Introduction: The Critical Role of Hydrogen Storage in a Clean Energy Future
As the world grapples with the urgent need to transition to clean energy sources, hydrogen has emerged as a promising solution with the potential to revolutionize our energy landscape. This versatile energy carrier offers a path to decarbonization across various sectors, from transportation to industry. However, the success of the hydrogen economy hinges on a critical factor: efficient and effective storage solutions.
Hydrogen: The Versatile Clean Energy Carrier
Hydrogen stands out as a clean energy carrier due to its unique properties:
- High energy density: Hydrogen has nearly three times the energy content of gasoline on a mass basis.
- Zero emissions: When used in fuel cells, hydrogen produces only water, electricity, and heat.
- Versatility: It can be used across multiple sectors, including transportation, industry, and power generation.
- Renewable production: Hydrogen can be produced from various renewable sources, supporting the transition to a sustainable energy system.
“Hydrogen is not just a fuel; it’s a key enabler of the clean energy transition, offering a pathway to decarbonize sectors that are difficult to electrify directly.”
– Innovellix Technical Director
The Imperative of Efficient Hydrogen Storage
While hydrogen offers immense potential, its widespread adoption faces a significant challenge: storage. The importance of efficient hydrogen storage cannot be overstated for several reasons:
- Energy density challenges: Despite its high energy content by weight, hydrogen has a low volumetric energy density at ambient conditions, necessitating advanced storage solutions.
- Safety considerations: Proper storage is crucial to ensure the safe handling and use of hydrogen across various applications.
- Enabling infrastructure: Effective storage solutions are essential for developing a robust hydrogen distribution network.
- Supporting renewable integration: Hydrogen storage can act as a buffer for intermittent renewable energy sources, enhancing grid stability.
Current Hydrogen Storage Landscape
Several methods for hydrogen storage are currently in use or under development:
Storage Method | Description | Advantages | Challenges |
---|---|---|---|
Compressed Gas | Hydrogen stored at high pressures (350-700 bar) | Established technology, fast refueling | Low volumetric density, high energy for compression |
Liquid Hydrogen | Hydrogen cooled to -253°C | Higher density than compressed gas | Energy-intensive liquefaction, boil-off losses |
Metal Hydrides | Hydrogen bonded with metal alloys | High volumetric density, low pressure storage | Heavy weight, slow kinetics |
Chemical Carriers | Hydrogen bound in chemical compounds | Liquid at ambient conditions, uses existing infrastructure | Energy required for hydrogen release, purity issues |
The Promise of Composite Gas Cylinders
Among the various storage solutions, composite gas cylinders have emerged as a leading technology for hydrogen storage, particularly for mobile and distributed applications. These advanced containers offer several key advantages:
- Lightweight design: Composite materials significantly reduce the overall weight of storage systems, crucial for transportation applications.
- High pressure capacity: Able to withstand pressures up to 700 bar, enabling higher hydrogen density storage.
- Enhanced safety: Advanced materials and designs provide improved safety features compared to traditional metal tanks.
- Scalability: Composite cylinders can be tailored for various applications, from portable devices to large-scale storage.
“Composite gas cylinders represent a quantum leap in hydrogen storage technology, offering the perfect balance of weight, safety, and performance needed to accelerate the hydrogen economy.”
– Innovellix CTO
Addressing the Challenges of Hydrogen Storage
Despite the promising attributes of composite gas cylinders, several challenges must be addressed to fully realize their potential in the hydrogen economy:
1. Cost Reduction
Currently, the production costs of composite cylinders are higher than traditional storage methods. Efforts to reduce costs include:
- Optimizing manufacturing processes
- Developing new, cost-effective materials
- Scaling up production to achieve economies of scale
2. Performance Optimization
Ongoing research aims to enhance the performance of composite cylinders through:
- Improving hydrogen storage density
- Enhancing thermal management for more efficient filling and discharging
- Extending the lifespan of cylinders to reduce lifecycle costs
3. Safety and Standardization
Ensuring the safety and reliability of composite cylinders is paramount. Key focus areas include:
- Developing robust safety standards and testing protocols
- Implementing advanced monitoring and control systems
- Harmonizing international regulations to facilitate global adoption
The Role of Composite Cylinders in Various Sectors
The versatility of composite gas cylinders positions them as a crucial technology across multiple sectors in the emerging hydrogen economy:
Transportation
In the transportation sector, composite cylinders are enabling the development of hydrogen fuel cell vehicles with improved range and performance:
- Passenger vehicles: Lightweight cylinders contribute to extended driving ranges.
- Heavy-duty trucks: High-capacity storage supports long-haul transportation needs.
- Buses and trains: Efficient storage systems enable practical refueling and operation schedules.
Industry
Industrial applications benefit from the scalability and safety features of composite cylinders:
- Chemical processing: On-site hydrogen storage for various industrial processes.
- Steel manufacturing: Supporting the transition to hydrogen-based steel production.
- Power generation: Enabling hydrogen use in gas turbines and fuel cells for electricity production.
Energy Storage and Grid Balancing
Composite cylinders play a crucial role in integrating renewable energy sources into the grid:
- Long-duration storage: Seasonal storage of excess renewable energy as hydrogen.
- Grid stabilization: Rapid response capabilities for balancing supply and demand fluctuations.
- Decentralized energy systems: Supporting microgrids and off-grid applications.
The Future of Hydrogen Storage: Innovations on the Horizon
As research and development in hydrogen storage technologies continue, several promising innovations are emerging that could further enhance the capabilities of composite gas cylinders:
1. Advanced Materials
Next-generation composite materials are being developed to improve the performance and cost-effectiveness of hydrogen storage:
- Nanocomposites: Incorporating nanomaterials to enhance strength and reduce permeation.
- Biobased composites: Exploring sustainable materials to reduce environmental impact.
- Smart materials: Developing self-healing composites for improved durability and safety.
2. Hybrid Storage Systems
Innovative approaches combine different storage technologies to optimize performance:
- Cryo-compressed storage: Merging the benefits of liquid and compressed gas storage.
- Composite-metal hybrid tanks: Combining the strengths of different materials for enhanced properties.
3. Integrated Systems
Future storage solutions may incorporate additional functionalities:
- Built-in purification: Integrating hydrogen purification capabilities within the storage system.
- Smart monitoring: Embedding sensors and IoT connectivity for real-time performance tracking.
- Thermal management: Incorporating advanced cooling systems for more efficient operation.
“The future of hydrogen storage lies in integrated, intelligent systems that not only store hydrogen safely and efficiently but also actively contribute to the overall performance of hydrogen-powered applications.”
– Innovellix SEO
Conclusion: The Path Forward
As we stand on the brink of a hydrogen-powered future, the critical role of efficient and effective storage solutions cannot be overstated. Composite gas cylinders have emerged as a promising technology, offering a unique combination of lightweight design, high pressure capacity, and enhanced safety features that position them at the forefront of hydrogen storage solutions.
However, realizing the full potential of hydrogen as a clean energy carrier will require continued innovation, investment, and collaboration across industries and sectors. By addressing the challenges of cost, performance, and safety, while leveraging emerging technologies and materials, we can unlock the true potential of hydrogen storage and pave the way for a sustainable, clean energy future.
The journey towards widespread adoption of hydrogen technologies is complex and multifaceted, but the potential rewards – in terms of environmental sustainability, energy security, and economic growth – are immense. As we delve deeper into the world of composite gas cylinders and their role in the hydrogen economy, we’ll explore the technical innovations, economic considerations, and environmental impacts that make this technology so promising for the future of clean energy storage.
Understanding Composite Gas Cylinders: Structure and Materials
Composite gas cylinders represent a significant leap forward in hydrogen storage technology. These advanced containers are engineered to safely store hydrogen at high pressures while maintaining a lightweight profile. Let’s dive deep into the structure and materials that make these cylinders so promising for the future of clean energy.
At its core, a composite gas cylinder consists of two main components: an inner liner and an outer reinforcement layer. The inner liner serves as a gas-tight barrier, preventing hydrogen from escaping. The outer layer, typically made of high-strength fibers, provides the structural integrity needed to withstand high internal pressures.
The inner liner is usually constructed from materials such as high-density polyethylene (HDPE), aluminum, or steel. HDPE liners are becoming increasingly popular due to their lightweight nature and excellent chemical resistance. Aluminum liners offer a good balance of weight and permeability, while steel liners provide maximum durability but at a higher weight cost.
The outer reinforcement layer is where composite materials truly shine. This layer typically consists of high-strength fibers embedded in a resin matrix. The most common fibers used are carbon fiber, glass fiber, and aramid (such as Kevlar). Each of these materials brings unique properties to the table:
- Carbon fiber: Exceptional strength-to-weight ratio and stiffness
- Glass fiber: Good strength and lower cost compared to carbon fiber
- Aramid: High impact resistance and excellent fatigue properties
The choice of fiber depends on the specific application requirements and cost considerations. Many high-performance cylinders use a combination of these fibers to optimize performance.
Composite gas cylinders are classified into different types based on their construction:
Type | Description | Typical Use |
---|---|---|
Type I | All-metal construction | Low-pressure applications |
Type II | Metal liner with partial fiber wrapping | Medium-pressure applications |
Type III | Metal liner with full fiber wrapping | High-pressure applications |
Type IV | Plastic liner with full fiber wrapping | Ultra-high-pressure applications |
Type III and Type IV cylinders are the most promising for hydrogen storage due to their ability to withstand high pressures while maintaining a low weight. These cylinders can typically handle pressures up to 700 bar (10,000 psi), allowing for significant hydrogen storage capacity.
