Oil and gas pipelines are essential infrastructure for the transportation of hydrocarbons from the source to the market. They are also subject to various challenges, such as corrosion, fatigue, erosion, abrasion, impact, temperature fluctuations, pressure variations, and environmental regulations. These challenges can affect the performance, reliability, safety, and sustainability of the pipelines, and increase the operational and maintenance costs.
To overcome these challenges, engineers and operators are increasingly looking for alternative materials that can offer better properties and performance than conventional steel pipes. One of the most promising alternatives is composite materials.
Composite materials are materials that are made of two or more different components that have different physical and chemical properties. When combined, these components create a new material that has superior characteristics than the individual components. For example, a composite material can have higher strength, stiffness, corrosion resistance, fatigue resistance, thermal stability, or electrical conductivity than its constituents.
Composite materials have been used in various industries, such as aerospace, automotive, marine, construction, and sports. However, their application in oil and gas pipelines is relatively new and emerging. Composite pipes have several advantages over steel pipes in oil and gas applications, such as:
- Corrosion resistance: Composite pipes are immune to corrosion caused by water, chemicals, or microorganisms. They do not require any coating or cathodic protection to prevent corrosion.
- Fatigue resistance: Composite pipes can withstand repeated loading and unloading cycles without cracking or failing. They have high fracture toughness and damage tolerance.
- Weight reduction: Composite pipes are lighter than steel pipes by up to 70%. This reduces the transportation, installation, and handling costs of the pipes.
- Lower installation costs: Composite pipes can be installed using simpler and faster methods than steel pipes. They can be spooled, reeled, towed, or drilled without any welding or special equipment.
- Environmental friendliness: Composite pipes have lower carbon footprint and greenhouse gas emissions than steel pipes. They also reduce the risk of oil spills and leaks that can harm the environment.
According to a report by MarketsandMarkets, the global market size of composite pipes in the oil and gas industry was valued at USD 1.5 billion in 2018 and is projected to reach USD 3.4 billion by 2024, at a compound annual growth rate (CAGR) of 14.4%. The main drivers for this growth are the increasing demand for corrosion-resistant pipes, the rising exploration and production activities in deep water and unconventional reservoirs, and the growing focus on environmental sustainability.
There are different types of composite pipes that are used in oil and gas pipelines, depending on the application and requirements. The most common types are:
- Thermoplastic composite pipe (TCP): This is a composite pipe that consists of a thermoplastic inner liner (such as polyethylene or polyamide) that is reinforced with continuous fibers (such as glass or carbon) embedded in a thermoplastic matrix (such as polypropylene or polyvinylidene fluoride). TCP has high flexibility, chemical resistance, thermal stability, and pressure rating. It is suitable for dynamic applications such as risers, flowlines, jumpers, and umbilicals.
- Glass reinforced plastic (GRP): This is a composite pipe that consists of a thermosetting resin (such as epoxy or polyester) that is reinforced with glass fibers. GRP has high strength-to-weight ratio, corrosion resistance, and durability. It is suitable for static applications such as onshore pipelines, water injection lines, and cooling water lines.
- Fiber reinforced plastic (FRP): This is a composite pipe that consists of a thermosetting resin (such as epoxy or vinyl ester) that is reinforced with fibers other than glass (such as carbon or aramid). FRP has higher strength, stiffness, and temperature resistance than GRP. It is suitable for high-pressure and high-temperature applications such as offshore pipelines, subsea pipelines, and downhole tubing.
The purpose of this guide is to provide an overview of the design, fabrication, installation, testing, and maintenance of composite pipes for oil and gas applications. It will also discuss the cost-benefit analysis, future trends, and opportunities for composite pipes in the oil and gas industry. This guide is intended for engineers and operators who want to learn more about composite materials and their advantages over steel in oil and gas pipelines.
Key Takeaways:
Topic | Summary |
---|---|
What are composite materials? | Composite materials are materials that are made of two or more different components that have different physical and chemical properties. When combined, |
these components create a new material that has superior characteristics than the individual components. | |
Why are composite materials used in oil and gas pipelines? | Composite materials have several advantages over steel pipes in oil and gas applications, |
such as corrosion resistance, | |
fatigue resistance, | |
weight reduction, | |
lower installation costs, | |
and environmental friendliness. | |
What are the main types of composite pipes? | The main types of composite pipes are thermoplastic composite pipe (TCP), |
glass reinforced plastic (GRP), | |
and fiber reinforced plastic (FRP). Each type has different properties and performance depending on the application and requirements. | |
What is the purpose and scope of this guide? | The purpose of this guide is to provide an overview of the design, |
fabrication, | |
installation, | |
testing, | |
and maintenance of composite pipes for oil and gas applications. | |
It will also discuss the cost-benefit analysis, | |
future trends, | |
and opportunities for composite pipes in the oil and gas industry. | |
This guide is intended for engineers and operators who want to learn more about composite materials and their advantages over steel in oil and gas pipelines. |
If you want to know more about composite materials and how they can help you improve your oil and gas pipeline projects, please contact us, the leading provider of composite pipe solutions. Innovellix is a company that specializes in designing, manufacturing, installing, testing, and maintaining composite pipes for oil and gas applications. Innovellix has extensive experience and expertise in delivering high-quality and cost-effective composite pipe solutions for various projects around the world. Innovellix can help you optimize your pipeline performance, reliability, safety, and sustainability with composite materials.
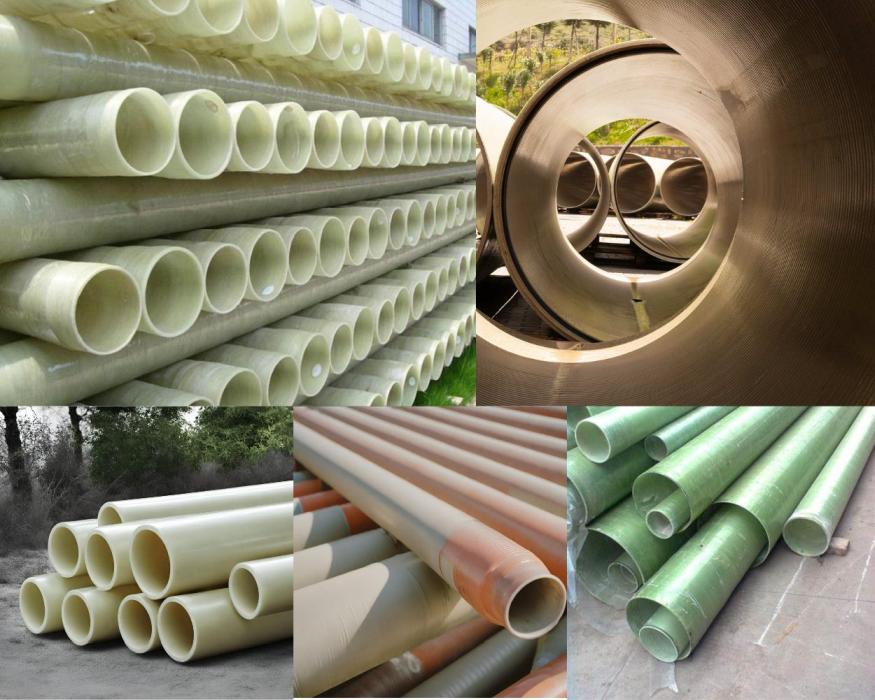
Design Considerations for Composite Pipes
Composite pipes are not a one-size-fits-all solution for oil and gas applications. They require careful design considerations to ensure that they meet the specific requirements and challenges of each project. The design of composite pipes involves selecting the appropriate material, fiber, resin, and reinforcement architecture, as well as applying the relevant design methods and standards. In this section, we will discuss the factors that affect the design of composite pipes, such as pressure, temperature, fluid properties, environmental conditions, and service life. We will also explain how to choose the suitable composite pipe type, such as TCP, GRP, or FRP, for different applications. Finally, we will describe the design calculations and software tools that can be used for composite pipes.
Pressure
One of the most important factors that influence the design of composite pipes is the internal pressure that the pipe has to withstand. The pressure rating of a composite pipe depends on the strength and stiffness of the composite material, as well as the geometry and thickness of the pipe wall. The pressure rating also varies with the temperature and time of exposure, as composite materials tend to degrade over time under high pressure and temperature conditions.
The pressure rating of a composite pipe can be determined by using the hoop stress equation, which relates the internal pressure, pipe diameter, and wall thickness. The hoop stress equation is given by:
σh=2tPD
where σh is the hoop stress, P is the internal pressure, D is the pipe diameter, and t is the wall thickness.
The hoop stress equation assumes that the pipe is thin-walled and isotropic, meaning that it has uniform properties in all directions. However, composite pipes are neither thin-walled nor isotropic. They have varying properties depending on the orientation and arrangement of the fibers and resin. Therefore, the hoop stress equation has to be modified to account for these factors.
One way to modify the hoop stress equation is to use an effective modulus of elasticity for the composite material, which is a weighted average of the longitudinal and transverse moduli of elasticity of the fibers and resin. The effective modulus of elasticity can be calculated by using micromechanics models, such as the rule of mixtures or the Halpin-Tsai model. These models take into account the volume fraction and aspect ratio of the fibers and resin in the composite material.
