Centrifugal Casting: Pipe is spun around a mold and resin is poured in, using centrifugal forces to distribute the resin. Fast, automated process.
- Pulltrusion: Combines the pultrusion and filament winding processes. Fibers are impregnated and wound around a mandrel that is continuously pulled.
Other secondary processes like curing, coating, and machining may be used to obtain the final pipes. Manufacturing is optimized based on required pipe performance and production parameters.
Benefits of Composite Pipes
Composite pipes made with composite materials like fiberglass and carbon fiber reinforced polymer offer numerous advantages compared to traditional metal and plastic piping:
- High Strength-to-Weight Ratio: Composites like carbon fiber are significantly stronger than steel while being much lighter, allowing large diameter, high pressure pipes.
- Corrosion Resistance: Composites are not affected by corrosion from chemicals, saltwater, oils, or soil conditions. This enables a long service life.
- Design Flexibility: Properties like pressure rating, chemical resistance, and temperature range can be optimized by selecting different resins, fibers, and manufacturing methods.
- Improved Flow: Smooth internal pipe walls and low friction polymer liners maximize flow capacity compared to rough steel and plastic pipes.
- Lower Maintenance: The inert composite material does not degrade or require external coatings, linings, or cathodic protection like steel pipes.
- Safety: Composite materials do not spark and are non-conductive, improving safety during transportation and installation compared to metals.
- Sustainability: Composite pipes have a lower carbon footprint compared to alternatives due to lightweight nature and corrosion resistance.
This combination of benefits makes advanced composite pipes advantageous for many demanding pipeline applications.
Applications of Composite Pipes
The unique performance properties of composite pipes make them well suited for industries with challenging service conditions:
Oil and Gas
- Gathering systems, injection lines, multi-phase pipelines
- Offshore flexible risers and flowlines
- Process water and produced water pipelines
Chemical and Industrial
- Acid, caustic and toxic material transfer lines
- Solvent, slurry and tailings pipelines
- District heating and cooling pipes
Desalination and Water Utilities
- Seawater intake and brine outfall pipelines
- Potable water transmission and distribution
- Wastewater collection networks
Mining
- Pit dewatering and process pipelines
- Slurry and tailings transport lines
- Heap leach distribution pipe networks
Clean Energy
- Hydrogen gas, ammonia, and CO2 transport
- Geothermal plant steam lines
- Pumped hydroelectric penstocks
The performance requirements in these industries, from high pressure and temperature to highly corrosive conditions, can be reliably met using optimized composite pipe designs.
Composite Pipes vs Traditional Pipe Materials
Composite pipes have distinct advantages in material properties and performance over traditional metal and plastic piping alternatives:
Parameter | Composite Pipes | Steel Pipes | Plastic Pipes (HDPE) |
---|---|---|---|
Tensile Strength | Very High | Moderate | Moderate |
Pressure Rating | Up to 1500 psi | Up to 2000 psi | Up to 300 psi |
Temperature Range | -40°F to 250°F | -20°F to 250°F | -70°F to 140°F |
Chemical Resistance | Excellent | Fair | Good |
Permeability | Very Low | Low | Moderate |
Cost | Moderate | Low | Low |
Installation | Easy | Difficult | Easy |
Environmental Impact | Low | High | Moderate |
Useful Life | 50+ years | 30 years | 50+ years |
The balanced material properties of composite piping fill a crucial gap between the capabilities of traditional pipeline infrastructure materials like steel and plastics. This enables composite pipes to meet demanding performance requirements beyond the reach of current alternatives.
Composite Pipe Standards and Certification
The growing adoption of composite piping has led to the development of various standards and certifications to ensure quality:
- ISO 14692: International standard covering design, manufacturing, and testing of thermoplastic composite pipes. Specifies requirements and test methods.
- ASTM D2996: Standard specification for filament wound “Fiberglass” pipe. Covers material, workmanship, dimensions, and properties.
- ASTM D2310: Standard classification system for composite pipes based on materials, manufacturing method, and reinforcement.
- ASTM D2992: Standard practice for obtaining hydrostatic design basis for reinforced thermosetting resin pipes. Defines procedure to establish pipe pressure ratings.
- ASME B31.3: Code with requirements for process piping, including certification of composite piping materials.
- NACE SP0294: Standard for the design, installation, and service of reinforced thermoset and thermoplastic composite pipelines in oil and gas production.
These standards help ensure quality, safety, and reliability as composite piping sees wider adoption across industries. New standards are also under development as material science and pipe technology continues advancing.
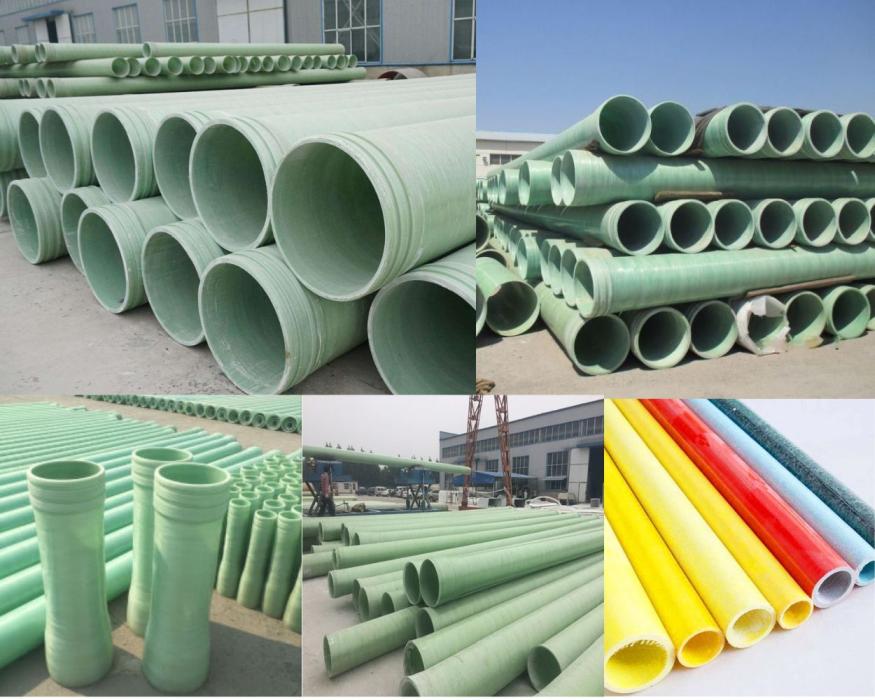
History and Origins
While advanced composite materials are on the cutting edge of technology today, the origins of composite piping date back over a century:
- 1920s: First pipes constructed by reinforcing thermoset resins with asbestos fibers. Later replaced with fiberglass.
- 1950s: Commercialization of composite pipes for low pressure applications like wastewater.
- 1960s: Filament wound epoxy and polyester pipes developed for higher pressure chemical transport.
- 1970s: Offshore oil and gas gathering systems start adopting composite flexible pipes.
- 1980s: Pultruded composite pipes introduced for corrosive chemical handling applications.
