
Pipes can burst for several common reasons, including corrosion, freezing temperatures, high water pressure, accidental damage, and more. When pipes burst, it causes major water damage and is a plumbing emergency. Traditionally, burst pipes are repaired by welding, clamping, or fully replacing the damaged section. However, these methods can be expensive, time consuming, disruptive, and require special skills. An alternative solution is using composite materials such as fiberglass cloth and epoxy resins to reinforce and repair burst pipes. Composite materials can create a durable “cast” around the damaged section, restoring strength and preventing leaks. This article will provide a comprehensive guide on using composite materials to repair burst pipes, featuring products and services from Innovellix, a leading company in composite pipe repair solutions.
What are Composite Materials and How Do They Work?
Composite materials refer to products made by combining two or more materials with distinct characteristics to create an end material with enhanced properties. The individual materials work together to give the composite materials increased strength, lightness, corrosion resistance, or other beneficial qualities. Some common examples of composite materials are:
- Carbon fiber: Made of thin strands of carbon bonded together with epoxy resins. Extremely strong and light. Used in aircraft, race cars, sporting goods, etc.
- Fiberglass: Made of extremely fine glass fibers woven into a cloth-like material and bonded with epoxy or polyester resins. Used for boat hulls, surfboards, pipes, storage tanks, etc.
- Kevlar: Made of aromatic polyamide fibers woven together and bonded with resins. Used for bulletproof vests, helmets, brake pads, etc. due to its high strength.
To repair burst pipes:
- The pipe surface is cleaned and roughened up to allow the composite materials to bond properly.
- Resin material is used to saturate fiberglass cloth, which helps the cloth harden into a solid, pipe-shaped shell.
- The resin-saturated cloth is wrapped around the damaged section of pipe.
- As it cures and hardens, it forms a reinforced “cast” around the pipe.
This cast is corrosion resistant, structurally strong, and seals leaks. It also protects the damaged pipe from further deterioration.
What are the Advantages of Using Composite Materials for Pipe Repair?
Composite materials offer many advantages for reinforcing and repairing burst pipes: Lightweight and Easy to Apply
- Fiberglass cloth and resins are much lighter than metal replacement parts or welds.
- Composite materials are wrapped externally around the damaged pipe so there is no need for pipe removal.
- Application is simple and various pipe configurations like bends and elbows can be accommodated.
Cost Effective and Time Saving
- Entire pipe sections do not need replacement.
- Less heavy equipment, excavation, downtime required compared to pipe replacement.
- Cures rapidly allowing quick return to service.
Durable and Long Lasting
- Withstands corrosion, abrasion, vibration and pressure fluctuations over decades.
- Can last 50+ years even in harsh conditions.
- Maintains strength and pipe integrity as it ages.
Safe and Environmentally Friendly
- Composite application produces no flames, sparks or hazardous fumes.
- Creates no site contamination or waste products to dispose of.
Versatile
- Effective on many pipe materials like concrete, steel, iron, PVC etc.
- Can repair joints, cracks, holes, gouges, bursts or severely corroded sections.
- Suitable for a very wide range of pipe sizes from 1⁄2 inch to several feet diameter.