Another way to modify the hoop stress equation is to use a design factor or safety factor for the composite material, which is a ratio of the allowable stress to the ultimate stress of the material. The design factor or safety factor accounts for the uncertainties and variations in the material properties, manufacturing process, loading conditions, environmental effects, and service life of the composite pipe. The design factor or safety factor can be determined by using empirical data from testing or by following industry standards and guidelines.
Some of the standards and guidelines that provide design factors or safety factors for composite pipes are:
- ISO 14692: Petroleum and natural gas industries — Glass-reinforced plastics (GRP) piping
- API 15S: Specification for Spoolable Reinforced Plastic Line Pipe
- DNVGL-ST-F119: Thermoplastic composite pipes (TCP)
- ASME B31.8: Gas Transmission and Distribution Piping Systems
These standards and guidelines specify different design factors or safety factors depending on the type of composite pipe, application, service condition, and failure mode. For example, ISO 14692 recommends a design factor of 0.67 for GRP pipes used in offshore applications with a service life of 20 years. API 15S recommends a design factor of 0.5 for TCP pipes used in onshore applications with a service life of 50 years.
Temperature
Another important factor that influences the design of composite pipes is the temperature that the pipe has to withstand. The temperature rating of a composite pipe depends on the thermal stability and expansion coefficient of the composite material, as well as the thermal conductivity and heat transfer coefficient of the fluid inside and outside the pipe. The temperature rating also varies with the pressure and time of exposure, as composite materials tend to degrade over time under high temperature and pressure conditions.
The temperature rating of a composite pipe can be determined by using the thermal stress equation, which relates the temperature change, pipe diameter, wall thickness, and thermal expansion coefficient. The thermal stress equation is given by:
σt=αEΔT
where σt is the thermal stress, α is the thermal expansion coefficient, E is the modulus of elasticity, and ΔT is the temperature change.
The thermal stress equation assumes that the pipe is free to expand or contract due to the temperature change. However, composite pipes are usually constrained by the supports or joints that connect them to the rest of the pipeline system. Therefore, the thermal stress equation has to be modified to account for the boundary conditions and compatibility of the pipe with the adjacent components.
One way to modify the thermal stress equation is to use an effective thermal expansion coefficient for the composite material, which is a weighted average of the longitudinal and transverse thermal expansion coefficients of the fibers and resin. The effective thermal expansion coefficient can be calculated by using micromechanics models, such as the rule of mixtures or the Halpin-Tsai model. These models take into account the volume fraction and aspect ratio of the fibers and resin in the composite material.
Another way to modify the thermal stress equation is to use a thermal expansion allowance or compensation for the composite pipe, which is a length or diameter change that is allowed or provided to accommodate the thermal expansion or contraction of the pipe. The thermal expansion allowance or compensation can be determined by using empirical data from testing or by following industry standards and guidelines.
Some of the standards and guidelines that provide thermal expansion allowance or compensation for composite pipes are:
- ISO 14692: Petroleum and natural gas industries — Glass-reinforced plastics (GRP) piping
- API 15S: Specification for Spoolable Reinforced Plastic Line Pipe
- DNVGL-ST-F119: Thermoplastic composite pipes (TCP)
- ASME B31.8: Gas Transmission and Distribution Piping Systems
These standards and guidelines specify different thermal expansion allowance or compensation depending on the type of composite pipe, application, service condition, and installation method. For example, ISO 14692 recommends a thermal expansion allowance of 0.3% of the pipe length for GRP pipes used in offshore applications with a temperature range of -20°C to 80°C. API 15S recommends a thermal expansion compensation of 0.5% of the pipe diameter for TCP pipes used in onshore applications with a temperature range of -40°C to 100°C.
Fabrication Methods for Composite Pipes
Composite pipes are not only designed to meet the specific requirements and challenges of each project, but also fabricated to ensure that they have the desired properties and performance. The fabrication of composite pipes involves forming the composite material into the shape of a pipe, either by applying resin to dry fibers or by using pre-impregnated fibers, and then curing the resin to harden the pipe. There are different fabrication methods for composite pipes, depending on the type of composite material, the geometry and thickness of the pipe wall, and the production rate and quality. In this section, we will discuss the main fabrication methods for composite pipes, such as filament winding, pultrusion, extrusion, injection molding, and braiding. We will also compare the advantages and disadvantages of each method in terms of cost, quality, productivity, and flexibility. Finally, we will describe the quality control and inspection techniques for composite pipes, such as visual inspection, ultrasonic testing, acoustic emission testing, and hydrostatic testing.
Filament Winding
Filament winding is one of the most common and widely used fabrication methods for composite pipes. It is a process that involves winding continuous fibers impregnated with resin around a rotating mandrel or core in a predetermined pattern to form a pipe. The resin can be either thermosetting or thermoplastic, depending on the type of composite pipe. The fibers can be either glass, carbon, aramid, or a combination of them, depending on the desired properties and performance of the pipe.
The filament winding process consists of four main steps: fiber impregnation, fiber winding, resin curing, and pipe removal. The fiber impregnation step involves passing the fibers through a resin bath or a resin applicator to coat them with resin. The fiber winding step involves feeding the impregnated fibers to a winding machine that controls the speed, tension, angle, and position of the fibers as they are wound around the mandrel. The resin curing step involves applying heat and pressure to the wound pipe to initiate and complete the chemical reaction that hardens the resin. The pipe removal step involves extracting the cured pipe from the mandrel by either pulling or cutting it off.
The filament winding process can produce composite pipes with various diameters, lengths, wall thicknesses, and fiber orientations. The diameter and length of the pipe are determined by the size and shape of the mandrel. The wall thickness of the pipe is determined by the number of layers or plies of fibers that are wound around the mandrel. The fiber orientation of the pipe is determined by the winding angle or helix angle of the fibers relative to the longitudinal axis of the mandrel.
The filament winding process has several advantages over other fabrication methods for composite pipes, such as:
- High strength-to-weight ratio: Filament winding can produce composite pipes with high strength-to-weight ratio by aligning most of the fibers in the hoop direction, which is the direction of the maximum stress due to the internal pressure.
- High pressure rating: Filament winding can produce composite pipes with high pressure rating by increasing the wall thickness or the number of plies of fibers that are wound around the mandrel.
- High production rate: Filament winding can produce composite pipes with high production rate by using automated or semi-automated winding machines that can wind multiple fibers simultaneously.
- Low material waste: Filament winding can produce composite pipes with low material waste by using pre-impregnated fibers that have precise resin content and minimal excess resin.
However, filament winding also has some disadvantages compared to other fabrication methods for composite pipes, such as:
- Limited geometry: Filament winding can only produce composite pipes with cylindrical or conical geometry, and cannot produce composite pipes with complex shapes or features, such as bends, branches, or flanges.
- Limited fiber orientation: Filament winding can only produce composite pipes with fiber orientation that varies from 0° (longitudinal) to 90° (hoop), and cannot produce composite pipes with fiber orientation that is off-axis or multidirectional, such as ±45° or quasi-isotropic.
- High equipment cost: Filament winding requires expensive equipment, such as mandrels, winding machines, resin baths, ovens, and autoclaves, to produce composite pipes.
Some examples of composite pipes produced by filament winding are:
- Thermoplastic composite pipe (TCP): TCP is a composite pipe that consists of a thermoplastic inner liner (such as polyethylene or polyamide) that is reinforced with continuous fibers (such as glass or carbon) embedded in a thermoplastic matrix (such as polypropylene or polyvinylidene fluoride). TCP is produced by filament winding pre-impregnated thermoplastic tapes around a removable metal mandrel at high temperature and pressure. TCP has high flexibility, chemical resistance, thermal stability, and pressure rating. It is suitable for dynamic applications such as risers, flowlines, jumpers, and umbilicals12.
- Glass reinforced plastic (GRP): GRP is a composite pipe that consists of a thermosetting resin (such as epoxy or polyester) that is reinforced with glass fibers. GRP is produced by filament winding pre-impregnated or wetted glass rovings around a permanent or collapsible mandrel at room temperature and pressure. GRP has high strength-to-weight ratio, corrosion resistance, and durability. It is suitable for static applications such as onshore pipelines, water injection lines, and cooling water lines.