The manufacturing process for composite cylinders is a critical factor in their performance. The most common method is filament winding, where continuous fibers are precisely wound around the liner in a computer-controlled process. This technique allows for optimal fiber orientation to maximize strength and minimize weight.
“The precision of the filament winding process is crucial. Even small variations in fiber tension or orientation can significantly impact the cylinder’s performance and safety.”
– Innovellix Technical Director
Advanced manufacturing techniques are continually being developed to improve cylinder performance. For example, some manufacturers are exploring the use of 3D printing to create complex liner geometries that optimize gas flow and storage efficiency.
The resin matrix used to bind the fibers is another critical component. Epoxy resins are commonly used due to their excellent adhesion properties and chemical resistance. However, researchers are exploring new resin formulations to further enhance performance, such as self-healing resins that can automatically repair minor damage.
One of the key advantages of composite cylinders is their ability to be tailored for specific applications. By adjusting the fiber type, orientation, and resin formulation, manufacturers can optimize cylinders for different pressure ranges, temperature conditions, and even specific vehicle designs.
“The versatility of composite materials allows us to design cylinders that meet the exact needs of each application, whether it’s for a passenger vehicle, a long-haul truck, or a stationary storage system.”
– Innovellix CTO
Safety is paramount in the design of composite gas cylinders. These cylinders undergo rigorous testing, including burst tests, cycle tests, and environmental exposure tests. Many cylinders are equipped with smart sensors that can monitor internal pressure, temperature, and even detect potential leaks or damage.
The future of composite gas cylinders looks promising, with ongoing research focused on further improving their performance. Some areas of active development include:
- Nano-enhanced materials for improved strength and gas barrier properties
- Advanced fiber architectures for optimized stress distribution
- Integration of energy-absorbing materials for enhanced crash safety
- Development of recyclable and biodegradable composites for improved sustainability
As hydrogen continues to play a larger role in our clean energy future, the importance of efficient and safe storage solutions cannot be overstated. Composite gas cylinders, with their unique combination of high-performance materials and advanced engineering, are poised to meet this challenge head-on.
“The rapid advancements we’re seeing in composite materials and manufacturing techniques are positioning these cylinders at the forefront of hydrogen storage technology. They’re not just a stepping stone – they’re a long-term solution for safe, efficient hydrogen storage.”
– Innovellix SEO
Understanding the structure and materials of composite gas cylinders is crucial for appreciating their potential impact on the hydrogen economy. As we continue to refine and improve these technologies, we move closer to a future where clean, hydrogen-powered solutions are not just possible, but practical and widespread.
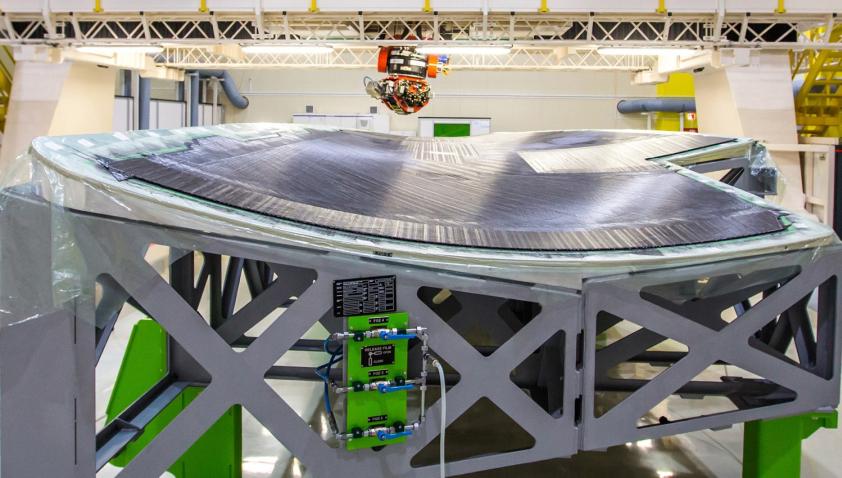
Key Advantages of Composite Cylinders for Hydrogen Storage
As we journey towards a sustainable energy future, hydrogen emerges as a promising clean energy carrier. However, the challenge of storing this lightweight gas efficiently and safely has been a significant hurdle. Enter composite cylinders – a game-changing technology that’s revolutionizing hydrogen storage. Let’s dive into the key advantages that make composite cylinders the most promising technology for hydrogen storage.
1. Lightweight Design and Improved Fuel Efficiency
One of the most significant advantages of composite cylinders is their lightweight nature. Compared to traditional metal tanks, composite cylinders can be up to 70% lighter. This weight reduction has a cascading effect on overall vehicle performance and fuel efficiency.
“The lightweight nature of composite cylinders is a game-changer for hydrogen-powered vehicles. Every kilogram saved in tank weight translates to extended range and improved fuel efficiency.”
– Innovellix Technical Director
1.1 Comparison with Traditional Storage Methods
Let’s compare the weight of different hydrogen storage methods for a 5 kg hydrogen capacity:
Storage Method | Tank Weight (kg) | Total Weight (kg) |
---|---|---|
Steel Tank (Type I) | 125 | 130 |
Aluminum Tank (Type III) | 55 | 60 |
Composite Cylinder (Type IV) | 35 | 40 |
As we can see, composite cylinders offer a significant weight advantage, which directly translates to improved vehicle performance.
1.2 Impact on Vehicle Performance
The lightweight nature of composite cylinders contributes to vehicle performance in several ways:
- Increased Range: Lighter vehicles require less energy to move, extending the driving range.
- Improved Acceleration: Less weight means better power-to-weight ratio, resulting in improved acceleration.
- Enhanced Handling: Lower vehicle weight improves maneuverability and reduces wear on suspension components.
- Increased Payload Capacity: For commercial vehicles, lighter tanks mean more capacity for cargo.
2. High Pressure Capacity and Increased Storage Density
Composite cylinders excel in their ability to withstand high pressures, allowing for more hydrogen to be stored in a given volume. This high-pressure capacity is crucial for achieving practical driving ranges in hydrogen-powered vehicles.
2.1 Technical Specifications of Composite Cylinders
Modern Type IV composite cylinders can safely store hydrogen at pressures up to 700 bar (10,000 psi). This high-pressure storage significantly increases the amount of hydrogen that can be stored in a given volume.
Pressure (bar) | Hydrogen Density (kg/m³) | Energy Density (MJ/L) |
---|---|---|
350 | 23.3 | 2.8 |
700 | 39.3 | 4.7 |
As we can see, doubling the pressure from 350 bar to 700 bar increases the hydrogen density by nearly 70%, significantly improving the energy storage capacity.
2.2 Advancements in Pressure Ratings
The development of composite cylinders has seen steady improvements in pressure ratings over the years:
- 1990s: 350 bar (5,000 psi) systems
- 2000s: 700 bar (10,000 psi) systems become commercially available
- 2020s: Research into 1000+ bar systems for even higher storage density
“The ability of composite cylinders to safely contain hydrogen at such high pressures is a testament to the advanced materials and manufacturing techniques used in their production. This high-pressure capability is key to making hydrogen-powered vehicles a practical reality.”
– Innovellix CTO
3. Enhanced Safety Features
Safety is paramount when dealing with high-pressure hydrogen storage. Composite cylinders offer several advanced safety features that make them the preferred choice for hydrogen storage.
3.1 Burst Resistance and Failure Modes
Composite cylinders are designed with safety as a top priority. Some key safety features include:
- High Burst Pressure: Typically designed to withstand 2.25 times the service pressure
- Leak-Before-Burst Design: In case of damage, the cylinder is designed to leak slowly rather than catastrophically rupture
- Impact Resistance: The fiber wrapping provides excellent resistance to impacts and punctures
- Fire Resistance: Many composite cylinders include thermal protection systems to prevent rupture in case of fire
3.2 Smart Monitoring Systems
Modern composite cylinders often incorporate advanced monitoring systems:
- Pressure Sensors: Continuously monitor internal pressure
- Temperature Sensors: Track temperature changes that could affect cylinder integrity
- Strain Gauges: Detect any deformation or damage to the cylinder
- Wireless Communication: Allow real-time monitoring and early warning of potential issues
4. Durability and Corrosion Resistance
Composite cylinders offer superior durability and corrosion resistance compared to traditional metal tanks, leading to longer service life and reduced maintenance costs.
4.1 Longevity Compared to Metal Tanks
Composite cylinders typically have a design life of 15-30 years, compared to 10-15 years for metal tanks. This extended lifespan is due to several factors:
- Fatigue Resistance: The fiber reinforcement provides excellent resistance to cyclic loading
- Chemical Inertness: The inner liner is typically made of materials that do not react with hydrogen
- UV Resistance: Outer layers are designed to withstand prolonged exposure to sunlight
4.2 Performance in Various Environmental Conditions
Composite cylinders maintain their performance across a wide range of environmental conditions:
- Temperature Range: Typically rated for operation from -40°C to +85°C
- Humidity Resistance: The composite structure is not susceptible to moisture-induced degradation
- Salt Spray Resistance: Ideal for marine applications where metal tanks would be prone to corrosion
5. Versatility and Adaptability
Composite cylinders offer unparalleled versatility, making them suitable for a wide range of applications beyond just automotive use.
