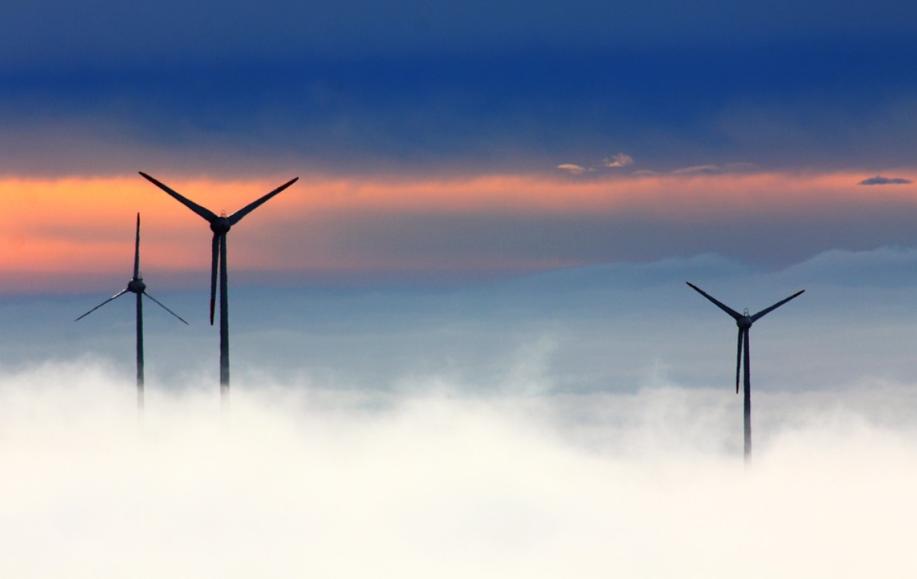
Composite materials have emerged as a game-changer in the field of wind energy, transforming the way we harness the power of the wind. These advanced materials, composed of two or more different components, have revolutionised the design and construction of wind turbines, making them more efficient, durable, and cost-effective. In this article, we will explore the remarkable impact of composite materials on the wind energy industry and delve into the various ways they are shaping the future of renewable energy.
The Rise of Composite Materials
Composite materials have gained significant traction in recent years due to their exceptional mechanical properties and versatility. By combining different materials, such as fibers and resins, engineers have been able to create lightweight, yet incredibly strong structures that can withstand the harsh conditions prevalent in wind energy applications. The development and widespread adoption of composites have opened up new avenues for innovation, enabling the design of larger and more efficient wind turbines.
Enhanced Efficiency and Performance
Lighter Blades for Increased Energy Capture
One of the key areas where composite materials have made a significant impact is in the construction of wind turbine blades. Traditionally, blades were primarily made of steel or fiberglass, but these materials posed limitations in terms of weight, size, and performance. With composites, manufacturers can now produce longer and lighter blades, allowing for increased energy capture from the wind. These materials provide the necessary strength and stiffness while reducing the overall weight, resulting in improved turbine efficiency.
Superior Strength and Durability
Composite materials offer exceptional strength-to-weight ratios, making them ideal for wind turbine components. The use of composites in critical areas, such as the rotor hub and tower, enhances structural integrity, enabling turbines to withstand higher wind speeds and harsh environmental conditions. The inherent durability of composites also leads to reduced maintenance and repair costs, as these materials are resistant to corrosion, fatigue, and degradation.
Cost-Effectiveness and Sustainability
Lower Manufacturing and Maintenance Costs
The adoption of composite materials has brought about cost advantages in both the manufacturing and maintenance of wind turbines. The manufacturing process of composites involves molding or laying up the material layers, which can be automated, resulting in increased production efficiency and reduced labor costs. Additionally, the lightweight nature of composites simplifies transportation and installation, reducing the overall project costs. Furthermore, the exceptional durability of composites minimizes the need for frequent repairs and replacements, resulting in long-term cost savings.
Environmental Benefits and Lifecycle Analysis
In the pursuit of sustainable energy solutions, composite materials offer significant environmental benefits. As wind energy continues to replace fossil fuel-based power generation, the use of composites further contributes to reducing greenhouse gas emissions. Moreover, composite materials can be recycled at the end of their lifecycle, minimizing waste and promoting a circular economy. Lifecycle analysis studies have shown that composite wind turbine blades have a lower environmental impact compared to conventional alternatives, making them an attractive choice for renewable energy projects.