- Fiber reinforced plastic (FRP): FRP is a composite pipe that consists of a thermosetting resin (such as epoxy or vinyl ester) that is reinforced with fibers other than glass (such as carbon or aramid). FRP is produced by filament winding pre-impregnated or wetted fibers around a permanent or collapsible mandrel at room temperature and pressure. FRP has higher strength, stiffness, and temperature resistance than GRP. It is suitable for high-pressure and high-temperature applications such as offshore pipelines, subsea pipelines, and downhole tubing
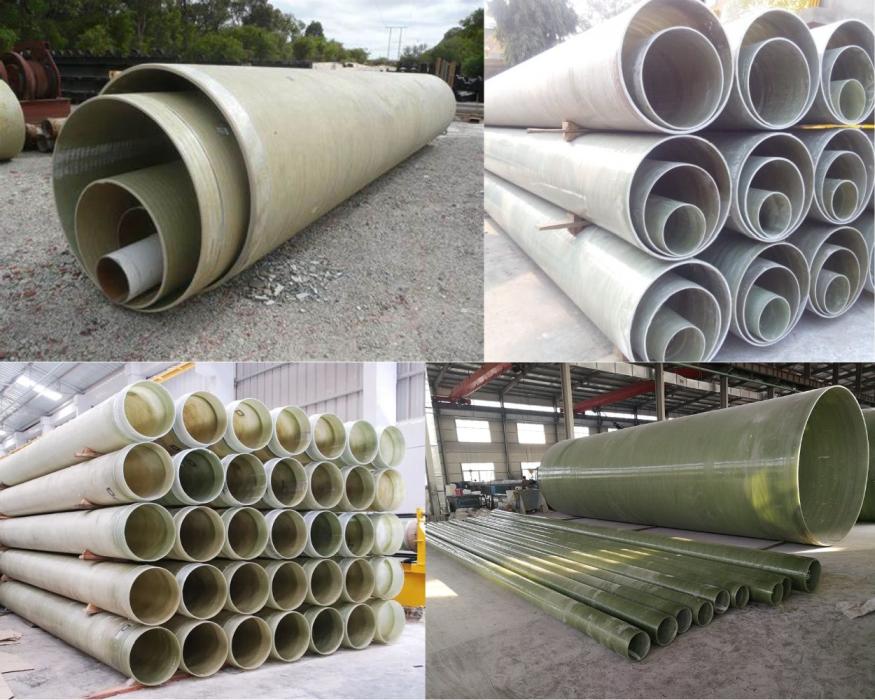
Fabrication Method | Description | Advantages | Disadvantages |
---|---|---|---|
Continuous filament winding | A process that involves winding continuous fibers impregnated with resin around a rotating mandrel in a predetermined pattern. The resin is then cured by heat or chemical reaction to form a hollow cylindrical pipe. | – High strength and stiffness in the hoop direction – High production rate and automation – Low material waste and cost | – Limited design flexibility and complexity – Limited fiber orientation and placement – High equipment and tooling cost |
Extrusion | A process that involves forcing a heated resin-fiber mixture through a die or nozzle to form a continuous solid or hollow pipe. The pipe is then cooled and cut to the desired length. | – High production rate and automation – High dimensional accuracy and consistency – Low material waste and cost | – Limited fiber content and orientation – Limited pipe diameter and thickness – High thermal and shear stresses |
Pultrusion | A process that involves pulling continuous fibers impregnated with resin through a heated die or mold to form a continuous solid or hollow pipe. The pipe is then cooled and cut to the desired length. | – High strength and stiffness in the longitudinal direction – High production rate and automation – High fiber content and orientation | – Limited design flexibility and complexity – Limited pipe diameter and thickness – High equipment and tooling cost |
Hand layup | A process that involves placing layers of dry fabrics or prepregs by hand onto a mold to form a laminate stack. Resin is applied to the dry fabrics after layup is complete or already present in the prepregs. The laminate is then cured by heat or chemical reaction to form a solid or hollow pipe. | – High design flexibility and complexity – High fiber orientation and placement – Low equipment and tooling cost | – Low production rate and automation – Low dimensional accuracy and consistency – High labor cost and skill requirement |
Installation Techniques for Composite Pipes
Composite pipes are not only fabricated to ensure that they have the desired properties and performance, but also installed to ensure that they function properly and safely in the pipeline system. The installation of composite pipes involves connecting the pipes to each other and to the rest of the pipeline components, such as valves, fittings, flanges, and supports. There are different installation techniques for composite pipes, depending on the type of composite material, the geometry and length of the pipe, and the environmental and operational conditions. In this section, we will discuss the main installation techniques for composite pipes, such as spooling, reeling, towing, J-laying, S-laying, and horizontal directional drilling. We will also compare the advantages and disadvantages of each technique in terms of speed, safety, reliability, and environmental impact. Finally, we will describe the challenges and solutions for installing composite pipes in harsh environments, such as deep water, arctic regions, and seismic zones.
Spooling
Spooling is one of the simplest and most common installation techniques for composite pipes. It is a process that involves winding the pipe around a large-diameter drum or spool on a vessel or a platform. The pipe can be either pre-fabricated onshore or fabricated onboard using continuous filament winding or extrusion. The spooling process can be either clockwise or counter-clockwise, depending on the direction of rotation of the drum or spool.
The spooling process consists of three main steps: pipe loading, pipe transportation, and pipe unloading. The pipe loading step involves attaching the pipe to the drum or spool and winding it around it until it reaches the desired length or capacity. The pipe transportation step involves moving the vessel or platform with the drum or spool to the installation site. The pipe unloading step involves unwinding the pipe from the drum or spool and laying it on the seabed or connecting it to the existing pipeline.
The spooling process can install composite pipes with various diameters, lengths, and wall thicknesses. The diameter and wall thickness of the pipe are determined by the design and fabrication methods. The length of the pipe is determined by the size and capacity of the drum or spool. The maximum length of a composite pipe that can be installed by spooling is typically around 10 km.
The spooling process has several advantages over other installation techniques for composite pipes, such as:
- Low installation cost: Spooling can install composite pipes with low installation cost by using simple equipment and procedures. It does not require any welding or special connectors to join the pipes.
- High installation speed: Spooling can install composite pipes with high installation speed by using continuous or long-length pipes that reduce the number of joints and connections. It can also install multiple pipes simultaneously by using multiple drums or spools.
- High installation quality: Spooling can install composite pipes with high installation quality by minimizing the bending and twisting stresses on the pipes during loading, transportation, and unloading. It can also protect the pipes from external damage by using protective coatings or covers.
However, spooling also has some disadvantages compared to other installation techniques for composite pipes, such as:
- Limited installation depth: Spooling can only install composite pipes at shallow or moderate water depths, up to 500 m, due to the hydrostatic pressure and buoyancy forces that affect the stability and integrity of the drum or spool.
- Limited installation flexibility: Spooling can only install composite pipes along straight or slightly curved routes, and cannot install composite pipes along complex or irregular routes, such as bends, branches, or slopes.
- High transportation risk: Spooling involves transporting large and heavy drums or spools with long lengths of pipes on vessels or platforms, which can pose a high risk of accidents or damage due to the weather conditions, sea currents, or human errors.
Some examples of composite pipes installed by spooling are:
- Thermoplastic composite pipe (TCP): TCP is a composite pipe that consists of a thermoplastic inner liner (such as polyethylene or polyamide) that is reinforced with continuous fibers (such as glass or carbon) embedded in a thermoplastic matrix (such as polypropylene or polyvinylidene fluoride). TCP can be installed by spooling either pre-fabricated onshore or fabricated onboard using continuous filament winding. TCP has high flexibility, chemical resistance, thermal stability, and pressure rating. It is suitable for dynamic applications such as risers, flowlines, jumpers, and umbilicals.
- Glass reinforced plastic (GRP): GRP is a composite pipe that consists of a thermosetting resin (such as epoxy or polyester) that is reinforced with glass fibers. GRP can be installed by spooling pre-fabricated onshore using continuous filament winding or pultrusion. GRP has high strength-to-weight ratio, corrosion resistance, and durability. It is suitable for static applications such as onshore pipelines, water injection lines, and cooling water lines.
- Fiber reinforced plastic (FRP): FRP is a composite pipe that consists of a thermosetting resin (such as epoxy or vinyl ester) that is reinforced with fibers other than glass (such as carbon or aramid). FRP can be installed by spooling pre-fabricated onshore using continuous filament winding or pultrusion. FRP has higher strength, stiffness, and temperature resistance than GRP. It is suitable for high-pressure and high-temperature applications such as offshore pipelines, subsea pipelines, and downhole tubing.
Reeling
Reeling is another common installation technique for composite pipes. It is a process that involves winding the pipe around a large-diameter reel on a vessel or a platform. The pipe can be either pre-fabricated onshore or fabricated onboard using continuous filament winding or extrusion. The reeling process can be either clockwise or counter-clockwise, depending on the direction of rotation of the reel.
The reeling process consists of three main steps: pipe loading, pipe transportation, and pipe unloading. The pipe loading step involves attaching the pipe to the reel and winding it around it until it reaches the desired length or capacity. The pipe transportation step involves moving the vessel or platform with the reel to the installation site. The pipe unloading step involves unwinding the pipe from the reel and laying it on the seabed or connecting it to the existing pipeline.
The reeling process can install composite pipes with various diameters, lengths, and wall thicknesses. The diameter and wall thickness of the pipe are determined by the design and fabrication methods. The length of the pipe is determined by the size and capacity of the reel. The maximum length of a composite pipe that can be installed by reeling is typically around 20 km.
The reeling process has several advantages over other installation techniques for composite pipes, such as:
- Low installation cost: Reeling can install composite pipes with low installation cost by using simple equipment and procedures. It does not require any welding or special connectors to join the pipes.
- High installation speed: Reeling can install composite pipes with high installation speed by using continuous or long-length pipes that reduce the number of joints and connections. It can also install multiple pipes simultaneously by using multiple reels.
- High installation quality: Reeling can install composite pipes with high installation quality by minimizing the bending and twisting stresses on the pipes during loading, transportation, and unloading. It can also protect the pipes from external damage by using protective coatings or covers.
However, reeling also has some disadvantages compared to other installation techniques for composite pipes, such as:
- Limited installation depth: Reeling can only install composite pipes at shallow or moderate water depths, up to 500 m, due to the hydrostatic pressure and buoyancy forces that affect the stability and integrity of the reel.
- Limited installation flexibility: Reeling can only install composite pipes along straight or slightly curved routes, and cannot install composite pipes along complex or irregular routes, such as bends, branches, or slopes.