5.1 Applications in Different Sectors
The adaptability of composite cylinders has led to their adoption in various sectors:
- Automotive: Passenger cars, buses, and heavy-duty trucks
- Marine: Boats and ships, including large vessels
- Aerospace: Aircraft and spacecraft fuel systems
- Stationary Storage: Grid energy storage and backup power systems
- Portable Power: Fuel cell systems for remote or off-grid applications
5.2 Customization Potential
Composite cylinders can be customized to meet specific application requirements:
- Shape Flexibility: Can be designed in various shapes to fit available space
- Scalability: Easy to scale up or down in size for different storage capacities
- Integration: Can be designed to integrate seamlessly with other vehicle or system components
“The versatility of composite cylinders is a key factor in their widespread adoption. From cars to ships to grid storage, their adaptability is driving innovation across multiple industries.”
– Innovellix SEO
6. Cost-effectiveness and Scalability
While the initial cost of composite cylinders may be higher than traditional metal tanks, their long-term cost-effectiveness and potential for scalability make them an attractive option for hydrogen storage.
6.1 Initial Investment vs. Long-term Benefits
When considering the cost of composite cylinders, it’s important to look at the total cost of ownership:
- Lower Maintenance Costs: Due to their durability and corrosion resistance
- Extended Lifespan: Longer service life means less frequent replacement
- Fuel Efficiency Savings: Lightweight design contributes to overall vehicle efficiency
- Safety Benefits: Reduced risk of accidents and associated costs
6.2 Production Scalability
As demand for hydrogen storage solutions grows, the production of composite cylinders is becoming increasingly scalable:
- Automated Manufacturing: Advanced filament winding techniques allow for high-volume production
- Material Advancements: Ongoing research into more cost-effective fiber and resin materials
- Economies of Scale: Increasing production volumes are driving down costs
7. Environmental Benefits
Composite cylinders not only enable the use of clean hydrogen energy but also offer environmental advantages in their own right.
7.1 Contribution to Reducing Carbon Footprint
The use of composite cylinders contributes to carbon footprint reduction in several ways:
- Enabling Clean Energy: Facilitates the use of zero-emission hydrogen fuel
- Weight Reduction: Lighter vehicles consume less energy, reducing overall emissions
- Long Lifespan: Less frequent replacement means reduced manufacturing-related emissions
7.2 Recyclability and End-of-Life Considerations
While recycling composite materials can be challenging, progress is being made:
- Material Recovery: Techniques are being developed to recover carbon fibers for reuse
- Design for Recycling: New designs aim to make separation of materials easier at end-of-life
- Repurposing: Exploring second-life applications for cylinders that no longer meet automotive standards
8. Future Developments and Potential Improvements
The field of composite cylinders for hydrogen storage is rapidly evolving, with several exciting developments on the horizon:
- Higher Pressure Ratings: Research into 1000+ bar storage systems for even greater energy density
- Advanced Materials: Exploration of new fiber and resin combinations for improved performance
- Smart Cylinders: Integration of advanced sensors and IoT connectivity for real-time monitoring and predictive maintenance
- Improved Manufacturing: Development of faster, more efficient production techniques to reduce costs
- Enhanced Safety Features: Ongoing research into fire protection and impact resistance
“The future of composite cylinders is incredibly exciting. We’re not just improving existing technology; we’re reimagining what’s possible in hydrogen storage. The innovations we’re working on today will shape the clean energy landscape for decades to come.”
– Innovellix Technical Director
Conclusion: The Role of Composite Cylinders in the Hydrogen Economy
Composite cylinders stand at the forefront of hydrogen storage technology, offering a unique combination of advantages that make them indispensable in the transition to a hydrogen-based economy. Their lightweight design, high-pressure capacity, enhanced safety features, and versatility address many of the challenges that have historically hindered the widespread adoption of hydrogen as an energy carrier.
As we look to the future, the continued development and refinement of composite cylinder technology will play a crucial role in making hydrogen a viable and competitive energy option across various sectors. From powering our vehicles to storing renewable energy for the grid, composite cylinders are set to be a cornerstone of our clean energy infrastructure.
The journey towards a sustainable, hydrogen-powered future is well underway, and composite cylinders are helping to pave the way. As technology continues to advance and production scales up, we can expect to see even more innovative applications and improvements in the years to come. The promise of clean, efficient, and safe hydrogen storage is becoming a reality, thanks in large part to the remarkable capabilities of composite cylinders.
Comparing Composite Cylinders to Other Hydrogen Storage Methods
As we continue our exploration of hydrogen storage technologies, it’s crucial to understand how composite cylinders stack up against other storage methods. In this section, we’ll dive deep into a comparison of composite cylinders with alternative hydrogen storage solutions, examining their strengths, weaknesses, and potential applications.
1. Liquid Hydrogen Storage
Liquid hydrogen storage involves cooling hydrogen to its liquid state at -253°C (-423°F). This method offers some advantages but also comes with significant challenges.
Advantages of Liquid Hydrogen Storage:
- High energy density (about 8.5 MJ/L compared to 4.5 MJ/L for 700 bar compressed gas)
- Reduced storage volume compared to gaseous hydrogen
- Easier to transport in large quantities
Disadvantages of Liquid Hydrogen Storage:
- Significant energy required for liquefaction (typically 30-40% of the energy content of hydrogen)
- Continuous boil-off losses (0.3-3% per day)
- Complex and expensive cryogenic storage systems
- Safety concerns due to extremely low temperatures
“While liquid hydrogen offers impressive energy density, the energy-intensive liquefaction process and ongoing boil-off losses make it less practical for widespread use, especially in mobile applications.”
– Innovellix Technical Director
In contrast, composite cylinders for compressed hydrogen storage offer a more practical solution for many applications, particularly in the transportation sector. They don’t require the extreme cooling of liquid hydrogen, eliminating the need for complex cryogenic systems and reducing energy losses.
2. Metal Hydride Storage
Metal hydride storage involves absorbing hydrogen into metal alloys, forming metal hydrides. This method has been explored for its potential to store hydrogen at lower pressures and higher densities than compressed gas.
Advantages of Metal Hydride Storage:
- Higher volumetric density than compressed gas (up to 150 kg H2/m3)
- Lower operating pressures (typically 10-50 bar)
- Improved safety due to lower pressures and solid-state storage
Disadvantages of Metal Hydride Storage:
- Heavy weight of metal hydride materials (typically 2-3% hydrogen by weight)
- Slow kinetics of hydrogen absorption and desorption
- Heat management required during charging and discharging
- Limited operating temperature range
- High cost of some metal hydride materials
Composite cylinders, while operating at higher pressures, offer significant weight advantages over metal hydride systems. This makes them more suitable for mobile applications where weight is a critical factor.
3. Cryogenic Compressed Hydrogen
Cryogenic compressed hydrogen, also known as cryo-compressed hydrogen, combines aspects of both liquid and compressed gas storage. It involves storing hydrogen at low temperatures (typically around -150°C to -210°C) and moderate pressures (250-350 bar).
Advantages of Cryogenic Compressed Hydrogen:
- Higher volumetric density than room temperature compressed gas
- Lower pressures than typical high-pressure compressed gas storage
- Reduced boil-off compared to liquid hydrogen
Disadvantages of Cryogenic Compressed Hydrogen:
- Complex system requiring both cryogenic cooling and pressure containment
- Energy required for cooling, though less than for full liquefaction
- Limited commercial availability and higher cost
“Cryo-compressed hydrogen represents an interesting middle ground between liquid and compressed gas storage, but the complexity of the system currently limits its widespread adoption.”
– Innovellix CTO
Composite cylinders for compressed hydrogen storage offer a simpler and more cost-effective solution compared to cryo-compressed systems. While they may have lower volumetric density, their ease of use and established technology make them more practical for many applications.
4. Comparative Analysis: Composite Cylinders vs. Other Storage Methods
To better understand how composite cylinders compare to other hydrogen storage methods, let’s examine key performance metrics:
Storage Method | Gravimetric Density (wt%) | Volumetric Density (kg H2/m3) | Operating Pressure (bar) | Operating Temperature (°C) |
---|---|---|---|---|
Composite Cylinders (700 bar) | 5.5-6.5 | 40-45 | 700 | Ambient |
Liquid Hydrogen | ~100 (excluding tank) | 70-80 | 1-5 | -253 |
Metal Hydrides | 1-7 | 50-150 | 10-50 | 25-120 |
Cryo-Compressed (250 bar) | 5.5-6.5 | 55-60 | 250-350 | -150 to -210 |
This comparison highlights several key advantages of composite cylinders:
- Operational Simplicity: Composite cylinders operate at ambient temperatures, eliminating the need for complex cooling systems.
- Weight Efficiency: They offer competitive gravimetric density, crucial for mobile applications.
- Technological Maturity: Composite cylinders are a well-established technology with proven safety records.
- Scalability: The manufacturing process for composite cylinders is highly scalable, supporting widespread adoption.
5. Application-Specific Comparisons
Let’s examine how composite cylinders compare to other storage methods in specific applications:
5.1 Automotive Applications
For passenger vehicles and light-duty trucks, composite cylinders offer several advantages:
- Lightweight design improves vehicle efficiency
- Fast refueling times (3-5 minutes) comparable to conventional vehicles
- No boil-off losses during vehicle downtime
- Operational simplicity and lower maintenance requirements
In contrast, liquid hydrogen storage faces challenges in automotive applications due to boil-off losses and the complexity of cryogenic systems. Metal hydrides, while potentially offering higher volumetric density, struggle with weight issues and slow kinetics that can impact refueling times.
