What are composite materials and how are they made?
Composite materials are materials made from two or more constituent materials with significantly different physical or chemical properties. The individual components remain separate and distinct within the finished structure. The new material may be preferred for many reasons: common examples include materials which are stronger, lighter, or less expensive when compared to traditional materials.
The most common composites are fiber-reinforced polymers. The fiber acts as reinforcement and provides strength and stiffness. Common fibers used include glass, carbon and aramid. The polymer acts as the matrix or binder and holds the fibers together. Common polymers used include epoxy, vinyl ester, and polyester resins.
The manufacturing process typically involves impregnating the reinforcing fibers with the polymer resin. The fiber architecture can be unidirectional, woven fabrics, or randomly oriented chopped strands. The fiber-resin mixture is molded into the final part shape. The fibers resist load and provide strength while the resin transfers load between fibers and provides a surface layer.
Other methods of making composite materials include metal matrix composites reinforced with ceramic particulates, and ceramic matrix composites reinforced with ceramic fibers or whiskers. Properties can be tailored for specific applications by selecting appropriate fiber and matrix combinations.What are the advantages and disadvantages of composite materials compared to traditional materials like metals?
Some key advantages of polymer matrix composites:
- High strength-to-weight ratio – Composites are much lighter than metals like steel and aluminium for similar strength. This is beneficial for transportation applications.
- Design flexibility – Composites can be molded into complex part shapes. The fiber reinforcement can be aligned to optimize strength and stiffness.
- Corrosion resistance – The polymer matrix protects the fibers from environmental damage. Useful for infrastructure and marine applications.
- High fatigue strength – Composites withstand cyclic fatigue loading better than metals. Useful for dynamic applications.
- Lower maintenance – Composites do not suffer from corrosion and fatigue like metals. This reduces inspection and maintenance costs.
- Thermal and electrical insulation – The low thermal conductivity of the polymer matrix provides insulation against heat and electricity. Useful for thermal management and electrical applications.
Some disadvantages compared to metals:
- Higher cost – Composite materials and fabrication are typically more expensive than metals. However, the lifecycle costs may be lower.
- Complex design analysis – The anisotropic properties complicate design analysis compared to isotropic metals.
- Environmental degradation – The polymer matrix can deteriorate due to moisture absorption and UV exposure. Requires surface protection.
- Low service temperature – Polymers tend to soften at moderately high temperatures, limiting usage compared to high melting point metals.
- Low electrical and thermal conductivity – The insulating matrix reduces electrical and thermal conductivity, which may be undesirable for some applications.
- Difficult to repair – Composite damage is not easy to detect visually or repair unlike metals.
What industries commonly use composite materials and for what applications?
Some major industries using composites and their applications:
Aerospace – Aircraft structures, wings, fuselages, empennage, interiors, engine components. Benefits include reduced weight, corrosion resistance, and improved fatigue life.
Automotive – Body panels, bumpers, leaf springs, drive shafts, suspensions, wheels, brakes. Lightweight construction improves fuel efficiency. High strength for crashworthiness.
Marine – Boat hulls, decks, masts. Benefits include light weight, corrosion resistance, impact resistance.
Construction – Concrete reinforcement, bridge decks, building facades and roofs, pipes. Composites provide strength, light weight, and durability.
Consumer Products – Sporting goods like golf clubs, tennis rackets, bicycles. Electronics housing. Luggage shells. Helmets. Provide high strength, light weight.
Wind Energy – Wind turbine blades. Resistance to fatigue loads with low weight. Corrosion resistance.
Oil and Gas – Downhole tubing, casing, pipes. Provide high strength, corrosion resistance for oil well environments.
Electrical – High voltage insulators, circuit boards, switches. Electrical and thermal insulation properties utilized.
Medical – Joint replacements, dental fixtures, medical devices. Tailored properties, biocompatibility.
