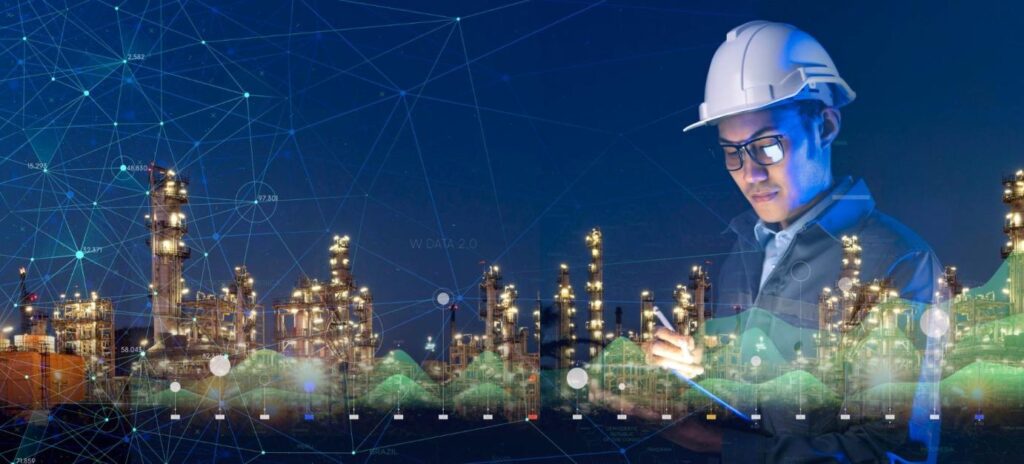
The oil and gas industry has always been at the forefront of technological advancements, constantly seeking innovative solutions to enhance efficiency and address challenges. In recent years, composites have emerged as a game-changing material, revolutionizing various sectors with their unique properties and versatility. This comprehensive guide aims to explore the role of composites in the oil and gas industry, highlighting their benefits, applications, and future prospects.
I. The Role of Composites in the Oil and Gas Industry
Composites, also known as composite materials, are engineered materials made by combining two or more different constituent materials to create a superior and specialized material. In the context of the oil and gas industry, composites offer remarkable advantages over traditional materials like steel or concrete. Their lightweight nature, high strength-to-weight ratio, and resistance to corrosion make them a compelling choice for numerous applications.
II. Benefits and Applications of Composites
Composites find extensive utilization across various sectors within the oil and gas industry, both in offshore exploration and onshore operations. Their remarkable properties make them suitable for a wide range of applications, from subsea pipelines and offshore drilling rigs to storage tanks and pipeline systems. The benefits of composites in the oil and gas industry include:
Corrosion Resistance: Composite materials exhibit excellent resistance to corrosion, a critical advantage in an industry where exposure to harsh environments and corrosive substances is commonplace.
Weight Reduction and Increased Durability: The lightweight nature of composites allows for significant weight reduction in structures and equipment, leading to improved fuel efficiency and reduced transportation costs. Additionally, composites offer enhanced durability and fatigue resistance, ensuring prolonged service life.
Enhanced Chemical Resistance: Composites possess superior chemical resistance, making them suitable for applications involving exposure to chemicals, acids, and other aggressive substances commonly encountered in the oil and gas industry.
Thermal Insulation Properties: Composites can provide excellent thermal insulation, making them valuable for applications where temperature control and insulation are crucial, such as pipelines or storage tanks.
Through a thorough understanding of composites and their applications, the oil and gas industry can unlock new possibilities for efficiency, safety, and sustainability.
Understanding Composites
A. Definition and Composition
What are composites?
Composites are materials composed of two or more distinct components that, when combined, create a new material with enhanced properties and performance characteristics. The components, known as matrix and reinforcement, work together synergistically to achieve specific mechanical, thermal, or chemical properties desired for a particular application.
Types of composite materials
There are several types of composite materials commonly used in the oil and gas industry. These include fiber-reinforced composites, particulate composites, and laminated composites. Fiber-reinforced composites, such as fiberglass or carbon fiber composites, are widely utilized due to their high strength and stiffness.
Key components of composites
The key components of composites are the matrix and reinforcement. The matrix material holds the reinforcement together, providing shape and protection, while the reinforcement material, often in the form of fibers or particles, imparts strength and other desired properties to the composite. The choice of matrix and reinforcement materials depends on the application requirements.