5.2 Stationary Storage
For large-scale stationary storage, the comparison becomes more nuanced:
- Liquid hydrogen may be more suitable for very large-scale storage due to its higher volumetric density
- Composite cylinders offer flexibility in scaling storage capacity and easier maintenance
- Metal hydrides could be viable for stationary applications where weight is less critical, but heat management remains a challenge
“In stationary applications, the choice between storage methods often comes down to scale, local regulations, and specific operational requirements. Composite cylinders offer a versatile solution that can be easily scaled and integrated into various systems.”
– Innovellix SEO
5.3 Transportation and Distribution
For hydrogen transportation and distribution, different storage methods have their niches:
- Liquid hydrogen is often preferred for long-distance bulk transport due to its high density
- Composite cylinders excel in regional distribution and for smaller-scale transport needs
- Cryo-compressed storage is being explored for long-haul trucking, offering a balance between density and operational flexibility
6. Safety Considerations
Safety is paramount in hydrogen storage, and each method has its own safety profile:
Composite Cylinders:
- Designed with multiple safety features, including burst-resistant construction
- Undergo rigorous testing and certification processes
- Leak-before-burst design provides an additional safety margin
Liquid Hydrogen:
- Extremely low temperatures pose risks of cryogenic burns
- Rapid expansion if containment is breached
- Requires specialized handling and storage equipment
Metal Hydrides:
- Generally considered safer due to lower operating pressures
- Potential for uncontrolled heat generation during rapid charging
- Some materials may be pyrophoric if exposed to air
Composite cylinders offer a strong safety profile, combining the benefits of established safety standards with advanced materials that provide inherent safety features.
7. Economic Considerations
The economic viability of different hydrogen storage methods depends on various factors:
Storage Method | Initial Cost | Operating Cost | Maintenance Cost |
---|---|---|---|
Composite Cylinders | Moderate | Low | Low |
Liquid Hydrogen | High | High (due to liquefaction and boil-off) | Moderate |
Metal Hydrides | Moderate to High | Low | Moderate |
Cryo-Compressed | High | Moderate | Moderate to High |
Composite cylinders offer a balanced economic profile, with moderate initial costs offset by low operating and maintenance costs. This makes them particularly attractive for applications requiring frequent cycling and long-term use.
8. Environmental Impact
The environmental impact of hydrogen storage methods extends beyond their operational phase:
- Composite Cylinders: Made from recyclable materials, with ongoing research into more sustainable production methods
- Liquid Hydrogen: High energy consumption for liquefaction impacts overall environmental footprint
- Metal Hydrides: Some rare materials used in advanced metal hydrides may have significant environmental impacts in extraction and processing
- Cryo-Compressed: Combines environmental considerations of both compressed gas and cryogenic systems
Composite cylinders, with their potential for recycling and ongoing improvements in production efficiency, offer a promising path for environmentally conscious hydrogen storage.
9. Future Developments and Potential
As hydrogen technology continues to evolve, each storage method is seeing ongoing research and development:
Composite Cylinders:
- Development of higher-pressure systems (900+ bar) for increased storage density
- Advanced materials for improved strength-to-weight ratios
- Integration of smart sensors for real-time monitoring and predictive maintenance
Liquid Hydrogen:
- Improved insulation technologies to reduce boil-off
- More efficient liquefaction processes to reduce energy consumption
Metal Hydrides:
- Research into new alloys with higher storage capacities and faster kinetics
- Development of nanostructured materials for improved performance
Cryo-Compressed:
- Optimization of temperature and pressure parameters for maximum efficiency
- Development of more cost-effective cryogenic systems
“The future of hydrogen storage lies in continuous innovation across all technologies. Composite cylinders, with their versatility and established foundation, are well-positioned to incorporate new advancements and maintain their competitive edge.”
– Innovellix Technical Director
Conclusion
In comparing composite cylinders to other hydrogen storage methods, it’s clear that each technology has its strengths and ideal applications. Composite cylinders stand out for their versatility, safety, and practicality across a wide range of uses, particularly in mobile and distributed storage applications.
While liquid hydrogen excels in large-scale stationary storage and long-distance transport, and metal hydrides offer potential for compact, low-pressure storage, composite cylinders provide a balanced solution that meets the needs of many current and emerging hydrogen applications. Their combination of lightweight design, operational simplicity, and scalability makes them a frontrunner in the race to establish widespread hydrogen infrastructure.
As the hydrogen economy continues to grow, it’s likely that we’ll see a mix of storage technologies deployed to meet diverse needs. However, the ongoing development of composite cylinder technology, coupled with its established safety record and economic viability, positions it as a key player in the future of hydrogen storage. Whether powering vehicles, supporting renewable energy integration, or enabling portable power solutions, composite cylinders are set to play a crucial role in unlocking the potential of hydrogen as a clean energy carrier.
Why Composite Gas Cylinders Are the Most Promising Technology for Hydrogen Storage
Hey there, future fuel enthusiasts! Are you ready to dive into the world of hydrogen storage? Buckle up, because we’re about to explore why composite gas cylinders are the coolest thing since sliced bread when it comes to storing this super-fuel of the future. It’s like giving hydrogen its own high-tech superhero suit!
The Hydrogen Hype: What’s the Big Deal?
Before we jump into the world of composite cylinders, let’s talk about why hydrogen is such a big deal. Hydrogen is like the Superman of fuels:
- Clean as a Whistle: When you use hydrogen, the only thing that comes out is water. No nasty smoke or greenhouse gases!
- Power Packed: Hydrogen packs a lot of energy in a small space. It’s like a tiny powerhouse!
- Versatile Victor: You can use hydrogen in cars, buses, trains, and even to power buildings.
But here’s the catch: hydrogen is a bit of a diva. It needs special care when we store and move it around. That’s where our heroes, the composite gas cylinders, come in!
Mind-Blowing Fact: Hydrogen is the lightest element in the universe, but it can pack three times more energy than gasoline of the same weight!
Composite Cylinders: The Superheroes of Hydrogen Storage
Now, let’s meet our stars of the show: composite gas cylinders. These aren’t your grandpa’s old metal tanks. They’re like the Iron Man suits of the gas cylinder world. Here’s why they’re so awesome:
- Lightweight Champions: Composite cylinders are way lighter than traditional metal ones. It’s like comparing a feather to a brick!
- Tough Cookies: Don’t let their light weight fool you. These cylinders are super strong and can handle high pressures.
- Rust? What Rust?: Unlike metal tanks, composite cylinders don’t rust. They laugh in the face of corrosion!
- Safety First: These cylinders are designed to be extra safe. If something goes wrong, they’re less likely to explode like a metal tank might.
Companies like Innovellix are at the forefront of developing these advanced composite solutions, pushing the boundaries of what’s possible in hydrogen storage technology.
The Secret Sauce: What Makes Composite Cylinders Tick?
You might be wondering, “What’s so special about these composite cylinders?” Well, it’s all about the materials and how they’re put together. Let’s break it down:
- Fiber Power: Composite cylinders use super-strong fibers like carbon or glass. These fibers are like the muscles of the cylinder.
- Resin Magic: The fibers are held together by special glue called resin. It’s like the skin that keeps everything in place.
- Layer Cake Design: The cylinders are built in layers, kind of like a high-tech sandwich. Each layer has a job to do.
- Liner Love: Inside the cylinder is a special liner that keeps the hydrogen from leaking out. It’s like the cylinder’s own personal bodyguard for the hydrogen.
The Big Picture: Composite cylinders are like a team of superheroes working together. Each part has its own superpower, but together they make an unbeatable force for storing hydrogen safely and efficiently.
Why Composite Cylinders Are the Future of Hydrogen Storage
Okay, so composite cylinders sound cool, but why are they the best choice for hydrogen storage? Let’s count the ways:
- More Hydrogen, Less Weight: Because they’re so light, you can carry more hydrogen without making your vehicle too heavy. It’s like packing a big lunch in a tiny lunchbox!
- Safety Dance: Composite cylinders are designed to fail safely if something goes wrong. Instead of a big boom, they might just leak slowly. That’s way less scary!
- Long-Lasting Legends: These cylinders can last for many years without wearing out. They’re like the energizer bunny of the gas cylinder world!
- Shape Shifters: Composite cylinders can be made in different shapes to fit better in cars or other tight spaces. They’re like the Transformers of the fuel storage world!
- Cool Under Pressure: They can handle super-high pressures, which means you can squish more hydrogen into the same space. It’s like giving hydrogen its own little high-pressure apartment!
Composite vs. Traditional: The Showdown
Let’s see how composite cylinders stack up against their old-school metal cousins:
Feature | Composite Cylinders | Metal Cylinders |
---|---|---|
Weight | Light as a feather | Heavy as a rock |
Strength | Super strong | Strong, but heavier |
Corrosion Resistance | Rust? What rust? | Can rust over time |
Safety in Failure | Fails safely, no explosion | Can explode if damaged |
Lifespan | Long-lasting champ | Good, but needs more care |
Shape Flexibility | Can be many shapes | Usually just cylinders |
As you can see, composite cylinders are winning this race by a mile!
The Green Team: Composites and the Environment
Now, you might be thinking, “This all sounds great, but are composite cylinders good for the planet?” Great question! Let’s look at the eco-friendly side of these high-tech tanks:
- Fuel Efficiency Boost: Because they’re so light, vehicles using composite cylinders use less fuel to carry them around. That means fewer emissions!
