Mining operations face numerous challenges, including the exposure of equipment and structures to harsh environments that can lead to corrosion and deterioration. In recent years, composites have gained significant attention for their exceptional corrosion resistance and durability in the mining industry. This article explores the benefits of composites, their applications in mining, and their role in enhancing the longevity and efficiency of mining operations.
Table of Contents
- Composites in Mining Industry
- Understanding Corrosion in the Mining Industry
- The Significance of Corrosion Resistance and Durability
- Composite Materials and Their Unique Properties
- Applications of Composites in Mining
- Benefits of Composites in the Mining Industry
- Challenges and Considerations
- Future Developments and Innovations
- Conclusion
- FAQs
1. Composites in Mining Industry
The mining industry plays a crucial role in the global economy, extracting valuable resources from the Earth. However, mining operations often face adverse conditions such as exposure to corrosive substances, extreme temperatures, and high mechanical stress. These conditions can lead to rapid deterioration of traditional materials, resulting in increased maintenance costs and downtime. To overcome these challenges, the use of corrosion-resistant and durable materials, such as composites, has emerged as an innovative solution.
2. Understanding Corrosion in the Mining Industry
Corrosion is a natural electrochemical process that occurs when metals are exposed to certain environments. In the mining industry, corrosive agents such as acidic or alkaline solutions, abrasive minerals, and moisture pose a significant threat to equipment, infrastructure, and machinery. Corrosion can weaken structures, reduce operational efficiency, and increase safety risks. Therefore, finding materials with high resistance to corrosion is essential for sustainable mining operations.
3. The Significance of Corrosion Resistance and Durability
Corrosion resistance and durability are crucial factors in the mining industry. By employing corrosion-resistant materials, mining companies can extend the lifespan of equipment and structures, reduce maintenance costs, and ensure safe and efficient operations. Durability is equally important as it ensures the longevity of components, reducing the need for frequent replacements and repairs. Composites offer exceptional corrosion resistance and durability, making them an ideal choice for various mining applications.

4. Composite Materials and Their Unique Properties
Composites are engineered materials that combine two or more distinct components to create a material with enhanced properties. Typically, composites consist of a reinforcing phase, such as fibers or particles, embedded within a matrix material. The reinforcing phase provides strength and stiffness, while the matrix material protects the reinforcing phase and provides additional properties like corrosion resistance.
Composite materials offer several unique properties that make them well-suited for the mining industry. They possess high strength-to-weight ratios, excellent corrosion resistance, and exceptional mechanical properties. Composites can be tailored to specific applications, allowing for optimal performance in various mining environments.
5. Applications of Composites in Mining
Composites find extensive applications in the mining industry, ranging from structural components to protective coatings. Some common uses include:
5.1. Pipes and Tanks
Composite pipes and tanks are widely used in mining operations due to their corrosion resistance and durability. They offer excellent resistance to chemical and abrasive attacks, reducing the risk of leaks, and extending the service life of these critical assets.
5.2. Conveyor Systems
Composite materials are employed in conveyor systems, offering high wear resistance and reduced friction. This enhances the efficiency and reliability of material transportation in mining operations.
5.3. Structural Components
Composites are utilized in structural components such as support beams, gratings, and panels. These materials provide high strength and stiffness while resisting corrosion and minimizing maintenance requirements.
5.4. Protective Coatings
Composites can be applied as protective coatings to mining equipment and structures, safeguarding them against corrosive agents. These coatings act as barriers, preventing direct contact between the corrosive environment and the underlying materials.
6. Benefits of Composites in the Mining Industry
The use of composites in the mining industry offers numerous benefits:
- Enhanced Corrosion Resistance: Composites exhibit superior resistance to corrosion, reducing the need for frequent maintenance and replacements.
- Extended Service Life: Composites’ durability and resistance to harsh conditions enable mining equipment and structures to operate for longer periods without significant deterioration.
- Weight Reduction: Composites are lightweight, leading to reduced transportation costs and improved energy efficiency in mining operations.
- Improved Performance: The exceptional mechanical properties of composites, such as high strength and stiffness, enhance the overall performance of mining equipment and structures.
- Cost Savings: By minimizing maintenance requirements, reducing downtime, and extending the service life of assets, composites contribute to significant cost savings for mining companies.
7. Challenges and Considerations
While composites offer compelling advantages, their implementation in the mining industry is not without challenges. Some key considerations include:
- Cost: Composites can have higher upfront costs compared to traditional materials. However, the long-term benefits and savings often outweigh the initial investment.