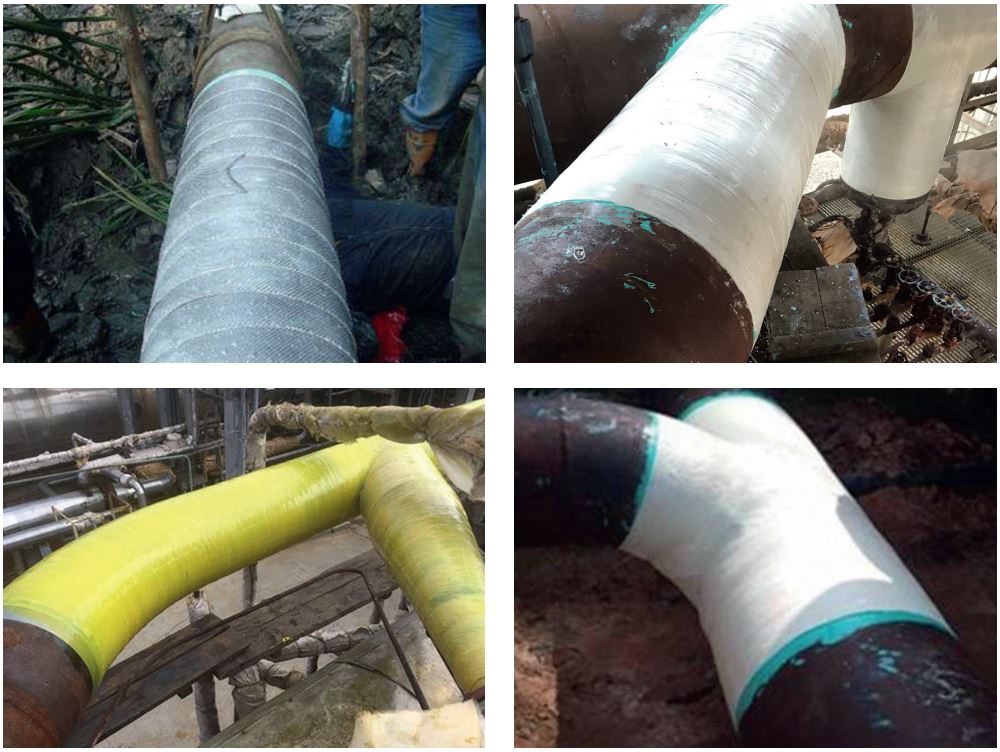
Why Choose Innovellix for Your Composite Pipe Repair Needs?
Innovellix is a pioneering industry leader in composite pipe repair products and services. With over 20 years experience, Innovellix has successfully completed repairs for hundreds of clients across critical industries like oil and gas, chemical, mining, wastewater and power generation. The company is highly regarded for technical expertise, innovative products and exceptional service. Innovellix Composite Pipe Repair Solutions Innovellix offers a complete line of high performance composite pipe repair materials including epoxy, polyurethane and vinyl ester resins paired with fiberglass, carbon and other reinforcing fabrics. An extensive product range allows precision matching to operating temperatures, pressures, fluid exposures and other requirements. Innovellix Composite Wrap Pipeline Repair The patented Innovellix Composite Wrap system can reinforce pipe defects on straight runs, bends, elbows, diameter transitions and more without stopping flow. Custom designed for each application, the composite wrap integrates seamlessly with existing line layouts. Innovellix Composite Pipe Repair Services Innovellix technicians are highly experienced in assessing damage, calculating repair design parameters, installing composite materials and quality testing finished applications. Services range from small scale emergency repairs to large multi-year maintenance contracts managing facilities’ entire composite repair needs. Why Innovellix is the Right Choice With Innovellix, clients gain a true partner for the life of their assets. A partial list of advantages includes:
- Decades of real-world experience across entire application spectrum
- Cutting-edge proprietary repair products proven in the field
- Large technical staff enables custom solutions for unique needs
- Industry leadership in quality processes and safety standards
- Rapid 24/7 response to emergency repair situations
- Single source for all composite pipe repair requirements
How to Use Innovellix Composite Pipe Repair Solutions
Using Innovellix composite solutions to reinforce burst or damaged pipes is straightforward: Step 1: Contact Innovellix with details about your pipe damage. Provide pipe specifics like material, size, years in service etc. as well as operating conditions. Step 2: Innovellix engineers will assess the damage and calculate exactly how much composite material is required for a successful repair. An official quote or proposal will be provided outlining the custom recommended resin and reinforcing fabrics for your application. Step 3: Schedule the repair work with Innovellix technicians at your convenience. The damaged section of pipe must be safely accessible. Take appropriate measures to depressurize and drain the pipe if necessary. Step 4: At the repair site, Innovellix crews will prepare the surface, apply release agents, saturate fabric with resins and wrap the pipe, adding layers until the design thickness is achieved. Step 5: Once the composite repair has fully cured, pressure test to validate strength and leak sealing. Finish with inspection and documentation of the completed job. Your pipe is now restored to original working integrity with the added benefits of corrosion resistance and long term durability thanks to its composite reinforcement!