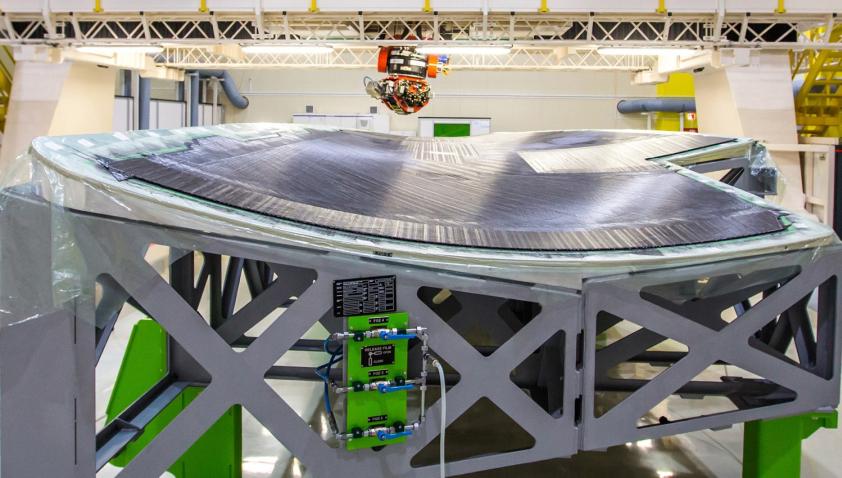
B. Manufacturing Processes
Resin transfer molding (RTM)
RTM is a manufacturing process where liquid resin is injected into a mold containing the reinforcement material. The resin then cures, creating a solid composite with the desired shape. RTM offers good control over resin distribution and is suitable for producing complex shapes and large-scale components.
Filament winding
Filament winding involves winding continuous fibers, typically impregnated with resin, onto a rotating mandrel in a specific pattern. This process produces high-strength cylindrical or spherical structures such as pipes or pressure vessels. Filament winding enables precise fiber orientation and controlled resin content.
Pultrusion
Pultrusion is a continuous manufacturing process where fibers and resin are pulled through a heated die, which cures the resin and shapes the composite. It is commonly used to produce constant cross-section profiles with high fiber volume fractions, such as rods, tubes, and beams.
Compression molding
Compression molding involves placing pre-cut reinforcement materials in a mold and then applying heat and pressure to consolidate the materials and cure the resin. This process is suitable for producing large, flat or moderately curved components with intricate details.
Understanding the different types of composites and the manufacturing processes involved is crucial for selecting the appropriate materials and fabrication methods in the oil and gas industry.
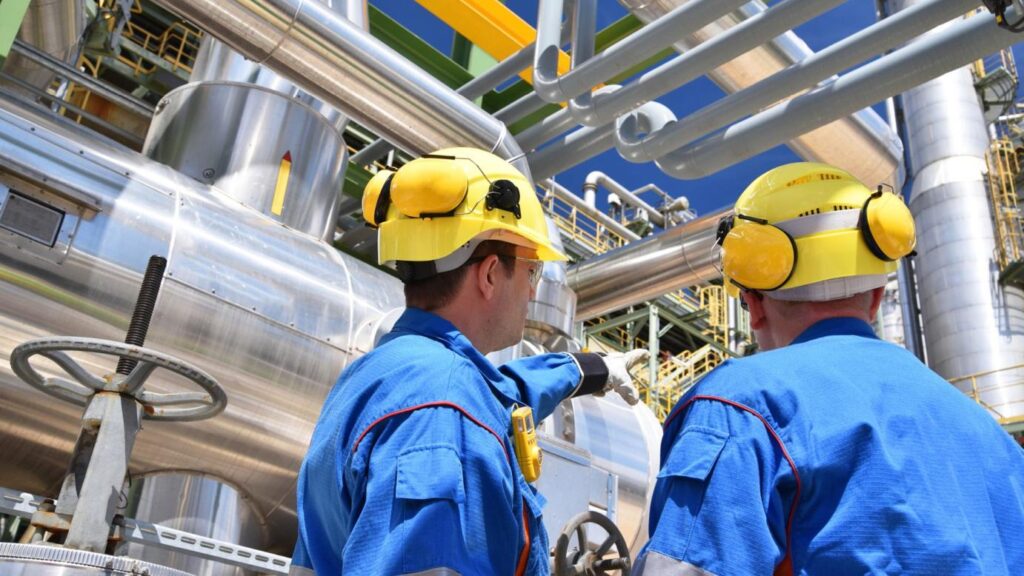
Composite Materials in Oil and Gas
A. Applications in Offshore Exploration
Subsea pipelines and risers
Composite materials have found extensive applications in subsea pipelines and risers. These structures are subjected to harsh underwater environments, including corrosion, high pressures, and temperature variations. Composites offer excellent resistance to corrosion, reducing the need for frequent maintenance and ensuring the integrity of the pipelines and risers.
Floating production storage and offloading (FPSO) vessels
FPSO vessels, used for offshore oil and gas production and storage, benefit from the use of composite materials. Composites provide lightweight construction, leading to increased payload capacity and reduced structural weight. Moreover, composites offer excellent resistance to seawater, chemicals, and fatigue, enhancing the durability and longevity of FPSO vessels.
Offshore drilling rigs
Composite materials are employed in various components of offshore drilling rigs. For example, composite gratings and walkways provide corrosion resistance, reduced weight, and improved safety for personnel working in these environments. Additionally, composite materials are used in drilling riser systems, where their high strength-to-weight ratio contributes to the overall efficiency and reliability of drilling operations.