- Long-Lasting Love: Since these cylinders last a long time, we don’t need to make new ones as often. That saves energy and resources.
- Recyclable Rockstars: While it’s still a challenge, new technologies are making it easier to recycle composite materials.
- Clean Fuel Partner: By making it easier to use hydrogen, composite cylinders are helping to promote this clean fuel. It’s like they’re cheering, “Go green!”
Innovellix’s optimal composite solutions are at the forefront of developing these eco-friendly composite technologies, pushing the boundaries of what’s possible in sustainable hydrogen storage.
The Road Ahead: What’s Next for Composite Cylinders?
Hold onto your hats, because the future of composite cylinders is even more exciting! Here’s a sneak peek at what’s coming down the pipeline:
- Smart Cylinders: Imagine tanks that can tell you how much hydrogen is left or if there’s a problem. It’s like giving your cylinder its own brain!
- Even Lighter Materials: Scientists are working on new fibers and resins that could make cylinders even lighter and stronger.
- Shape-Shifting Tanks: Future cylinders might be able to change shape to fit different vehicles or spaces. Transformer tanks, anyone?
- Self-Healing Heroes: Some researchers are working on materials that can fix small damages by themselves. It’s like giving your cylinder superpowers!
Cool Fact: Some scientists are even looking into using special nanomaterials in composite cylinders. These tiny particles could make the cylinders even stronger and better at holding hydrogen!
Challenges on the Horizon: What’s Standing in Our Way?
Now, it’s not all smooth sailing in the world of composite cylinders. There are still some hurdles to overcome:
- Cost Concerns: Right now, composite cylinders can be pricier than metal ones. But as we make more of them, the price is coming down.
- Manufacturing Mastery: Making these high-tech cylinders takes special skills and equipment. We need more experts to join the composite crew!
- Testing Times: We need to keep developing better ways to test these cylinders to make sure they’re safe and strong.
- Recycling Riddles: While composites are great in use, we’re still figuring out the best ways to recycle them at the end of their life.
Your Role in the Composite Revolution
You might be thinking, “This all sounds cool, but what does it mean for me?” Well, as a citizen of the future, you have a part to play:
- Stay Informed: Keep learning about hydrogen and composite technologies. Knowledge is power!
- Spread the Word: Share what you’ve learned with friends and family. The more people know, the faster we can make progress.
- Support Green Tech: When you have the chance, support companies and policies that are pushing for cleaner fuels and better storage solutions.
- Think Hydrogen: Next time you’re thinking about a new car or energy solution, consider hydrogen options. Your choice can help drive the market!
Companies like Innovellix are leading the way in various markets, including hydrogen storage solutions. By supporting such innovative companies, you’re helping to shape a cleaner, more sustainable future.
Wrapping Up: The Composite-Powered Future
Whew! We’ve covered a lot of ground in our journey through the world of composite gas cylinders and hydrogen storage. From lightweight champions to shape-shifting future tanks, these high-tech containers are leading the charge in making hydrogen a practical fuel for our world.
Composite cylinders are more than just fancy gas tanks. They’re a key piece of the puzzle in our quest for cleaner, more efficient energy. By making it easier and safer to store and transport hydrogen, they’re helping to pave the way for a greener future.
Sure, there are still challenges to overcome, but the road ahead looks bright. With ongoing research and development, composite cylinders are set to become even better, smarter, and more eco-friendly.
So the next time you hear about hydrogen-powered cars or see a sleek new fuel cell vehicle, remember – there’s a good chance composite cylinders are part of the magic making it all possible. The composite revolution is here, and it’s helping to fuel a cleaner, more exciting future for all of us!
The Big Takeaway: Composite gas cylinders are the unsung heroes of the hydrogen revolution. They’re making it possible to store and use this clean fuel in ways we never could before. As this technology continues to improve, it’s opening doors to a future where clean, hydrogen-powered vehicles and devices are a part of our everyday lives. The future is looking lighter, stronger, and greener, thanks to the power of composites!
Economic Considerations: Cost-Effectiveness of Composite Cylinders
As we delve into the economic aspects of composite cylinders for hydrogen storage, it’s crucial to understand that their cost-effectiveness is not just about the initial price tag. We need to consider the entire lifecycle costs, performance benefits, and long-term economic implications. Let’s break down these factors to get a comprehensive view of the economic landscape surrounding composite cylinders.
Initial Investment vs. Long-term Benefits
At first glance, composite cylinders may seem more expensive than traditional metal tanks. However, this initial cost needs to be weighed against the long-term benefits and cost savings they offer.
Upfront Costs
The primary factors contributing to the higher initial costs of composite cylinders include:
- Advanced materials (carbon fiber, high-performance resins)
- Specialized manufacturing processes
- Rigorous testing and certification requirements
While these factors drive up the initial price, they also contribute to the superior performance and longevity of composite cylinders.
Long-term Cost Savings
Over time, composite cylinders can offer significant cost savings through:
- Reduced fuel consumption due to lighter weight
- Lower maintenance costs
- Extended lifespan compared to metal tanks
- Potential for higher resale value
“When evaluating the economics of composite cylinders, it’s crucial to look beyond the sticker price. The long-term operational savings and performance benefits often outweigh the higher initial investment, especially in high-use scenarios like commercial fleets.”
– Innovellix Technical Director
Cost Breakdown and Comparison
To better understand the economic implications, let’s break down the costs associated with composite cylinders and compare them to traditional alternatives.
Cost Factor | Composite Cylinders | Traditional Metal Tanks |
---|---|---|
Initial Purchase Price | Higher | Lower |
Installation Costs | Similar | Similar |
Maintenance Costs | Lower | Higher |
Operational Costs (fuel efficiency) | Lower | Higher |
Lifespan | Longer | Shorter |
End-of-Life Value | Potentially Higher | Lower |
Factors Influencing Cost-Effectiveness
Several factors can influence the cost-effectiveness of composite cylinders:
1. Scale of Production
As production volumes increase, economies of scale come into play. This can significantly reduce the per-unit cost of composite cylinders.
- Bulk purchasing of raw materials
- Streamlined manufacturing processes
- Amortization of research and development costs
2. Technological Advancements
Ongoing research and development in materials science and manufacturing techniques are continually improving the cost-effectiveness of composite cylinders.
- More efficient use of carbon fiber
- Advanced resin systems with improved performance
- Automated manufacturing processes reducing labor costs
3. Regulatory Environment
Government policies and regulations can significantly impact the economic viability of composite cylinders:
- Incentives for low-emission vehicles
- Carbon pricing mechanisms
- Fuel efficiency standards
4. Market Demand
As the demand for hydrogen-powered vehicles and systems grows, it can drive down costs through:
- Increased competition among manufacturers
- Greater investment in research and development
- Improved supply chain efficiencies
Cost Projections and Future Trends
Looking ahead, several trends are likely to impact the cost-effectiveness of composite cylinders:
1. Decreasing Carbon Fiber Costs
Carbon fiber, a key component in composite cylinders, has seen steady price decreases over the years. This trend is expected to continue, driven by:
- Increased production capacity
- Improved manufacturing processes
- Development of alternative precursors
2. Advancements in Manufacturing Technologies
Emerging technologies are set to revolutionize the production of composite cylinders:
- 3D printing of complex geometries
- Automated fiber placement systems
- In-situ polymerization techniques
3. Integration of Smart Technologies
The incorporation of smart sensors and monitoring systems can enhance the value proposition of composite cylinders by:
- Optimizing performance and efficiency
- Enabling predictive maintenance
- Enhancing safety features
“The integration of smart technologies in composite cylinders isn’t just about adding bells and whistles. It’s about creating a more efficient, safer, and ultimately more cost-effective hydrogen storage solution. This is where the true value lies in the long run.”
– Innovellix CTO
Case Studies: Real-World Cost-Effectiveness
To illustrate the economic benefits of composite cylinders, let’s look at some real-world examples:
Case Study 1: Commercial Fleet Operations
A logistics company transitioning to hydrogen-powered trucks found that despite the higher initial investment in composite cylinders:
- Fuel costs decreased by 15% due to improved vehicle efficiency
- Maintenance costs were reduced by 20% over a 5-year period
- The extended lifespan of the cylinders resulted in a 10% reduction in total cost of ownership
Case Study 2: Public Transportation
A city implementing hydrogen-powered buses with composite cylinders reported:
- 30% increase in operational range compared to metal tank equivalents
- 50% reduction in refueling time, improving overall fleet efficiency
- Projected 25% savings in lifecycle costs over a 12-year period
Economic Impact on the Hydrogen Economy
The cost-effectiveness of composite cylinders has broader implications for the hydrogen economy as a whole:
1. Accelerating Adoption
As composite cylinders become more cost-effective, they can drive faster adoption of hydrogen technologies across various sectors:
- Transportation (passenger vehicles, trucks, buses)
- Industrial applications
- Energy storage for renewable power systems
2. Infrastructure Development
The economic viability of composite cylinders can spur investment in hydrogen infrastructure:
- Refueling stations
- Production facilities
- Distribution networks
3. Job Creation and Economic Growth
The composite cylinder industry has the potential to create new jobs and drive economic growth:
- Manufacturing jobs
- Research and development positions
- Service and maintenance roles
Challenges and Opportunities
While the economic outlook for composite cylinders is promising, there are still challenges to overcome:
Challenges:
- High initial costs deterring some potential adopters
- Limited economies of scale in current production
- Perception of hydrogen as a niche technology
Opportunities:
- Continued research into more cost-effective materials and processes
- Government incentives to promote clean energy technologies
- Partnerships between industry players to drive innovation and reduce costs
“The economic challenges facing composite cylinders are not insurmountable. In fact, they present opportunities for innovation and collaboration that could lead to breakthroughs in cost-effectiveness. It’s an exciting time to be in this field.”
