
Composite pipe repairs involve applying fiber-reinforced polymer (FRP) materials to damaged pipes to restore structural integrity. These repairs provide a cost-effective and safe alternative to traditional weld repairs or full pipe replacements. Key benefits of composite pipe repairs include:
- Cost efficiency – Composite repairs can cost 50-80% less than pipe replacement
- Durability – Properly designed repairs can last 20+ years
- Versatility – Composites can repair complex geometries and variety of pipe materials
- Safety – No hot work required so reduced safety risks
- Minimal downtime – Many repairs can be done with the pipe still in service
Composite pipe repairs are used extensively in the oil & gas, chemical, power, and municipal industries. They allow asset owners to extend the lifetime of critical piping infrastructure suffering from corrosion, mechanical damage, or weld defects.
Why Perform Composite Pipe Repairs
Composite Pipe Repair
Composite pipeline repair is a method of restoring the structural integrity and functionality of damaged or corroded pipes using composite materials. Composite materials applied outside or/and inside bond to the pipe surface and provide strength and corrosion resistance. Composite pipeline repairs can be applied to various types of pipe defects, such as cracks, dents, gouges, and corrosion, and can be performed quickly and with minimal or no disruption to operations. Composite pipeline repairs are a cost-effective and reliable solution for extending the service life of pipelines.
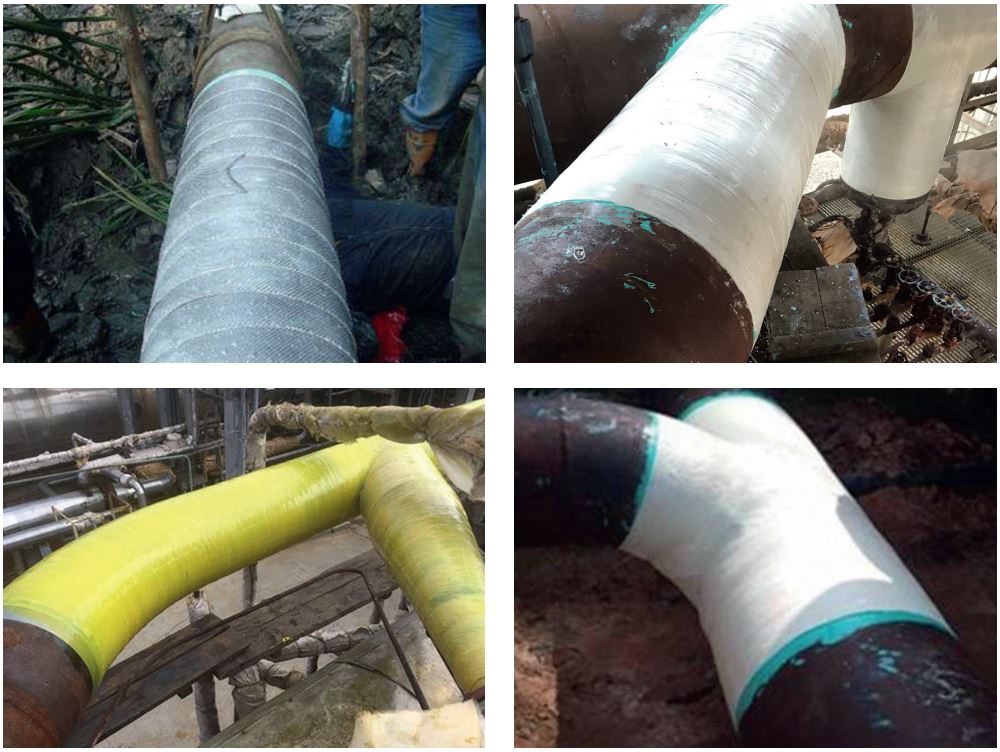
Piping systems transporting water, steam, oil, natural gas and other products are vital components across all industries. Over time, these pipes can experience different types of damage:
- External corrosion and pitting
- Cracks, gouges or dents
- Weld defects
- Internal corrosion or erosion

This damage threatens the structural integrity and pressure containment capability of the piping system. If left unaddressed, it can progress into leaks, ruptures or catastrophic failures. Performing a structural composite repair restores the load-bearing capacity of the pipe using fiber-reinforced polymer wrapping. This allows asset owners to cost-effectively extend the lifetime of their piping assets while avoiding unplanned outages or spills. Proactive repairs also reduce risks to personnel, environment and asset integrity. Overall, composite repairs provide an optimum balance between safety, cost and performance.