- High transportation risk: Reeling involves transporting large and heavy reels with long lengths of pipes on vessels or platforms, which can pose a high risk of accidents or damage due to the weather conditions, sea currents, or human errors.
Some examples of composite pipes installed by reeling are:
- Thermoplastic composite pipe (TCP): TCP is a composite pipe that consists of a thermoplastic inner liner (such as polyethylene or polyamide) that is reinforced with continuous fibers (such as glass or carbon) embedded in a thermoplastic matrix (such as polypropylene or polyvinylidene fluoride). TCP can be installed by reeling either pre-fabricated onshore or fabricated onboard using continuous filament winding. TCP has high flexibility, chemical resistance, thermal stability, and pressure rating. It is suitable for dynamic applications such as risers, flowlines, jumpers, and umbilicals .
- Fiber reinforced plastic (FRP): FRP is a composite pipe that consists of a thermosetting resin (such as epoxy or vinyl ester) that is reinforced with fibers other than glass (such as carbon or aramid). FRP can be installed by reeling pre-fabricated onshore using continuous filament winding or pultrusion. FRP has higher strength, stiffness, and temperature resistance than GRP. It is suitable for high-pressure and high-temperature applications such as offshore pipelines, subsea pipelines, and downhole tubing.
The difference between spooling and reeling is that spooling involves winding the pipe around a large-diameter drum or spool, while reeling involves winding the pipe around a large-diameter reel. Both spooling and reeling are installation techniques for composite pipes that use simple equipment and procedures, and can install long lengths of pipes with high speed and quality. However, spooling and reeling have some limitations, such as limited installation depth, flexibility, and risk. Spooling and reeling are suitable for different types of composite pipes, such as TCP, GRP, or FRP, depending on the design and fabrication methods.
Installation Technique | Description | Advantages | Disadvantages |
---|---|---|---|
Spooling | Spooling involves winding the pipe around a large-diameter drum or spool, which can be transported to the installation site and unwound to lay the pipe. Spooling can be used for both onshore and offshore applications, such as water, oil, or gas pipelines. | – High installation speed and efficiency – Low installation cost and risk – High installation quality and accuracy | – Limited installation depth and length – Limited pipe diameter and thickness – High transportation and storage cost |
Reeling | Reeling involves winding the pipe around a large-diameter reel, which can be mounted on a vessel or a platform and rotated to lay the pipe. Reeling can be used for offshore applications, such as subsea or deepwater pipelines. | – High installation speed and efficiency – Low installation cost and risk – High installation quality and accuracy | – Limited installation depth and length – Limited pipe diameter and thickness – High bending and unbending stresses |
Towing | Towing involves towing the pipe from the fabrication site to the installation site by using a tugboat or a barge. The pipe can be towed in a single or multiple segments, depending on the length and diameter of the pipe. Towing can be used for both onshore and offshore applications, such as water, oil, or gas pipelines. | – High installation depth and length – High pipe diameter and thickness – Low bending and unbending stresses | – Low installation speed and efficiency – High installation cost and risk – Low installation quality and accuracy |
J-laying | J-laying involves laying the pipe from a vessel or a platform that has a J-shaped ramp or stinger at its stern. The pipe is fed from the vessel or platform to the ramp or stinger, where it bends into a J-shape before entering the water. J-laying can be used for offshore applications, such as subsea or deepwater pipelines. | – High installation depth and length – High pipe diameter and thickness – Low bending and unbending stresses | – Low installation speed and efficiency – High installation cost and risk – Low installation quality and accuracy |
S-laying | S-laying involves laying the pipe from a vessel or a platform that has an S-shaped ramp or stinger at its stern. The pipe is fed from the vessel or platform to the ramp or stinger, where it bends into an S-shape before entering the water. S-laying can be used for offshore applications, such as subsea or shallow water pipelines. | – High installation speed and efficiency – High installation quality and accuracy – Low bending and unbending stresses | – Limited installation depth and length – Limited pipe diameter and thickness – High installation cost and risk |
This table summarizes the main installation techniques for composite pipes.
Testing Procedures for Composite Pipes
Composite pipes are not only installed to ensure that they function properly and safely in the pipeline system, but also tested to ensure that they meet the specified requirements and standards. The testing of composite pipes involves applying various loads and conditions to the pipes and measuring their responses and behaviors. There are different testing procedures for composite pipes, depending on the type of composite material, the geometry and thickness of the pipe, and the service and performance criteria. In this section, we will discuss the main testing procedures for composite pipes, such as mechanical testing, thermal testing, chemical testing, and aging testing. We will also explain the objectives and criteria of each testing procedure in terms of performance evaluation, qualification assessment, failure analysis, and service life prediction. Finally, we will describe the testing equipment and standards for composite pipes, such as ASTM D2992, ASTM D2996, ASTM D2517, and ISO 14692.
Mechanical Testing
Mechanical testing is one of the most important and common testing procedures for composite pipes. It is a process that involves applying mechanical loads or stresses to the pipes and measuring their mechanical properties or responses, such as strength, stiffness, strain, deformation, fracture, or fatigue. Mechanical testing can be performed on both flat specimens and actual pipes to evaluate the material behavior and structural performance of composite pipes.
Some of the mechanical tests that are performed on composite pipes are:
- Compression test: Composite compression testing methods provide a means of introducing a compressive load into the material while preventing it from buckling. Compression tests can measure the compressive strength and modulus of elasticity of composite materials in different directions, such as longitudinal, transverse, or off-axis. Compression tests can also measure the buckling resistance and stability of composite pipes under axial or lateral loads.
- Interlaminar shear strength test: The interlaminar shear strength (ILSS) is another important mechanical test that provides information about the quality of the resin-fiber bond. ILSS tests can measure the shear strength and modulus of elasticity of composite materials in the thickness direction, which is perpendicular to the fiber layers or plies. ILSS tests can also measure the delamination resistance and toughness of composite pipes under interlaminar shear stresses.
- Shear test: Shear tests can measure the shear strength and modulus of elasticity of composite materials in different directions, such as longitudinal-transverse or longitudinal-thickness. Shear tests can also measure the shear resistance and stiffness of composite pipes under shear loads or torsion.
- Hardness: Hardness tests can measure the resistance of composite materials to indentation or penetration by a hard object or tool. Hardness tests can provide an indication of the wear resistance and abrasion resistance of composite materials and pipes.
- Tensile test: Tensile tests can measure the tensile strength and modulus of elasticity of composite materials in different directions, such as longitudinal, transverse, or off-axis. Tensile tests can also measure the strain rate sensitivity and ductility of composite materials and pipes.
- Flexural test: Flexural tests can measure the flexural strength and modulus of elasticity of composite materials in different directions, such as longitudinal or transverse. Flexural tests can also measure the bending resistance and deflection of composite pipes under flexural loads or moments.
- Impact test: Impact tests can measure the impact strength and energy absorption of composite materials under dynamic loads or shocks. Impact tests can also measure the impact resistance and damage tolerance of composite pipes under impact loads or impacts.
- Fatigue test: Fatigue tests can measure the fatigue strength and fatigue life of composite materials under cyclic loads or stresses. Fatigue tests can also measure the fatigue resistance and durability of composite pipes under fatigue loads or fatigue cycles.
The objectives and criteria of mechanical testing for composite pipes are:
- Performance evaluation: Mechanical testing can evaluate the performance of composite pipes under various loading scenarios and conditions that simulate the actual service environment, such as pressure, temperature, fluid properties, and environmental factors. Mechanical testing can also compare the performance of different types of composite pipes, such as TCP, GRP, or FRP, or the performance of composite pipes with steel pipes.
- Qualification assessment: Mechanical testing can assess the qualification of composite pipes for the specified requirements and standards that govern the design, fabrication, installation, testing, and maintenance of the pipeline system. Mechanical testing can also verify the compliance of composite pipes with the relevant codes, regulations, and specifications that apply to the oil and gas industry.
- Failure analysis: Mechanical testing can analyze the failure modes and mechanisms of composite pipes under the extreme or unexpected loads or conditions that cause the pipe rupture, leakage, or malfunction. Mechanical testing can also identify the root causes and contributing factors of the pipe failure, such as material defects, manufacturing errors, installation errors, operational errors, or environmental effects.
- Service life prediction: Mechanical testing can predict the service life of composite pipes under the normal or expected loads or conditions that affect the pipe performance, reliability, safety, and sustainability over time. Mechanical testing can also estimate the remaining life and residual strength of the pipe after a certain period of service or a certain level of damage.