– Innovellix SEO
Strategies for Improving Cost-Effectiveness
To further enhance the economic viability of composite cylinders, several strategies can be employed:
1. Design Optimization
- Use of advanced simulation tools to optimize cylinder design
- Exploration of novel geometries to improve performance-to-cost ratio
- Integration of multifunctional materials to enhance value
2. Supply Chain Improvements
- Vertical integration to reduce costs and improve quality control
- Development of strategic partnerships with material suppliers
- Implementation of just-in-time manufacturing principles
3. Circular Economy Approaches
- Development of recycling and reuse programs for end-of-life cylinders
- Exploration of bio-based and recyclable composite materials
- Implementation of lifecycle assessment tools in product development
Conclusion: The Economic Promise of Composite Cylinders
As we’ve explored in this section, the economic considerations surrounding composite cylinders for hydrogen storage are complex and multifaceted. While the initial investment may be higher compared to traditional alternatives, the long-term benefits in terms of performance, efficiency, and durability make a compelling case for their cost-effectiveness.
The ongoing advancements in materials science, manufacturing technologies, and smart systems are continually improving the economic proposition of composite cylinders. As production scales up and the hydrogen economy gains momentum, we can expect to see further improvements in cost-effectiveness.
For businesses and policymakers looking to invest in sustainable energy solutions, composite cylinders represent not just a technological choice, but an economic opportunity. They are a key enabler of the hydrogen economy, offering a pathway to more efficient, cleaner, and ultimately more cost-effective energy systems.
As we move forward, it will be crucial to continue investing in research and development, fostering collaborations between industry and academia, and creating supportive policy frameworks. By doing so, we can unlock the full economic potential of composite cylinders and accelerate the transition to a sustainable hydrogen-powered future.
“The economic story of composite cylinders is still being written. With continued innovation and strategic investment, these advanced storage solutions have the potential to not only become more cost-effective but to drive the economics of the entire hydrogen ecosystem. The future is bright, and it’s powered by hydrogen stored in composite cylinders.”
– Innovellix Technical Director
Environmental Impact and Sustainability of Composite Cylinders
As the world shifts towards cleaner energy solutions, the environmental impact and sustainability of hydrogen storage technologies have come under increasing scrutiny. Composite cylinders, while offering significant advantages in terms of performance and safety, also present unique challenges and opportunities from an environmental perspective. In this section, we’ll explore the lifecycle environmental impact of composite cylinders, from raw material extraction to end-of-life considerations, and examine the ongoing efforts to enhance their sustainability.
1. Life Cycle Assessment of Composite Cylinders
To fully understand the environmental impact of composite cylinders, it’s essential to consider their entire life cycle. Life Cycle Assessment (LCA) is a standardized method for evaluating the environmental impacts associated with all stages of a product’s life, from raw material extraction through materials processing, manufacture, distribution, use, repair and maintenance, and disposal or recycling.
1.1 Raw Material Extraction and Processing
The primary materials used in composite cylinders include:
- Carbon fiber or glass fiber
- Epoxy resin or thermoplastic polymers
- Metal or polymer liners
Each of these materials has its own environmental footprint:
Material | Primary Environmental Concerns |
---|---|
Carbon Fiber | High energy intensity in production, potential for toxic emissions |
Glass Fiber | Lower energy intensity than carbon fiber, but still significant |
Epoxy Resin | Derived from petroleum, potential for VOC emissions |
Thermoplastic Polymers | Potentially more recyclable, but still petroleum-based |
Metal Liners | Mining impacts, energy-intensive processing |
“The environmental impact of raw material extraction for composite cylinders is significant, but it’s important to consider this in the context of the cylinder’s entire lifecycle performance. The lightweight nature of composites often leads to energy savings that can offset initial production impacts.”
– Innovellix Technical Director
1.2 Manufacturing Process
The manufacturing of composite cylinders, typically through filament winding processes, has its own environmental considerations:
- Energy consumption during production
- Potential for waste generation
- Use of solvents and other chemicals in the process
However, advancements in manufacturing technologies are continually improving the efficiency and reducing the environmental impact of these processes.
1.3 Use Phase
During their operational life, composite cylinders offer several environmental benefits:
- Lightweight design leading to improved fuel efficiency in transportation applications
- Longer lifespan compared to traditional metal cylinders, reducing the need for frequent replacements
- Higher storage capacity, potentially reducing the number of cylinders needed for a given application
1.4 End-of-Life Considerations
The end-of-life phase presents one of the most significant challenges for the sustainability of composite cylinders. Unlike metal cylinders, which are relatively easy to recycle, composite materials present unique recycling challenges due to their mixed material nature.
2. Environmental Benefits of Composite Cylinders
Despite the challenges, composite cylinders offer several environmental benefits that make them an attractive option for hydrogen storage:
2.1 Reduced Carbon Footprint in Transportation
The lightweight nature of composite cylinders can significantly reduce the overall weight of hydrogen-powered vehicles, leading to improved fuel efficiency. This weight reduction can result in substantial CO2 emissions savings over the lifetime of the vehicle.
Vehicle Type | Estimated CO2 Savings (over 10-year lifespan) |
---|---|
Passenger Car | 2-3 tons |
Light Commercial Vehicle | 4-6 tons |
Heavy-Duty Truck | 15-20 tons |
2.2 Enabling Clean Energy Transition
By providing efficient and safe storage solutions for hydrogen, composite cylinders play a crucial role in enabling the transition to clean energy. They support the development of hydrogen infrastructure, which is essential for the widespread adoption of hydrogen as a clean energy carrier.
“Composite cylinders are not just a storage solution; they’re a key enabler of the hydrogen economy. Their performance characteristics allow for the practical implementation of hydrogen technologies across various sectors, accelerating our transition to a cleaner energy future.”
– Innovellix CTO
2.3 Resource Efficiency
The durability and long lifespan of composite cylinders contribute to resource efficiency by reducing the need for frequent replacements. This longevity helps conserve raw materials and energy that would otherwise be required for manufacturing replacement cylinders.
3. Challenges in Sustainability
While composite cylinders offer significant environmental benefits, they also present several sustainability challenges that the industry is actively working to address:
3.1 Energy-Intensive Production
The production of carbon fiber, a key component in many high-performance composite cylinders, is particularly energy-intensive. Efforts are underway to reduce this energy consumption through:
- Development of alternative precursor materials
- Optimization of carbonization processes
- Exploration of renewable energy sources for production
3.2 End-of-Life Recycling
Recycling composite materials presents significant technical and economic challenges. Current efforts to improve recyclability include:
- Development of thermoplastic composites that are more easily recycled
- Advancement of chemical recycling processes for thermoset composites
- Exploration of mechanical recycling techniques for fiber recovery
3.3 Potential for Microplastic Pollution
As composite materials degrade, there is potential for the release of microplastic particles. Research is ongoing to understand and mitigate this risk, including:
- Development of biodegradable resin systems
- Improved surface treatments to reduce material shedding
- Enhanced end-of-life management to prevent environmental release
4. Innovations in Sustainable Composite Cylinder Technology
The composite cylinder industry is actively pursuing innovations to enhance sustainability across the entire lifecycle of their products:
4.1 Bio-Based and Recycled Materials
Researchers and manufacturers are exploring the use of bio-based and recycled materials in composite cylinders:
- Bio-based resins derived from plant sources
- Recycled carbon fiber from aerospace and automotive industries
- Natural fiber reinforcements as alternatives to glass or carbon fiber
4.2 Advanced Manufacturing Techniques
New manufacturing processes are being developed to reduce waste and energy consumption:
- Automated fiber placement for improved material efficiency
- Out-of-autoclave curing processes to reduce energy use
- Additive manufacturing for complex geometries and reduced material waste
4.3 Smart Cylinder Technologies
Integration of smart technologies can improve the sustainability of composite cylinders by:
- Enabling predictive maintenance to extend cylinder lifespan
- Optimizing usage patterns for improved efficiency
- Facilitating end-of-life management and recycling
“The future of composite cylinders lies in smart, sustainable designs. By integrating sensors and advanced materials, we can create cylinders that not only perform better but also have a significantly reduced environmental footprint throughout their lifecycle.”
– Innovellix SEO
5. Regulatory Landscape and Industry Initiatives
The sustainability of composite cylinders is increasingly influenced by regulatory requirements and industry-led initiatives:
5.1 Regulatory Developments
Governments and regulatory bodies are implementing policies to promote sustainability in the composite industry:
- Extended Producer Responsibility (EPR) schemes
- Mandatory recycling targets for composite materials
- Carbon pricing mechanisms affecting material choices
5.2 Industry Collaborations
Collaborative efforts within the industry are driving sustainability improvements:
- Development of standardized LCA methodologies for composite materials
- Establishment of recycling networks and infrastructure
- Joint research initiatives on sustainable materials and processes
6. Future Outlook and Sustainability Roadmap
The path towards more sustainable composite cylinders involves a multi-faceted approach:
6.1 Material Innovations
- Development of fully recyclable composite systems
- Advancement of bio-based materials with performance parity to conventional composites
- Integration of self-healing and self-monitoring capabilities for extended lifespan
6.2 Manufacturing Advancements
- Implementation of closed-loop manufacturing systems
- Increased use of renewable energy in production processes
- Development of zero-waste manufacturing techniques
6.3 End-of-Life Management
- Establishment of global recycling infrastructure for composite materials
- Development of economically viable recycling processes
- Implementation of design-for-recycling principles in cylinder development
6.4 Lifecycle Optimization
- Integration of LCA principles into the design process
- Development of cylinders optimized for specific application lifecycles
- Implementation of circular economy principles in the composite cylinder value chain
Conclusion
The environmental impact and sustainability of composite cylinders for hydrogen storage present both challenges and opportunities. While the production of composite materials can be energy-intensive and end-of-life management remains a significant challenge, the benefits of lightweight design, extended lifespan, and enabling clean energy technologies make composite cylinders a crucial component in the transition to a sustainable energy future.