- 1990s: High performance thermoplastic composite pipes developed using new polymers.
- 2000s: Large diameter composite pipes up to 60 inches produced for high pressure oil and gas transmission.
The 21st century has seen accelerating development of composite piping technology leveraging advanced materials science like carbon reinforced polymers. This has enabled their expanding adoption across industries.
Composite Pipes Industry Growth
The global composite pipes market has charted robust growth as industries recognize their advantages. Some trends include:
- Annual composite pipe market projected to reach $3.3 billion by 2027, growing at over 7% CAGR.
- Double digit growth forecast in Asia-Pacific region propelled by rising urbanization and industrial investments.
- Oil and gas industry holds major share of composite pipe demand, expected to reach $1.5 billion by 2028.
- Growing use of composite pipes over 12 inches in diameter for high pressure transmission pipelines.
- Increasing adoption forecast for seawater intake, wastewater, district cooling, and high temperature steam applications.
- Construction, municipal infrastructure, and clean energy industries emerging as major growth sectors.
The composite pipe industry is poised for strong continued growth as more industries transition from traditional pipe infrastructure. Composite piping technology and manufacturing capabilities are rapidly evolving to meet this rising global demand.
Challenges for Composite Pipes
While exhibiting promising properties and advantages over incumbent materials, composite pipes face some challenges constraining adoption:
- High Initial Costs: Composite pipes have a higher initial cost compared to plastic and steel alternatives, impacting project budgets and payback expectations.
- Lack of Longevity Data: Being a newer material, real-world service lifetimes across decades are limited compared to traditional pipes. More data needed.
- Joining and Installation: Optimal methods for joining and field installation of composite pipes are still being established across various applications.
- Standards Development: Consensus standards guiding the qualification, design, and testing of composite pipes still under development for many industries.
- Competition: Displacing entrenched steel and plastic piping supply chains in industries that have used them for decades presents inertia to be overcome.
However, these drawbacks are progressively being addressed through technological refinements, accumulating service data, evolving best practices, and updated standards.
The Future of Composite Pipes
Advanced composite materials science and pipe manufacturing processes will continue advancing in the coming decade, expanding capabilities and opening new applications.
- Smart Pipes: Embedding sensors to monitor strain, temperature, leaks, and pipe health. Enables predictive maintenance.
- Corrosion Resistance: Next-generation thermoplastic resins and liners to handle hot acids, caustics, and brines.
- Deepwater Infrastructure: High strength-to-weight ratios ideal for ultra-deep subsea risers and pipelines.
- ** Natural Gas**: Cost-competitive composite pipes for natural gas gathering and regional transmission systems.
- Hydrogen Economy: Durable, non-permeable, non-embrittling composite hydrogen transmission pipelines.
- Large Diameters: Manufacturing and installation innovations to economically scale composite pipes above 60 inch diameters.
- Bendable Pipes: Flexible composite pipes for laying arduous subsea routes, moving seabeds, and active faults.
The accelerated pace of composite piping innovation promises to address emerging challenges across industries and enable the pipelines of the future.
Conclusion
- Advanced composite pipes made with engineered materials like carbon and glass reinforced polymers offer game-changing capabilities over conventional metal and plastic piping.
- Composite pipes provide an optimized balance of high strength, corrosion resistance, low permeability, light weight, and pressure handling that fills a crucial gap between capabilities of existing pipe infrastructure.
- Standards development, accumulating service data, and manufacturing improvements are addressing adoption challenges and enabling broader industry transition to composite piping.
- Robust demand growth, promising innovations, and compelling cost efficiencies make advanced composite pipes the future of safe, sustainable, and efficient pipeline infrastructure across critical industries.
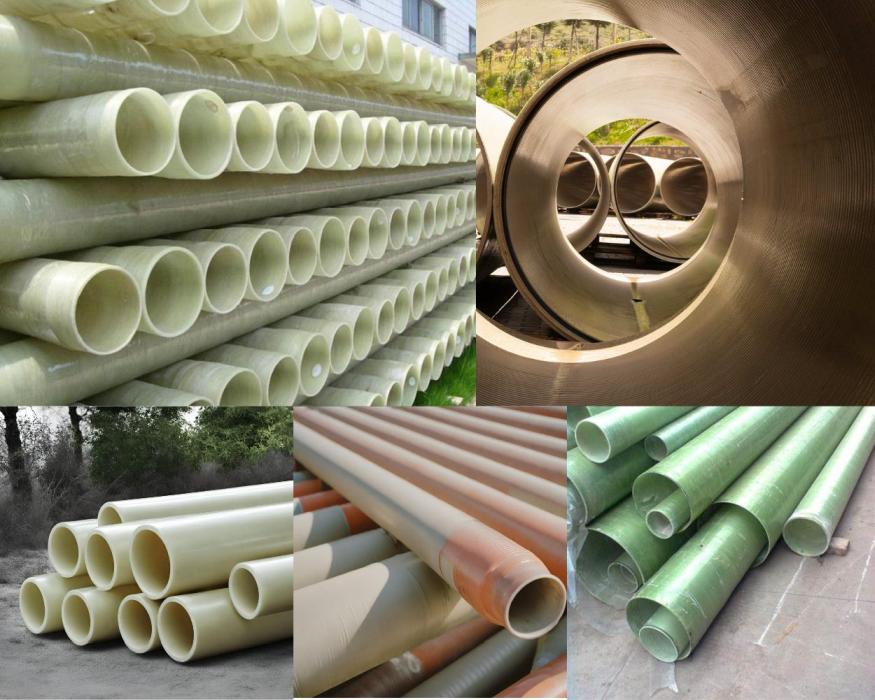
Composite Pipes for Oil and Gas
Composite pipes are a new type of pipe for oil and gas applications. Composite pipes are made of thermoplastic polymers and glass or carbon fibers, which give them many advantages over conventional steel pipes. Some of these advantages are lighter weight, higher corrosion resistance, lower installation and maintenance costs, and longer service life. However, composite pipes also face some challenges, such as high initial cost, low public awareness, lack of standards and regulations, and technical issues related to thermal expansion, permeation, and joining.
https://en.wikipedia.org/wiki/Fibre-reinforced_plastic
Materials and Manufacturing of Advanced Composite Pipes
Composite pipes derive their enhanced capabilities from the specialized materials and manufacturing processes used to construct them. The composition and fabrication of the pipes can be optimized to achieve the required performance properties for different applications.
Raw Materials for Composite Pipes
The two primary constituents that make up composite pipe materials are:
Reinforcing Fibers
Fibers provide the strength and stiffness for the pipe structure. Common options:
- Glass Fibers: Silica-based fibers offer good strength, chemical resistance, and low cost. Popular options are E-Glass, S-Glass, and AR-Glass.
- Carbon Fibers: Extremely strong and stiff for their weight. Allows very thin, lightweight, high strength pipes.
- Aramid Fibers: Made from aromatic polyamides. Provide very high tensile strength and heat resistance. Kevlar is a common brand.