B. Applications in Onshore Operations
Storage tanks and containers
Composite materials are widely used in the construction of storage tanks and containers in the oil and gas industry. Composites offer superior corrosion resistance, preventing leaks and ensuring the safe storage of hazardous substances. The lightweight nature of composites allows for easier installation and reduces transportation costs.
Pipeline systems
Composite materials play a vital role in onshore pipeline systems. They are used as liners, coatings, and repair systems to address corrosion, erosion, and mechanical damage. Composite liners offer an additional layer of protection, reducing the risk of leaks and extending the service life of pipelines. Moreover, composite repair systems provide cost-effective solutions for rehabilitating and reinforcing pipelines without the need for extensive excavation.
Well casings and liners
Composite materials are utilized in well casings and liners to enhance their structural integrity and performance. Composites provide corrosion resistance, high strength, and flexibility, allowing for efficient well drilling, completion, and production. Additionally, composite liners offer improved hydraulic efficiency and prevent the contamination of groundwater.
C. Advantages of Composites in Oil and Gas
Corrosion resistance
Composite materials exhibit exceptional resistance to corrosion, a critical advantage in the oil and gas industry. Corrosion can compromise the structural integrity of equipment and infrastructure, leading to costly repairs and safety hazards. Composites mitigate this risk by providing long-lasting protection against corrosive environments.
Weight reduction and increased durability
Composites offer significant weight reduction compared to traditional materials like steel. This weight reduction translates into lower transportation costs, increased payload capacity, and improved operational efficiency. Additionally, composites have high fatigue resistance, ensuring prolonged durability and reduced maintenance requirements.
Enhanced chemical resistance
The oil and gas industry often involves exposure to harsh chemicals, such as acids and solvents. Composites exhibit excellent resistance to chemical degradation, making them suitable for handling and storing corrosive substances. This chemical resistance ensures the integrity of equipment and reduces the risk of leaks or failures.
Thermal insulation properties
Composite materials possess inherent thermal insulation properties. They can provide insulation against high temperatures, preserving the integrity of pipelines, storage tanks, and other critical infrastructure. Composites also contribute to energy efficiency by minimizing heat transfer, reducing the need for additional insulation systems.
Composite materials offer numerous advantages in various applications within the oil and gas industry. Their corrosion resistance, weight reduction, enhanced durability, chemical resistance, and thermal insulation properties make them a preferred choice for critical operations.
Case Studies
A. Successful Composite Applications in Offshore
Case study 1: Composite risers in deepwater drilling
In deepwater drilling operations, composite risers have proven to be a game-changer. Traditional steel risers are heavy and susceptible to corrosion, requiring frequent inspections and maintenance. However, the use of composite risers offers numerous advantages. They are lightweight, corrosion-resistant, and possess high strength. These properties allow for increased operational efficiency, reduced installation and maintenance costs, and enhanced safety. Several offshore projects have successfully deployed composite risers, demonstrating their reliability and effectiveness in deepwater exploration.
Case study 2: Composite repair systems for pipelines
Pipeline integrity is crucial in the oil and gas industry, and composite repair systems have emerged as a reliable solution. Traditional repair methods often involve extensive excavation and replacement, leading to significant downtime and costs. Composite repair systems offer a non-intrusive alternative, allowing for in-situ repairs without disrupting the pipeline operations. These systems utilize composite materials, such as epoxy-based wraps or patches, to reinforce damaged sections, restore structural integrity, and prevent further deterioration. Several pipeline operators have implemented composite repair systems, resulting in cost savings, improved pipeline performance, and extended service life.
B. Successful Composite Applications in Onshore
Case study 3: Composite storage tanks in harsh environments
Harsh environments, such as chemical plants or industrial facilities, demand robust storage solutions. Composite storage tanks have proven to be an excellent choice in these settings. Composites offer exceptional resistance to corrosion, chemicals, and environmental factors, ensuring the safe storage of hazardous substances. These tanks are lightweight, easy to install, and require minimal maintenance compared to traditional materials. Case studies have shown that composite storage tanks outperform conventional alternatives, providing long-term durability, reduced life cycle costs, and increased operational safety.
Case study 4: Composite pipeline rehabilitation
As existing pipeline infrastructure ages, rehabilitation becomes essential to ensure continued performance and prevent leaks. Composite materials have revolutionized the pipeline rehabilitation process. Composite liners, wraps, or coatings can be applied to existing pipelines to restore their structural integrity and extend their service life. These solutions offer excellent corrosion resistance, improve hydraulic efficiency, and reduce the risk of leaks or failures. Several successful case studies have demonstrated the effectiveness of composite pipeline rehabilitation, providing cost-effective and sustainable solutions for aging pipeline networks.
Case studies showcasing successful composite applications in both offshore and onshore operations highlight the tangible benefits of these materials in the oil and gas industry. The use of composite risers, repair systems, storage tanks, and pipeline rehabilitation solutions has resulted in improved performance, cost savings, increased safety, and enhanced environmental sustainability.
