Boom! The deafening sound of explosives cracking rock echoes through the mining tunnel. Whirrrr. Whirrrr. The teeth of a massive tunnel boring machine grind away, inching forward through solid stone. Clank! Clank! Ore cars rattle down tracks carting freshly blasted payload. The sounds of mining bombard the ears, while lungs fill with dust kicked up in the process. It’s dirty, dangerous work. But composite materials are starting to transform and strengthen this gritty industry in ways you’d never imagine.
Seems weird, right? Fragile plastics and textiles revolutionizing the tough world of mining? You betcha! Lighter, stronger composite materials made of fibers like graphite, fiberglass, Kevlar, and carbon are muscling their way into mining. Replacing traditional materials like steel and aluminum, composites provide superior strength-to-weight ratios. That means equipment can haul bigger loads using less fuel while standing up to abusive operating environments. Cha-ching!
So how are these space-age materials reshaping mines of the future? Let’s dig in.
First up, that boring machine carving up solid rock like a Thanksgiving turkey? The cutterhead, once made of steel, is now often built with composite materials or clad in abrasion-resistant composite wear plates. Going with composites lightens the load, reducing power needs and machine wear. Ka-pow!
Ore cars are getting a makeover too. These rugged workhorses used to be built solely from steel. But composite gondolas made of materials like fiberglass now haul heavier payload. And their corrosion resistance gives them longer service lives. Choo-choo!
Even ventilation ducting throughout the mine is utilizing composites. Lighter weight ducts simplify installation and require less structural support. Their durability handles dust and debris kicked up during blasting. Perfect for clearing the air down there!
With composite technology strengthening their game, mines are reaching new levels of productivity and efficiency. Workers can extract more resources while equipment operates smoothly despite harsh conditions. Talk about a winning combo! Who knew that brainy new materials could pump so much innovation and opportunity into the brute force world of mining? The synergistic mix gets ingenuity flowing. And that’s golden.
Pipes and Piping Systems: Channeling Strength Through the Maze
Miles of piping snake through mines, forming a maze of veins funneling water, ventilation, and slurry transport. Traditional steel and HDPE pipes withstand corrosion and abrasion. But they’re heavy. And their rigidity complicates installation, requiring extra fittings and supports. What a headache!
Enter composite piping. These pliable pipe designs based on materials like thermoset resin and fiberglass reinforcements are changing the game. Their outstanding strength-to-weight ratio allows larger diameter composite pipes to replace smaller traditional pipes. And their flexibility eases installation around turns and through uneven tunnels. Drilling and anchoring to hang pipes is often reduced too. Talk about a relief!
Composite pipe joints are also revolutionizing down there. Steel couplings require heavy wrenches to bolt pipe ends together. But composite joints made of tough thermoplastics use quick connect or interference fit designs. Pull, click, twist, lock! They go together fast by hand without messy solvent cement. Installation time and costs plummet!
Pumps are pumped up too. Composite impellers weigh less than metal designs, reducing load on motors. Housings reinforced with materials like carbon fiber withstand pressure and corrosion, maximizing service life. For slurry transport, composite pipesexcel. Non-stick surfaces maintain efficiency by resisting material buildup. And they fight corrosion as abrasive slurries churn through. No erosion allowed!
By combining extreme durability, lightweight versatility, and ease of handling, composite piping solutions are optimizing flow and transport underground. As smart materials muscle their way into mines, workers breathe easier and installation gets simpler. Now that’s smooth flowing progress worth tapping into!