- Design and Testing: Proper design and rigorous testing are essential to ensure the suitability and reliability of composite materials in mining applications.
- Compatibility: Composites must be compatible with existing infrastructure and systems within mining operations to ensure seamless integration.
8. Future Developments and Innovations
The ongoing research and development in composite materials hold promising prospects for the mining industry. Advancements in composite manufacturing techniques, novel matrix materials, and improved reinforcement technologies will further enhance their properties and expand their applications. Future innovations may include self-healing composites, smart sensors embedded within composites, and advanced nanocomposites with enhanced performance.
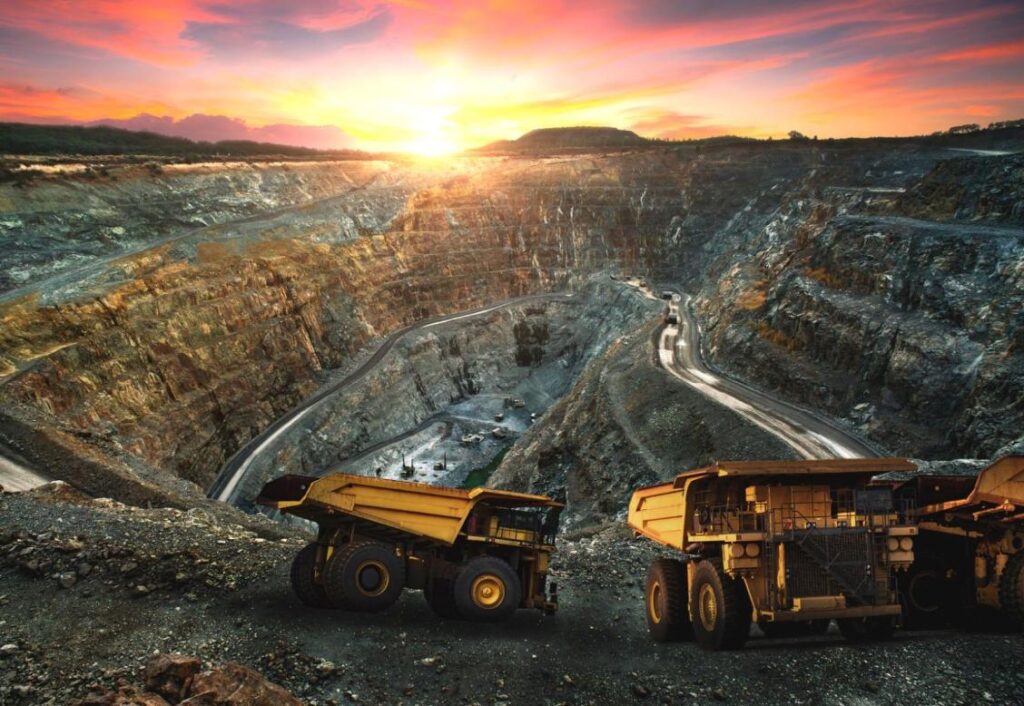
9. Conclusion
In conclusion, corrosion resistance and durability are critical factors in the mining industry to ensure the longevity and efficiency of operations. Composites offer exceptional properties that address these challenges, making them an ideal choice for various mining applications. By utilizing composites, mining companies can reduce maintenance costs, extend equipment lifespan, and enhance overall operational performance. As research and development continue, the future of composites in mining looks promising, ushering in a new era of sustainable and resilient mining practices.
10. FAQs
Q1. Are composites more expensive than traditional materials in the mining industry?
While composites may have higher upfront costs, their long-term benefits and cost savings often outweigh the initial investment. Their enhanced durability and corrosion resistance reduce maintenance costs and extend the service life of assets.
Q2. Can composites withstand extreme temperatures encountered in mining operations?
Yes, composites can be engineered to withstand a wide range of temperatures, making them suitable for mining applications that involve extreme heat or cold environments.
Q3. How do composites contribute to environmental sustainability in the mining industry?
Composites’ lightweight nature reduces transportation costs and energy consumption, leading to a smaller carbon footprint. Additionally, their extended service life reduces the need for frequent replacements, minimizing waste generation.
Q4. Can existing mining infrastructure accommodate the use of composites?
Yes, proper design and compatibility considerations ensure the seamless integration of composites with existing mining infrastructure. It is essential to work closely with engineering experts during the implementation process.
Q5. What advancements can we expect in composite materials for mining in the future?
Future advancements may include self-healing composites that can repair damage, smart sensors embedded within composites for real-time monitoring, and advanced nanocomposites with enhanced performance properties.