Challenges and Limitations
The widespread adoption of composite materials in the oil and gas industry has brought numerous benefits, but it is essential to acknowledge and address the challenges and limitations associated with their use. This chapter explores some of the key challenges and limitations faced when utilizing composites in the industry.
A. Design and Testing Standards
Industry regulations and certifications
The oil and gas industry operates within strict regulatory frameworks to ensure safety and compliance. However, the use of composite materials may require the development of specific standards and certifications to address unique characteristics and performance requirements. Establishing comprehensive design guidelines, testing protocols, and certification processes specific to composite materials is crucial for their wider acceptance and deployment in the industry.
Performance testing and validation
Validating the performance and durability of composite materials is an ongoing challenge. Rigorous testing and evaluation are necessary to ensure that composites can withstand the demanding conditions encountered in oil and gas operations, including extreme temperatures, pressure differentials, and corrosive environments. Developing standardized testing procedures and methodologies tailored to composite materials is essential to instill confidence in their reliability and longevity.
B. Cost Considerations
Initial investment and long-term savings
While composites offer numerous benefits, their initial cost can be higher compared to traditional materials. The expense associated with research, development, and manufacturing processes for composite materials may pose a barrier to adoption, particularly for smaller companies or projects with limited budgets. However, it is important to consider the long-term savings potential, including reduced maintenance, improved operational efficiency, and extended service life, which can offset the initial investment.
Cost comparison with traditional materials
Evaluating the cost-effectiveness of composite materials compared to traditional alternatives is crucial. Conducting comprehensive cost analyses that consider factors such as material acquisition, manufacturing, installation, maintenance, and lifecycle costs is necessary to make informed decisions. Additionally, as the demand for composites increases, economies of scale and advancements in manufacturing processes are likely to contribute to cost reductions, enhancing their competitiveness.
C. Environmental Impact and Sustainability
Recycling and disposal of composites
Composite materials pose challenges in terms of end-of-life management. Developing efficient recycling and disposal methods for composites is essential to minimize their environmental impact. Advances in recycling technologies, such as composite shredding and thermal decomposition, are being explored to recover valuable materials and reduce waste. Additionally, promoting the use of bio-based or recyclable composite materials can contribute to greater sustainability in the oil and gas industry.
Future developments for sustainable composites
Continued research and development efforts are focused on improving the sustainability of composite materials. This includes exploring the use of renewable resources, bio-based resins, and recyclable fibers. Collaborative initiatives among industry stakeholders, academia, and research institutions are driving innovation in sustainable composites, aiming to minimize their carbon footprint and enhance their environmental compatibility.
Addressing these challenges and limitations requires collaboration among industry players, regulatory bodies, and research institutions. By investing in research, developing comprehensive standards, and fostering innovation, the oil and gas industry can overcome these obstacles and further unlock the potential of composite materials.
Future Trends and Innovations
The oil and gas industry is continuously evolving, and so are the trends and innovations in composite materials. This chapter explores some of the exciting advancements and future trends that hold promise for revolutionizing the use of composites in the industry.
A. Advancements in Composite Technology
Nanocomposites and hybrid materials
Nanotechnology has the potential to revolutionize composite materials by enhancing their mechanical, thermal, and chemical properties. Nanocomposites, which incorporate nanoscale fillers or reinforcements, offer improved strength, durability, and resistance to environmental factors. Additionally, the development of hybrid materials, combining different types of fibers or matrices, enables the customization of composites for specific applications, further expanding their versatility.
Smart composites and sensors
The integration of smart technologies and sensors within composite materials opens up new possibilities for real-time monitoring, data collection, and analysis. Smart composites equipped with embedded sensors can detect and transmit information regarding stress levels, temperature, corrosion, and structural integrity. This data enables proactive maintenance and reduces the risk of failure, enhancing safety and operational efficiency in oil and gas operations.
B. Industry Collaboration and Research Initiatives
Partnerships for innovation
Collaboration among oil and gas companies, composite manufacturers, research institutions, and technology providers is vital for driving innovation and accelerating the adoption of composites. Through strategic partnerships and joint research initiatives, knowledge sharing, and resource pooling, industry players can leverage their expertise and resources to overcome technological barriers and develop cutting-edge composite solutions.
Research on advanced composite materials
Ongoing research efforts focused on advancing composite materials continue to propel the industry forward. Scientists and engineers are exploring novel materials, improving manufacturing processes, and investigating new applications for composites in the oil and gas sector. This research aims to address existing challenges, enhance performance characteristics, and uncover new opportunities for composite materials in various operational environments.
C. Sustainability and Environmental Considerations
Eco-friendly composite materials
The drive for sustainability is influencing the development of eco-friendly composite materials. Researchers are exploring bio-based resins, recycled fibers, and environmentally friendly manufacturing processes to reduce the carbon footprint of composites. These advancements contribute to the industry’s commitment to environmental stewardship and align with global efforts to mitigate climate change and promote a circular economy.