The testing equipment and standards for mechanical testing of composite pipes are:
- ASTM D2992: Standard Practice for Obtaining Hydrostatic or Pressure Design Basis for Fiberglass (Glass-Fiber-Reinforced Thermosetting-Resin) Pipe and Fittings
- ASTM D2996: Standard Specification for Filament-Wound Fiberglass (Glass-Fiber-Reinforced Thermosetting-Resin) Pipe
- ASTM D2517: Standard Specification for Reinforced Epoxy Resin Gas Pressure Pipe and Fittings
- ISO 14692: Petroleum and natural gas industries — Glass-reinforced plastics (GRP) piping
Test | Standard | Equipment | Purpose |
---|---|---|---|
Compression test | ISO 14126, ASTM D3410, ASTM D6641, ASTM D695 | Compression testing machine, compression fixture, strain gauge or extensometer | To measure the compressive strength and modulus of elasticity of composite materials and pipes in different directions |
Interlaminar shear strength test | ASTM D2344, ISO 14130 | Interlaminar shear testing machine, interlaminar shear fixture, strain gauge or extensometer | To measure the interlaminar shear strength and modulus of elasticity of composite materials and pipes in the thickness direction |
Shear test | ASTM D3518, ISO 14129 | Shear testing machine, shear fixture, strain gauge or extensometer | To measure the shear strength and modulus of elasticity of composite materials and pipes in different directions |
Hardness test | ASTM D2583, ISO 2039-1 | Hardness testing machine, hardness indenter, hardness scale or meter | To measure the hardness and wear resistance of composite materials and pipes |
Tensile test | ISO 527-4, ISO 527-5, ASTM D3039 | Tensile testing machine, tensile fixture, strain gauge or extensometer | To measure the tensile strength and modulus of elasticity of composite materials and pipes in different directions |
Flexural test | ISO 14125, ASTM D7264 | Flexural testing machine, flexural fixture, strain gauge or extensometer | To measure the flexural strength and modulus of elasticity of composite materials and pipes in different directions |
Impact test | ISO 179-1, ISO 179-2, ASTM D256, ASTM D6110 | Impact testing machine, impact pendulum or hammer, impact notch or specimen holder | To measure the impact strength and energy absorption of composite materials and pipes under dynamic loads |
Fatigue test | ISO 13003, ASTM D3479, ASTM E466 | Fatigue testing machine, fatigue fixture, strain gauge or extensometer, load cell or force transducer | To measure the fatigue strength and fatigue life of composite materials and pipes under cyclic loads |
This table summarizes the main testing procedures for mechanical testing of composite pipes. It shows the standards that provide the test methods and procedures, the equipment that perform the tests and measurements, and the purpose of each test in terms of evaluating the mechanical properties and performance of composite pipes.
Maintenance Practices for Composite Pipes
Composite pipes are not only tested to ensure that they meet the specified requirements and standards, but also maintained to ensure that they function properly and safely in the pipeline system. The maintenance of composite pipes involves monitoring, inspecting, repairing, and replacing the pipes and their components as needed. There are different maintenance practices for composite pipes, depending on the type of composite material, the geometry and length of the pipe, and the environmental and operational conditions. In this section, we will discuss the main maintenance practices for composite pipes, such as pigging, cathodic protection, coating, and patching. We will also explain the objectives and benefits of each maintenance practice in terms of performance improvement, reliability enhancement, safety assurance, and cost reduction. Finally, we will describe the challenges and solutions for maintaining composite pipes in harsh environments, such as corrosion, erosion, abrasion, and impact damage.
Pigging
Pigging is one of the most common and effective maintenance practices for composite pipes. It is a process that involves inserting a device called a pig into the pipe and pushing it through the pipe by the fluid flow or by an external force. The pig can perform various functions, such as cleaning, inspecting, measuring, or sealing the pipe. Pigging can be performed on both new and existing pipes to maintain their cleanliness and integrity.
Some of the pigging methods that are performed on composite pipes are:
- Cleaning pigging: Cleaning pigging involves using a pig that has brushes, scrapers, magnets, or jets to remove any deposits, debris, or foreign objects from the pipe wall or bore. Cleaning pigging can improve the flow efficiency, reduce the pressure drop, prevent blockages, and extend the service life of the pipe.
- Inspection pigging: Inspection pigging involves using a pig that has sensors, cameras, or transmitters to detect any defects, anomalies, or changes in the pipe wall or bore. Inspection pigging can provide information about the condition, performance, and integrity of the pipe.
- Measurement pigging: Measurement pigging involves using a pig that has gauges, meters, or indicators to measure any parameters, such as diameter, thickness, temperature, pressure, or flow rate of the pipe wall or bore. Measurement pigging can provide data about the dimensions, properties, and characteristics of the pipe.
- Sealing pigging: Sealing pigging involves using a pig that has seals, plugs, or valves to isolate or seal a section of the pipe wall or bore. Sealing pigging can enable repairs, modifications, or testing of the pipe without interrupting the fluid flow.
The objectives and benefits of pigging for composite pipes are:
- Performance improvement: Pigging can improve the performance of composite pipes by removing any obstructions or contaminants that may affect the fluid flow, the heat transfer, or the chemical reaction. Pigging can also optimize the fluid velocity, the pressure distribution, or the temperature profile.
- Reliability enhancement: Pigging can enhance the reliability of composite pipes by detecting any defects or anomalies that may compromise the strength, the stiffness, or the durability. Pigging can also monitor the stress, the strain, or the fatigue.
- Safety assurance: Pigging can assure the safety of composite pipes by preventing any failures or leaks that may cause the fluid loss, the environmental damage, or the human injury. Pigging can also verify the compliance, the quality, or the functionality.
- Cost reduction: Pigging can reduce the cost of composite pipes by avoiding any repairs or replacements that may incur the material waste, the labor expense, or the downtime loss. Pigging can also increase the productivity, the efficiency, or the profitability.
The testing equipment and standards for pigging of composite pipes are:
- ASTM F3087: Standard Specification for Acrylonitrile-Butadiene-Styrene (ABS) Composite Sewer Piping Systems Based on Controlled Outside Diameter
- ASTM F3123: Standard Specification for Metric Outside Diameter Polyethylene (PE) Plastic Pipe (DR-PN)
- ISO 14692: Petroleum and natural gas industries — Glass-reinforced plastics (GRP) piping
Cost-Benefit Analysis of Composite Pipes
Composite pipes are not only maintained to ensure that they function properly and safely in the pipeline system, but also evaluated to ensure that they are economically viable and beneficial. The evaluation of composite pipes involves comparing the costs and benefits of using composite pipes versus alternative materials or solutions for a given project or application. There are different evaluation methods for composite pipes, depending on the scope, objective, and criteria of the analysis. In this section, we will discuss the main evaluation method for composite pipes, which is cost-benefit analysis (CBA). We will also explain the steps and components of CBA, such as identifying and quantifying the costs and benefits, discounting and aggregating the costs and benefits, and calculating and interpreting the net present value (NPV) and benefit-cost ratio (BCR). Finally, we will provide some examples and case studies of CBA for composite pipes in different industries and sectors.
What is cost-benefit analysis?
Cost-benefit analysis (CBA) is an analytical technique that assesses the economic, environmental, and social impacts of a project or policy on society as a whole. CBA compares the total costs and benefits of a project or policy over its lifetime, expressed in present value terms. CBA aims to answer the question: Is the project or policy worth doing from a social perspective?
The main steps of CBA are:
- Define the scope and objective of the analysis: This step involves defining the purpose, scope, objective, and criteria of the analysis. It also involves identifying the project or policy options to be compared, such as using composite pipes versus steel pipes or doing nothing.
- Identify and quantify the costs and benefits of each option: This step involves identifying and quantifying all the relevant costs and benefits of each option for all the affected parties over the project or policy lifetime. The costs include all the resources used or sacrificed to implement the option, such as capital costs, operating costs, maintenance costs, environmental costs, social costs, etc. The benefits include all the positive effects or outcomes of the option, such as revenue, savings, efficiency, quality, safety, environmental benefits, social benefits, etc.
- Discount and aggregate the costs and benefits of each option: This step involves discounting and aggregating all the future costs and benefits of each option to their present values using a discount rate. The discount rate reflects the time value of money and the opportunity cost of capital. The present value of costs (PVC) is the sum of all the discounted costs of an option. The present value of benefits (PVB) is the sum of all the discounted benefits of an option.
- Calculate and interpret the net present value (NPV) and benefit-cost ratio (BCR) of each option: This step involves calculating and interpreting two key indicators of economic efficiency for each option: NPV and BCR. NPV is the difference between PVB and PVC. NPV measures the net benefit or surplus of an option to society. A positive NPV indicates that an option is economically efficient and socially desirable. A negative NPV indicates that an option is economically inefficient and socially undesirable. BCR is the ratio between PVB and PVC. BCR measures the return or payoff of an option to society. A BCR greater than one indicates that an option is economically efficient and socially desirable. A BCR less than one indicates that an option is economically inefficient and socially undesirable.
- Compare and rank the options based on NPV and BCR: This step involves comparing and ranking all the options based on their NPV and BCR values. The option with the highest NPV or BCR is usually preferred over other options. However, other factors such as risk, uncertainty, distributional effects, non-monetary impacts, etc., may also be considered in making a final decision.
The main components of CBA are:
- Costs: Costs are all the negative impacts or outcomes of a project or policy on society. Costs can be classified into different types, such as:
- Capital costs are the initial costs of acquiring, constructing, or installing the project or policy assets, such as composite pipes, equipment, facilities, etc. Capital costs can be estimated by using the unit cost method, the cost-capacity method, the learning curve method, or the cost index method.
- Operating costs: Operating costs are the recurring costs of operating and maintaining the project or policy assets, such as composite pipes, equipment, facilities, etc. Operating costs can be estimated by using the operating ratio method, the maintenance factor method, the life cycle cost method, or the cost function method.
- Environmental costs: Environmental costs are the costs of environmental impacts or externalities caused by the project or policy activities, such as emissions, pollution, waste, noise, etc. Environmental costs can be estimated by using the market price method, the damage cost method, the abatement cost method, or the contingent valuation method.