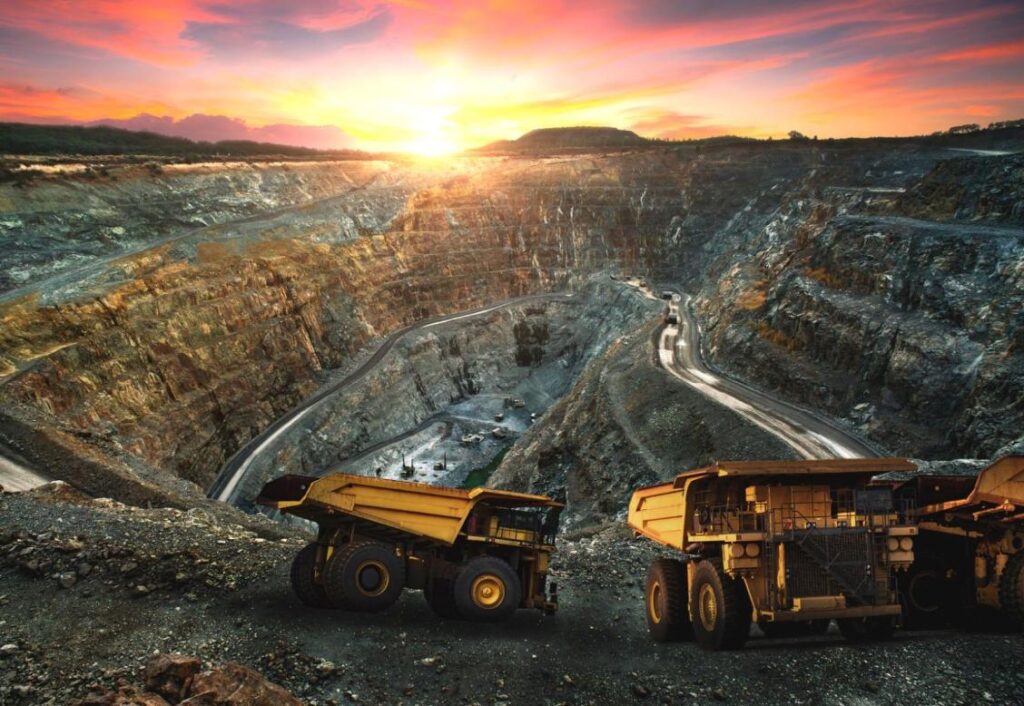
Tanks and Storage Solutions: Composite Materials in the Background
Deep in the bowels of mining operations, composites work quietly but critically behind the scenes. Massive tanks hold water and chemical solutions for vital processes like mineral processing and water treatment. Traditionally made from steel or concrete, these huge vessels now utilize composite materials to offer advantages.
For starters, corrosion resistance. The mineral-rich, wet environments common in mines aggressively attack traditional tank materials. But fiber-reinforced plastic (FRP) composite tanks withstand these punishing conditions. Tanks made of vinylester and polyester resins blended with glass fibers have an especially long service life. No rust, no problem!
Composite materials in mining also provide superior strength-to-weight ratios, allowing larger capacities in tight spaces underground. Installation is simplified due to lightweight components that are easily assembled on site. And with no repainting or corrosion-prevention required, maintenance is minimal. Out of sight, out of mind!
Storage tanks for fuel and other hydrocarbons utilize composite containment systems too. Inner tanks made of materials like HDPE eliminate corrosion while composite outer shells provide structural support. Interstitial space allows monitoring between walls. Secondary containment to prevent leaks is mandatory in mines, and composites fit the bill.
Inert, non-reactive composites also safely store aggressive chemicals like cyanide used in leaching processes. Cyanide tanks equipped with composite structural reinforcements and liners ensure reliable corrosion resistance. Playing it safe takes priority with composites!
Down in the dark depths, these rugged and low maintenance tanks provide critical support out of the spotlight. Composites withstand tough conditions over decades of service, enabling smooth ongoing operations. Their hidden role keeping mines functioning makes them MVPs of the underground.
Structural Components and Support Systems: Skeletons of Strength
Mines require extensive structural support. Ladders, platforms, ramps and stairways allow worker access. Conveyor belts move materials. Retaining walls and meshes prevent cave-ins. Traditional steel or wood construction strains under these demands. But composites are reinforcing and reinventing underground structures and systems.
Fiber-reinforced plastic (FRP) composites are replacing steel in ladders and stairways. Their corrosion resistance handles humidity and chemical exposure. Electrical resistivity increases safety. FRP’s strength and light weight eases installation in tight drifts and shafts compared to heavy and cumbersome steel. And visibility is enhanced, reducing accidents.
Conveyor structure assembly is speeding up too. FRP sections are prefabricated offsite for rapid on-site installation. Dimensional consistency improves precision while reducing heavy equipment needs. Maintenance-free FRP withstands abrasion from material transfer over decades. Now that’s moving in the right direction!
Retaining structures like ribs and meshes traditionally relied on steel, concrete and shotcrete. But FRP composites in forms like glass fiber rebar and cellular confinement systems are proving superior. Their lightweight flexibility suits unstable ground conditions. Corrosion resistance and high strength enhances long-term stability. And lighter weight means less load on weakened ground. Disaster avoided!
Platforms, handrails, and access ladders also utilize high-strength, lightweight FRP composites that simplify installation in tight drifts. Durability and corrosion resistance withstand exposure. And unlike steel, FRP won’t conduct electricity, improving safety. Plus, it won’t ice up in low temperatures. Sure footing everywhere!
Down there in the deep, composites provide critical structural support with less weight yet extreme strength. As materials technology advances, mines are able to safely reinforce operations while reducing risks. That’s the kind of structural innovation that drives progress!