Lifecycle assessment and carbon footprint reduction
Understanding the environmental impact of composite materials throughout their lifecycle is becoming increasingly important. Conducting comprehensive lifecycle assessments helps identify areas where carbon emissions can be minimized, energy efficiency improved, and waste reduced. By optimizing the production, use, and disposal stages, the oil and gas industry can further enhance the sustainability profile of composites.
As the oil and gas industry embraces these future trends and innovations, composite materials will continue to play a significant role in shaping the industry’s future. By harnessing the potential of advanced materials, investing in research and development, and fostering collaboration, the industry can unlock new possibilities, improve performance, and drive sustainable growth.
Summary
Composites have emerged as a game-changing technology in the oil and gas industry, offering numerous benefits and applications across various operations. In this comprehensive guide, we have explored the role of composites, their manufacturing processes, and their applications in both offshore and onshore settings. We have also delved into the advantages of composites, presented case studies showcasing successful applications, and discussed the challenges and limitations associated with their use.
Throughout this guide, it has become evident that composites provide a host of advantages, including corrosion resistance, weight reduction, increased durability, and enhanced chemical resistance. These properties make them ideal for applications such as subsea pipelines, storage tanks, well casings, and more. The case studies highlighted the successful implementation of composites in offshore and onshore settings, demonstrating their reliability and effectiveness in real-world scenarios.
However, the use of composites in the oil and gas industry does come with challenges and limitations. Design and testing standards, industry regulations, and certifications are crucial to ensure the safe and reliable performance of composite materials. Cost considerations, both in terms of initial investment and long-term savings, must also be evaluated to make informed decisions. Furthermore, environmental impact and sustainability aspects, including recycling and disposal, require careful attention to mitigate any negative effects.
Looking towards the future, we explored exciting trends and innovations that will shape the use of composites in the oil and gas sector. Advancements in nanocomposites, hybrid materials, and smart composites with embedded sensors promise to revolutionize the industry by enhancing performance and enabling real-time monitoring. Industry collaboration and research initiatives foster innovation, while sustainable practices and eco-friendly composite materials contribute to environmental stewardship.
In conclusion, composites have revolutionized the oil and gas industry, offering a wide range of benefits and applications. By understanding their composition, manufacturing processes, and the challenges associated with their use, industry professionals can make informed decisions when considering the adoption of composites. With ongoing advancements, collaborations, and a focus on sustainability, composites are poised to play a pivotal role in the future of the oil and gas sector.
As we conclude this comprehensive guide on revolutionizing the oil and gas industry with composites, let’s address some common questions that often arise regarding the use of composites in this sector.
Q1: What are the main advantages of using composites in the oil and gas industry?
Composites offer several advantages, including exceptional corrosion resistance, reduced weight leading to easier transportation and installation, increased durability in harsh environments, and enhanced chemical resistance. Additionally, composites provide thermal insulation properties, contribute to improved energy efficiency, and enable design flexibility.
Q2: How do composites compare to traditional materials in terms of cost?
While the initial investment in composites may be higher than that of traditional materials, their long-term savings outweigh the upfront costs. Composites’ superior durability and resistance to corrosion eliminate the need for frequent maintenance and repairs, resulting in reduced operational costs over time.
Q3: Are composites environmentally friendly?
Composites can be environmentally friendly when used responsibly. They have the potential for recycling and reuse, which helps minimize waste. Additionally, their lightweight nature contributes to reduced energy consumption during transportation and installation. However, it is important to implement proper recycling and disposal practices to ensure their sustainability.
Q4: What regulations and certifications govern the use of composites in the industry?
The oil and gas industry follows stringent regulations and certifications to ensure the safe and reliable use of composites. These may include industry-specific standards, such as API (American Petroleum Institute) standards, ISO (International Organization for Standardization) certifications, and other regional or national regulations. Adhering to these guidelines ensures compliance and maintains high-quality standards.
Q5: What is the future outlook for composite materials in the oil and gas sector?
The future of composite materials in the oil and gas sector is promising. Ongoing research and development efforts focus on advancing composite technology, including the development of nanocomposites, hybrid materials, and smart composites with embedded sensors. Collaboration between industry stakeholders and research institutions drives innovation, paving the way for new applications and improved performance.
With these frequently asked questions addressed, we hope to have provided a clear understanding of composites and their impact on the oil and gas industry. As technologies evolve and sustainability becomes increasingly important, composites are poised to play an integral role in shaping the future of this sector.
Q1: What are the composite materials used in the oil and gas industry?
Composite materials commonly used in the oil and gas industry include fiber-reinforced polymers (FRPs) such as fiberglass composites, carbon fiber composites, and aramid fiber composites. These materials offer excellent strength-to-weight ratios and corrosion resistance, making them suitable for various applications in this industry.
Q2: What are the four types of composites?
The four main types of composites are:
Polymer Matrix Composites (PMCs): These composites consist of a polymer resin matrix reinforced with fibers such as fiberglass or carbon fibers.
Metal Matrix Composites (MMCs): In MMCs, a metal matrix is reinforced with ceramic or metallic fibers to enhance mechanical properties.