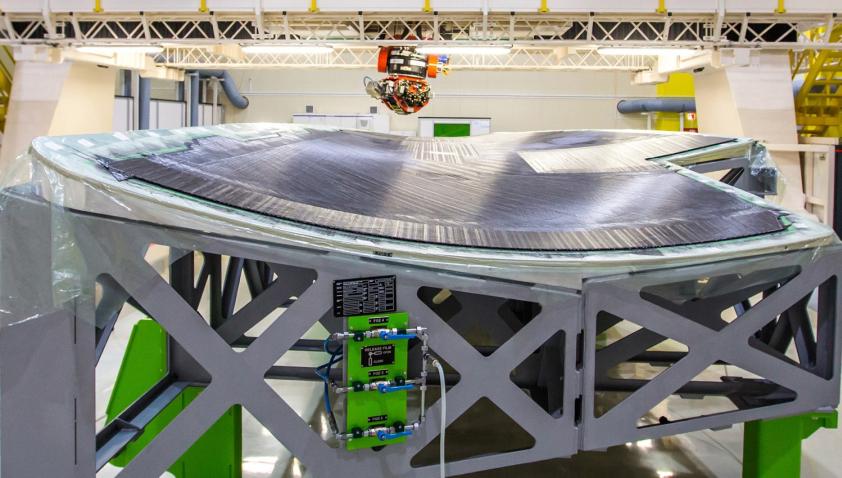
How do the properties of composite materials compare to metals, ceramics, and polymers?
Metals: Metals have high strength, ductility, and fracture toughness but also high densities. Composites match or exceed the strength and stiffness of metals while maintaining a much lower density. Composites are more versatile than metals in tailoring properties. However, metals have better thermal and electrical conductivity.
Ceramics: Ceramics exhibit excellent hardness, heat resistance, corrosion resistance, and compressive strength. However, they have low fracture toughness and tensile strength. In comparison, composites have superior tensile strength and fracture resistance but lower temperature capability than ceramics.
Polymers: Polymers provide versatility, low density, and ease of processing but have poor mechanical properties compared to metals and ceramics. Reinforcing polymers with fibers can drastically increase their strength, stiffness, and temperature resistance while maintaining light weight. This makes composites preferable over unreinforced polymers for structural applications.
In summary:
- Strength/stiffness – composites match or exceed metals but lower than ceramics
- Density – composites lower than both metals and ceramics
- Thermal stability – lower than ceramics but better than polymers
- Thermal conductivity – lower than metals but higher than polymers
- Electrical conductivity – lower than metals but higher than polymers
- Toughness – superior to ceramics but inferior to metals
- Corrosion resistance – better than metals but application-specific relative to ceramics
- Cost – higher than metals and polymers but lower than machined ceramics
What types of reinforcement and matrix materials are commonly used in composites?
Reinforcements:
- Fibers – glass, carbon, aramid, boron, silicon carbide
- Particulates – calcium carbonate, alumina, silicon carbide
- Nanomaterials – carbon nanotubes, graphene
Matrices:
- Polymer – epoxy, polyester, vinyl ester, phenolic
- Metal – aluminum, magnesium, titanium, nickel
- Ceramic – aluminum oxide, silicon carbide, glass-ceramic
- Carbon – pyrolytic carbon, graphite
Common composite types:
- Fiber reinforced polymer (FRP) – glass/epoxy, carbon/epoxy
- Metal matrix composites (MMC) – SiC/Al, B/Al, WC/Co
- Ceramic matrix composites (CMC) – SiC/SiC, Carbon/Carbon
- Polymer matrix nanocomposites – CNT/epoxy, graphene/epoxy
The fiber and matrix combination is tailored to meet specific property and performance requirements such as strength, temperature capability, environmental resistance, weight, and cost. The fiber type, architecture and volume fraction can be optimized to take advantage of composite capabilities.