Composite Repair Materials
Composite pipe repairs consist of three components:
- Surface filler – Smooths pits/gouges and provides foundation
- Resin adhesive – Bonds all layers and provides corrosion protection
- Reinforcing fibers – Provide strength and stiffness
Fiber materials used include:
- Glass fiber
- Carbon fiber
- Aramid fiber
Carbon offers the highest strength and stiffness while glass is more cost-effective. Resin matrices are typically epoxy, polyester or vinyl ester.
Design Standards for Composite Repairs
Composite pipe repairs must adhere to recognized industry standards to ensure safety, reliability and confidence. The two main standards are:
- ASME PCC-2 – Article 4.1 Composite Repairs
- ISO 24817 – Petroleum and natural gas industries – Composite repairs
These standards provide requirements and guidelines for:
- Qualification testing of repair materials
- Engineering design procedures
- Installation and inspection
- Documentation and traceability
Adhering to these codes ensures that pipe repairs are engineered to validated methods and properly installed by certified technicians.
Advantages of Composite Pipe Repairs
Cost efficiency
- 50-80% cheaper than pipe replacement
- Faster installation reduces labor and downtime expenses
Minimal disruption
- Many repairs can be done online with no shutdown
- Shortens outage time for repairs needing isolation
Durability
- 20+ year design life
- Withstand harsh environments
Safety
- No hot work, fire or electrical hazards
- Lower safety risks for personnel
Custom solutions
- Engineer repairs for specific damage type and pipe specs
- Accommodate complex geometries
Composite Repair Process
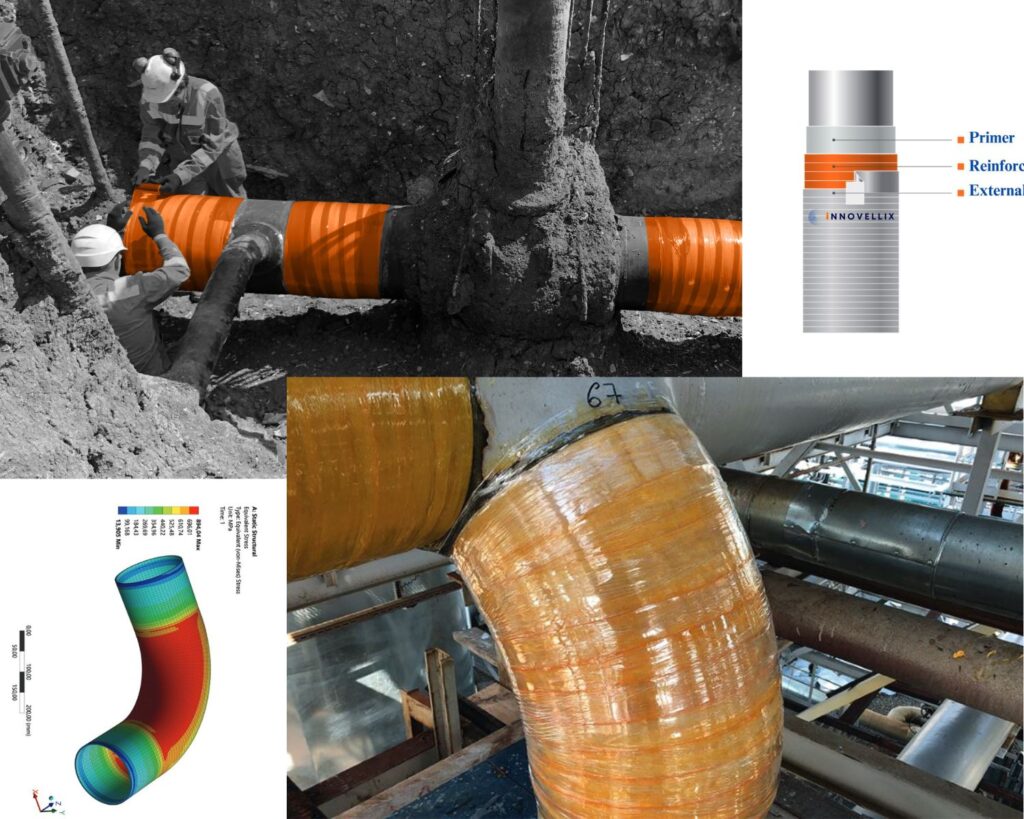
Performing a successful composite pipe repair involves careful planning, engineering design, surface preparation and installation stages: Planning
- Assess pipe specs, operating conditions and defect details
- Determine repair standards, materials and acceptance criteria
Design
- Engineer thickness, length and fiber orientation
- Account for pressure, thermal and external loads
Surface preparation
- Blast cleaning to remove coatings and corrosion
- Profile surface to 60-85μm anchor pattern
Installation
- Apply filler to reshape surface (if needed)
- Wrap resin-wetted reinforcing fibers
- Allow proper cure time before returning to service
Composite wrap pipeline repair