Ceramic Matrix Composites (CMCs): CMCs consist of a ceramic matrix reinforced with ceramic fibers, providing high-temperature resistance and strength.
Natural Fiber Composites (NFCs): NFCs utilize natural fibers such as wood, flax, or hemp, embedded in a polymer matrix, offering renewable and sustainable alternatives to traditional composites.
Q3: What are composite materials in the offshore industry?
Composite materials find various applications in the offshore industry, including:
Subsea pipelines and risers: Composite pipes and risers provide corrosion resistance, reduced weight, and improved durability for transporting oil and gas from offshore wells to processing facilities.
Floating Production Storage and Offloading (FPSO) vessels: Composites are used in the construction of FPSO hulls, providing weight reduction and enhanced resistance to harsh offshore environments.
Offshore drilling rigs: Composite materials are employed in the construction of drilling risers, derricks, and other structural components, offering corrosion resistance and increased load-bearing capabilities.
Q4: What are three examples of composites?
Three examples of composites are:
Fiberglass composites: Fiberglass composites consist of a polymer matrix reinforced with glass fibers. They are widely used in various industries, including aerospace, automotive, and construction.
Carbon fiber composites: Carbon fiber composites utilize carbon fibers embedded in a polymer matrix. They offer exceptional strength and stiffness while remaining lightweight, making them ideal for applications in aerospace, sports equipment, and high-performance vehicles.
Wood-plastic composites: Wood-plastic composites combine wood fibers or particles with a polymer matrix. These composites offer the appearance and workability of wood while providing enhanced durability and resistance to moisture and insects.
Q5: What are the five basic types of composite materials?
The five basic types of composite materials are:
Polymer Matrix Composites (PMCs)
Metal Matrix Composites (MMCs)
Ceramic Matrix Composites (CMCs)
Natural Fiber Composites (NFCs)
Hybrid Composites: These composites combine two or more types of reinforcement or matrix materials, such as carbon fibers with ceramic matrices or natural fibers with polymer matrices.
Q6: What are four materials that can be made from crude oil?
Crude oil can be processed to produce various materials, including:
Gasoline: Used as a fuel for internal combustion engines in vehicles.
Diesel: Used as a fuel for diesel engines in vehicles and machinery.
Jet fuel: Used as fuel for aircraft engines.
Petrochemicals: Crude oil is a source of raw materials for the production of plastics, synthetic fibers, solvents, lubricants, and other chemicals used in various industries.
Q1: What are six composite materials?
Six examples of composite materials are:
Fiberglass: A composite material made of glass fibers embedded in a polymer matrix, commonly used in construction, automotive parts, and boat hulls.
Carbon Fiber Reinforced Polymer (CFRP): A composite material that combines carbon fibers with a polymer matrix, known for its high strength and lightweight properties. It is widely used in aerospace, sports equipment, and automotive industries.
Aramid Fiber Reinforced Polymer (AFRP): A composite material that utilizes aramid fibers, such as Kevlar, in a polymer matrix. It offers high strength, impact resistance, and is commonly used in protective gear, bulletproof vests, and aerospace applications.
Natural Fiber Composites (NFCs): Composites that use natural fibers, such as bamboo, flax, or hemp, combined with a polymer matrix. NFCs are increasingly used in eco-friendly applications like furniture, packaging, and construction materials.
Metal Matrix Composites (MMCs): Composites that incorporate metal matrices, like aluminum, reinforced with ceramic or metallic fibers. MMCs find applications in aerospace, automotive, and sporting goods industries.
Ceramic Matrix Composites (CMCs): Composites composed of a ceramic matrix reinforced with ceramic fibers. CMCs exhibit high-temperature resistance and are used in aerospace, automotive, and thermal management applications.
Q2: What is the most popular composite?
One of the most popular composites is fiberglass. Fiberglass composites consist of glass fibers embedded in a polymer matrix, typically made of epoxy or polyester resin. Fiberglass is widely used in construction, automotive parts, marine applications, and various consumer products due to its excellent strength, durability, and cost-effectiveness.
Q3: What is the most common type of composite?
The most common type of composite is the Fiber-Reinforced Polymer (FRP) composite. FRPs utilize various types of fibers, such as fiberglass or carbon fibers, embedded in a polymer matrix, commonly epoxy or polyester resin. FRP composites are extensively used in industries such as construction, aerospace, automotive, marine, and infrastructure due to their versatility, strength, and corrosion resistance.
Q4: Which industries use composite materials?
Several industries use composite materials, including:
Aerospace: Composites are used in aircraft structures, interiors, and components to reduce weight and improve fuel efficiency.
Automotive: Composite materials find applications in car bodies, interiors, and high-performance components to enhance strength, reduce weight, and increase fuel economy.
Construction: Composites are used in building structures, bridges, and infrastructure for their strength, durability, and corrosion resistance.
Marine: Composite materials are utilized in boat hulls, decks, and components for their lightweight properties, corrosion resistance, and improved performance in water.
Sports and Recreation: Composites are commonly used in sports equipment such as tennis rackets, golf clubs, bicycles, and skis to provide strength, stiffness, and lightness.