What are the Challenges of Using Composite Materials for Pipe Repair?
While composite repair is highly effective, there are some challenges to consider: Surface Preparation Pipe surfaces must be thoroughly cleaned, dried and abraded to allow composite materials to bond tightly. Surface preparation takes time. Defect Assessment The pipe defect must be carefully measured to design an appropriately sized repair. If undersized, performance will be compromised. Quality Control Applying composites is part science, part art. Operators must be skilled so repairs meet engineering specifications. Testing ensures strength. Personnel Specialized training and certification is required for personnel doing surface analysis, composite calculations and hands-on installation work. However, Innovellix actively helps clients address these challenges. Surface profiling, repair design, personnel competency development and inspection processes are all part of comprehensive Innovellix service capabilities.
common causes and consequences of burst pipes: Causes:
- Freezing temperatures: As water in pipes freezes and expands, it can lead to bursts. This is common in areas not built for freezing weather.
- Old pipes: Over time, pipes corrode and weaken, making them more likely to burst from pressure.
- High water pressure: Excessive water pressure stresses pipe walls and causes bursts.
- Accidents/damage: Construction work, falling objects, etc. can physically damage pipes.
- Tree roots: Roots that invade and block pipes can cause bursts.
- Clogs: Blockages raise pressure and can burst pipes.
Consequences:
- Flooding: Burst pipes release high volumes of water, causing flooding, water damage to structures, erosion, mold, etc. This can require extensive repairs.
- Interruptions: Bursts cut off water supply for households and businesses, disrupting daily life.
- Injuries: Exposure to floods from burst pipes can cause injuries from slips/falls.
- High costs: Pipe repairs, flood recovery efforts, property damage claims lead to high economic costs.
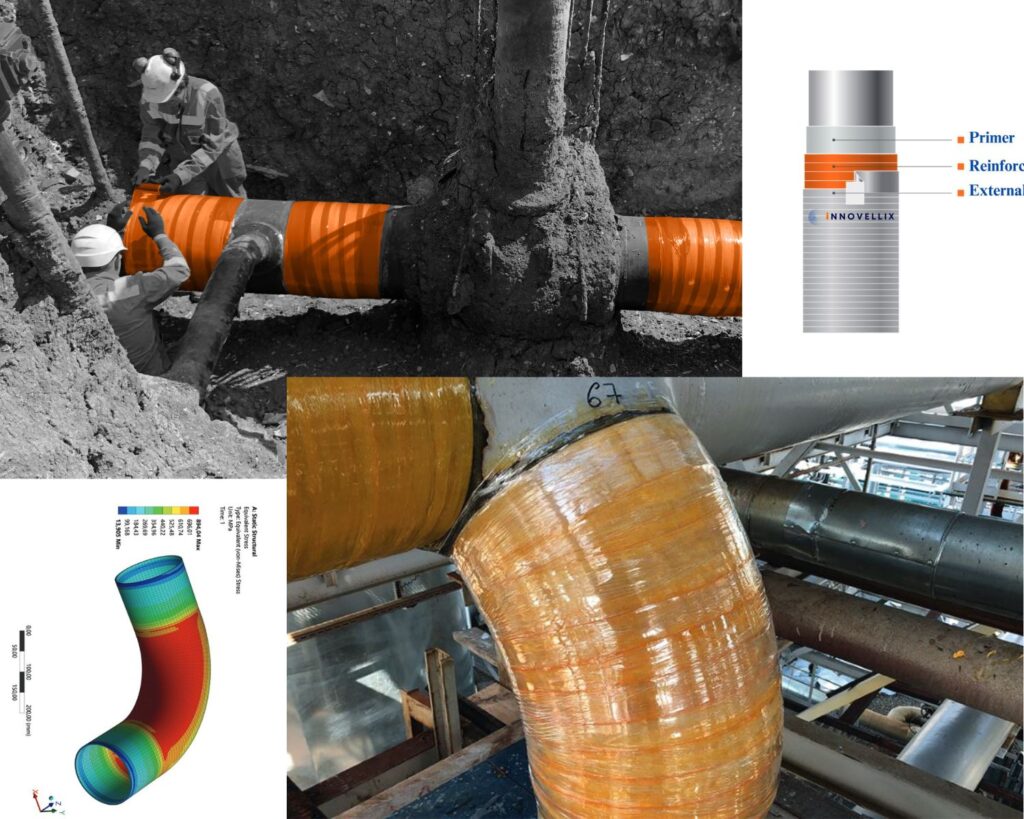
In summary, burst pipes are usually caused by freezing, pressure, corrosion, accidents, or clogs. The consequences include flooding, water damage to property requiring expensive repairs, loss of water service, injuries, and high overall economic costs. Proper maintenance and pressure regulation can help prevent bursts.
What are the main advantages of using composite materials to repair burst pipes?
Composite materials offer several key benefits for repairing burst pipes compared to traditional metallic repair methods like welded steel sleeves. Using composites can reduce repair time, restore full pipe strength, extend service life, and limit future corrosion.
Faster Repairs and Less Downtime