Composite wrap pipeline repair is a technique for fixing damaged pipes using fiber-reinforced polymer composites. This method involves wrapping the damaged pipe area with composites made of high-strength fibers and polymer resin, which reinforces the structure and restores its original pressure capacity. The process includes surface cleaning, applying adhesive, wrapping the composite material, and curing, followed by inspection to ensure integrity

Case Study: Natural Gas Transmission Pipeline Repair
A major gas utility experienced external corrosion and missing pipe supports on a 24-inch natural gas transmission pipeline. This prompted an immediate downrating of the maximum allowable operating pressure (MAOP) to 200psi. 6 weeks were required to design and install composite repairs on 600 linear feet of the pipeline using carbon fiber and fiberglass materials. This allowed the pipeline to be returned to full pressure service for the winter season. The composite reinforcement was designed to handle 1000psi even with a through-wall failure. It provides reliable long-term repairs with 50-year service life.
Composite Pipe Repair Materials
Choosing the right materials is critical for composite pipe repairs to restore the full structural integrity of the piping system. Repair systems consist of surface fillers, resins and fiber reinforcements.
Surface Fillers
Surface fillers, mastics or putties fill pits, gouges and surface irregularities to provide a smooth foundation for the composite wrap. Ideal properties include:
- Smooth consistency for easy spreading
- Rapid cure at ambient temperatures
- Strong adhesion and cohesive strength
- Resistance to cathodic disbondment
- Compatibility with resin system
Typical filler materials include epoxy, polyester or vinyl ester putties.
Resin Adhesives
The resin matrix bonds the components of the repair together and provides protection against corrosion or chemical attack. Key characteristics include:
- Strong adhesion to substrates and fibers
- Resistance to operational temperatures
- Chemical and corrosion resistance
- Strength, stiffness and toughness
Epoxy, polyester and vinyl ester are common resin options. Epoxy provides the best all-around performance.
Reinforcing Fibers
Fibers provide strength and stiffness to the repair laminate. The main options include: Glass Fibers
- Lower cost
- Provide moderate strength
- Susceptible to alkalis
Carbon Fibers
- Highest strength and stiffness
- 10 x stronger than steel
- Expensive
Aramid Fibers
- High strength-to-weight ratio
- Impact resistance
- Moderate stiffness
Fiber orientation, number of layers and wrapping technique must be engineered to suitable withstand stresses.