- Basalt Fibers: Abundant fibers made from volcanic rock. Offer strength, thermal stability, and low cost.
Polymer Resins
Bind the reinforcing fibers and provide a protective matrix. Thermoplastic or thermoset resins are used:
- Thermoset Resins: Cure into a rigid, highly crosslinked polymer network. Popular options are epoxy, polyester, and vinyl ester.
- Thermoplastic Resins: Soften upon heating and solidify when cooled. Allows some reprocessing. Common choices are PE, PP, PVC, and nylon.
Optimized combinations of reinforcing fibers and polymer resins enable tailored composite pipes with application-specific performance properties.
Composite Pipe Manufacturing Processes
Different techniques are utilized to manufacture composite pipe sections, each having particular advantages:
Filament Winding
- Fibers are impregnated with resin then wrapped around a spinning mandrel in precise patterns.
- Allows accurate control of fiber orientation, number of layers, and resin content.
- Suitable for small to very large diameter pipes, elbows, and complex components.
Pultrusion
- Fibers drawn through a resin bath then cured by heating dies to produce a constant profile.
- Highly automated continuous process ideal for straight sections with lower cost.
- Mainly used for smaller diameter pipes due to fixed die shaping.
Pulltrusion
- Combines pultrusion with separate filament winding of inner and outer layers.
- Provides good fiber orientation control and high production speeds.
- Used for straight sections needing high strength and stiffness.
Centrifugal Casting
- Pipe formed by spinning mold and simultaneously pouring in resin using centrifugal forces.
- Very fast, fully automated process ideal for high volume production.
- Mainly used for small to medium diameter straight pipes.
In-situ Polymerization
- Pipe formed directly on-site over a mandrel or existing pipe.
- Resin impregnated reinforcements are applied and cured.
- Allows very large diameter pipes tailored for field conditions.
Secondary processes like curing, coating, jointing are used to obtain the final pipes. The manufacturing method is optimized based on required pipe properties, dimensions, and production parameters.
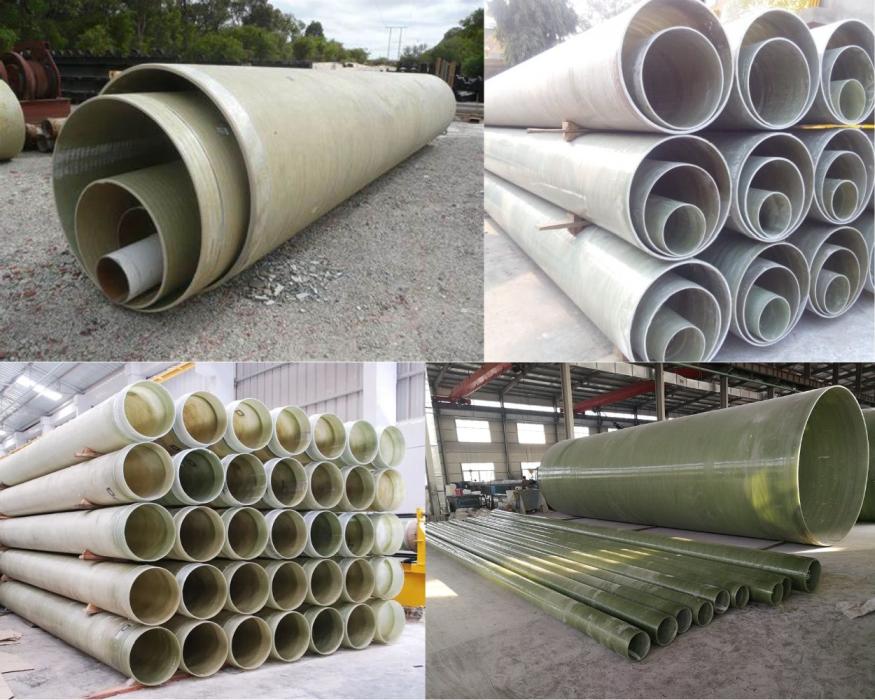
Composite Pipe Structures
The composition and arrangement of the different layers in a composite pipe wall can be designed to achieve application-specific performance objectives:
Basic Structure
- Internal corrosion barrier
- Structural reinforcement layers
- External protection layer
Typical Multi-Layer Structure
- Internal liner: Polymer layer for fluid flow and corrosion protection.
- Abrasion resistant layer: Provides protection for pipe structural layers.
- Hoop windings: Fibers wound circumferentially to resist hoop stresses.
- Helical windings: Fibers wound at an angle to provide axial strength.
- External layer: Polymer coating for environmental protection.
By optimizing the materials, orientation, and sequence of the different layers, the pipe’s structural integrity, pressure handling, temperature rating, chemical resistance, and other properties can be engineered.
Hybrid Pipe Structures
Composite materials can also be combined with traditional pipe materials in hybrid pipe designs that utilize the relative advantages of each:
- Metallic inner liner + Composite structural layer
- Composite outer layer on steel/plastic pipe
- Composite repaired section integrated into existing pipelines
Benefits of Manufacturing Process Control
Complete control over the entire manufacturing process of composite pipes enables many advantages compared to field fabrication methods for metal and plastic piping:
- Each pipe is constructed to exact optimized specifications without reliance on field welding/jointing skill.
- Automated winding and molding processes provide repeatability and reliability.
- Compact portable equipment allows pipe production directly on-site.
- Higher quality assurance with process monitoring and NDT testing.
- Improved pipe performance with flexible material and layer design.
- Lower costs from automated mass production and minimal field labor.
By utilizing dedicated pipe manufacturing facilities and machinery, composite piping can be constructed to the highest quality standards with optimized properties.
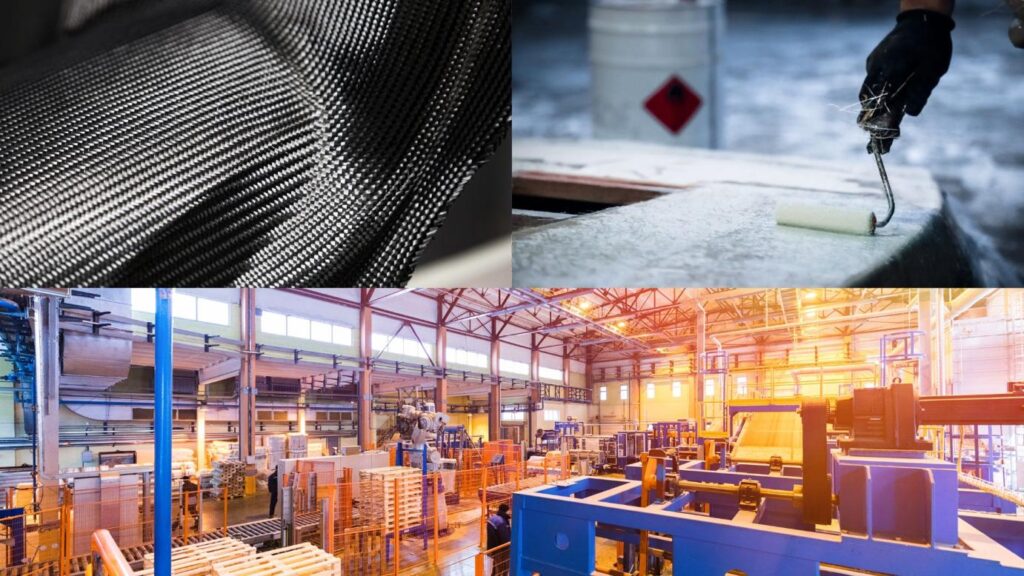
Composite Pipe Manufacturing Standards
Manufacturing standards have been introduced that define the processes, testing procedures, inspection requirements, and qualifications needed to produce quality composite piping:
- ASME B31.3 – Process Piping Code includes requirements for filament wound composite pipe fabrication.