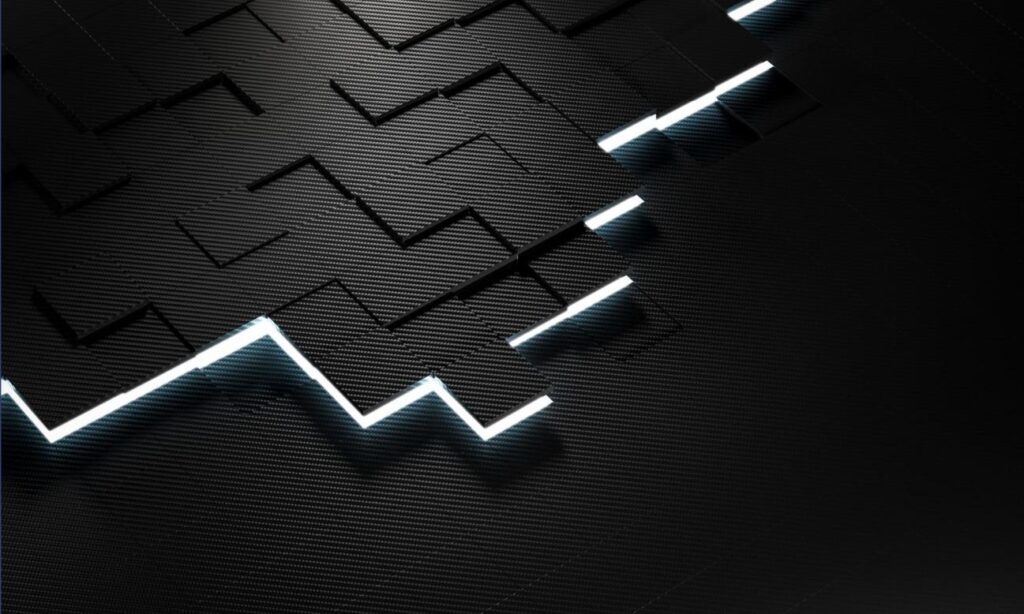
6. How does the fiber-matrix interface affect the properties of composite materials?
The fiber-matrix interface plays a critical role in determining the mechanical properties and performance of composites. A strong interface bond is desired to enable efficient load transfer between the fibers and matrix. However, an overly strong bond can lead to brittle material behavior.
Load transfer: Efficient transfer of stress from the matrix to the high strength fibers requires a strong interface bond. This enhances the mechanical properties of the composite. A weak bond leads to poor stress transfer and underutilization of the fiber strength.
Fiber pull-out: During fracture, fibers tend to debond from the matrix and undergo frictional pull-out. This dissipates energy and increases the overall toughness of the composite. A weak interface promotes pull-out while an extremely strong bond leads to less pull-out and brittle fracture.
Environmental resistance: The interface protects the fiber from mechanical abrasion and shields it from damaging environments. A weak interface permits the environment to attack the fiber surface initiating strength degradation, swelling and debonding.
Thermal conductivity: Heat is conducted across the interface from the matrix to the fibers. A weak bond or interfacial voids increase thermal resistance, reducing conductivity. This lowers the maximum service temperature of the composite.
Chemical interaction: Reactions between the fiber and matrix at the interface can produce brittle reaction products which degrade mechanical performance. Compatible sizing applied to the fibers prevents such degradation.
Controlling the fiber-matrix interfacial strength through sizings and surface treatments is crucial to optimizing overall composite properties and performance.
7. What are some common manufacturing processes used to fabricate composite components?
Here are some of the most common manufacturing processes:
- Hand layup – Reinforcing layers or fabrics are impregnated with resin by hand before molding. Simple, low cost, limited to low production rates.
- Spray up – Simultaneous spraying of fiber and resin onto a mold. Used for large, simple parts like boat hulls. High resin content.
- Filament Winding – Fibers are impregnated with resin and then continuously wound over a rotating mandrel to obtain complex shapes like cylinders and tubes.
- Pultrusion – Continuous fibers are impregnated with resin and pulled through a shaped die for constant cross-section parts like rods and beams.
- Resin Transfer Molding (RTM) – Fibers are placed in a mold cavity before liquid resin is injected under pressure. Efficient for complex and large parts in medium production runs.
- Vacuum Bag Molding – Fibers and resins are laid up on a mold before a flexible film is used to apply vacuum pressure for consolidation. Variants include VARTM which uses resin infusion.
- Compression Molding – Molding material is placed in an open, heated mold cavity before the mold halves are closed under high pressure. Used for high volume production.
- Autoclave Molding – Parts are cured in a high pressure, high temperature oven to achieve high fiber volumes and low void content. Used for advanced composites in aerospace applications.