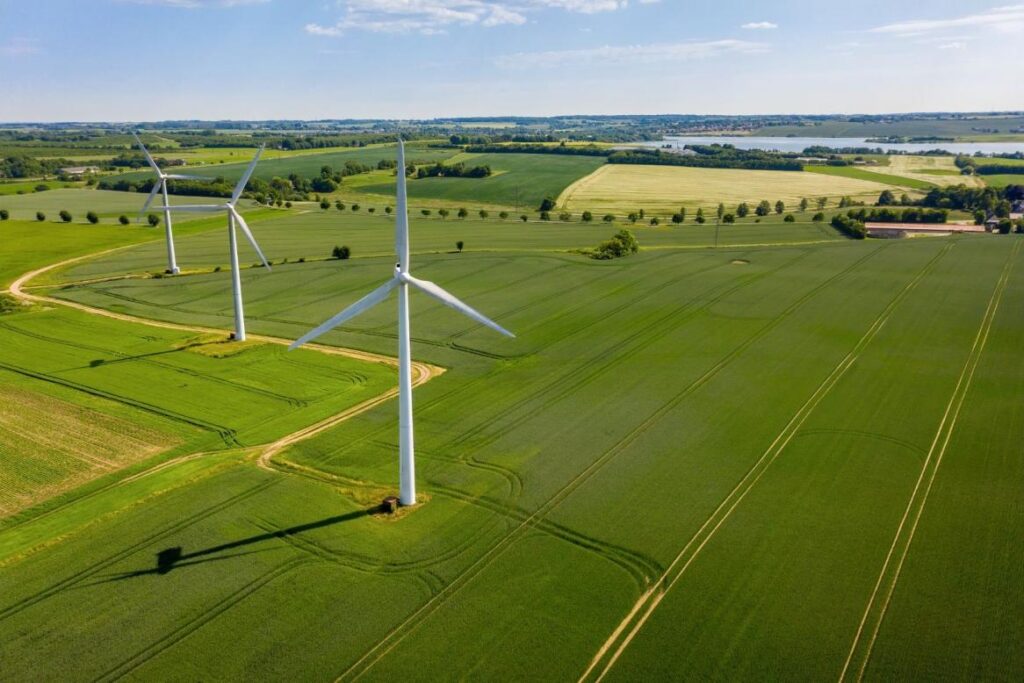
Advantages of Composite Materials in Wind Energy
2.1 Lightweight and High Strength: One of the key advantages of composite materials in wind energy is their high strength-to-weight ratio. Compared to traditional materials like steel, composites offer superior strength while being significantly lighter. This allows for the construction of larger and more efficient wind turbine blades that can capture more wind energy.
2.2 Fatigue Resistance: Wind turbines are subjected to constant and varying loads due to wind conditions. Composite materials exhibit excellent fatigue resistance, meaning they can withstand cyclic loading without experiencing significant degradation in performance. This makes composites highly durable and reliable in the long run.
2.3 Corrosion Resistance: Traditional materials like steel are prone to corrosion, especially in offshore wind farms where exposure to saltwater is inevitable. Composite materials, on the other hand, are highly resistant to corrosion, making them well-suited for offshore wind turbine installations. This not only extends the lifespan of wind turbine components but also reduces maintenance costs.
2.4 Design Flexibility: Composite materials offer greater design flexibility compared to conventional materials. They can be molded into complex shapes, allowing for optimized aerodynamic profiles and improved energy capture. This flexibility also enables designers to tailor the properties of composites for specific applications, optimizing their performance and efficiency.
Applications of Composite Materials in Wind Turbines:
3.1 Wind Turbine Blades: The most common application of composite materials in wind energy is the construction of turbine blades. Composite blades are longer, lighter, and more aerodynamically efficient compared to traditional blades made of steel or wood. This allows them to capture more wind energy and generate higher power outputs. Additionally, composite blades are less susceptible to fatigue, reducing the maintenance requirements and increasing the overall reliability of wind turbines.
3.2 Nacelles and Hubs: Composite materials are also used in the construction of nacelles and hubs, which house the generator, gearbox, and other vital components of a wind turbine. The lightweight nature of composites reduces the overall weight of the nacelle, enabling easier installation and reducing the structural loads on the tower. Moreover, composite materials’ corrosion resistance ensures the longevity of these components, even in harsh environments.
3.3 Tower Construction: Although towers are primarily made of steel or concrete, composite materials are increasingly being used to reinforce and strengthen critical areas of wind turbine towers. For instance, composite wraps can be applied to the tower’s base to enhance its structural integrity and prevent fatigue-related issues. This helps in prolonging the lifespan of the tower and reducing maintenance requirements.
The Future of Composite Materials in Wind Energy:
The use of composite materials in the wind energy industry is expected to grow rapidly in the coming years. Ongoing research and development efforts are focused on further improving the performance and cost-effectiveness of composite materials. This includes advancements in manufacturing techniques, such as automated processes, to reduce production time and costs. Additionally, the development of sustainable and recyclable composites is being explored to align with the industry’s environmental goals.
Composite materials have revolutionised the wind energy industry by offering a multitude of benefits, including lightweight construction, high strength, fatigue resistance, corrosion resistance, and design flexibility. With these advantages, wind turbines can be built larger, more efficient, and longer-lasting. As the demand for renewable energy continues to rise, composite materials will play an increasingly vital role in driving the efficiency and reliability of wind energy, contributing to a greener and more sustainable future.