- Social costs: Social costs are the costs of social impacts or externalities caused by the project or policy activities, such as accidents, injuries, illnesses, deaths, etc. Social costs can be estimated by using the human capital method, the willingness to pay method, the willingness to accept method, or the quality-adjusted life year method.
- Benefits: Benefits are all the positive impacts or outcomes of a project or policy on society. Benefits can be classified into different types, such as:
- Revenue: Revenue is the income generated by the project or policy activities, such as sales, fees, tariffs, subsidies, etc. Revenue can be estimated by using the demand analysis method, the price analysis method, the elasticity analysis method, or the market share analysis method.
- Savings: Savings are the cost reductions or avoidances achieved by the project or policy activities, such as energy savings, water savings, material savings, etc. Savings can be estimated by using the engineering analysis method, the economic analysis method, the statistical analysis method, or the simulation analysis method.
- Efficiency: Efficiency is the improvement in productivity or performance achieved by the project or policy activities, such as output per input, quality per output, or service per quality. Efficiency can be estimated by using the ratio analysis method, the benchmarking analysis method, the index number analysis method, or the data envelopment analysis method.
Quality is the improvement in customer satisfaction or value achieved by the project or policy activities, such as reliability, safety, durability, aesthetics, etc. Quality can be estimated by using the customer survey method, the customer feedback method, the customer loyalty method, or the customer satisfaction index method.
- Safety: Safety is the reduction in risk or uncertainty achieved by the project or policy activities, such as accidents, injuries, illnesses, deaths, etc. Safety can be estimated by using the risk analysis method, the uncertainty analysis method, the probability analysis method, or the reliability analysis method.
- Environmental benefits: Environmental benefits are the benefits of environmental impacts or externalities caused by the project or policy activities, such as emissions reduction, pollution prevention, waste management, noise reduction, etc. Environmental benefits can be estimated by using the market price method, the damage cost method, the abatement cost method, or the contingent valuation method.
- Social benefits: Social benefits are the benefits of social impacts or externalities caused by the project or policy activities, such as health improvement, education enhancement, income generation, poverty alleviation, etc. Social benefits can be estimated by using the human capital method, the willingness to pay method, the willingness to accept method, or the quality-adjusted life year method.
The objectives and benefits of CBA for composite pipes are:
- Economic efficiency: CBA can evaluate the economic efficiency of composite pipes by comparing their costs and benefits over their lifetime. CBA can also compare the economic efficiency of different types of composite pipes, such as TCP, GRP, or FRP, or the economic efficiency of composite pipes with steel pipes or other alternatives. CBA can help to select the most economically efficient and socially desirable option for a given project or application.
- Environmental sustainability: CBA can evaluate the environmental sustainability of composite pipes by assessing their environmental impacts and benefits over their lifetime. CBA can also compare the environmental sustainability of different types of composite pipes, such as TCP, GRP, or FRP, or the environmental sustainability of composite pipes with steel pipes or other alternatives. CBA can help to select the most environmentally friendly and socially responsible option for a given project or application.
- Social welfare: CBA can evaluate the social welfare of composite pipes by measuring their social impacts and benefits over their lifetime. CBA can also compare the social welfare of different types of composite pipes, such as TCP, GRP, or FRP, or the social welfare of composite pipes with steel pipes or other alternatives. CBA can help to select the most socially beneficial and equitable option for a given project or application.
The testing equipment and standards for CBA of composite pipes are:
- NPV calculator: A NPV calculator is a tool that calculates the NPV of a project or policy option by discounting and aggregating the costs and benefits over the project or policy lifetime using a discount rate. A NPV calculator can be found online or in spreadsheet software.
- BCR calculator: A BCR calculator is a tool that calculates the BCR of a project or policy option by dividing the PVB by the PVC. A BCR calculator can be found online or in spreadsheet software.
- ISO 15686-5: Buildings and constructed assets — Service life planning — Part 5: Life cycle costing
- ASTM E917: Standard Practice for Measuring Life-Cycle Costs of Buildings and Building Systems
Cost-Benefit Analysis Component | Description | Example |
---|---|---|
Costs | Costs are all the negative impacts or outcomes of a project or policy on society. Costs can be classified into different types, such as capital costs, operating costs, environmental costs, social costs, etc. | Capital costs are the initial costs of acquiring, constructing, or installing the project or policy assets, such as composite pipes, equipment, facilities, etc. For example, the capital cost of a composite pipe project may include the cost of purchasing the pipe material, fabricating the pipe segments, transporting the pipe segments to the installation site, etc. |
Benefits | Benefits are all the positive impacts or outcomes of a project or policy on society. Benefits can be classified into different types, such as revenue, savings, efficiency, quality, safety, environmental benefits, social benefits, etc. | Revenue is the income generated by the project or policy activities, such as sales, fees, tariffs, subsidies, etc. For example, the revenue of a composite pipe project may include the income from selling the fluid transported by the pipe, charging a fee for using the pipe service, receiving a subsidy for using a low-carbon technology, etc. |
Discount rate | Discount rate is the rate used to convert future costs and benefits to their present values. Discount rate reflects the time value of money and the opportunity cost of capital. | The discount rate can be determined by using various methods, such as social rate of time preference (SRTP), social opportunity cost of capital (SOCC), weighted average cost of capital (WACC), etc. For example, Australia recommends using a real discount rate of 7% for CBA of infrastructure projects.. |
Present value of costs (PVC) | Present value of costs (PVC) is the sum of all the discounted costs of a project or policy option over its lifetime. PVC measures the total cost or sacrifice of a project or policy option to society. | PVC can be calculated by using the following formula: PVC = C0 + C1/(1+r) + C2/(1+r)^2 + … + CT/(1+r)^T where C0 is the cost in year 0 (the base year), C1 is the cost in year 1, C2 is the cost in year 2,… CT is the cost in year T (the final year), r is the discount rate, and T is the project or policy lifetime. For example, if a composite pipe project has a capital cost of $100 million in year 0 and an operating cost of $10 million per year for 20 years, and the discount rate is 7%, then PVC = 100 + 10/(1+0.07) + 10/(1+0.07)^2 + … + 10/(1+0.07)^20 = $176.6 million |
Coating.
Coating is another useful maintenance practice for composite pipes. It is a process that involves applying a protective layer or coating to the pipe surface to prevent or reduce the corrosion, erosion, abrasion, or impact damage of the pipe by the surrounding environment. Coating can be performed on both new and existing pipes to enhance their durability and performance.
Some of the coating methods that are performed on composite pipes are:
- Powder coating: Powder coating involves applying a dry powder of resin and pigment to the pipe surface using electrostatic spray or fluidized bed techniques. The powder is then cured by heating or ultraviolet radiation to form a hard and smooth coating. Powder coating can provide a uniform and thick coating with high adhesion, corrosion resistance, and abrasion resistance.
- Liquid coating: Liquid coating involves applying a liquid solution of resin and pigment to the pipe surface using spray, dip, or brush techniques. The liquid is then cured by drying or chemical reaction to form a thin and flexible coating. Liquid coating can provide a customized and versatile coating with high flexibility, chemical resistance, and impact resistance.
- Film coating: Film coating involves applying a pre-formed film of resin and pigment to the pipe surface using heat or pressure techniques. The film is then bonded to the pipe surface by melting or adhesive to form a seamless and smooth coating. Film coating can provide a durable and aesthetic coating with high gloss, color, and UV resistance.
The objectives and benefits of coating for composite pipes are:
- Corrosion prevention: Coating can prevent or reduce the corrosion of composite pipes by creating a barrier between the pipe surface and the corrosive environment, such as water, salt, acid, etc. Coating can also inhibit the electrochemical reactions that cause corrosion by providing electrical insulation or cathodic protection.
- Erosion prevention: Coating can prevent or reduce the erosion of composite pipes by reducing the friction between the pipe surface and the erosive environment, such as sand, gravel, slurry, etc. Coating can also protect the pipe surface from wear and tear by providing hardness or toughness.
- Abrasion prevention: Coating can prevent or reduce the abrasion of composite pipes by increasing the smoothness of the pipe surface and decreasing the roughness of the abrasive environment, such as rocks, debris, tools, etc. Coating can also resist the scratching and scuffing of the pipe surface by providing lubricity or elasticity.
- Impact prevention: Coating can prevent or reduce the impact damage of composite pipes by absorbing or dissipating the energy of the impact environment, such as hammers, vehicles, vessels, etc. Coating can also prevent or reduce the cracking or breaking of the pipe surface by providing strength or ductility.
The testing equipment and standards for coating of composite pipes are:
- ASTM D4541: Standard Test Method for Pull-Off Strength of Coatings Using Portable Adhesion Testers
- ASTM D3359: Standard Test Methods for Measuring Adhesion by Tape Test
- ASTM D4060: Standard Test Method for Abrasion Resistance of Organic Coatings by the Taber Abraser
- ASTM D2794: Standard Test Method for Resistance of Organic Coatings to the Effects of Rapid Deformation (Impact)
Future Trends and Opportunities for Composite Pipes
Composite pipes are not only evaluated to ensure that they are economically viable and beneficial, but also innovated to ensure that they are technologically advanced and competitive. The innovation of composite pipes involves developing new materials, designs, processes, and applications for composite pipes to meet the changing needs and challenges of the market. There are different future trends and opportunities for composite pipes, depending on the drivers, barriers, and enablers of the innovation. In this section, we will discuss the main future trends and opportunities for composite pipes, such as smart composites, bio-composites, nano-composites, and hybrid composites. We will also explain the advantages and disadvantages of each future trend and opportunity in terms of performance improvement, cost reduction, environmental sustainability, and social welfare. Finally, we will provide some examples and case studies of innovative projects and products for composite pipes in different industries and sectors.