8. How are composite materials tested and inspected for quality control?
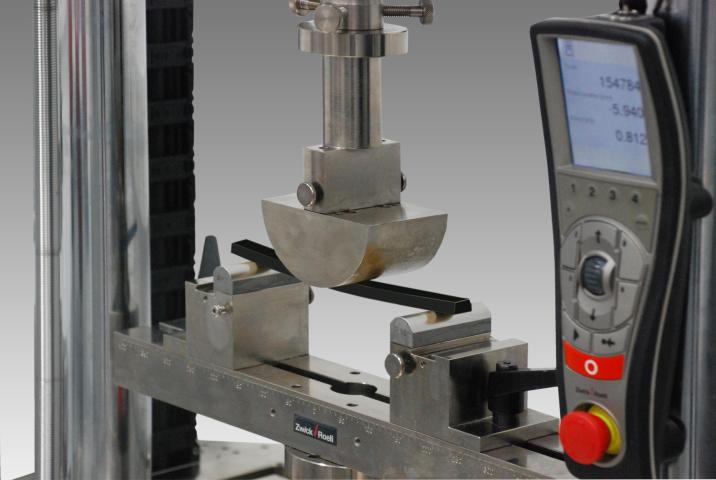
Common test methods for composite quality control include:
- Tensile testing – Assesses ultimate tensile strength, elastic modulus, Poisson’s ratio, strain to failure. Performed according to ASTM D3039.
- Flexural testing – Determines flexural modulus and strength under bending loads. Follows ASTM D7264 test standard.
- Compression testing – Measures compressive properties in fiber direction. Done per ASTM D6641.
- Shear testing – Determines in-plane and interlaminar shear strength and modulus. Follows ASTM D5379.
- Impact testing – Evaluates impact energy for damage and penetration. Follows ASTM D7136 and D5628.
- Fatigue testing – Assesses fatigue strength and life under cyclic loading. Uses ASTM D3479.
- Fracture toughness testing – Determines critical stress intensity factor and matrix toughness. Uses ASTM D5045.
- Chemical resistance testing – Evaluates material stability when exposed to different chemical environments.
- Creep testing – Measures deformation over time under sustained loading at elevated temperature. Follows ASTM D2992.
Inspection methods include visual inspection for defects, tap testing, ultrasonic scanning, radiography, shearography, and thermography to detect flaws in composites.
9. What factors influence the cost of manufacturing composite materials and parts?
Key factors affecting composite manufacturing costs:
- Materials – Carbon fiber is more expensive than glass. Aerospace-grade prepregs are pricier than commodity prepregs.
- Fiber volume fraction – Higher fiber volume gives better properties but increases material cost. Typical range is 50-70%.
- Labor – Extensive manual labor in layup/molding increases costs. Automation reduces labor and cost.
- Number of plies – More unidirectional plies or thicker laminates mean more raw material and cost.
- Processing method – Hand layup is economical at low volumes. Autoclave molding requires high capital investment.
- Tooling – Typical composites tools require high cost due to tight tolerances and surface finish requirements. Consumable or “soft” tooling can reduce cost.
- Production volume – Higher volumes distribute fixed costs and enable economy of scale to lower per part cost.
- Part size and shape – Larger and more complex shapes require more material and processing time. Simpler geometries reduce cost.
- Quality requirements – Aerospace grade composites require more extensive process control and inspection which increase cost.
- Machining/finishing – Trim machining, hole drilling, edge finishing add to cost for final part. Minimizing this reduces cost.
10. What are some emerging trends and innovations in composite materials?
Major trends include:
- Automated manufacturing – Automated fiber placement, automated tape laying, and robotics to reduce labor cost.
- Out-of-autoclave processing – OoA processes like vacuum-assisted resin transfer molding to reduce equipment cost.
- Recycling – Methods to reuse scrap and reclaim value from production waste and end-of-life parts.
- Nanocomposites – Incorporating nanoparticles like graphene and nanotubes to enhance properties at lower loadings.
- Natural fibers – Use of plant-based fibers like flax and hemp as “green” reinforcement alternatives.
- Textile composites – Multidimensional woven fabrics and near net shape preforms to enable complex geometry while reducing waste.
- Smart composites – Embedded sensors to allow real-time monitoring of strain, damage, and other parameters.
- Multifunctionality – Tailoring composites to combine strength with additional properties like electrical conductivity or energy absorption.
- Process monitoring – In situ monitoring to assess cure and detect defects during fabrication, reducing inspection time.
- Multiscale and multiphysics modeling – Advanced simulation tools to optimize designs and predict performance.
- High-volume applications – Increased use of composites in cost-sensitive sectors like automotive and construction through novel materials and manufacturing techniques.