- ASTM D2996 – Standard for Filament Wound Fiberglass Pipe covers manufacturing, inspection, and testing.
- ISO 14692 – Petroleum and natural gas industries standard establishes QA/QC guidelines and qualifications for facilities and processes.
- API 15HR – Specification for High Pressure Fiberglass Line Pipe governs manufacture of pipes for offshore and onshore oil and gas applications.
- NACE SP0294 – Standard for Reinforced Composite Pipelines in Oil and Gas applies to both thermoset and thermoplastic pipes.
Compliance with applicable standards ensures composite pipes are fabricated to specifications needed for industry applications.
Composite Pipe Sustainability
Composite pipes offer sustainability advantages owing to their material composition and longevity:
- Lower Carbon Footprint: Composite pipes are lighter than metal alternatives, reducing transportation emissions. They also last longer, avoiding repeat pipe replacements.
- Recyclability: Thermoset composites can be ground for reuse as filler. Thermoplastic composites are remoldable. At end of life, pipes can be utilized for energy recovery.
- Corrosion Resistance: Composites are inert, avoiding the need for linings, coatings, and cathodic protection required by steel pipes over their lifespan.
- Design Optimization: Excellent strength-to-weight ratio allows design optimization to use less material and minimize resource consumption.
- Enhanced Asset Lifespan: Composite materials enable extended service lifetimes and continued performance enhancement for pipelines.
Composite piping systems provide an environmentally friendly and resource efficient alternative to traditional pipeline materials.
The Future of Composite Pipe Manufacturing
Composite pipe manufacturing technology continues to rapidly advance:
- Mass Production: Scaled-up automated factories will reduce costs through high volume production.
- Smart Pipes: Sensors and data transmission integrated during manufacture for asset monitoring.
- New Materials: Novel resins, fibers, and nanomaterials to enhance capabilities.
- Hybrid Pipes: Combinations with thermoplastics and metals tailored for unique applications.
- Large Diameters: Manufacturing innovations to produce very large 60+ inch diameter composite pipes.
- Spoolable Pipes: Flexible composite pipes can be pre-spooled then uncoiled during installation.
- In-field Production: Portable plants allow custom on-site pipe fabrication.
- Quality Control: Advanced NDT, process monitoring, and automation will ensure reliability.
Continued advances in materials science, equipment automation, and manufacturing techniques will unlock new potential for composite piping systems.
- Composite pipes achieve tailored performance properties by selection of optimized reinforcements like glass, carbon, and aramid fibers combined with polymer resins.
- Manufacturing methods like filament winding allow construction of specialized multi-layer pipe structures engineered for durability, pressure handling, and chemical resistance.
- Compliance with industry standards ensures quality control over the automated composite pipe manufacturing process resulting in reliable, high performing piping systems.
- Composite materials and manufacturing refinements will provide the foundation for the next generation of smart, efficient, and sustainable pipeline infrastructure.
Comparing Composite Pipes to Traditional Pipeline Materials
Composite pipes made with advanced engineered materials provide significant performance advantages over conventional pipeline infrastructure options like steel and plastic piping. Understanding how composite pipes differ from traditional alternatives helps highlight their benefits.
Composite Pipes vs Steel Pipes
Steel has been the incumbent material for high pressure and large diameter pipelines for decades. Composite piping offers many advantages compared to steel:
Strength-to-Weight Ratio
- Composites like carbon fiber are 5 times stronger than steel on a weight basis.
- This allows high strength, large diameter thin-walled composite pipes to replace heavy, thick steel pipes.
Corrosion Resistance
- Steel pipes are prone to internal and external corrosion requiring coatings, linings and cathodic protection.
- Composites do not corrode, avoiding the maintenance needed for steel pipe longevity.
Construction and Installation
- Steel pipe sections require heavy equipment and skilled welds for jointing during construction.
- Composite pipes have built-in joints and can be produced in very long continuous lengths, significantly reducing field fabrication needs.
Flow Efficiency
- The smooth internal bore and low friction of composites enables higher fluid flow capacity compared to rough steel pipes.
- Composites maintain consistent flow performance over time unlike steel pipes subject to internal corrosion and fouling.
Safety
- Steel pipes can spark, require cathodic protection systems, and carry electric current.
- Non-conductive, non-sparking composites improve safety.
Sustainability
- Steel pipelines have over 5 times the carbon footprint of composite alternatives per kilometer of pipe.
- Steel pipe corrosion shortens asset lifespan, necessitating rebuilds. Composites last longer.
Costs
- Composite pipe installation requires less labor and equipment versus heavyweight welded steel.
- The corrosion resistance eliminates recoatings over pipe lifetime.
Composite pipes offset their higher upfront cost with lifecycle advantages over traditional steel pipelines.
Composite Pipes vs Plastic Pipes
While plastics like HDPE are used for some small to medium pressure applications, composite piping offers superior performance:
Pressure Rating
- HDPE pipes are typically rated for pressures up to 125-150 psi.
- Composites can reliably manage pressures above 500 psi for high pressure applications.
Temperature Rating
- HDPE pipes must be derated for temperatures above 73°F.
- Composite pipes can withstand operating temperatures up to 250°F without derating.
Chemical Resistance
- HDPE has limited resistance to chemicals like benzene, toluene, methanol.
- Composite materials can be chosen for broad chemical compatibility strength.
Mechanical Properties
- The high longitudinal and hoop strength of composites exceeds plastic pipe capabilities.
- Composites maintain higher strengths at elevated temperatures unlike plastics.
Permeability
- HDPE allows some gas diffusion and vapor transmission.
- Composites can be engineered for very low permeability critical for gases.
Lifespan
- HDPE is susceptible to slow crack growth, oxidization, and environmental stress cracking.
- Glass and carbon reinforced composites offer superior environmental durability.
The advanced mechanical properties of composite piping opens applications beyond the limits of plastic piping systems.