As the industry continues to innovate, we can expect to see significant improvements in the sustainability profile of composite cylinders. From the development of bio-based and recyclable materials to the implementation of advanced manufacturing techniques and smart technologies, the future of composite cylinders is poised to align more closely with circular economy principles and sustainability goals.
The journey towards truly sustainable composite cylinders will require ongoing collaboration between material scientists, manufacturers, regulators, and end-users. By addressing the entire lifecycle of these products, from raw material extraction to end-of-life management, the composite cylinder industry has the potential to not only minimize its environmental impact but also to play a pivotal role in enabling the clean energy transition.
As we move forward, it will be crucial to continue investing in research and development, fostering cross-industry collaborations, and implementing supportive policies to drive the sustainability agenda. With concerted efforts and continued innovation, composite cylinders can become not just a high-performance solution for hydrogen storage, but also a model for sustainable technology in the clean energy sector.
Regulatory Landscape and Safety Standards for Composite Hydrogen Cylinders
As the hydrogen economy continues to grow, the regulatory landscape and safety standards for composite hydrogen cylinders play a crucial role in ensuring the safe and widespread adoption of this technology. This section delves into the complex web of international codes, certification processes, and emerging trends that shape the development and use of composite hydrogen cylinders.
1. International Codes and Standards
The regulatory framework for composite hydrogen cylinders is built upon a foundation of international codes and standards. These guidelines ensure consistency in design, manufacturing, testing, and use across different regions and applications.
1.1 Key International Standards
- ISO 11119-3: Specifies requirements for the design, manufacturing, and testing of fully wrapped composite gas cylinders
- ISO 11623: Outlines periodic inspection and testing procedures for composite gas cylinders
- UN GTR No. 13: Global technical regulation on hydrogen and fuel cell vehicles
- SAE J2579: Standard for fuel systems in fuel cell and other hydrogen vehicles
These standards form the backbone of regulatory compliance for composite hydrogen cylinders, ensuring a baseline of safety and performance across the industry.
1.2 Regional Variations
While international standards provide a global framework, regional variations exist to address specific local concerns and regulatory environments:
Region | Key Regulations | Unique Aspects |
---|---|---|
European Union | EC 79/2009, EU 406/2010 | Emphasis on type-approval process for hydrogen components |
United States | DOT FMVSS 304, NFPA 2 | Focus on crash safety and fire protection |
Japan | JARI S001, S002 | Stringent requirements for material compatibility with hydrogen |
China | GB/T 35544-2017 | Specific standards for fuel cell electric vehicles |
“Navigating the complex landscape of international and regional standards is crucial for manufacturers and operators in the hydrogen cylinder industry. Compliance with these standards not only ensures safety but also opens doors to global markets.”
– Innovellix Technical Director
2. Certification Processes
The certification of composite hydrogen cylinders involves rigorous testing and validation processes to ensure compliance with safety standards and regulatory requirements.
2.1 Type Approval Process
The type approval process typically involves the following steps:
- Design Review: Evaluation of cylinder design against applicable standards
- Prototype Testing: Rigorous testing of prototype cylinders
- Manufacturing Process Audit: Inspection of production facilities and processes
- Quality Management System Review: Assessment of quality control measures
- Documentation Review: Examination of technical documentation and test reports
- Final Approval: Issuance of type approval certificate
2.2 Key Performance Tests
Composite hydrogen cylinders must undergo a series of performance tests to achieve certification:
- Burst Test: Verifies the cylinder’s ability to withstand pressures well above normal operating conditions
- Cycle Test: Assesses the cylinder’s durability under repeated pressurization and depressurization
- Environmental Exposure Test: Evaluates resistance to various environmental conditions
- Bonfire Test: Ensures proper functioning of pressure relief devices in fire conditions
- Drop Test: Verifies the cylinder’s ability to withstand impact
- Permeation Test: Measures the rate of hydrogen permeation through the cylinder wall
“The certification process for composite hydrogen cylinders is not just a regulatory hurdle; it’s a critical step in ensuring the safety and reliability of these advanced storage solutions. Each test is designed to simulate real-world conditions and potential failure modes.”
– Innovellix CTO
3. Safety Considerations
Safety is paramount in the design, manufacture, and use of composite hydrogen cylinders. Several key safety considerations are addressed through regulatory requirements and industry best practices.
3.1 Material Compatibility
Ensuring material compatibility with hydrogen is crucial to prevent embrittlement and degradation over time. Regulations typically require:
- Use of hydrogen-compatible materials for all components in contact with hydrogen
- Extensive testing of materials under simulated service conditions
- Regular inspections to detect any signs of material degradation
3.2 Pressure Management
Effective pressure management is critical for the safe operation of composite hydrogen cylinders:
- Pressure Relief Devices (PRDs): Required to prevent over-pressurization
- Pressure Monitoring Systems: Often integrated to provide real-time pressure data
- Fill Protocols: Standardized filling procedures to prevent overfilling
3.3 Leak Detection and Management
Hydrogen’s small molecule size makes leak prevention and detection crucial:
- Stringent leak testing requirements during manufacturing and periodic inspections
- Implementation of advanced leak detection systems in hydrogen facilities
- Development of safe venting procedures for controlled hydrogen release
4. Emerging Trends and Future Outlook
The regulatory landscape for composite hydrogen cylinders is continually evolving to keep pace with technological advancements and growing market demands.
4.1 Harmonization of Standards
There is a growing push towards greater harmonization of international standards to facilitate global trade and adoption of hydrogen technologies:
- Efforts to align testing procedures across different regions
- Development of globally recognized certification processes
- Collaboration between standards organizations to reduce regulatory discrepancies
4.2 Integration of Smart Technologies
The incorporation of smart technologies in composite hydrogen cylinders is driving new regulatory considerations:
- Development of standards for integrated sensors and monitoring systems
- Regulatory frameworks for data management and cybersecurity in smart cylinders
- Certification processes for AI-driven predictive maintenance systems
“The integration of smart technologies in composite hydrogen cylinders is not just about adding features; it’s about creating a new paradigm of safety and efficiency. Regulators and industry leaders must work together to develop standards that embrace these innovations while ensuring robust safety measures.”
– Innovellix SEO
4.3 Addressing New Applications
As hydrogen finds new applications, regulations are adapting to address unique challenges:
- Aviation: Development of standards for high-altitude and aerospace applications
- Marine: Regulations for hydrogen storage in maritime environments
- Large-scale Storage: Standards for grid-scale hydrogen storage solutions
4.4 Focus on Sustainability
Emerging regulations are increasingly incorporating sustainability considerations:
- Life cycle assessment requirements for composite materials
- Standards for recyclability and end-of-life management of cylinders
- Incentives for use of bio-based or recycled materials in cylinder production
5. Challenges in Regulatory Compliance
While the regulatory framework for composite hydrogen cylinders is comprehensive, several challenges persist:
5.1 Keeping Pace with Innovation
The rapid pace of technological advancement in composite materials and hydrogen storage technologies often outpaces regulatory updates. This can lead to:
- Regulatory gaps for novel materials or designs
- Delays in bringing innovative products to market
- Potential safety risks if regulations don’t address new failure modes
5.2 Cost of Compliance
Meeting stringent regulatory requirements can be costly, particularly for smaller manufacturers:
- Expensive testing procedures
- Need for specialized equipment and facilities
- Ongoing costs for recertification and compliance monitoring
5.3 Global Market Access
Despite efforts towards harmonization, differences in regional standards can create barriers to global market access:
- Need for multiple certifications for different markets
- Variations in testing requirements across regions
- Potential for trade disputes over regulatory differences
6. Best Practices for Regulatory Compliance
To navigate the complex regulatory landscape, industry stakeholders can adopt several best practices:
6.1 Proactive Engagement with Regulators
- Participate in standards development processes
- Engage in dialogue with regulatory bodies to address emerging challenges
- Contribute to industry working groups focused on regulatory issues
6.2 Comprehensive Documentation
- Maintain detailed design and manufacturing records
- Document all testing procedures and results thoroughly
- Implement robust quality management systems
6.3 Continuous Education and Training
- Stay informed about regulatory updates and emerging standards
- Provide regular training for staff on compliance requirements
- Develop internal expertise in regulatory affairs
6.4 Investment in Advanced Testing Capabilities
- Develop in-house testing facilities where feasible
- Partner with accredited testing laboratories
- Explore advanced simulation techniques to complement physical testing
Conclusion
The regulatory landscape and safety standards for composite hydrogen cylinders form a critical foundation for the safe and widespread adoption of hydrogen technologies. As the industry continues to evolve, so too must the regulatory framework, balancing the need for safety with the imperative for innovation.