A major advantage of composite pipe repairs is the ability to complete jobs much faster with less downtime compared to cutting out and replacing pipe sections. Composites cure rapidly, allowing repairs to be returned to service in 24 hours or less in many cases. The alternative of welding steel sleeves is far more labor and time intensive. Composite wraps can also stop active leaks when combined with a filler material, avoiding the need to immediately take the pipe out of service. This allows for a temporary patch until the full composite reinforcement can be installed after the leak is contained. The potential to avoid pipe depressurization is a huge bonus.
Restoring Full Strength and Stiffness
Properly designed composite reinforcements are engineered to withstand the operating pressures and mechanical loads on the pipe. The composite materials share stresses with the pipe wall, restoring strength to meet or exceed original specifications. In fact, composite repairs have been proven to increase burst pressures and fatigue life compared to unrepaired defects through extensive full-scale testing. Composites also enhance stiffness to resist further deformation from dents, gouges, or other damage.
Extending Service Life
While steel sleeves have a finite lifetime before corrosion attacks the weld joints, composites are highly resistant to corrosion even in the harshest environments. The adhesive resin provides an impermeable moisture barrier to protect the pipe exterior underneath. Research on long-term composite pipe repair performance shows excellent retention of strength and interlaminar shear properties after many years. Some field installations have now been in place over 20 years and remain in “like new” condition. This durability exceeds traditional repair methods.
Limiting Further Corrosion
In addition to sealing off pipe defects, composite materials serve as an external protective barrier against further corrosion damage. The resin encapsulates the pipe surface while the fiber reinforcement provides impact and abrasion resistance. By leaving the original pipe intact rather than cutting it out, future corrosion growth along existing welds or at heat affected zones is also avoided. This gives composites an advantage for extending asset service life compared to welded steel repairs.
Other Benefits
Composite pipe repairs offer a few other advantages as well:
- Lower safety risks – No hot work permits or confined space entries required
- Greater flexibility – Can reinforce complex geometries like elbows, tees, even leak sites
- Lightweight – Easier handling than heavy welded steel sleeves
- Cost savings – Lower installation expense for many applications
In summary, composite reinforcement is an advanced repair technique that can maximize remaining pipe strength and service life at a reasonable cost. The faster repairs and reduced downtime translate into major advantages for keeping critical pipelines operating safely. With an experienced design team and proper installation procedures, composites provide reliable and long-lasting repairs.