Composite Pipe Material Properties
The properties of finished composite pipes depend on the constituent materials and manufacturing process used. However, typical values contrast sharply with traditional pipe materials:
Parameter | Unit | Composite Pipes | Carbon Steel Pipes | HDPE Pipes |
---|---|---|---|---|
Tensile Strength | psi | 30,000 – 60,000 | 60,000 | 3,000 |
Elastic Modulus | psi | 1.5 – 6 x 106 | 30 x 106 | 0.12 x 106 |
Density | g/cc | 1.5 – 2.0 | 7.8 | 0.95 |
Poisson’s Ratio | – | 0.3 | 0.3 | 0.46 |
Thermal Conductivity | W/m-K | 0.5 – 5 | 52 | 0.4 |
Maximum Operating Temperature | °F | 140 – 250 | 150 | 140 |
Coefficient of Friction | – | 0.07 – 0.2 | 0.05 | 0.05 – 0.09 |
This allows composite pipes to deliver substantially higher mechanical performance compared to legacy pipeline materials.
Applications for Composite Pipes
The advantages of composite pipes makes them well suited for challenging pipeline applications where steel and plastic fall short:
Oil & Gas Exploration
- Offshore flexible risers, jumpers, and flowlines
- Remote area multi-phase gathering pipelines
High Pressure Transmission
- Natural gas and hydrogen pipelines
- CO2 transport for carbon sequestration
Water Injection Pipelines
- Enhanced oil recovery water injection lines
- District heating systems
Geothermal Energy
- Steam gathering headers and laterals
- Brine injection pipelines
Industrial Plants
- Acid, caustic and toxic material handling
- High temperature low pressure steam
Mining Slurry Transport
- Copper mine tailing pipelines
- Coal slurry lines
The unique material properties of composite pipes open new horizons beyond the constraints of conventional pipeline infrastructure.
Composite Pipe Joining Methods
A variety of methods are utilized for joining composite pipes depending on the application:
- Flanged Joints: Flanges are molded end fittings for composite pipes enabling straightforward connection via bolts.
- Victaulic Couplings: Circumferential clamps provide rigid pipe couplings. Grooves molded into the pipe ends enable quick attachment.
- Adhesive Bonded Joints: Pipes joined using high strength epoxy adhesives applied between the pipe ends. Provides monolithic joints.
- Mechanical Joints: Internally expansible metallic joints that provide rigidity. Useful for connections to legacy metal piping.
- Threaded Joints: Male and female threaded fittings molded on pipe ends enabling direct threading together.
- Onsite Wet Layup Joints: Field applied composite repair laminates for insitu joint fabrication during pipe laying.
The variety of connection methods allow composite pipelines to be adapted for different field assembly requirements.
Composite Pipe Specifications
Industry groups have developed standards that define technical specifications for composite piping:
ASTM D2992
Standard practice for obtaining design basis for reinforced thermoset resin pipe. Provides methodology to establish hydrostatic design stresses and pipe pressure ratings.
ASTM D3517
Specifies requirements and test methods for pultruded glass fiber reinforced thermoset composite tubulars. Covers dimensions, mechanical properties, and appearance.
API 15S
Specification for spoolable reinforced plastic line pipe by API covers materials, design, manufacture, and testing of pipes up to 8 inch diameter.
ISO 14692
Petroleum and natural gas industry standard gives specifications for composite pipes larger than 8 inch diameter including design, testing, QA, and installation.
ASME B31.3
Process piping code includes requirements for construction, pressure testing, design, and certification of fiber reinforced thermoset plastic piping systems.
Compliance with such standards ensures quality and reliability for safety-critical pipeline projects.
The Future of Composite Pipes
The ongoing materials science and manufacturing advances promise to expand the performance envelope and cost competitiveness of composite piping:
- Larger Diameters: Manufacturing capabilities to produce composite pipes above 60 inches for gas transmission.
- High Temperatures: New resins, coatings, and liners to allow temperatures above 250°F.
- Smart Pipes: Embedded sensors, communications, and robotics for pipeline monitoring.
- Bendable Pipes: Flexible composite pipes for arduous subsea routes and dynamic applications.
- Hybrid Pipes: Combinations with traditional pipe materials tailored for unique applications.
- Cost Parity: Process improvements for composite pipe production volume and capital efficiency.
- New Markets: Construction, district energy systems, space exploration, and offshore industries.
The widening capabilities gap between composite and legacy piping materials points to their bright future across energy, industrial, and civil infrastructure.
- Composite pipes provide balanced mechanical properties and corrosion resistance that exceeds the limits of both high strength steel and plastic pipeline materials.
- The strengths of composite piping make it advantageous for demanding oil and gas, chemical, mining, and clean energy industry applications.
- Ongoing improvements in composite materials, manufacturing, and jointing technology will address cost and adoption barriers.
- Composite pipes are poised to become the next generation of sustainable and high efficiency infrastructure for vital pipelines across industries.
Key Applications and Use Cases for Advanced Composite Pipes
The unique capabilities of composite pipes made with advanced fiber reinforced polymers makes them advantageous across a diverse range of demanding industry applications. Understanding key use cases provides insight into how composite piping provides value.
Oil and Gas Industry
The oil and gas sector presents some of the most challenging demands for pipeline infrastructure. Composite pipes deliver advantages across upstream, midstream, and downstream applications:
Upstream
- Offshore flexible risers and flowlines
- Multiphase gathering pipelines at wellheads
- Water injection lines for enhanced oil recovery
Midstream
- Corrosive oil and gas transmission pipelines
- Gas gathering systems at shale well pads
- Produced water and brine disposal lines
Downstream
- Refinery piping systems carrying acids, caustics, and brines
- Cryogenic LNG pipes
- Tank farm containment berms
Composite materials withstand offshore, oil field, and plant conditions that shorten lifespan for steel and plastic piping. High pressure ratings, chemical resistance, and temperature tolerance drive adoption.
Oil and Gas Applications
Water and Wastewater Industry
Composite pipes provide advantages for both clean and wastewater management:
Water Delivery
- Long distance water transmission mains
- District drinking water distribution networks
- Seawater intake pipelines for desalination
Wastewater Collection
- Large diameter municipal sewage collection pipes
- Corrosive industrial wastewater gathering lines
- Brine outfall pipelines from desalination
Water Treatment
- Plant process piping carrying chlorine, acids, and chemicals
- Filter backwash discharge lines
Corrosion resistance avoids internal buildup and blockages that hinder flow in aging steel and concrete water infrastructure. Smooth bores maintain carrying capacity.
Mining Industry
Mining operations impose severe demands on pipelines owing to abrasion and corrosion:
Slurry Transport
- Copper concentrate pipelines
- Iron ore slurry lines
- Coal slurry transport over long distances
Mine Dewatering
- Pit bottom water gathering pipes
- Vertical risers to surface holding ponds
Heap Leach Lines
- Distribution pipes carrying corrosive leaching acids and brines
Process Piping
- Sulfuric acid, sodium cyanide, and chemical transport lines
- Drainage networks carrying runoff with heavy metals
Composite durability handles abrasive slurries, acids, brines and minerals that destroy traditional pipe materials.