The future of composite hydrogen cylinders lies not just in technological advancements, but in the development of smart, adaptive regulatory systems that can keep pace with innovation while ensuring the highest standards of safety. By embracing emerging trends, addressing persistent challenges, and adopting best practices for compliance, the industry can pave the way for a safer, more efficient hydrogen economy.
As we look to the future, the continued collaboration between industry stakeholders, regulatory bodies, and research institutions will be crucial in shaping a regulatory landscape that fosters innovation, ensures safety, and accelerates the global transition to clean hydrogen energy.
Future Outlook: Challenges and Opportunities for Composite Gas Cylinders
As we look towards the future of hydrogen storage and the role of composite gas cylinders, it’s clear that both significant challenges and exciting opportunities lie ahead. This section will explore the potential hurdles facing the industry, as well as the promising developments that could shape the future of composite gas cylinders for hydrogen storage.
1. Technological Advancements
The rapid pace of technological innovation presents both challenges and opportunities for the composite gas cylinder industry.
1.1 Materials Science Breakthroughs
Advancements in materials science are opening up new possibilities for composite gas cylinders:
- Nanomaterials: Integration of nanomaterials like carbon nanotubes could enhance strength and reduce weight
- Smart Materials: Development of self-healing composites to improve longevity and safety
- Biobased Composites: Exploration of sustainable, bio-derived materials for more environmentally friendly cylinders
“The future of composite gas cylinders lies in the convergence of advanced materials and smart technologies. We’re not just making stronger cylinders; we’re creating intelligent storage solutions that can adapt to their environment and provide real-time data on their condition.”
– Innovellix Technical Director
1.2 Manufacturing Innovations
New manufacturing techniques are set to revolutionize the production of composite gas cylinders:
- Additive Manufacturing: 3D printing of complex geometries and integrated components
- Automated Fiber Placement: Precision layup for optimized strength-to-weight ratios
- In-situ Monitoring: Real-time quality control during the manufacturing process
2. Market Dynamics and Economic Factors
The future of composite gas cylinders is closely tied to broader market trends and economic considerations.
2.1 Hydrogen Economy Growth
The expansion of the hydrogen economy presents significant opportunities:
Sector | Potential Impact on Composite Cylinders |
---|---|
Transportation | Increased demand for lightweight, high-pressure storage solutions |
Energy Storage | Large-scale storage needs for grid balancing and renewable energy integration |
Industrial Applications | Growing use of hydrogen in manufacturing processes requiring safe storage |
2.2 Cost Considerations
Economic factors will play a crucial role in the adoption of composite gas cylinders:
- Raw Material Costs: Fluctuations in carbon fiber and resin prices could impact cylinder costs
- Scale Economies: Increased production volumes may lead to cost reductions
- Lifecycle Cost Analysis: Long-term benefits may outweigh higher initial costs
3. Regulatory Landscape and Safety Standards
The evolving regulatory environment will shape the future of composite gas cylinders.
3.1 Harmonization of Global Standards
Efforts towards global standardization could bring both challenges and opportunities:
- Potential for streamlined certification processes
- Challenges in aligning diverse regional requirements
- Opportunities for expanded market access with unified standards
3.2 Enhanced Safety Requirements
Increasing focus on safety could drive innovation in cylinder design:
- Development of advanced pressure relief systems
- Integration of smart sensors for real-time monitoring
- Improved fire resistance and impact protection technologies
“As we push the boundaries of hydrogen storage, safety remains our top priority. The future of composite gas cylinders will be defined by our ability to innovate within increasingly stringent safety frameworks.”
– Innovellix CTO
4. Environmental Considerations and Sustainability
The growing emphasis on sustainability presents both challenges and opportunities for the composite gas cylinder industry.
4.1 Lifecycle Assessment
Increasing focus on environmental impact throughout the product lifecycle:
- Development of more sustainable manufacturing processes
- Exploration of recyclable and biodegradable composite materials
- Implementation of closed-loop recycling systems for end-of-life cylinders
4.2 Carbon Footprint Reduction
Opportunities to contribute to overall carbon emission reductions:
- Lightweight cylinders improving vehicle fuel efficiency
- Enabling broader adoption of hydrogen as a clean energy carrier
- Potential for carbon capture and storage applications
5. Integration with Smart Technologies
The incorporation of smart technologies into composite gas cylinders offers exciting possibilities for the future.
5.1 Internet of Things (IoT) Integration
Connectivity and data-driven insights could revolutionize cylinder management:
- Real-time monitoring of pressure, temperature, and structural integrity
- Predictive maintenance capabilities to prevent failures
- Optimized fleet management and logistics for cylinder operators
5.2 Artificial Intelligence and Machine Learning
Advanced analytics could enhance safety and performance:
- AI-driven optimization of cylinder design for specific applications
- Machine learning algorithms for early detection of potential issues
- Automated decision-making for safe cylinder operation and maintenance
6. Challenges in Scaling Production
Meeting the growing demand for composite gas cylinders presents several challenges:
6.1 Manufacturing Capacity
- Need for significant investment in production facilities
- Challenges in maintaining quality control at higher production volumes
- Potential supply chain bottlenecks for key materials
6.2 Workforce Development
- Shortage of skilled workers in advanced composites manufacturing
- Need for specialized training programs and education initiatives
- Challenges in attracting talent to the composites industry
7. Emerging Applications and Market Opportunities
New applications for composite gas cylinders are emerging, presenting exciting opportunities for growth:
7.1 Aerospace and Aviation
- Lightweight hydrogen storage for fuel cell-powered aircraft
- High-pressure gas storage for satellite propulsion systems
- Cryogenic tanks for space exploration missions
7.2 Marine and Offshore Applications
- Hydrogen storage for zero-emission ships and boats
- Underwater compressed air energy storage systems
- Offshore wind energy storage solutions
7.3 Portable and Wearable Technologies
- Miniaturized composite cylinders for personal oxygen devices
- Integrated gas storage for advanced diving equipment
- Portable power solutions for remote and off-grid applications
“The versatility of composite gas cylinders is opening doors to applications we hadn’t even imagined a few years ago. From the depths of the ocean to the edge of space, these advanced storage solutions are enabling new possibilities across industries.”
– Innovellix SEO
8. Research and Development Priorities
To address future challenges and capitalize on opportunities, several key areas of research and development are emerging:
8.1 Material Innovations
- Development of stronger, lighter carbon fibers
- Exploration of novel matrix materials for improved performance
- Research into multifunctional composites with integrated sensing capabilities
8.2 Design Optimization
- Advanced computational modeling for optimized cylinder geometries
- Topology optimization for weight reduction and strength enhancement
- Development of modular and scalable cylinder designs
8.3 Manufacturing Process Improvements
- Automation and robotics for high-precision, high-volume production
- Development of rapid curing technologies for faster manufacturing
- Exploration of continuous manufacturing processes for large-scale production
9. Collaboration and Partnerships
The future of composite gas cylinders will likely be shaped by strategic collaborations across industries:
9.1 Industry-Academia Partnerships
- Joint research initiatives for breakthrough technologies
- Development of specialized education programs for composite engineering
- Shared facilities for advanced testing and prototyping
9.2 Cross-Sector Collaborations
- Partnerships between composite manufacturers and hydrogen producers
- Collaboration with automotive and aerospace industries for integrated design solutions
- Joint ventures with technology companies for smart cylinder development
10. Policy and Incentives
Government policies and incentives will play a crucial role in shaping the future of composite gas cylinders:
10.1 Research Funding
- Increased government investment in composite materials research
- Grants and subsidies for advanced manufacturing technologies
- Support for demonstration projects and pilot programs
10.2 Market Incentives
- Tax credits for adoption of composite cylinder technologies
- Regulatory frameworks promoting lightweight and safe hydrogen storage solutions
- Carbon pricing mechanisms favoring low-emission technologies
Conclusion: Navigating the Future Landscape
The future of composite gas cylinders for hydrogen storage is filled with both exciting opportunities and significant challenges. As we look ahead, several key themes emerge:
- Technological Innovation: Continued advancements in materials science, manufacturing processes, and smart technologies will drive the evolution of composite gas cylinders, enabling safer, more efficient, and more versatile storage solutions.
- Market Expansion: The growth of the hydrogen economy across various sectors will create new opportunities for composite gas cylinders, from transportation and energy storage to emerging applications in aerospace and marine industries.
- Sustainability Focus: Environmental considerations will play an increasingly important role, driving the development of more sustainable materials, manufacturing processes, and end-of-life solutions for composite cylinders.
- Regulatory Adaptation: The evolving regulatory landscape will shape the development and adoption of composite gas cylinders, with a continued emphasis on safety and standardization.
- Collaborative Approach: Addressing the challenges and capitalizing on the opportunities ahead will require close collaboration between industry players, academic institutions, and government bodies.
As the industry navigates this complex landscape, those who can innovate, adapt, and collaborate effectively will be best positioned to lead the way in shaping the future of hydrogen storage. The journey ahead is challenging, but the potential rewards – in terms of technological advancement, economic growth, and environmental impact – are immense.
The future of composite gas cylinders is not just about storing hydrogen; it’s about storing the potential for a cleaner, more sustainable energy future. As we continue to push the boundaries of what’s possible with these advanced storage solutions, we move closer to realizing the full potential of the hydrogen economy and its promise of clean, efficient, and abundant energy for generations to come.