FAQ
What are the key differences between pipe repair using composite wraps versus steel sleeves?
Composite wraps and steel sleeves offer two distinct repair methods for reinforcing pipeline defects like corrosion or mechanical damage. While both can restore pressure containment, there are some notable differences:
Installation & Safety
A major advantage of composites is the simpler, safer installation process compared to welding heavy steel sleeves. Composite materials are wrapped onto pipe surfaces using a wet layup technique with resins that cure at ambient temperatures. This avoids hot work permits, confined space entries, and other risks associated with welding or metal fabrication. The composite fabric and adhesive resin are also much lighter than steel sleeves, avoiding heavy lifts or special equipment. Installations can typically be performed by a small 2-3 person crew without needing certified welders. The lower temperatures and elimination of welding fumes or arc flash hazards also improve the work environment.
Flexibility & Conformability
The wet resin used with composites allows the fiber reinforcement to conform closely to many pipe surfaces, including irregular shapes like wrinkle bends or ovalities. This provides good intimacy and adhesion over the full repair area. Rigid steel sleeves can struggle matching complex pipe geometries. Composite materials are designed to be anisotropic, with tailorable strength and stiffness properties in different directions. This allows the fiber architecture to be optimized for expected load conditions. Steel has fixed isotropic properties.
Long-Term Durability
While steel sleeves rely on coating systems to prevent external corrosion, the composite matrix provides an impermeable moisture barrier along with impact and abrasion resistance from the fibers. Well-designed composites show excellent retention of mechanical properties after many years in aggressive soil or underwater environments. The composite installation process also avoids creating new welds vulnerable to corrosion or weld defects over time. Any corrosion under an existing weld is left undisturbed. Thermal expansion mismatches between composites and steel are accommodated by the resin system.
Customization
Composite materials can be produced in many widths tailored to specific pipe diameters. A single fabric roll length can reinforce multiple repair lengths on various pipe sizes, allowing flexible inventory. This differs from steel sleeves that require close fit-up and often need custom fabrication for a given application. The composite thickness applied can also be varied to match operating pressures, defect severity, and other loads. This optimized “right-sizing” can save unnecessary material costs in some cases. Steel sleeves have a fixed thickness.
Performance Testing
Lastly, advanced composite systems undergo extensive third-party testing to validate long-term performance under sustained pressures, fatigue cycling, bending loads, and other stringent conditions. This includes testing actual field installations to failure to prove safety factors. Most steel sleeves lack this degree of full-scale testing. In summary, composite reinforcement offers a versatile, durable, and rigorously-validated repair technique with safety and installation advantages over traditional steel sleeves. While advanced engineering is still vital for proper design, composite materials enable high-performance repairs under a wide range of demanding applications.
What data exists on the long-term performance of composite pipe repairs in gas pipelines?
There are several major long-term testing programs focused specifically on validating the durability of composite repairs in high pressure gas transmission pipelines. Key findings demonstrate continued excellent performance exceeding 20+ years in some cases:
PRCI Composite Repair Study
The Pipeline Research Council International is conducting an extensive 10-year buried pipe study on composite repairs from 10 different manufacturers, including cyclic pressure testing and periodic burst tests. The program involves Grade X42 pipe samples with machined corrosion patches that are reinforced with various composite systems and monitored using strain gages over the multi-year testing duration. Early results after 3 years show strain reductions ranging from 23-62% beneath the composite repairs compared to unreinforced samples. All repairs are maintaining or increasing burst pressures relative to the baseline measurements, with no indications of performance decline thus far. The study is providing valuable data for qualifying the long-term permanence of repairs.
Stress Engineering 20-Year Exposures
Independent assessments by Stress Engineering Services have examined composite repair performance after prolonged environmental exposures. This includes 20-year marine immersion testing, along with field installations from operating pipelines that have been in place over 15 years. Results found excellent retention of composite strength, stiffness, and interlaminar shear properties in the long-term samples. Any strength knockdowns following aggressive aging conditions were minor compared to the high safety factors designed into the repairs. Real-world repairs showed no indications of reduced integrity over time.