Q5: What are two examples of composites?
Two examples of composites are:
Fiberglass: A composite material made of glass fibers embedded in a polymer matrix, commonly used in construction, automotive parts, and boat hulls.
Carbon Fiber Reinforced Polymer (CFRP): A composite material that combines carbon fibers with a polymer matrix, known for its high strength and lightweight properties. It is widely used in aerospace, sports equipment, and automotive industries.
Q6: What is the use of composite materials in marine?
Composite materials find extensive use in marine applications due to their favorable properties such as lightweight, high strength, and resistance to corrosion and degradation in a marine environment. They are used in boat hulls, decks, masts, propellers, and other components to improve performance, fuel efficiency, and durability. Composite materials offer advantages such as reduced weight, increased speed, improved fuel economy, and lower maintenance requirements in marine vessels.
Q7: What are the two main parts in composites?
The two main parts in composites are the reinforcement and the matrix.
Reinforcement: The reinforcement in composites provides strength, stiffness, and other desired mechanical properties. It is usually in the form of fibers, particles, or flakes, such as fiberglass, carbon fibers, or natural fibers like bamboo or flax.
Matrix: The matrix material surrounds and holds the reinforcement in place, providing cohesion, transferring load, and protecting the reinforcement from external factors. The matrix is typically a polymer resin, such as epoxy, polyester, or vinyl ester, which can be cured or hardened to form a solid composite structure.
Q1: Is carbon fiber a composite?
Yes, carbon fiber is a composite material. It is made up of thin strands of carbon fibers that are embedded in a polymer matrix. The carbon fibers provide the strength and stiffness, while the polymer matrix holds the fibers together and provides protection. The combination of carbon fibers and the polymer matrix creates a composite material with exceptional strength-to-weight ratio and other desirable properties.
Q2: What are the three components of a composite?
The three components of a composite material are:
Reinforcement: This component provides the strength, stiffness, and other desired mechanical properties to the composite. It can be in the form of fibers, particles, or flakes. Examples include carbon fibers, glass fibers, or natural fibers like bamboo or flax.
Matrix: The matrix material surrounds and holds the reinforcement in place, providing cohesion, transferring load, and protecting the reinforcement from external factors. The matrix is typically a polymer resin, such as epoxy, polyester, or vinyl ester, which can be cured or hardened to form a solid composite structure.
Interface: The interface is the region where the reinforcement and matrix interact. It plays a crucial role in transferring stress between the reinforcement and matrix, ensuring efficient load transfer and preventing delamination or separation.
Q3: What is the difference between carbon fiber and composite?
Carbon fiber is a type of reinforcement material used in composites. It consists of thin, strong, and lightweight carbon fibers. On the other hand, a composite refers to a material that consists of two or more distinct components, such as fibers and a matrix, combined to create a material with enhanced properties.
In summary, carbon fiber is a specific type of reinforcement material used in composites, while a composite refers to the overall material formed by combining reinforcement and matrix components.
Q4: Is carbon fiber a metal or plastic?
Carbon fiber is neither a metal nor a plastic. It is a type of material derived from carbon atoms, and it exhibits unique properties such as high strength, low weight, and excellent stiffness. Carbon fiber is commonly used as a reinforcement component in composite materials, where it is combined with a polymer matrix to create strong and lightweight composites.
Q5: What is the difference between resin and composite?
Resin and composite are related but distinct terms in the context of composite materials.
Resin: Resin refers to the polymer material used as the matrix component in a composite. It is typically a liquid or semi-liquid substance that can be cured or hardened to form a solid material. Resins such as epoxy, polyester, and vinyl ester are commonly used in composite manufacturing.
Composite: A composite refers to the overall material formed by combining two or more components, typically a reinforcement and a matrix. The reinforcement provides strength and stiffness, while the matrix holds the reinforcement in place and protects it. The combination of reinforcement and matrix creates a composite material with superior properties compared to its individual components.
In essence, resin is a specific component of a composite material, while composite refers to the entire material formed by combining the reinforcement and matrix.
Q6: What is the strongest composite material?
The strongest composite material is debatable and depends on the specific application and desired properties. However, carbon fiber reinforced composites, particularly those using high-performance carbon fibers like carbon nanotubes or graphene, are known for their exceptional strength and stiffness. These composites exhibit high tensile strength and are widely used in industries such as aerospace and sports.
Q7: What is the future of composite materials?
The future of composite materials is promising, with ongoing advancements and innovations driving their widespread adoption in various industries. Some key trends and developments shaping the future of composites include:
Enhanced Performance: Continued research and development efforts are focused on improving the strength, stiffness, and other mechanical properties of composites. This includes the use of advanced reinforcements, such as carbon nanotubes or graphene, and developing hybrid composite systems.
Lightweighting: The demand for lightweight materials to improve energy efficiency and reduce carbon emissions is driving the adoption of composites. Lightweight composites enable the design of more fuel-efficient vehicles, aircraft, and structures, offering significant advantages over traditional materials.