Chemical Industry
Chemical plants present extremely aggressive environments requiring specialized piping:
Acid Transport
- Sulfuric, hydrochloric, and phosphoric acid transfer lines
- Scrubber discharge pipes carrying acidic fumes
Caustic Transport
- Sodium hydroxide, potassium hydroxide transfer pipes
- Drain lines with high pH effluents
Solvents and Organics
- Benzene, acetone, phenol and other hydrocarbon lines
- Vent anddrainage networks carrying organics
Process Piping
- Steam, glycol, amine, refrigerant, and cryogenic pipes
- High purity chemical distribution lines
Careful composite material selection ensures compatibility with virtually any chemical, solving corrosion issues with steel and plastics.
Clean Energy Industry
Composite pipes support the safe growth of renewable energy infrastructure:
Hydrogen Pipelines
- Cross-country hydrogen transmission pipelines
- Distribution systems to fueling stations
Carbon Capture and Sequestration
- CO2 gathering pipelines from emission sources
- CO2 injection lines for underground storage
Geothermal Energy
- Steam gathering systems at geothermal wells
- Brine injection lines for reservoir pressure maintenance
Solar Thermal Plants
- Heat transfer fluid pipelines
- Steam headers carrying saturated steam
Biofuel Production
- Ethanol plant process piping carrying organics and derivatives
- Biodiesel production piping with corrosive effluents
Composite pipes avoid potential hydrogen embrittlement of steel, safely contain CO2, and handle geothermal extremes.
Other Key Applications
Many other infrastructure sectors benefit from advanced composite piping:
Municipal Infrastructure
- District energy systems distributing heating and cooling
- Buried service utility pipes for electricity, gas, and telecom
Industrial Plants
- Chemical, refinery, and processing facilities piping systems
- Drainage networks carrying corrosive runoff and process fluids
Desalination
- Large diameter seawater intake pipelines
- Brine outfall pipes carrying corrosive discharge
Construction
- Concrete pumping lines subject to high abrasion
- Highrise building water distribution risers
Defense Infrastructure
- Fuel depots, ammo dumps, and missile site piping
- Temporary pipelines deployed quickly in field conditions
Agriculture
- Irrigation systems piping carrying abrasive particulate matter
- Water lines for livestock operations
The advantages of composite materials make them the ideal piping solution for old and emerging applications alike.
Composite Pipes for Corrosive Services
The chemical resistance of composite pipes makes them invaluable for handling aggressive substances. Some examples:
Acids
- Sulfuric acid – Handling lines, storage tank drainage
- Hydrofluoric acid – High purity chemical distribution
- Phosphoric acid – Fertilizer manufacturing process piping
Caustics
- Sodium hydroxide – Transfer lines, containments
- Potassium hydroxide – Drainage networks
- Ammonium hydroxide – Refrigeration systems
Solvents
- Xylene, toluene, hexane – Transfer piping
- MEK, acetone – Chemical plant vent headers
- Phenol, creosols – Distillation column reflux piping
Brines
- Sodium chloride – Desalination plant outfall pipes
- Calcium chloride – Storage tank containment berms
- Zinc bromide – Geothermal plant gathering lines
Other
- Hydrogen sulfide – Refinery effluent processes
- Sodium hypochlorite – Disinfection systems
- Sodium cyanide – Gold leaching transport lines
Proper composite selection avoids corrosion, containment leaks, and plant shutdowns.
Designing Composite Pipes for Specific Applications
Composite piping offers great flexibility to engineer the pipe composition and construction for unique performance requirements:
Material Selection
- Choose glass, carbon, aramid, or basalt fiber reinforcement materials based on strength, cost, and chemical needs.
- Select resins like epoxy, polyester, vinyl ester based on temperature rating, chemical resistance, and performance needs.
Layer Sequence
- Optimize sequence of internal liner, structural layer, external coating based on service duty.
- Add abrasion resistant or permeation barrier layers for tough services.
Fiber Orientation
- Orient fibers in hoop or helical windings for axial, hoop, or biaxial strength.
- Balance burst pressure rating, axial load capacity, and collapse resistance.
Diameter and Wall Thickness
- Design to achieve high pressure capacity through increased thickness and windings.
- Optimize for weight and stiffness by diameter to thickness ratio selection.
This flexibility enables engineered composite piping tailored for the most challenging fluid transport applications.
Composite Pipe Operating Envelope
The composite fabrication provides wide ranging operational envelopes not achievable with steel or plastics:
Pressure Ratings
- Up to 1500 psi maximum allowable operating pressures possible.
- Well above ratings for HDPE piping. Comparable to steel.
Temperature Ranges
- Continuous operating temps from -50°F to 250°F.
- Exceeds undegregated range for plastics. Similar to steel.
Chemical Resistance
- Excellent resistance to virtually all chemicals from 2 to 14 pH.
- Greater immunity versus traditional materials.
Permeability
- Essentially zero gas, vapor or moisture diffusion through pipe wall.
- Critical for gases and containment structures.
Thermal Cycling
- Can survive repeated thermal cycles without damage or fatigue.
- Unlike plastics which crack and steel that deforms.
This gives designers much wider latitude when developing new piping systems with composites.
- Composite pipes enable breakthrough capabilities for industries like oil and gas, chemical, mining, and clean energy with highly demanding applications.
- Characteristics like temperature, pressure, chemical, and abrasion resistance can be optimized through tailored pipe construction and materials selection.
- The flexible design envelope surpasses limitations of traditional steel and plastic piping infrastructure.
- As more real-world performance data accumulates, composite pipes are emerging as the ideal solution for ever more complex and challenging fluid transport applications.
Design, Testing and Certification of Composite Pipes
The engineering design, rigorous testing, and codified certification processes involved in developing composite piping systems ensures their safe, reliable, and optimal performance for demanding industry applications.
Design Codes and Standards
Composite pipe design closely follows comprehensive codes and standards developed by various professional organizations:
- ASME B31.3 – Process Piping Code includes requirements for design, materials, construction, inspection and testing of fiber reinforced thermoset composite piping.
- ASTM D2992 – Standard practice for obtaining hydrostatic design stresses for reinforced thermoset resin pipes. Provides formulas and methodology for design calculations.
- ASTM D3517 – Standard for pultruded composite pipes covers design requirements including stiffnesses and pressure ratings.
- ISO 14692 – Petroleum and natural gas standard provides design guidelines for reinforced thermoset and thermoplastic composite pipe.
- API 15HR – Specification for reinforced thermoset resin pipe for offshore oil and gas. Defines design process and requirements.
- NACE SP0294 – Standard for reinforced composite pipe in oil and gas service governs design, including pressure containment.
Compliance ensures optimal engineered pipe systems meeting safety factors.
Design Principles
The material anisotropy and multilayer construction of composite pipes necessitates specialized design methods. Key principles include:
- Hoop Stress: Circumferential or hoop stress from internal pressure governs the design. Calculates required laminate thickness.
- Axial Stress: Longitudinal loads from pressure end force, buoyancy, weight, bending. Determines axial reinforcement.
- Burst Pressure: Derive burst pressure from hoop strength. Burst pressure rating is typically > 3X operating pressure.