Smart Composites
Smart composites are composite materials that can sense, respond, or adapt to external stimuli or changes in their environment. Smart composites can be classified into different types, such as self-healing composites, self-cleaning composites, self-monitoring composites, and self-regulating composites.
Some of the advantages of smart composites for composite pipes are:
- Performance improvement: Smart composites can improve the performance of composite pipes by enhancing their functionality and reliability. For example, self-healing composites can repair any cracks or damages in the pipe wall or bore by releasing healing agents or activating healing mechanisms. Self-cleaning composites can remove any deposits or contaminants from the pipe surface or bore by using photocatalytic or hydrophobic coatings. Self-monitoring composites can detect any defects or anomalies in the pipe wall or bore by using embedded sensors or indicators. Self-regulating composites can adjust any parameters or properties of the pipe wall or bore by using shape memory or piezoelectric materials.
- Cost reduction: Smart composites can reduce the cost of composite pipes by reducing their maintenance and operation costs. For example, self-healing composites can reduce the repair costs by avoiding any leaks or failures in the pipe. Self-cleaning composites can reduce the cleaning costs by maintaining the flow efficiency and heat transfer of the pipe. Self-monitoring composites can reduce the inspection costs by providing real-time data and alerts on the condition and integrity of the pipe. Self-regulating composites can reduce the energy costs by optimizing the fluid velocity and pressure distribution of the pipe.
Some of the disadvantages of smart composites for composite pipes are:
- High initial cost: Smart composites have a high initial cost compared to conventional composites due to their complex material composition and fabrication process. Smart composites require additional components or materials such as healing agents, sensors, actuators, etc., that increase their material cost. Smart composites also require advanced techniques such as nanotechnology, biotechnology, etc., that increase their manufacturing cost.
- Technical challenges: Smart composites face technical challenges in terms of their compatibility, durability, and functionality. Smart composites need to be compatible with the base composite material and the surrounding environment to avoid any adverse effects or interactions. Smart composites need to be durable enough to withstand the mechanical, thermal, chemical, or electrical stresses that may affect their performance or reliability. Smart composites need to be functional enough to perform their intended tasks or functions without any errors or failures.
Some examples of smart composites for composite pipes are:
Some examples of smart composites for composite pipes are:
- Self-healing thermoplastic composite pipe (TCP): TCP is a composite pipe that consists of a thermoplastic inner liner (such as polyethylene or polyamide) that is reinforced with continuous fibers (such as glass or carbon) embedded in a thermoplastic matrix (such as polypropylene or polyvinylidene fluoride). TCP can be self-healing by using microcapsules that contain healing agents (such as epoxy resin) that are dispersed in the thermoplastic matrix. When a crack occurs in the pipe wall or bore, the microcapsules rupture and release the healing agents that fill and bond the crack.
- Self-cleaning glass reinforced plastic (GRP): GRP is a composite pipe that consists of a thermosetting resin (such as epoxy or polyester) that is reinforced with glass fibers. GRP can be self-cleaning by using photocatalytic coatings (such as titanium dioxide) that are applied on the pipe surface. When exposed to sunlight, the photocatalytic coatings generate reactive oxygen species that oxidize the organic deposits or contaminants on the pipe surface.
- Self-monitoring fiber reinforced plastic (FRP): FRP is a composite pipe that consists of a thermosetting resin (such as epoxy or vinyl ester) that is reinforced with fibers other than glass (such as carbon or aramid). FRP can be self-monitoring by using embedded sensors (such as fiber optic sensors) that are integrated with the fiber reinforcement. The sensors can measure various parameters, such as strain, temperature, pressure, or flow rate, and transmit the data to a remote control center for real-time monitoring and analysis.
- Self-regulating thermoplastic composite pipe (TCP): TCP is a composite pipe that consists of a thermoplastic inner liner (such as polyethylene or polyamide) that is reinforced with continuous fibers (such as glass or carbon) embedded in a thermoplastic matrix (such as polypropylene or polyvinylidene fluoride). TCP can be self-regulating by using shape memory materials (such as shape memory polymers or shape memory alloys) that are incorporated in the thermoplastic matrix. The shape memory materials can change their shape or stiffness in response to external stimuli, such as temperature, electric current, or magnetic field, and thus adjust the diameter, curvature, or orientation of the pipe.
Conclusion
Composite pipes are a type of pipes that are made of composite materials, which are materials that consist of two or more different materials that are combined to create a new material with enhanced properties and performance. Composite pipes have many advantages over conventional pipes, such as steel pipes, such as:
- Higher strength-to-weight ratio: Composite pipes have higher strength-to-weight ratio than steel pipes, which means they can withstand higher loads or pressures with lower weight or thickness. This reduces the material and transportation costs, and increases the installation speed and flexibility.
- Higher corrosion resistance: Composite pipes have higher corrosion resistance than steel pipes, which means they can resist the chemical or electrochemical attacks from the fluid or the environment. This reduces the maintenance and operation costs, and increases the service life and reliability.
- Higher thermal stability: Composite pipes have higher thermal stability than steel pipes, which means they can maintain their shape and properties under high or low temperatures. This reduces the thermal expansion or contraction stresses, and increases the heat transfer and efficiency.
- Higher design flexibility: Composite pipes have higher design flexibility than steel pipes, which means they can be customized and optimized for different applications and conditions. This increases the functionality and performance of the pipe system.
Composite pipes are widely used in various industries and sectors, such as oil and gas, water, mining, power, etc. Composite pipes can be fabricated using different methods, such as continuous filament winding, extrusion, pultrusion, etc. Composite pipes can be installed using different techniques, such as spooling, reeling, towing, J-laying, S-laying, etc. Composite pipes can be tested using different procedures, such as mechanical testing, thermal testing, chemical testing, aging testing, etc. Composite pipes can be maintained using different practices, such as pigging, cathodic protection, coating, patching, etc.
Composite pipes are also constantly innovated to meet the changing needs and challenges of the market. Some of the future trends and opportunities for composite pipes are smart composites, bio-composites, nano-composites, and hybrid composites. These composite materials can sense, respond, or adapt to external stimuli or changes in their environment. These composite materials can also use natural or renewable resources or nanoscale structures to enhance their properties and performance.
Composite pipes are evaluated using cost-benefit analysis (CBA), which is an analytical technique that assesses the economic, environmental, and social impacts of a project or policy on society as a whole. CBA compares the total costs and benefits of a project or policy over its lifetime, expressed in present value terms. CBA aims to answer the question: Is the project or policy worth doing from a social perspective?
Composite pipes are a promising technology that can revolutionize the pipeline industry with their superior properties and performance. Composite pipes can provide significant benefits to society in terms of economic efficiency, environmental sustainability, and social welfare. Composite pipes can also overcome the limitations and challenges of conventional pipes in terms of material availability, installation feasibility, testing reliability, and maintenance durability.
Innovellix is a leading company that specializes in composite materials and composite pipes. Innovellix offers a wide range of products and services for composite materials and composite pipes, such as:
- Design and engineering: Innovellix provides design and engineering solutions for composite materials and composite pipes, such as material selection, structural analysis, fluid dynamics, thermal analysis, etc.
- Fabrication and installation: Innovellix provides fabrication and installation services for composite materials and composite pipes, such as continuous filament winding, extrusion, pultrusion, spooling, reeling, towing, J-laying, S-laying, etc.
- Testing and inspection: Innovellix provides testing and inspection services for composite materials and composite pipes, such as mechanical testing, thermal testing, chemical testing, aging testing, pigging, cathodic protection, coating, patching, etc.
- Maintenance and repair: Innovellix provides maintenance and repair services for composite materials and composite pipes, such as self-healing composites, self-cleaning composites, self-monitoring composites, self-regulating composites, etc.
Innovellix is committed to delivering high-quality products and services for composite materials and composite pipes that meet the needs and expectations of its customers. Innovellix is also dedicated to advancing the research and development of composite materials and composite pipes that meet the challenges and opportunities of the market. Innovellix is your trusted partner for composite materials and composite pipes.
If you want to learn more about composite materials and composite pipes, please visit our website at innovellix.com/what-we-do/. You can also contact us at innovellix.com/contact-us/ for any inquiries or feedbacks. Thank you for reading this article. We hope you enjoyed it.
You can also read about new type of composite pipe for oil and gas – Nexa Pipe.
FAQ Section for Composite Pipes
What are the benefits of composite pipes over steel pipes?
Composite pipes have many benefits over steel pipes, such as:
- Higher strength-to-weight ratio: Composite pipes can withstand higher loads or pressures with lower weight or thickness. This reduces the material and transportation costs, and increases the installation speed and flexibility.
- Higher corrosion resistance: Composite pipes can resist the chemical or electrochemical attacks from the fluid or the environment. This reduces the maintenance and operation costs, and increases the service life and reliability.
- Higher thermal stability: Composite pipes can maintain their shape and properties under high or low temperatures. This reduces the thermal expansion or contraction stresses, and increases the heat transfer and efficiency.