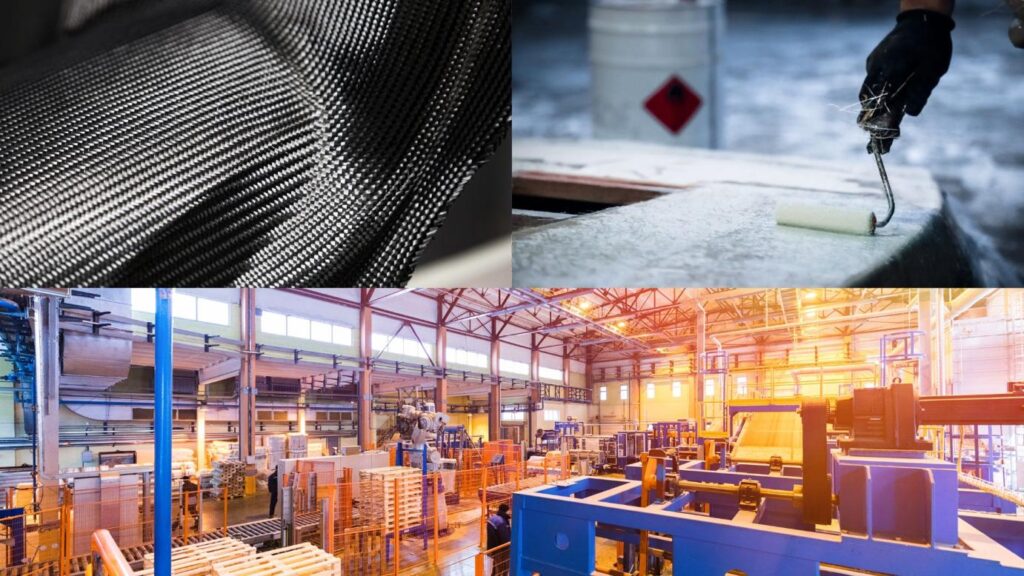
Conveyor Belts and Conveyor Systems: An Endless Cycle of Strength
Winding through miles of subterranean tunnels, conveyor belts are the circulatory system of mines, constantly moving material. Traditional rubber belts withstand abrasion but require heavy support systems and frequent maintenance. Now, next-gen composite conveyor belts are stepping up with super strength.
These new belts integrate tough polyethylene or polyester fabrics with high-strength fiber reinforcements. Aramid fibers like Kevlar provide tensile strength while rip-stop and curve-flex weaves enhance durability. Steel or PVC cables running longitudinally through the belt increase rigidity.
The result? Composite belts boast up to twice the tensile strength of conventional belt designs. They resist cuts and impacts from large falling rocks while maintaining flexibility. Long-lasting and easy to repair, their advanced materials reduce downtime. No wonder they’re pulling ahead!
But it’s not just the belt that’s getting an upgrade. Many components in the conveyor system are moving to composites. Super-slick UHMW-PE skirting prevents material buildup. Pultruded FRP troughing rollers ease belt alignment while resisting wear and corrosion. . Pulleys contain lubrication-free composites bearings. Lighter weight yet super strong drive drums rotate thousands of hours without maintenance.
By reinventing each aspect of conveyor technology with composites, mining operations gain big advantages. Extended service life, reduced power consumption, and lower maintenance keeps material moving safely and efficiently. Talk about a revolution in uptime!
For mines, these next-gen conveyor belts and systems are the beating heart of productivity. Their material muscle and longevity keeps operations flowing nonstop. So count on composites to just keep on trucking!

Protective Gear and Personal Safety Equipment: Outfitting Safety from Head to Toe
Whether inspecting dark passages or handling heavy machinery, danger lurks everywhere underground. So keeping miners safe means outfitting them in durable, specialized gear from headlamp to toe. The construction of this lifesaving equipment is being transformed by composite materials technology.
Let’s start with the cap lamp. Fiber reinforced housings withstand knocks and drops that would shatter traditional glass and plastic lamps. Durable enough for daily abuse underground. Their lightweight keeps hardhats securely in place for hours on end. And high-temperature composites allow integration of brighter, hotter LED modules without melting. Bright thinking!
Speaking of hardhats, models reinforced with aramid fibers provide ballistic protection from falling debris while remaining lightweight for all day wear. Tough but comfortable. They’ve got your head covered!
Protective eyewear is also utilizing composites. Sporty wraparound frames constructed from flexible yet robust composite materials withstand scratching and most impacts while improving fit. The future’s looking bright and clear.
Underfoot, composite toe caps and midsoles make work boots more durable, chemical resistant and safer than traditional leather. Aramid fiber shank plates prevent punctures to the sole. Comfortable, protective and compliant with safety codes. Now those are some seriously sturdy kicks!
First responders wear flame-resistant outerwear woven from oxidized polyacrylonitrile fibers. These thermally stable composites form a protective barrier between the wearer and fire while allowing body moisture to escape. Built to handle the heat!
By leveraging composites in personal protective equipment, mines equip their workforce with apparel that’s impervious to abuse. As materials science steps up to safeguard their most valuable resource – people – the future underground looks brighter.