Sustainability: There is a growing emphasis on developing sustainable composite materials, including the use of bio-based resins and natural fiber reinforcements. Recycling and end-of-life considerations are also being addressed to reduce the environmental impact of composites.
Integration of Smart Features: The integration of sensors, actuators, and other smart features within composite structures is an emerging trend. These smart composites can monitor their own structural health, detect damage or stress, and enable real-time feedback for maintenance or performance optimization.
Overall, the future of composite materials is expected to witness continuous advancements in performance, sustainability, and integration of smart functionalities, enabling their wider application across industries.
Q8: What are two examples of natural composites?
Two examples of natural composites are:
Wood: Wood is a natural composite material composed of cellulose fibers embedded in a lignin matrix. The arrangement of fibers provides wood with strength and stiffness, while the matrix offers cohesion and protection. Wood exhibits a unique combination of properties such as lightness, durability, and thermal insulation.
Bone: Bone is another natural composite material. It consists of a mineralized matrix, primarily composed of hydroxyapatite, and collagen fibers. The mineral component provides hardness and compressive strength, while the collagen fibers offer flexibility and tensile strength. The combination of these components results in a lightweight and strong material.
Q9: Is composite a sustainable material?
The sustainability of composites depends on various factors, including the specific composition of the composite, its end-of-life considerations, and the manufacturing processes involved. While composites offer several environmental benefits, such as lightweighting and improved energy efficiency, their sustainability can be further enhanced through:
Material Selection: Opting for sustainable and renewable reinforcement materials, such as natural fibers or bio-based polymers, can reduce the environmental impact of composites.
Recycling and Disposal: Developing efficient recycling processes for composite materials can help minimize waste and extend their lifecycle. Recycled composites can be used in secondary applications or as fillers for other materials.
Manufacturing Efficiency: Emphasizing energy-efficient manufacturing processes, reducing waste generation, and employing cleaner production techniques contribute to the sustainability of composite materials.
Overall, while composites have the potential to be sustainable materials, their sustainability is contingent on conscious material selection, recycling efforts, and environmentally responsible manufacturing practices.
Q10: What are the different types of composite materials?
There are various types of composite materials based on the nature of their reinforcement and matrix components. Some common types include:
Fiber-reinforced composites: These composites use high-strength fibers, such as carbon fibers, glass fibers, or aramid fibers, as the reinforcement component. The fibers are embedded in a polymer, metal, or ceramic matrix.
Particle-reinforced composites: In these composites, particles, such as metal, ceramic, or polymer particles, are dispersed within a matrix material to enhance specific properties like strength, wear resistance, or thermal conductivity.
Structural composites: These composites are designed to provide high structural integrity and are commonly used in applications where strength and stiffness are crucial. Examples include carbon fiber reinforced polymer (CFRP) composites used in aerospace and automotive industries.
Sandwich composites: Sandwich composites consist of a lightweight core material, such as foam or honeycomb structure, sandwiched between two thin, rigid face sheets. This construction provides high stiffness and strength while maintaining low weight.
Ceramic matrix composites (CMCs): CMCs combine ceramic fibers with a ceramic matrix, offering excellent high-temperature resistance, thermal stability, and wear resistance. They find applications in aerospace, energy, and nuclear industries.
Metal matrix composites (MMCs): MMCs utilize metal reinforcements, such as fibers or particles, within a metal matrix. These composites offer enhanced mechanical properties, improved thermal conductivity, and high-temperature resistance.
These are just a few examples, and composite materials can be tailored to meet specific requirements by combining different reinforcements and matrices.
Q11: What are the engineering applications of composites?
Composites find extensive use in various engineering applications due to their unique properties. Some common engineering applications of composites include:
Aerospace and Aviation: Composites are widely used in aerospace structures, including aircraft fuselages, wings, tail sections, and interior components. The lightweight nature and high strength-to-weight ratio of composites contribute to improved fuel efficiency and increased payload capacity.
Automotive Industry: Composites are employed in automotive applications to reduce vehicle weight and enhance fuel efficiency without compromising safety. Components like body panels, chassis structures, and interior parts can be made using composites.
Construction and Infrastructure: Composites find application in construction for bridges, columns, beams, and reinforcement of concrete structures. The high strength and corrosion resistance of composites make them suitable for challenging environments and seismic zones.
Marine Industry: Composites are used in the marine sector for boat hulls, decks, and superstructures. The corrosion resistance and lightweight properties of composites contribute to improved performance, fuel efficiency, and durability.
Sports and Recreation: Composites play a vital role in sporting equipment such as tennis rackets, golf clubs, bicycle frames, and helmets. They offer improved performance, durability, and flexibility compared to traditional materials.
Renewable Energy: Composites are utilized in wind turbine blades, solar panel structures, and hydroelectric components. Their high strength, corrosion resistance, and fatigue properties make them suitable for renewable energy applications.
These are just a few examples, and the engineering applications of composites continue to expand as their performance, manufacturing techniques, and design capabilities evolve.