Engineering Design of Composite Repairs
To provide a safe and reliable long-term repair, composite reinforcements must be designed in accordance with recognized codes. Critical considerations include:
Operating Conditions
- Pressure, temperature cycles
- External loads like bending, vibration, soil movement
- Pipeline contents and compatibility
Defect Details
- Remaining wall thickness
- Length and orientation
- Rate of corrosion progression
Repair Standards
- ASME PCC-2 or ISO 24817
- Repair class, lifetime, documentation needs
Load Analysis
- Hoop, axial, shear, peel and thermal stresses
- Cyclic pressure and fatigue evaluation
- Failure mode analysis
Material Selection
- Resin, fibers and filler
- Strength, stiffness, toughness needs
- Environmental durability
The end result is a detailed work pack with repair dimensions, materials and installation instructions tailored to the damage.
Composite repair technology is used to restore basic abilities in various structures and elements. These include thin-walled and vertical pipes, pipelines used in oil and gas processing, salt water intake pipelines, pipelines at docks and terminals, ship hulls, and other structural elements.
The advantages of composite repairs are as follows:
– They can be performed without the need for extensive pipeline repair, providing stability to structures in underwater environments and areas with variable water levels. This technology can address damages such as dents, potholes, cavities, and up to 80% thinning of the door frame.
– Composite repairs have a fast curing time, are easy to apply, and facilitate high repair speed.
– They offer anti-corrosion protection.
– This technology allows for the restoration of pipeline integrity.
– It enables structural repairs to steel sheathing and members.
– Composite repairs are suitable for fixing leaks.
– They are applicable to main and process pipelines handling various types of media (excluding highly abrasive substances). The temperature range it can withstand is from -40°C to 140°C, with the upper-pressure limit dependent on the density of the transferred material layer.
Installation Procedures
Proper installation by trained technicians is mandatory for composite repairs to deliver their full reinforcement capability over the long term. Key steps include:
Surface Preparation
Thorough surface preparation ensures proper adhesion between the pipe surface and repair laminate. This involves:
- Grit blasting to near-white metal cleanliness
- Removing coatings, oxides and contamination
- Creating 60-85μm anchor profile
Installation
Certified technicians wrap the resin-wetted reinforcing fibers using a controlled hand-tension wrapping technique:
- Ensure intimate contact to surface profile
- Control 50% overlap between layers
- Alternate orientation between +/-55°
- Work from center outwards
Cure
- Allow repair resin to fully cure as per specifications before disturbing
- Do not return pipe to service prior to full cure
QA/QC
- Visual and NDE inspection to ensure no voids
- Adhesion testing to validate bond strength
- Documentation for traceability
Applications of Composite Repairs
Composite reinforcement is used to address many common pipe defects across a variety of industries: External Corrosion
- Restores pressure containment capability
- Arrests further corrosion progression
Internal Corrosion
- Stops through-wall failures
- Reinforces future wall loss
Mechanical Damage
- Repair dents, gouges, cracks
- Reinforce weld defects
Pipeline Bends
- Reinforce wrinkle bends and miter joints
- Repair lamination flaws
Typical applications include pipes, vessels, tanks and other assets in oil & gas, chemical, power, water and wastewater service.
Training and Certification
Composite materials must be installed properly by competent personnel to achieve reliable repairs. This requires: Specialized Training
- Installer and supervisor programs
- Workshop and hands-on installation
- Engineering design software
Certification & Documentation
- Tracking repair materials
- Documenting surface profile
- Recording steps with photos
- Generating reports
Quality Control
- NDE and adhesion testing
- Visual inspection for voids
- Prevent contamination
Formal training and certification gives confidence in consistent quality workmanship. Many material suppliers offer authorized installer programs.
Composite reinforcement provides owners of pipes, vessels and tanks a proven and cost-effective method to extend asset lifetime affected by corrosion, cracks or mechanical damage. Engineered composite repairs can restore structural integrity and pressure containment capacity in accordance with ASME and ISO standards. Their versatility and customizability makes them applicable across many industries including oil & gas, chemical, power generation and municipal services. With proper materials, engineering and installation, composite repairs provide safe and reliable long-term repairs. Their use avoids costly shutdowns and replacement projects. Overall, composite repair is an optimum life extension solution balancing safety, performance and value.