Natural Gas STAR Partners
The EPA’s Natural Gas STAR program cites extensive use of composite repairs by partner pipeline operators with installations exceeding 10 years of service. The repairs continue to perform as designed without any issues related to environmental durability or cyclic pressures. Collectively, these major industry exposure programs provide substantial evidence that properly designed composite systems can maintain structural reinforcement and protective capabilities over decades in gas pipeline applications. When combined with sound engineering practices and quality installation procedures, composites present a reliable long-term repair option.
Can composite materials repair other defects beyond corrosion like dents and wrinkle bends?
Yes, composite reinforcement has been proven effective at restoring the integrity of several pipeline anomalies beyond just external corrosion defects:
Wrinkle Bends
These vintage construction features create localized buckles and high strain concentrations under operating pressures. The flexibility of composite materials allows them to intimately conform to the wrinkle profile. Testing shows average strain reductions over 40% in reinforced wrinkle bends, with proportional increases in fatigue life. Properly designed composites can reliably reinforce wrinkle bend cracks and fatigue damage long-term. The anisotropic properties also enable tuning the axial and hoop stiffness as needed. Wrinkle severity, pressure cycling impacts, and soil movement must still be assessed.
Plain Dents
Extensive research demonstrates composites reliably restoring burst capacity to depths up to 25% of the pipe diameter with no metal loss. The composite shares and reduces strain in the locally deformed region. Performance is strongly dependent on dent depth, with deeper cases needing more sophisticated analysis.
Mechanical Damage
Gouges, scrapes, metal loss, and other mechanical defects can also be reinforced using composites. This includes interacting damage like dents with gouges. The composite structural reinforcement restores hoop strength around the damaged area. Stress concentrators and crack initiators may still need to be addressed.
Bends & Elbows
The wet resin used in composites enables adhesion even on complex geometries like bends, elbows, tees, and flanges. The material can conform to most surfaces. Designs must account for the added bending strains alongside pressure stresses. In many cases, small localized composite repairs can remedy defects rather than replacing entire spool pieces. When combined with rigorous engineering analysis and testing, composites present expanded options for a range of pipeline anomalies. Certified installation and QA procedures remain critical for unconventional applications.
What standards and guidelines exist for properly designing and installing composite pipe repairs?
There are two major composite pipe repair codes with detailed requirements on qualification testing, design methods, materials selection, installation procedures, inspection, and documentation:
ASME PCC-2 Article 4.1
Developed by the American Society of Mechanical Engineers, ASME PCC-2 Article 4.1 provides guidance specifically for non-metallic composite reinforcement systems used in high risk applications like high pressure steel pipelines. This code outlines minimum requirements for short-term burst tests, environmental conditioning, fatigue cycling, defects simulations, and other performance validation tests. Various design equations are given based on laminate theory for calculating the required composite thickness and length. Additionally, ASME PCC-2 Article 4.1 includes specifications on surface preparation, application procedures, cure times, quality control, and documentation for composite repair installations. Compliance certifications are available but not formally required.
ISO 24817 Standard
The International Organization for Standardization publishes ISO 24817 which covers composite repairs across the full oil and gas sector. This includes pipelines, pressure vessels, tanks, and other assets. Like ASME PCC-2, ISO 24817 standard stipulates qualifications testing, composite design methodology, materials specifications, documentation procedures, and other requirements tailored specifically for polymeric composite reinforcements. Certification schemes are being developed to audit and qualify specific products or installation contractors to ISO 24817 rather than just self-declared compliance. This formal oversight aims to better regulate the global composite repair industry. Between these two codes, operators have sound technical guidance to properly design, install, and document composite reinforcements for restoring pipeline integrity. Further research and standards development continues to expand into more complex applications as the technology matures.