- Higher design flexibility: Composite pipes can be customized and optimized for different applications and conditions. This increases the functionality and performance of the pipe system.
How are composite pipes fabricated?
Composite pipes are fabricated using different methods, such as:
- Continuous filament winding: This method involves winding continuous fibers impregnated with resin around a rotating mandrel in a predetermined pattern. The resin is then cured by heat or chemical reaction to form a hollow cylindrical pipe.
- Extrusion: This method involves forcing a heated resin-fiber mixture through a die or nozzle to form a continuous solid or hollow pipe. The pipe is then cooled and cut to the desired length.
- Pultrusion: This method involves pulling continuous fibers impregnated with resin through a heated die or mold to form a continuous solid or hollow pipe. The pipe is then cooled and cut to the desired length.
- Hand layup: This method involves placing layers of dry fabrics or prepregs by hand onto a mold to form a laminate stack. Resin is applied to the dry fabrics after layup is complete or already present in the prepregs. The laminate is then cured by heat or chemical reaction to form a solid or hollow pipe.
How are composite pipes installed?
Composite pipes are installed using different techniques, such as:
- Spooling: This technique involves winding the pipe around a large-diameter drum or spool, which can be transported to the installation site and unwound to lay the pipe.
- Reeling: This technique involves winding the pipe around a large-diameter reel, which can be mounted on a vessel or a platform and rotated to lay the pipe.
- Towing: This technique involves towing the pipe from the fabrication site to the installation site by using a tugboat or a barge. The pipe can be towed in a single or multiple segments, depending on the length and diameter of the pipe.
- J-laying: This technique involves laying the pipe from a vessel or a platform that has a J-shaped ramp or stinger at its stern. The pipe is fed from the vessel or platform to the ramp or stinger, where it bends into a J-shape before entering the water.
- S-laying: This technique involves laying the pipe from a vessel or a platform that has an S-shaped ramp or stinger at its stern. The pipe is fed from the vessel or platform to the ramp or stinger, where it bends into an S-shape before entering the water.
How are composite pipes tested?
Composite pipes are tested using different procedures, such as:
- Mechanical testing: Mechanical testing involves applying various loads or stresses to the pipe to measure its strength, stiffness, durability, etc. Some of the mechanical tests for composite pipes are compression test, interlaminar shear strength test, shear test, hardness test, tensile test, flexural test, impact test, fatigue test, etc.
- Thermal testing: Thermal testing involves exposing the pipe to various temperatures or heat sources to measure its thermal properties, such as thermal conductivity, thermal expansion, thermal resistance, etc. Some of the thermal tests for composite pipes are thermal cycling test, thermal shock test, fire resistance test, etc.
- Chemical testing: Chemical testing involves exposing the pipe to various fluids or chemicals to measure its chemical properties, such as corrosion resistance, chemical resistance, permeability, etc. Some of the chemical tests for composite pipes are immersion test, exposure test, leakage test, etc.
- Aging testing: Aging testing involves exposing the pipe to various environmental factors or aging agents to measure its aging properties, such as weathering resistance, UV resistance, oxidation resistance, etc. Some of the aging tests for composite pipes are accelerated aging test, natural aging test, etc.
How are composite pipes maintained?
Composite pipes are maintained using different practices, such as:
- Pigging: Pigging involves inserting a device called a pig into the pipe and pushing it through the pipe by the fluid flow or by an external force. The pig can perform various functions, such as cleaning, inspecting, measuring, or sealing the pipe.
- Cathodic protection: Cathodic protection involves applying an electric current to the pipe to prevent or reduce the corrosion of the pipe by the surrounding environment. Cathodic protection can be performed on both metallic and non-metallic pipes to protect them from electrochemical reactions that cause metal loss or degradation.
- Coating: Coating involves applying a protective layer or coating to the pipe surface to prevent or reduce the corrosion, erosion, abrasion, or impact damage of the pipe by the surrounding environment. Coating can be performed on both new and existing pipes to enhance their durability and performance.
- Patching: Patching involves applying a patch or a repair material to the pipe surface to fix any cracks or damages in the pipe wall or bore. Patching can be performed on both new and existing pipes to restore their integrity and functionality.
What are the types of composite pipes?
Composite pipes can be classified into different types, based on the type of composite material, such as:
- Thermoplastic composite pipe (TCP): TCP is a composite pipe that consists of a thermoplastic inner liner (such as polyethylene or polyamide) that is reinforced with continuous fibers (such as glass or carbon) embedded in a thermoplastic matrix (such as polypropylene or polyvinylidene fluoride).
- Glass reinforced plastic (GRP): GRP is a composite pipe that consists of a thermosetting resin (such as epoxy or polyester) that is reinforced with glass fibers.
- Fiber reinforced plastic (FRP): FRP is a composite pipe that consists of a thermosetting resin (such as epoxy or vinyl ester) that is reinforced with fibers other than glass (such as carbon or aramid).
- Bio-composite pipe: Bio-composite pipe is a composite pipe that consists of a biodegradable or bio-based resin (such as polylactic acid or starch) that is reinforced with natural fibers (such as flax or hemp).
What are the applications of composite pipes?
Composite pipes are widely used in various industries and sectors, such as:
- Oil and gas: Composite pipes are used for oil and gas transportation, distribution, and production, especially in subsea, deepwater, offshore, and onshore applications. Composite pipes can offer high corrosion resistance, high pressure resistance, high temperature resistance, etc., for oil and gas applications.
- Water: Composite pipes are used for water supply, distribution, and treatment, especially in potable water, wastewater, irrigation, desalination, and hydroelectric applications. Composite pipes can offer high hygiene, high durability, high efficiency, etc., for water applications.
- Mining: Composite pipes are used for mining transportation, extraction, and processing, especially in slurry, tailings, leaching, and ventilation applications. Composite pipes can offer high abrasion resistance, high erosion resistance, high impact resistance, etc., for mining applications.
- Power: Composite pipes are used for power generation, transmission, and distribution, especially in thermal power, nuclear power, wind power, and solar power applications. Composite pipes can offer high thermal stability, high electrical insulation, high fire resistance, etc., for power applications.
What are the future trends and opportunities for composite pipes?
Composite pipes are constantly innovated to meet the changing needs and challenges of the market. Some of the future trends and opportunities for composite pipes are:
- Smart composites: Smart composites are composite materials that can sense, respond, or adapt to external stimuli or changes in their environment. Smart composites can be classified into different types, such as self-healing composites, self-cleaning composites, self-monitoring composites, and self-regulating composites.
- Nano-composites: Nano-composites are composite materials that use nanoscale structures or particles to enhance their properties and performance. Nano-composites can be classified into different types, such as carbon nanotube composites, graphene composites, nanoclay composites, and nanofiber composites.
- Hybrid composites: Hybrid composites are composite materials that use two or more different types of fibers or matrices to create a new material with synergistic effects. Hybrid composites can be classified into different types, such as interply hybrid composites, intraply hybrid composites, sandwich hybrid composites, and functionally graded hybrid composites.
How are composite pipes evaluated?
Composite pipes are evaluated using cost-benefit analysis (CBA), which is an analytical technique that assesses the economic, environmental, and social impacts of a project or policy on society as a whole. CBA compares the total costs and benefits of a project or policy over its lifetime, expressed in present value terms. CBA aims to answer the question: Is the project or policy worth doing from a social perspective?
The main steps of CBA are:
- Define the scope and objective of the analysis: This step involves defining the purpose, scope, objective, and criteria of the analysis. It also involves identifying the project or policy options to be compared, such as using composite pipes versus steel pipes or doing nothing.
- Identify and quantify the costs and benefits of each option: This step involves identifying and quantifying all the relevant costs and benefits of each option for all the affected parties over the project or policy lifetime. The costs include all the resources used or sacrificed to implement the option, such as capital costs, operating costs, maintenance costs, environmental costs, social costs, etc. The benefits include all the positive effects or outcomes of the option, such as revenue, savings, efficiency, quality, safety, environmental benefits, social benefits, etc.
- Discount and aggregate the costs and benefits of each option: This step involves discounting and aggregating all the future costs and benefits of each option to their present values using a discount rate. The discount rate reflects the time value of money and the opportunity cost of capital. The present value of costs (PVC) is the sum of all the discounted costs of an option. The present value of benefits (PVB) is the sum of all the discounted benefits of an option.
- Calculate and interpret the net present value (NPV) and benefit-cost ratio (BCR) of each option: This step involves calculating and interpreting two key indicators of economic efficiency for each option: NPV and BCR. NPV is the difference between PVB and PVC. NPV measures the net benefit or surplus of an option to society. A positive NPV indicates that an option is economically efficient and socially desirable. A negative NPV indicates that an option is economically inefficient and socially undesirable. BCR is the ratio between PVB and PVC. BCR measures the return or payoff of an option to society. A BCR greater than one indicates that an option is economically efficient and socially desirable. A BCR less than one indicates that an option is economically inefficient and socially undesirable.
- Compare and rank the options based on NPV and BCR: This step involves comparing and ranking all the options based on their NPV and BCR values. The option with the highest NPV or BCR is usually preferred over other options. However, other factors such as risk, uncertainty, distributional effects, non-monetary impacts, etc., may also be considered in making a final decision.
This table summarizes the main steps and components of CBA for composite pipes. It shows the description, example, and formula of each component in terms of costs, benefits, discount rate, present value, NPV, and BCR.