- Collapse Pressure: Resistance to external hydrostatic pressure collapse. Establishes minimum thickness.
- Cyclic Loading: Fatigue analysis for fluctuating pressure. Calculates damage fraction to determine design life.
- Temperature: Derating of material allowables under operating temperature exposure.
- Safety Factors: Partial safety factors for loads, materials, and consequences of failure.
Following established design principles results in right-sized, optimized composite piping.
Design Process
A typical composite pipe design process includes:
Service Conditions
- Internal and external pressure, temperature, fluid medium, installation site geography
Performance Requirements
- Diameter, operating pressure, design life, pressure cycling, stiffness, chemical resistance
Materials Selection
- Resin, fiber, and liner materials to meet performance needs
Design Analysis
- Hoop, axial, and collapse analysis. Fatigue and temperature derating.
Prototype Testing
- Hydrostatic burst, cyclic pressure, strain limit, NDE inspections to validate design
Safety Factors
- Specify safety factors for pressure, loads, materials, consequences of failure
Qualification Testing
- Long-term testing, accelerated life testing, and probabilistic analysis to validate
Certification
- Third party design review and plant audit for certification to industry standards
The extensive design rigor ensures optimal product performance safety margins.
Prototype Testing
Physical testing of composite pipe prototypes is undertaken to validate designs before final qualification:
Burst Testing
- Pipe samples pressurized to failure by hydrostatic jackets. Determines actual burst capacity.
Cyclic Pressure Testing
- Repeated pressure fluctuations from minimum to maximum are applied for extended durations up to millions of cycles. Validates fatigue life.
Collapse Testing
- External hydrostatic pressure increased until pipe crushes inward to gauge collapse rating.
Bend Testing
- Pipe subjected to bending loads until failure. Determines flexibility.
Pull-out Testing
- Mechanical testing of bonded joints. Validates joint integrity.
Chemical Exposure Testing
- Pipe samples immersed in various chemicals for extended periods and monitored for degradation. Verifies chemical compatibility.
Prototype testing provides real-world data to finalize designs before qualification.
Pipe Qualification Testing
Rigorous qualification testing programs are mandated by standards and end user specifications:
Hydrostatic Type Testing
- 100 hour sustained pressure test at 2X operating pressure rating. Confirms strength margins.
Long Term Hydrostatic Testing
- 1,000-10,000 hour sustained pressure test to validate long term pipe integrity and absence of creep or environmental stress cracking.
Cyclic Pressure Testing
- Pressure fluctuated from low to high for millions of cycles until failure. Proves fatigue life.
Accelerated Aging Testing
- Pipes subjected to simulated harsh environments and accelerated aging through temperature, radiation, chemicals.
Probabilistic Testing
- Burst, cyclic pressure, sustained loads to failure for probability distribution. Proves reliability.
NDE & Visual Inspection
- Non-destructive examination like X-ray and ultrasonic inspection along with visual checks. Confirms quality.
Passing qualification protocols confirms fitness for service in demanding conditions.
Pipe Certification
To provide full validation of their design, testing, and manufacture, composite pipes must be certified by respected third parties:
- Materials & Consistency: Certifies raw materials and resin meet specifications. Confirms manufacturing quality control.
- Design Methodology: Audit to approve theoretical design methodology follows codes and standards.
- Manufacturing Process: Certifies fabrication processes including NDT inspection adhere to qualified procedures.
- Testing: Witness of design validation, prototype, and qualification testing protocols to validate results.
- Quality Systems: Audit of pipe plant quality assurance, control systems and documentation for compliance.
- Code Compliance: Certifies all design, materials, manufacturing, inspection, testing and quality systems meet or exceed major code requirements.
Certification by approved agencies like DNV and Bureau Veritas provides assurance to end users that the pipes will perform reliably in service.
Installation Standards
In additional to manufacturing and design standards, various groups also publish installation specifications:
- ASME B31.3 – Provides requirements for transportation, handling, laying, joining, and pressure testing during installation.
- ASTM F1216 – Practice for installation of fiberglass pipe systems includes trenching, embedding, joining, and testing procedures.
- AWWA M45 – Manual for installation of fiberglass pressure pipe outlines best practices for storage, handling, laying, joining, testing.
- AGA PVC-12 – Guide for installing buried plastic pressure piping focuses on PE and PVC but also covers composite pipe.
Standards minimize handling risks and prove system integrity during pipeline construction.
The Future of Composite Pipe Design
Composite pipe engineering continues to evolve with new materials, analysis methods, and manufacturing techniques:
- New Materials: Novel resins, reinforced polymers and additives to expand capabilities
- Structural Analysis: Multi-scale and probabilistic modeling provides deeper insights
- Smart Pipelines: Integrated sensors, communications, and robotics into designs
- Manufacturing Innovations: Novel techniques enable new geometries and hybrid materials
- Code Development: Standards expanded for novel materials like thermoplastic composite pipe
- Reliability-based Design: Design margins and safety factors based on probabilistic methods
Ongoing advances will enable the next generation of optimized and intelligent composite piping infrastructure.
- Rigorous design codes, testing standards, and third party certification requirements ensure composite pipes provide the highest levels of safety and reliability.
- Following established design principles and analysis methods results in composite piping systems engineered for optimal performance.
- Extensive prototype testing and full-scale qualification provides real-world validation of designs and manufacturing quality.
- Certification of all aspects from raw materials to finished products delivers confidence in performance critical for offshore platforms, chemical plants, transmission pipelines, and other high consequence applications.
- Continued evolution of analysis methods, new materials, and manufacturing innovations points to an exciting future for “smart” high efficiency composite piping systems.
Conclusion: The Future of Pipeline Infrastructure is Composite
Advanced composite materials are poised to transform the global pipeline industry. As critical infrastructure ages and demand grows, the future points to high performance composite piping solutions.
Summary of Key Benefits
Composite pipes fabricated from engineered materials like carbon fiber and fiberglass offer unmatched capabilities:
- Outstanding Strength: Composites are stronger than steel on a strength-to-weight basis. Thin, lightweight composite structures offer extreme strength.
- Corrosion Immunity: Inert to corrosion, abrasion, and UV degradation. Avoid traditional pipe corrosion protection costs.
- Design Flexibility: Tailor composition and construction to achieve needed pressure, temperature, chemical, and mechanical properties.
- Life Extension: Restore existing pipelines by relining with composites. Extend asset life at lower cost than replacement.
- Flow Efficiency: Smooth walls and joints maintain carrying capacity and pressure, reducing pumping costs.
- Installation Speed: Long pipe lengths, built-in joints, and light weight enable rapid construction.
- Reduced Maintenance: Won’t degrade or corrode over time. Eliminates need for replacement or recoating.
- Leak Elimination: Fewer joints, seamless pipes, and non-permeable materials prevent leaks.
- Environmental: Long life, inertness, and lightweight nature offer sustainability benefits versus alternatives.
- Safety: Non-conductive and non-sparking. Improved reliability reduces hazards.
These characteristics make composite piping an ideal material across demanding industry applications.
Transforming Industries
The advantages of composite pipes are driving adoption in industries with critical pipeline infrastructure:
Oil and Gas
- Deepwater offshore gathering and multiphase transmission lines
- Shale play gas gathering and water disposal pipelines
- Oil sands production process water and tailings pipe networks
- Natural gas and hydrogen transmission pipelines
Water
- Aging water main replacement and rehabilitation
- Sewer overflow remediation
- Desalination plant seawater intakes and brine disposal
Mining
- Copper tailing slurry lines
- Hard rock and coal mine process water and chemical drainage transport
- Heap leach distribution pipe networks
Power Generation
- Solar thermal plant heat transfer fluid lines
- Geothermal steam gathering headers
- Nuclear plant raw water piping and containment spray lines
Chemical and Industrial
- Refinery effluent drainage collection networks
- Bulk chemical transfer lines for acids, caustics and toxic materials
- Steam and cryogenic chill water piping distribution
Legacy pipeline materials are reaching their limits across these industries. Composite piping offers breakthrough potential through its balanced properties, fabrication flexibility, and installation advantages.
Growth Projections
Double digit growth is forecast for composite pipes across sectors:
- Oil and gas pipelines: $1.5 billion by 2028 at 15% CAGR
- Chemical industry: $730 million by 2028 at 11% CAGR
- Water and wastewater: $530 million by 2027 at 7% CAGR
- Asia-Pacific market: $1.7 billion by 2027 at 16% CAGR
Several macro trends drive this growth:
- Aging pipeline infrastructure nearing end of lifespan
- Increasing transport of corrosive and toxic materials
- Accelerating renewable energy and hydrogen economy buildout
- New large scale projects in developing countries
- Urbanization, industrialization, and improved environmental standards
- Pipeline network expansion for energy security
These powerful forces point to intensifying demand for advanced composite piping solutions worldwide.
The Future is Composite
Ongoing innovation in materials, manufacturing, and installation will expand composites across new frontiers:
Materials
- Novel thermoset and thermoplastic resins for extreme temperatures
- Reinforcing fibers like boron and ultra high strength carbon
- Nanomaterials for multifunctional smart pipes
- 3D printed thermopolymers enable new structures
Manufacturing
- Highly automated factories with integrated robotics
- In-field and in-situ mobile manufacturing
- AI-optimized custom design and production
- Integrated piping modules and prefabrication
Asset Monitoring
- Embedded sensors to monitor strain, temperature, vibration, leaks
- Pipe robots that inspect condition
- Digital twin tracking of structural health
New Applications
- Deep sea mineral gathering in remote ocean locations
- Geothermal pipelines in high seismic regions
- Lunar and Martian pipelines as space exploration advances
- Fusion energy test reactors ultrahigh temperature piping
Business Models
- Pipelines-as-a-Service business models
- Composite relining services for life extension
- Integrated mobile pipe plant and logistics providers
The possibilities are endless as composite science and technology evolves.
Realizing the Future
To fully unlock the potential of composite piping, stakeholders across the pipeline industry must come together:
Technical Challenges
- Optimize materials for temperature, pressure, permeability
- Develop joining methods for new materials
- Create flexible bendable pipes
- Scale up manufacturing for cost competitiveness
- Build radio, satellites, drone systems for remote monitoring
- Leverage robotics for inspection and maintenance
- Reliability and lifecycle performance data
- Standards for novel materials like thermoplastic composite pipe
Commercialization
- Increase industry awareness of composite pipe capabilities -Availability of project financing mechanisms
- Foster early adopter partnerships
- Localized supply chains and skilled labor pool
- Establish maintenance support ecosystem
- Build-out ancillary technologies like pumps, valves, and ancillaries
Sustainability
- Conduct comprehensive sustainability lifecycle analysis
- Report verifiable emissions reductions
- Achieve environmental product declarations
- Enable a circular economy through material recovery
By coming together across the pipeline value chain, the full potential of composite piping technology can be realized, enabling the sustainable infrastructure of the future.
The Future is Here
Composite piping is reaching a tipping point as converging forces propel adoption. For industries demanding safe, efficient, and durable pipeline infrastructure, the time for composites is now.
Synthesizing decades of material science research with advanced manufacturing innovations, composite pipes are ready to deliver step-change improvements across the global pipeline infrastructure landscape.
With their unmatched durability, corrosion immunity, flow efficiency, lightweight versatility, and sustainability benefits, high performance composite pipes represent the future for vital energy, water, chemical, and industrial networks worldwide.
The age of composites has arrived. The future of pipeline infrastructure is now.
Frequently Asked Questions
What are composite pipes?
Composite pipes are made using polymer resins reinforced with fibers like glass, carbon, and aramid. The materials are combined to create pipe with enhanced properties compared to traditional materials like steel or plastic.
What industries use composite pipes?
Key industries adopting composite pipes include:
- Oil and gas
- Chemical and industrial plants
- Mining
- Water and wastewater
- Clean energy
What are the main benefits of composite pipes?
The main benefits include:
- High strength-to-weight ratio
- Corrosion and chemical resistance
- Design flexibility
- High pressure capacities
- Extended asset life
- Improved flow efficiency
How do composite pipes compare to steel or plastic pipes?
Composites offer superior strength and corrosion resistance compared to plastics like HDPE. They also have 5x the strength of steel on a weight basis. Composites avoid the corrosion maintenance issues of steel pipelines.
What temperature ranges can composite pipes withstand?
Composite pipes can operate from -50°F to 250°F continuously, exceeding the capabilities of HDPE pipe. The temperature rating meets or exceeds that of steel pipe.
How are composite pipes designed and tested?
Stringent industry codes and standards guide composite pipe design. Extensive prototype and qualification testing validates their performance. Third party agencies certify all design, materials, fabrication, and testing meet requirements.
How are composite pipes manufactured?
Common manufacturing methods include filament winding, pultrusion, centrifugal casting, and pulltrusion. The processes allow construction of specialized multi-layer pipe walls engineered for performance requirements.
What joining methods are used to connect composite pipes?
Typical joining methods include flanged joints, molded fittings, adhesive bonding, mechanically restrained joints, and wet layup of composite repairs at the joints during installation.
How are composite pipes installed?
The lightweight composite pipe segments can be installed using less heavy equipment than steel pipelines. Long 500m sections minimize field joints. Pipes are often directly buried, requiring less above ground supports.
Can composite pipes be repaired?
Sections of damaged composite pipe can be replaced. Pipe walls can also be repaired by adding layers of fiber reinforced polymer composite over the damaged areas.
How environmentally friendly are composite pipes?
Composite pipes have a lower carbon footprint compared to steel and plastics. Their corrosion resistance avoids frequent replacements. Composites also conserve material use through their strength.
What is the future outlook for composite pipes?
Robust growth is forecast as industries recognize the advantages of composites for demanding applications. Advances in materials, manufacturing, asset monitoring, and robotics will further expand capabilities.